Metal galling is a type of surface wear that causes metal to unintentionally engage with another metal in contact. Metal galling phenomena can result in the separation of metal pieces from the original component. The process of metal galling is quite rapid and once initiated can lead to component failure with subsequent operating cycles.
The galling mechanism in metals is quite different from other wear mechanisms due to the adhesion it creates. Contrary to other types of wear processes, metal galling causes the metal to adhere to the other material and is unique. Whereas, other wear forms involve erosion of one metal when in contact with another metal.
The effect of galling in metals can be at varying levels; Large or microscopic levels. Microscopic galling is not easily visible. Large metal galling can easily be seen on metal surfaces by the naked eye. Even though microscopic galling does not make the component completely useless, but still it can cause performance failure for components with tight tolerances.
Causes of Metal Galling
Galling in metals occur because of large frictional forces that cause adhesive wear. This usually happens when two or more metals are in contact with one another under the influence of very high loads. Ductile materials having a crystal structure that promotes cohesive attraction are ideal for metal galling. Many of industrial metals exhibit both of these characteristics and that is why galling is quite a common phenomenon among most metals. The frictional force gives the required energy for adhesion to occur. So for galling to occur all the following three factors need to be present:
- High frictional force
- Ductility of material (One softer than the other), and
- Cohesive attraction
Mechanism of Metal Galling : How does galling work?
Upon compressing one metal surface over another, they merge at the contact zone. The contact zone is the highest force point. When these compressive forces are large enough, friction is created and the pressure in the contact zone is also increased. The energy generated by this friction and pressure, causes adhesion between the two surfaces, welding the two materials together and plastically deforming them. The protruding points if available on any one of the surfaces can easily penetrate the surface oxide layer of the opposing material, causing damage to the metal beneath.
Now, when sliding friction occurs, the strong adhesion turns into galling. In the contact zone, the amount of stress increases which enables the two surfaces to break away from each other and dissolve the contact zone. This causes one material to lose particles to the other.
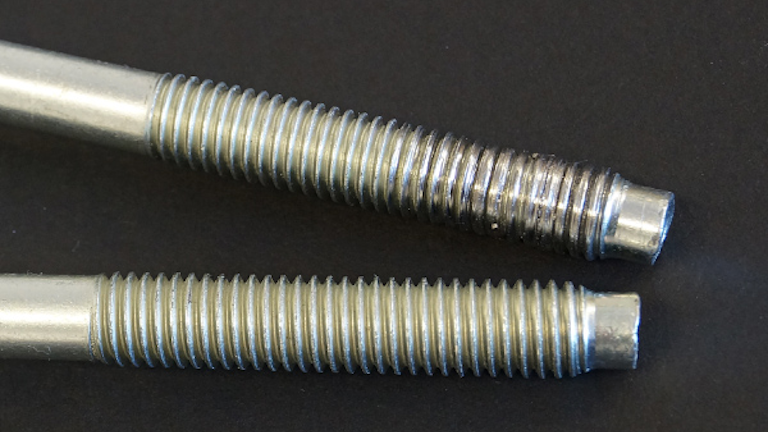
What does Galling look like?
Galling typically appears as surface damage or wear on metal components that are in sliding or rubbing contact with each other under pressure. Some common visual indications of galling include:
- Surface Scuffing: This involves the formation of scratches, grooves, or rough patches on the metal surface due to friction and material transfer between the mating surfaces.
- Discoloration: Galled surfaces may exhibit discoloration, often appearing as darkened or discolored areas resulting from the intense heat generated by friction during the rubbing process.
- Adhesion Marks: Galling can cause material from one metal surface to adhere to the other, leaving behind visible marks or patches where material transfer has occurred.
- Rounded Edges: The edges of components may become rounded or flattened due to plastic deformation caused by the repeated sliding or rubbing action, especially at points of contact.
- Surface Smearing: Galled surfaces may show signs of material transfer or smearing, where material from one surface is physically transferred and deposited onto the other surface.
