Uhm, is it about music? That’s what people ask us! Every time I tell people my profession, I am asked “What is Instrumentation Engineering?” So let’s get you through it.
By definition, Instrumentation Engineering is a branch that examines the measurement and control of different parameters and the systems associated with them.
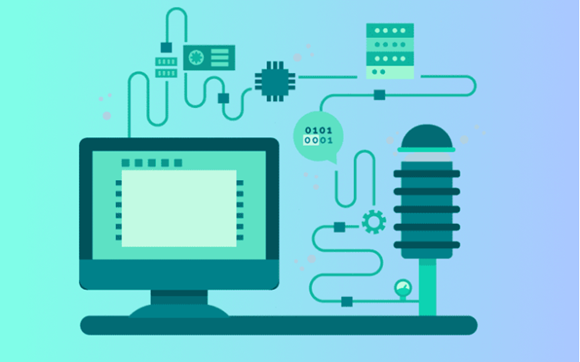
To put it simply, let me say that the perfect example of Instrumentation is our body. One such specific example is how our body regulates temperature.
For us to stay healthy our body temperature must range between 970 F and 990 F. So obviously, someone is constantly monitoring this temperature and maintaining it.
But who is it?
A controller. Its job is to continuously match the measuring value with a set point and then give a corrective output to meet our requirements. In our case, the hypothalamus is the controller here that regulates our body temperature.
Let’s see how.
A hot environment causes the hypothalamus to send signals to the sweat glands, causing you to sweat and cool off. And in the opposite case, when you feel cold, it sends signals to your muscles that create warmth.
Similarly, in any chemical process or power plant, there are a lot of parameters that have to be measured and controlled effectively to obtain the desired results.
As in our body, we have Temperature, BP, Sugar, etc.
In industries, we need to pay attention to the parameters mentioned below to gain effective control and obtain the desired product.
- Flow
- Level
- Pressure
- Temperature
- Analyzers
Components of Instrumentation
As the term “Instrumentation” starts with Instruments, Let’s first define it.
An instrument is a device that helps in measuring any of the process parameters. Valves, Thermocouples, Transmitters, Analyzers, etc are typical examples of instruments. These instruments become an essential part of instrumentation and control system design in process and power plants. For monitoring and controlling the system behavior, engineers are dependent on the values displayed in such instruments
There are three main components in any Instrumentation cycle that perform the activity of maintaining and controlling the process parameters effectively are :
- Sensor
- Controller
- Final Control Element
Instrumentation is basically the application of instruments for an experiment, measure, and control of pressure, temperature, flow, density, velocity, force, pH, humidity, or any other process variable of a properly defined system.
Each parameter can be measured through a sensor that is based on different principles and can be selected based on the process application.
Let us first clarify the concept of the sensor.
Sensors are devices that convert physical energy into electrical energy. Sensors are used in our day-to-day life as well eg. Gyser, thermometer, etc.
The most important role of an Instrumentation Engineer is to select the right sensor for the right application. And this depends on many factors like
- What is the service of the measuring medium?
- What is the desired output?
- What is the transmission mode required?
- Whether it has to be contact or non-contact type?
- What kind of principle best suits our needs?
And much more.
The next step after the sensor comes the transmitter. There’s a very thin line between sensors and transmitters which most people tend to overlook.
As said before, Sensors are devices that convert physical energy into electrical energy. Transmitters are devices that convert the electrical signal into the standard instrumentation signal which is 4-20ma.
Transmitters and sensors usually come in a single assembly that measures and transmits a signal based on its specifications.
The signal from the sensor is sent to a controller system, like PLC/ DCS. These systems are the brain of the process which are fed with formulas to generate desired outputs.
A set point i.e the desired value of a specific parameter is given to this controller. The controller then compares it with the value that is being measured by the sensor.
Based on the difference between the measuring value and the set point, the controller generates a corrective output.
This output is sent to a final control element which takes corrective measures to match the set point given by the user and the value being measured by the sensor.
In a control system, a final control element is a mechanical device that changes a process to match the setpoint and measuring value. Eg, Valves, Dampers, Gates.
