Nitrogen tanks, also known as nitrogen cylinders or nitrogen bottles, are containers specifically designed to store and transport nitrogen gas in its compressed form. Nitrogen is an odorless, colorless, and inert gas that is widely used in various industries and applications for a quite long time.
Nitrogen tanks are typically made of high-strength steel or aluminum alloy to withstand the high pressure generated when the gas is compressed. These tanks come in different sizes and capacities, ranging from small portable cylinders to large stationary tanks. The size and design of the tanks depend on the intended use and the amount of nitrogen required.
Nitrogen gas is often used in industries such as manufacturing, electronics, rubber, healthcare, food processing, mining, automotive, chemical, and aerospace. It is utilized for a variety of purposes, including purging, inerting, blanketing, and pressurizing. For example, nitrogen is commonly used to displace oxygen and moisture in sensitive manufacturing processes or to prevent the oxidation and spoilage of food products.
When using nitrogen from a tank, a regulator or pressure-reducing valve is attached to control the flow and pressure of the gas. This ensures that the nitrogen can be safely and accurately released for the intended application. It’s important to handle nitrogen tanks with care and follow proper safety guidelines, as they contain highly pressurized gas. Regular inspections, maintenance, and adherence to safety procedures are crucial to prevent accidents and ensure the safe handling of nitrogen. Various codes and standards including AMME, NFPA, CGA, ISO, DOT, etc provide guidelines for nitrogen tanks.
Why Store Nitrogen?
Storing nitrogen serves several important purposes across various industries and applications. Here are some common reasons for the storage of nitrogen:
Inerting: Nitrogen is an inert gas, meaning it does not easily react with other substances. This property makes it useful for inerting applications, where it is used to displace or reduce the presence of oxygen. By introducing nitrogen into a storage or processing environment, oxygen levels can be lowered, reducing the risk of oxidation, combustion, or degradation. Inerting is often employed in industries such as oil and gas, chemical manufacturing, and pharmaceuticals.
Blanketing: Nitrogen is used to create a protective atmosphere or nitrogen blanket over sensitive materials or substances. By filling a storage container or vessel with nitrogen, it can act as a barrier between the material and the surrounding air, preventing contact with oxygen and moisture. This is commonly done to protect perishable goods, such as food products, chemicals, and pharmaceuticals, from degradation, spoilage, or contamination.
Pressurizing: Some applications require the use of pressurized nitrogen gas. Nitrogen tanks provide a convenient and portable solution for storing and delivering compressed nitrogen. Pressurized nitrogen is used in various industrial processes, such as pneumatic tools, gas-assisted injection molding, and as a propellant in aerosol cans.
Laboratory and research applications: Nitrogen is extensively used in laboratories for a wide range of applications. It is often needed for sample storage, preservation, or as a carrier gas in gas chromatography. Storing nitrogen in tanks ensures a readily available and reliable source of this gas for laboratory operations.
Emergency backup: In critical systems or facilities where the interruption of gas supply can have serious consequences, storing nitrogen provides a backup or contingency plan. For example, in hospitals, nitrogen is often stored in tanks to support medical gas systems, ensuring a continuous supply of essential equipment such as ventilators or cryogenic storage.
In general, nitrogen is stored in its liquid form which calls for cryogenic needs. Fig. 1 below shows some typical nitrogen tanks.