- Surface Roughness: Galling can increase the surface roughness of metal components, making them feel rough or uneven to the touch.

Metals Susceptible to Galling
Austenitic Stainless Steel, Aluminum, and Titanium are the most prominent metals that frequently encounter galling issues. Martensitic stainless steels, tool steels, or other similar hardened materials are less likely to have metal galling occur.
When Does Galling Occur?
Applications involving two or more ductile materials imposing high frictional forces on one another are susceptible to galling. The most frequent instances of galling are found on fasteners made of Stainless steel and aluminum. While torquing, all such fasteners result in high frictional forces that are the prime component for metal galling to occur. Machinery subjected to excess friction is also at risk for galling.
How to Prevent Galling?
As metal galling can result in component failure leading to hazards, It must be prevented to occur. The factors that impact metal galling are
- Material
- Applied Load
- Lubrication and Coating
- Surface finish and Hardness
- Contact Area and Degree of Movement
A number of ways are prevalent in metal industries to prevent galling. Some of such methods for galling prevention are:
- Selecting a metal not prone to galling like hardened tool steels, work-hardened austenitic stainless steels, etc.
- Applying lubricants to reduce friction between surfaces. In recent times, anti-galling lubricants containing molybdenum compounds and anti-galling coatings are also available.
- Selecting a coarser thread to reduce the amount of friction in threaded fasteners.
- Reduction of thread tightening speed reduces frictional heating and the risk of galling. Manual tightening will help in such cases.
- Keeping the metal contact surfaces clean, and free from debris.
- Reducing the load values between contacting metallic surfaces.
- The use of dissimilar materials with low ductility or different grades of materials can reduce the galling effect.
- Bolts with dented or damaged threads increase the potential for galling. So, always clean and damage-free bolts need to be selected.
- Increasing contact area to lower the stresses below the threshold galling stress
- Increasing contact area to spread wear volume over a greater area and thus producing less depth of wear.
What is galling in metal?
Galling in metals is a problem that occurs when two contacting surfaces seize up due to cold welding.
What causes metal to gall?
The main cause of metal galling is friction force and adhesion. The sufficient friction force between contact surfaces causes adhesive wear.
What is anti-Gallant?
Anti-gallants are coatings used on metal surfaces to minimize the friction between rubbing surfaces and thus prevent the galling effect.
What is galling in stainless steel?
The seizure of stainless steel components causing severe adhesive wear is known as stainless steel galling. Because of the galling mechanism in stainless steel, components may become weak or even break.
What are the factors that affect the galling in stainless steel?
The factors that can impact the galling mechanism in metals are:
- Design
- Applied load
- Contact area and degree of movement
- Lubrication
- Surface finish and hardness
What is the galling resistance chart of materials?
The metal galling resistance chart is a representation that provides typical galling resistance characteristics for material combinations when used to rub against each other. A typical galling resistance chart is produced below as a sample.
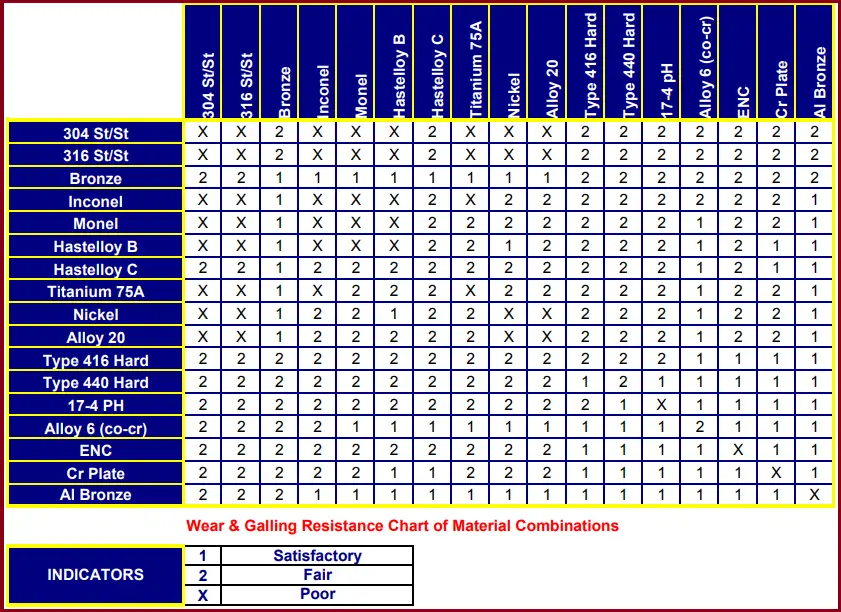
What hardness prevents galling in metals?