This cycle must go on continuously to get the desired product.
Apart from getting the desired output and production levels, what an Instrumentation Engineer needs to look after is the Safety of the Plant.
Not taking proper care of the systems and neglecting the safety norms can lead to an event like Bhopal Gas Tragedy.
Even though everything works in an automated process, it is very important to understand the catastrophic losses if the automated system suddenly stops working.
There have to be enough interlocks, safety alarms, and safety trips included in the system to avoid instrument and human errors.
A HAZOP study – Hazard and Operateblitly Study is performed by a group of professionals including Process Engineers, Instrumentation Engineers, and Safety Engineers to ensure the levels of safety required in a process plant before the designing of the plant is started.
Along with HAZOP, there are different studies like LOPA, Intrinsic Calculations, etc which take place after HAZOP.
This was a brief introduction to what Instrumentation Engineering is. Every topic mentioned here has its own roots and shall be explained in-depth in the upcoming articles.
Example of Instrumentation
Let us try to understand what we read above with an example.
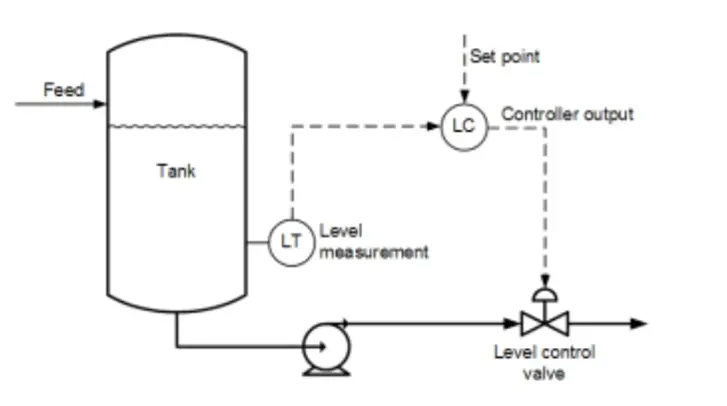
Assume that you have a tank whose level has to be maintained in such a way that the water in the tank must not go above 75% of the height of the tank.
Now, as in this picture (Fig. 2), we mounted a level sensor on the top of the tank. This sensor will be calibrated in such a way that it will sense when water reaches the desired set point.
Here the set point is 75% of the tank. As the water reaches the desired set point, it will send a signal to the controller.
The controller will now generate a corrective output and send it to the final control element which is the valve in this case.
As the water is more than the setpoint, the valve will now open and the water in the tank will drain out until it is below 75% of the tank height. This will continue as the water level fluctuates in the tank.
There are many ways to optimize the process below, which we’ll learn in the upcoming articles.
Hence, broadly, Instrumentation engineering is a specialization engineering branch for studying the basics of measuring instruments used in the design and configuration of automated systems in electrical, electronics, and pneumatic domains, etc. The majority of instrumentation engineers work in industries for automation and control of processes. Instrumentation and control systems optimize systems for increased productivity, reliability, safety, and stability. Several devices like microprocessors, microcontrollers, or PLCs are used to measure and control the system parameters.
Thank you for reading! Share your thoughts on this post in the comments section below! Let me know what you’d like to learn more about!
Picture Credits:
- https://leverageedu.com/blog/electronics-and-instrumentation-engineering/
- https://www.dataforth.com/tuning-level-control-loops.aspx
Thanks for the valuable information. Loved it
Good Morning
Can you please help me find a Work Integrated Learning / In-service training in Instrumentation to obtain my diploma, I have completed S4 in Electrical Engineering (Process Instrumentation).
Phone no: 065 970 8638
Thank you
Thank you for this valuable content.
Nice Post! Instrumentation Engineering involves the design, development, and maintenance of instruments used to measure and control various industrial processes. It encompasses components like sensors, transmitters, and controllers to gather data and manage systems efficiently. For instance, in a chemical plant, instrumentation engineers might deploy pressure sensors and temperature controllers to monitor and regulate reactions, ensuring optimal conditions and enhancing overall productivity.