Level measurement is a process of measuring/monitoring the fluid level within equipment (i.e. Vessel, Reactor, and Storage Tanks). Level measurement may be a Point level or continuous type which can be achieved with the help of a sensing element called the sensor.
Objectives of Level Measurement
There are several technologies available in the instrumentation Industry, Level Measurement is an essential activity in process engineering. The main objectives of level measurement are below mentioned with the possibility of Zero error.
- Online level measurement means a digital display of output data for alarm, trip, and record data as well.
- Increases process Efficiency
- Tackle or avoid Safety Related incidents
Types of Level Measurement
Level measurement techniques are mainly classified into two categories which are the following:
- Point Level measurement
- Continuous Level measurement
These two classifications of level measurement sensors are briefly described below:
Point Level Measurement:
Point level Measurement referred to as the instrument will produce the output or measure value when the level reaches a certain level (up to or greater than the Sensing element of the Level Instruments) within the equipment. Selected media (fluid type) used for level may be liquid, solid, or slurry.
Examples of Point level measurement sensors: Capacitance, Conductivity, Tuning fork
Level Indication basis in Point level measurement: This type of measurement detects high/low-level points where high is set to keep the equipment safe from future overfilling incidents & low to keep the plant safe from downtime.
Types of Point level measurement techniques:
Working of capacitance type sensor:
Capacitance-type sensors are rod-shaped like level measurement which is inserted from the top of the equipment. This type of level sensor works over the principle of change in capacitance.
Capacitance is directly dependent upon the amount of Fluid present within the Equipment. The thermal capacitance of process fluid gradually increases as the level inside the equipment increases and vice versa. Installation of this type of sensor is usually top-mounted.
Advantages of Capacitance type sensor:
- Suitable for liquid & solids.
- Cost-effective solution
- Used for Viscous media
- No mechanical or moving parts
- Small in construction
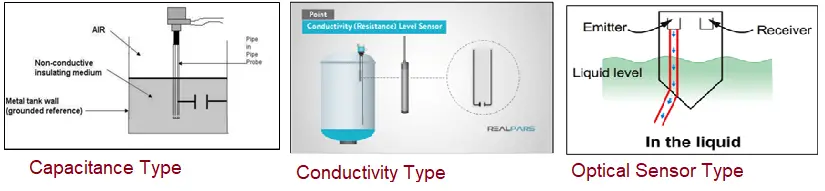
Working of Conductivity type sensor:
This type of sensor is also rod-shaped consisting of a pair of electrodes with the probe. An alternating current from an external source is supplied to the sensor. When the fluid level inside the equipment reaches up to the sensor, supplied alternating current helps to complete the circuit which causes current to flow. Thus fluid levels are calibrated from the output current value. Installation of this type of probe switch is usually top-mounted.
Advantages of Conductivity type sensor:
- Available at low cost
- Easy to use
- No mechanical or moving parts
Working of Optical type level sensor:
Working of optical type level sensors based on the emission of infrared light towards the application media. The principle used by the optical type level sensor is total internal reflection.
IR Light is emitted from the LED source called the sender, and the source which collects back IR light is called the receiver this all activity takes place within a prism arrangement. As emitted IR light from the sender gets absorbed or reflected in the application media, thus remained IR light is sent back to the receiver. Reflection of the IR light helps to detect the present liquid level.
Advantages of Optical type level sensor:
- Compact Size
- No Moving
- Inexpensive & Effective Solution
Working of Tuning fork type sensor:
Tuning forks have been used in level measurement since the 1970s. The working principle of the fork sensor is dependent on the application media which completely uses vibrations.
Case-I (Applicable for solid Media): The amplitude of the Vibration principle is used in the case of solids where a fork continuously vibrating at constant intervals gives an amplitude value let’s say X, this amplitude value acts as the threshold value.
When the solid material present inside the equipment contacts with the vibrating fork, the oscillation of amplitude gets changed from X. When this amplitude value goes below X which is the threshold value with the help of an inbuilt electronics system causes changes in output (Calibration or calculation of media level).