If both the metals have a hardness difference of at least 50 Brinell (20 Rc) then they harden at different rates and it reduces chances of metal galling.
Differences between Welding and Galling
Both welding and galling are different phenomena. Welding is a fabrication method for joining metals. Galling is a form of surface damage that occurs when two metal surfaces under pressure begin to adhere to each other, leading to friction, material transfer, and wear. The major differences between them are tabulated below:
Aspect | Welding | Galling |
---|---|---|
Definition | Joining process that fuses materials together using heat and/or pressure | Surface damage caused by friction between mating metal surfaces |
Occurrence | Deliberately performed during fabrication or repair | Unintended and undesirable during operation |
Purpose | Creates a strong, permanent bond between materials | Leads to wear and potential failure of components |
Mechanism | Fusion of materials at the atomic level | Material transfer and surface damage |
Temperature | Requires high temperatures to melt and fuse materials | Occurs at relatively lower temperatures due to friction |
Location | Typically occurs at specific joints or seams | Can occur anywhere metal surfaces rub against each other |
Effects | Intended to strengthen and join materials | Can weaken components and lead to operational issues |
Equipment | Requires welding equipment and expertise | No specialized equipment required |
Prevention | Controlled welding parameters and techniques | Proper lubrication and material selection |
What is an Example of Galling?
A common example of galling occurs is threaded fasteners, such as bolts and nuts, when they are tightened together under pressure. Some other typical examples are:
- Shafts and Bearings: In rotating machinery, such as engines, pumps, and gearboxes, shafts and bearings can experience galling when insufficient lubrication or improper surface finishes lead to friction between the mating surfaces. This can result in scoring, wear, and reduced performance of the equipment.
- Valves and Valve Seats: In valves used in hydraulic systems, engines, or pipelines, galling can occur between the valve stem and the valve seat due to repeated opening and closing actions. The high pressure and friction between the mating surfaces can cause material transfer and surface damage, affecting the sealing performance of the valve.
- Sliding Contact Surfaces: Any metal components in sliding contact, such as gears, cams, sliders, and tracks, can experience galling if proper lubrication is lacking or if the materials have incompatible properties. Galling in these components can lead to increased friction, wear, and even system failure if left unchecked.
- Pipe Fittings and Flanges: Galling can occur in pipe fittings, connectors, and flanges used in piping systems due to the tightening of threaded connections or the mating of flange faces. This can lead to damage to the sealing surfaces, compromising the integrity of the piping system and potentially causing leaks.
- Fastening Systems: Galling can also occur in non-threaded fastening systems, such as press-fit assemblies, where metal surfaces come into contact under pressure. This can lead to material transfer, deformation, and impaired functionality of the fastening system.
- Piping Shoe Supports and Structural Members
Let’s take a look at the following video to understand the metal galling in threads.
I have a outdoor yard wind spinner that hangs with a ball bearing swivel hook. The wind spinner has stopped working because the ball bearing swivel hook galled out. We had it lubricated before we hung it up in the tree. What type of steel hook will prevent this? The wind spinner is metal and a little heavy.
I’m a not a engineer and recently encountered the term galling in a conference. I found your article during follow-up research on the term. Thank you for a readable explanation of the process!