Steel is widely used in every known industry starting from construction to manufacturing. The worldwide requirement for steel is growing every year. Steel is strong, inexpensive and so versatile that the modern world can not be thought of without Steel. Studies show that after cement, Steel is the second most mass-produced commodity in the world. Steel is environmentally friendly, recyclable, sustainable, and produced in various shapes and forms. In this article, we will learn about the process of steelmaking i.e “How is steel made”?
What is Steel?
Steel is a ferrous alloy material composed of iron and carbon (0.002 to 2.14%) as the primary elements. Many other elements like manganese, silicon, chromium, nickel, phosphorus, oxygen, molybdenum, boron, cobalt, etc can be present or added purposefully to get some required properties. They are used in infrastructure, ships, weapons, railways, buildings, tools, cars, machines, etc. Steel is available in two crystalline forms; body-centered cubic and face-centered cubic. Depending on the alloying constituents the density of steel ranges between 7,750 and 8,050 kg/m3. Steel is ductile, hard, durable, possesses good strength, and can withstand shocks.
How is Steel Made? Steel Manufacturing Process
To produce steel first the iron ore is heated and melted in a furnace. The impurities are then removed from the molten iron. Carbon and other required alloying elements are added to make steel. Modern-day steelmaking is highly improved and specialized. There are two processes that are widely popular for modern-day steelmaking. They are:
- Blast Furnace
- Electric Arc Furnace.
Blast Furnace Steel Production Process
A blast furnace is a huge steel roughly cylindrical shell lined with heat-resistant brick. Steel production in a blast furnace is a continuous process. Hence, once steel manufacturing started, the production continues for years until the refractory lining is damaged or demand dropped. There are two processes by which steel is produced in a blast furnace
- The Bessemer Process for Steel production and
- The Open Hearth Process of Steelmaking
Steel manufacturing Principle of the Bessemer Process
The main raw materials for Steel production in a blast furnace are Iron ore, limestone, coke, and some scrap steel. These materials are charged into the blast furnace from the top and converted into molten pig iron. Next, a current of air is blown through the molten pig iron containing carbon, silicon, and manganese. These elements and some iron are oxidized. The carbon forms gas and escapes, But the oxidized silicon, manganese, and iron form a mixed ferrous-manganese silicate slag. This process is known as the Acid Bessemer Process.
The above oxidation process, especially the oxidation of silicon, produces a large amount of heat. This heat maintains the temperature and fluidity of the molten pig iron. If the content of silicon in the pig iron is very high, the heat evolved may be excessive, and cold steel scraps are added to the converter to lower the temperature.
Once the oxidation is completed, the produced mild steel contains a considerable amount of oxygen and maybe hydrogen which is rectified by spiegeleisen or ferromanganese additions. This is usually done when the metal is poured from the converter into the casting ladle.
All the reactions taking place in the converter are reflected in the flame which issues from the mouth of the converter. During the early part of the blow, when the manganese and silicon are being oxidized, the flame is short and of low luminosity, gradually increasing in length and luminosity as the blow proceeds and the carbon is eliminated. But the flame drops when decarburization is completed, and blowing is discontinued. Any prolongation of blowing after the drop of the flame results in the oxidation of iron and this is indicated by the number of brown fumes in the flame.
In the Basic Bessemer Process, the blowing is prolonged after the flame drops, and this period is known as the after-blow. The phosphorus is removed during the after-blow. The pig iron used in the basic process contains a low silicon and manganese content but is high in phosphorus. It is the oxidation of phosphorus that produces the necessary heat.
The removal of phosphorus necessitates a basic lined converter and a basic slag which is formed from lime added to the converter just before the molten pig iron is poured into it.
The procedure adopted in either the acid or basic process is similar. The molten pig iron is poured into the converter, which is in a horizontal position turned down so that the metal is away from the tuyeres. These tuyeres are fixed in the bottom of the converter and they supply the current of air. The blast is then put on, and the converter is rotated into a vertical position. Immediately the flame drops, the vessel is turned down again and the blown metal is poured into a casting ladle. At this stage, the finishing additions are usually made.