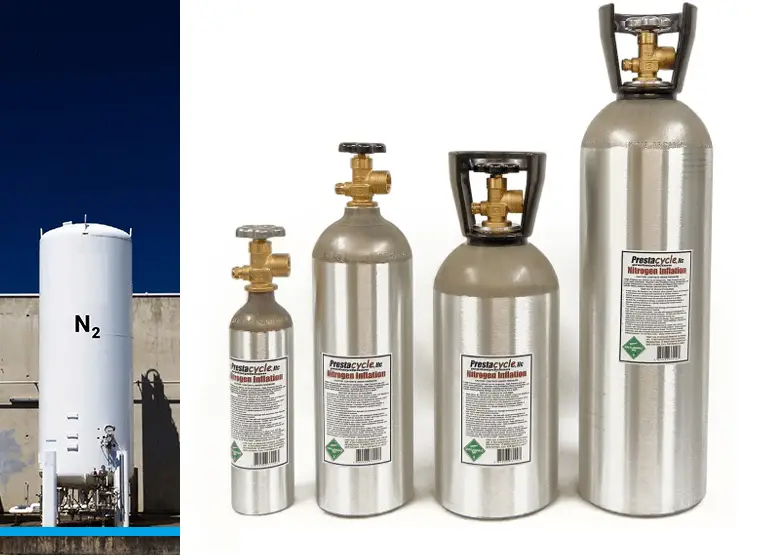
Liquid Nitrogen Tank
A liquid nitrogen tank, also known as a cryogenic tank or dewar, is a specialized container designed for the storage and transportation of liquid nitrogen. Unlike nitrogen gas stored in compressed gas cylinders, liquid nitrogen is extremely cold and maintained at a temperature of -196 degrees Celsius (-320.8 degrees Fahrenheit) at atmospheric pressure.
Liquid nitrogen tanks are constructed with materials that can withstand extremely low temperatures and prevent heat transfer from the environment. The tanks are typically double-walled or vacuum-insulated, which creates a thermal barrier to minimize heat exchange and maintain the low temperature of the liquid nitrogen inside.
Components of a Liquid Nitrogen Tank
The main components of a liquid nitrogen tank include:
- Inner Vessel: This is the innermost chamber that holds the liquid nitrogen. It is usually made of stainless steel or aluminum alloy and is designed to safely contain extremely cold liquid.
- Vacuum Space: Surrounding the inner vessel is a vacuum space that acts as insulation to minimize heat transfer. It prevents the entry of external heat and reduces heat conduction, convection, and radiation.
- Outer Jacket: The outer jacket is the outermost layer of the tank, made of a durable material such as steel or aluminum. It provides structural support and additional insulation to maintain the low temperature inside the tank.
- Pressure-Building Valve: Liquid nitrogen tanks are equipped with a pressure-building valve to allow controlled venting of gas that evaporates from the liquid nitrogen. This valve helps maintain the appropriate pressure within the tank.
Liquid nitrogen tanks are commonly used in various applications, including scientific research, cryogenic storage, medical facilities, and industrial processes. They provide a reliable and efficient method for storing and accessing liquid nitrogen, which is utilized in areas such as cryopreservation, cryosurgery, cryogenic cooling, and cryogenic testing.
Safety precautions must be followed when handling liquid nitrogen tanks, as the extremely cold temperature can cause frostbite and pose other hazards. Proper training and protective equipment are necessary to ensure safe operation and prevent accidents. If the liquid nitrogen is not handled and stored properly, it can cause cold burns or can cause explosions due to pressure built up.
Liquid nitrogen tanks provide several advantages including:
- Easy Accessibility for Medical Purposes
- Ease of Transportation and Loading Process
- No contamination
- Efficient operation
- Temperature preservation
Nitrogen Tank Sizes
Nitrogen tanks come in various sizes and capacities to cater to different needs and applications. The size of a nitrogen tank is typically determined by its capacity to hold compressed nitrogen gas, which is measured in cubic feet (ft³) or liters (L). Here are some common nitrogen tank sizes:
Small Portable Tanks:
These tanks are typically lightweight and easy to transport. They are often used for smaller-scale applications or for portable nitrogen supply. Common sizes include:
- 20 cubic feet (ft³) or 580 liters (L)
- 40 cubic feet (ft³) or 1,160 liters (L)
- 80 cubic feet (ft³) or 2,270 liters (L)
Intermediate Tanks:
Intermediate-sized tanks are suitable for moderate nitrogen requirements or for situations where a larger supply is needed but portability is not a major concern. Examples include:
- 125 cubic feet (ft³) or 3,540 liters (L)
- 180 cubic feet (ft³) or 5,090 liters (L)
- 250 cubic feet (ft³) or 7,080 liters (L)
Large Stationary Tanks:
These tanks are designed for stationary applications where a substantial nitrogen supply is required. They are commonly used in industrial settings or facilities with high nitrogen consumption. Sizes can range from a few hundred cubic feet to several thousand cubic feet.