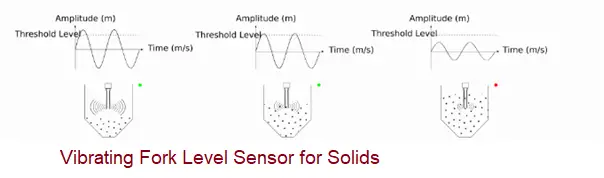
Case-II (applicable for liquid media): The principle is used “Frequency of operation” the in which frequency threshold value is generated due to the vibration of the tuning fork.
The natural Frequency of the fork gets reduces when the liquid media increases inside the equipment. Level measurement is calibrated in the condition when the natural frequency matches the threshold frequency.
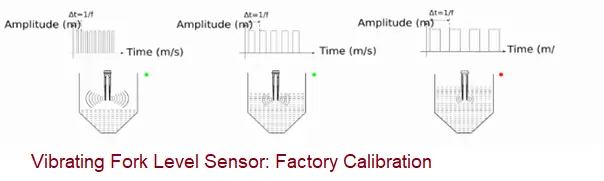
Advantages of tuning fork type level sensor:
- Compatible with high-temperature fluid
- Not affected by the flow behavior (i.e. turbulence, foaming, etc.)
- Small in size & easy to installation
Continuous Level Measurement:
Continuous Level measurement refers to the measurement in which media is present in the equipment from the ground level to the peak (top) Level. Continuous Level measurement can be used for liquid or solids.
Level Indication basis in Continuous Level monitoring: In this type of level measurement, each output value changes as fluid rises or down. The set Point can be decided from the range measured.
Types of continuous-level measurement techniques:
Working of Ultrasonic level sensor:
Ultrasonic type level sensor working principle based on the ultrasonic waves. Ultrasonic waves are emitted by the head of the sensor which is passed through the fluid media and finally gets received by the receptor of the sensing element after striking the bottom surface of the equipment. The time difference between ultrasonic wave emission & reception is used to calculate the distance (i.e. level). Ultrasonic waves used are sound waves for level measurement.
The level can be calculated by the equation:
Distance L = 1/2 × T × C
Where,
- T is the time difference between the emission & reception of waves (1/2 is used in the equation for wave travel for both emission & reception path).
- C is sonic speed
- L is distance
Advantages of Ultrasonic level sensor:
- The sensing element does not come in direct contact with application media
- Low cost-effective solution
- Not affected by the environmental condition (moisture, high ambient temperature)
Working of Radar type level sensor:
The radar-type level sensor working principle remains the same as in the ultrasonic-type level sensor case. Radio waves are responsible for level measurement instead of sound waves used in the ultrasonic-type level sensor. Radio waves are released from the antenna which is placed at the top of the equipment after striking the bottom surface these returned signals are received by the antenna as well.
Level measurement is achieved by the time difference between emission & received signals.
Advantages of Radar type level sensor:
- Non-contact type with application media
- Gives high-accuracy measurements.
- Suitable for vacuum & high-pressure applications.
Working of DP Type level sensor:
This type of level sensor work on the pressure difference. Two sensors are placed at low-pressure & High-pressure regions. The level is measured from the equation
Pressure = Density of fluid * acceleration due to gravity * Height
Rearranging equation;
Height = Pressure / (Density of fluid * acceleration due to gravity)
The density of process fluid remains constant for an accurate result.
Advantages of DP Type level sensor:
- Easy to install & removal
- High accuracy
- Easy maintenance & testing (block valves provided to keep instrument isolated from process fluid).
Causes / Impacts of Incorrect Level Measurements
- Case – I: If the measured level is lower than the actual level. It may produce an impact on the equipment (may damage).
- Case – II: If the measured level is High than the Actual level. Safety (instruments with their alarm, trip interlocks) & environmental Norms or standards are halted.