Hence, the process, whether acid or basic, consists of the following three stages:
- A hot metal supply.
- A suitable vessel for blowing the air through the molten pig iron.
- A casting ladle and ingot mold with an auxiliary plant, for teeming the steel into ingot form.
Steel Making Principle by the Open Hearth Process
In the open-hearth process of steel production the slag is the refining medium and serves two purposes:
- It is the oxidizing medium to remove the impurities.
- It works as a receptacle to retain the oxidation products in a stable form.
The raw materials for the acid process are of a siliceous nature, but low in sulfur and phosphorus. The maintenance of an acid slag prevents the elimination of these elements. The pig iron and scrap are charged, and when melted the slag is rendered fluid and oxidized by iron-ore additions. The carbon, silicon, and manganese present in the charge are oxidized by these ore additions. The carbon escapes as carbon monoxide gas, while the silica and manganese oxide passes into the slag, which is virtually a ferrous-manganous silicate.
In the basic process, a wider range of raw materials may be employed. The addition of Limestone forms a basic slag that affects the removal of sulfur and phosphorus. As far as possible, Siliceous materials should be avoided because an excessive lime is required to neutralize the silica formed, and if the slag becomes too siliceous the removal of sulfur and phosphorus is hindered and the basic lining of the furnace is attacked.
In many cases, cold or solid pig iron is charged into the furnace and the process is referred to as “the cold pig and scrap” process. At composite works, where blast-furnace metal is available, molten pig iron is employed. This is referred to as the “hot metal” process. Whether the process is acid or basic, and whether hot or cold pig iron is used, the same type of furnace is employed.
Steel Production by Electric Arc Furnace
In the production of steel, the direct arc resistance electric furnace is employed. In this type of electric arc furnace, the heat is generated by the arcs formed between the electrodes and the charge. The resistance is provided by the charge to the passage of the current. There are two methods of operating the electric arc furnace:
- The basic process.
- The acid process.
The basic process is carried out in a basic lined furnace. The production of high-grade tool steel, alloy, and special steels in ingot form is ideal in the basic process. The basic process is also used for the production of steel castings. On the contrary, the acid process operating with a silica-lined hearth is used chiefly for the production of steel castings.
Basic Process: In the basic electric arc steelmaking process a wide range of steel scrap is employed. The normal steel manufacturing procedure is to melt the scrap, which is recarburized with coke, anthracite, or broken electrodes, to give sufficient carbon at the “melt out” to assure a good carbon boil. As a rule, no pig iron is employed.
Acid Process: Acid-lined electric arc furnaces for steel making have a very limited application and are chiefly employed in steel foundries. Acid furnaces require selected scrap and raw materials low in sulfur and phosphorus. In many foundries, acid furnaces are used for the remelting of the scrap arising in the foundry, whilst basic-lined furnaces are used for converting the miscellaneous brought scrap into low sulfur and phosphorus steel.
The following flowchart by steel.org provides a nice animation of the steel manufacturing processes:
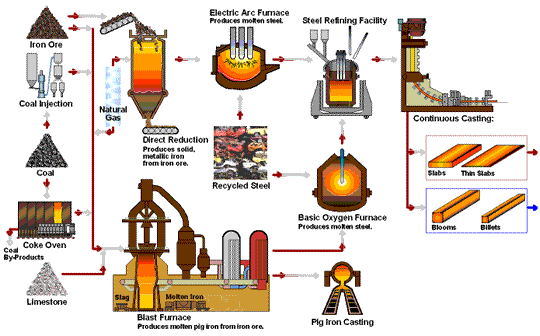
Hey nicely done and written, Surprised with your research. keep going.
Thank you for basic process, The normal steel manufacturing procedure is to melt the scrap, which is rebarbarized with coke, anthracite, or broken electrodes, to give sufficient carbon at the “melt out” to assure a good carbon boil.
clear to the point i have understood the process thank you
What are the major & minor factors that determine the Price of Steel Sales Price —
Its basically quality of material nd demand in the market..