- 500 cubic feet (ft³) or 14,160 liters (L)
- 1,000 cubic feet (ft³) or 28,320 liters (L)
- 3,000 cubic feet (ft³) or 84,960 liters (L)
It’s important to note that the specific sizes and capacities of nitrogen tanks may vary depending on the manufacturer and regional standards. When selecting a nitrogen tank, it’s essential to consider factors such as the required nitrogen volume, available space, portability needs, and the intended application to ensure the right size is chosen for the task at hand.
Materials for Nitrogen Tanks
Nitrogen tanks are typically made from materials that possess high strength and can withstand the high pressure generated by compressed nitrogen gas. The two most common materials used for nitrogen tanks are:
- Steel: Steel tanks are widely used for nitrogen storage due to their strength, durability, and ability to handle high-pressure applications. The steel used is often a high-strength alloy, such as chrome-molybdenum steel or aluminum-lined steel, which provides excellent resistance to rupture or deformation. Steel tanks are suitable for both portable and stationary nitrogen storage.
- Stainless Steel: Stainless steel is a commonly used material for the construction of liquid nitrogen tanks. It offers excellent strength, durability, and resistance to corrosion. The stainless steel used for cryogenic applications is typically low-temperature grades, such as 304 or 316 stainless steel, which can maintain their mechanical properties and integrity at very low temperatures. Stainless steel tanks provide reliable storage for liquid nitrogen and are often used in laboratory, medical, and industrial settings.
- Aluminum Alloy: Aluminum alloy tanks are another popular choice for nitrogen storage, particularly in applications where weight is a concern. Aluminum is lightweight and corrosion-resistant, making it suitable for portable nitrogen cylinders. Aluminum alloy tanks are commonly used for smaller-sized nitrogen cylinders, such as those used in laboratories or for portable nitrogen supply.
Both steel and aluminum alloy tanks undergo rigorous testing and certification processes to ensure their safety and compliance with industry standards. These tanks are designed to withstand high-pressure conditions and are equipped with safety features, such as pressure relief valves, to prevent over-pressurization.
It’s worth noting that the choice of material for a nitrogen tank may depend on factors such as the required capacity, portability needs, regulatory requirements, and specific industry standards. Manufacturers and suppliers can provide detailed information on the material composition and specifications of their nitrogen tanks to help customers select the appropriate option for their intended application.
Nitrogen Tank Price
The price of a nitrogen tank can vary depending on several factors, including the tank size, material, manufacturer, region, and any additional features or accessories included. Here are some approximate price ranges for nitrogen tanks:
- Small Portable Tanks: Smaller nitrogen tanks with capacities ranging from 20 cubic feet (ft³) to 80 ft³ can cost between $50 and $200.
- Intermediate Tanks: Intermediate-sized nitrogen tanks with capacities between 125 ft³ and 250 ft³ may range in price from $200 to $500.
- Large Stationary Tanks: Larger stationary nitrogen tanks with capacities of 500 ft³ or more can cost several thousand dollars, depending on the size and specifications. Prices can range from $1,000 to $10,000 or more.
It’s important to note that these price ranges are estimates and can vary significantly based on market conditions, location, and other factors. Additionally, prices may differ between different suppliers or manufacturers.
Dear Sir,
thanks for the previous piece of writing that includes good data.
There are some questions however as follows:
1.For big tanks/dewars what is the routine material of outer tank. In my humble opinion it must be again SS. However some manufacturers come up with CS as 516 Gr.60/70. It is OK then?
2. as far as the supporting system is mainly of outer vessel, how the inner and outer vessel are connected to each other to maintain the gap for insulating material and then to bear the load like seismic loads what else.
3. The interconnecting pipes between inner and outer vessel deemed to have loops to accept expansions/contractions. do you have any data on how this fact is being managed. Expansion joint seems not to be safe application here.
Milion thanks in advance if you good give me good vista of it.