Normalizing is a widely popular heat treatment process for metals to increase ductility and toughness. This heat treatment is also known as normalizing annealing as the normalizing heat treatment process is very similar to annealing treatment. In this article we will learn more about normalizing; its definition, purposes, process steps, applicability, normalizing vs annealing, etc.
Normalizing Definition/ What is normalizing?
Normalizing is defined as a heat treatment process where a material is heated to a predecided elevated temperature, hold at that temperature for a certain period of time (usually 10-20 minutes), and then allowed to cool freely in the air to reach room temperature. The normalizing process is usually applied to metals that have been subjected to thermal or mechanical hardening processes and require their microstructure to be normalized. After normalizing, the metal gets back its ductility and the hardness is reduced.
Metals Suitable to be Normalized
For the normalizing treatment of a metal, it must be receptive to normalizing. Various metals and alloys are suitable to be normalized like
- Iron-based alloys like Carbon steel, stainless steel, alloy steel, cast iron, etc.
- Nickel alloys
- Copper
- Aluminum
- Brass
Purpose of Normalizing
The main purposes of the normalizing heat treatment on metals are:
- To remove structural irregularities or impurities and defects from the metal.
- To improve ductility that has been lost in some metal processing.
- To reduce the hardness that has been increased by mechanical or thermal hardening processes.
- To increase the toughness of the metal.
- To relieve internal stresses.
- To get an improvement in machinability.
The Normalizing Process
Similar to annealing the normalizing process also follows three main stages; the Recovery stage, the Recrystallization stage, and the grain-growth stage. In the recovery stages of normalizing, the internal stresses are relieved by heating the material. Then the metal is heated to elevated temperatures above the recrystallization temperature of the metal where new grains are formed. Finally, in the grain growth stage of normalization, the grains develop fully when the material is cooled by air.
Applications for Normalizing
Normalizing treatment finds broad practical applications across several industries like Aerospace, Automotive, Heavy Equipment, Energy, Agriculture, Oil & Gas, etc. Usually, whenever metal is expected to get high residual stresses due to some kind of manufacturing steps, it is always suggested to normalize the metal using the normalizing heat-treatment process. A few examples include:
- Carbon steel is normalized when it is cold-rolled to reduce brittleness and increase ductility.
- After work hardening of ferritic stainless steel stampings in the automotive industry, they are normalized to regain their mechanical properties.
- After the thermal microstructure alteration during welding in nickel-based alloys in the nuclear industry, normalizing is performed.
Normalizing Steel
Steel normalizing is a heat treatment process performed after rolling, welding, or forging processes to refine the distorted grains in the microstructure. The normalizing process of steel involves the following steps:
- Steel is heated to about 40-500C (Refer to Fig. 1) above the upper critical temperature (A3 or Acm).
- The alloy is then held at that temperature for around 10-20 minutes.
- Cooling it in still or slightly agitated air to bring back to room temperature.
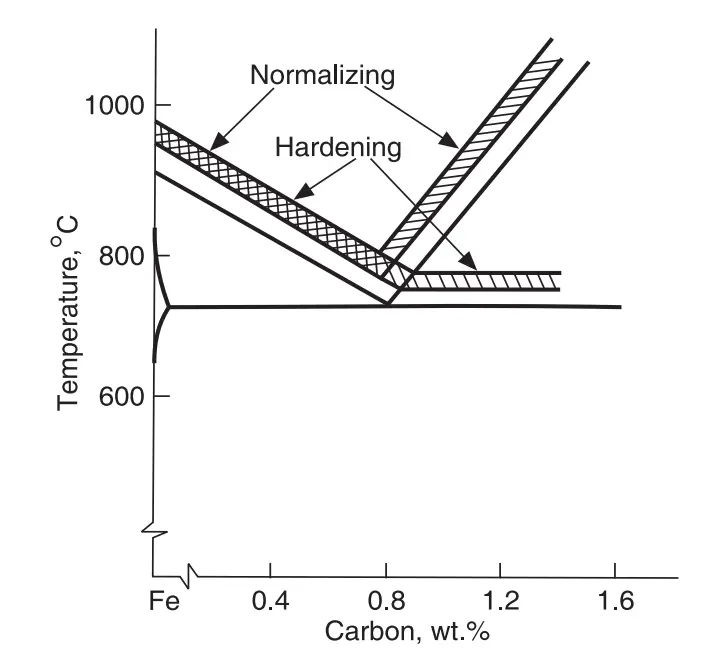
After normalizing, the resultant microstructure is usually perlite. The grain size in normalizing steel is governed by the section thickness. A variation in grain size is observed as the cooling rate varies from the case to the core. The normalizing temperature of steel varies with the carbon content as is clear from Fig. 1. The following table (Table 1) provides recommended normalizing temperatures for steel.
Carbon % | 0.1 | 0.2 | 0.3 | 0.4 | 0.6 | 0.8 | 1.0 | 1.1 | 1.2 |
Temperature, 0C | 920 | 900 | 880 | 860 | 840 | 820 | 830 | 900 | 925 |
Difference between Normalizing and Annealing
Even though the process steps for normalizing and annealing are almost similar there are specific differences between normalizing and annealing. The differences between annealing and normalizing are provided below in a tabular (Table 2) format.
Normalizing | Annealing |
The cooling rate in normalizing is faster than annealing. | Slower cooling rate as compared to normalizing. |
Slow cooling in room temperature. | Controlled slow cooling in a furnace. |
Mechanical Strength and hardness of normalized components are more. | Strength and hardness are lower as compared to the normalized parts. |
Machinability is more improved in normalizing. | Annealed product is soft and thus can stick to the machine during machining. |
Slightly less ductility. | More ductility. |
Less expensive | Comparatively costly |
The image in Fig. 2 shows the typical differences in nominal strength between Normalized and Annealed steel.
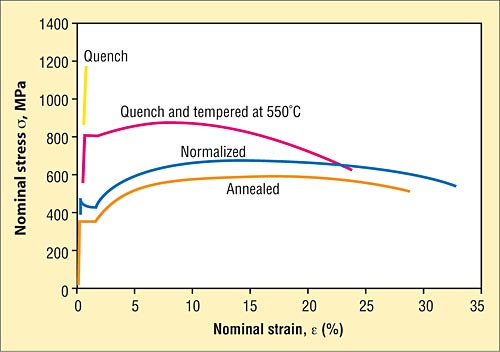
Kindly send this staff as PDFs..
Hi sir. This material is good
what will be the range of cooling rate of normalizing? For to say 300 C/hr, 500 C/hr, or 1000 C/hr, which one
Thank you for shared.
thanks
good work please i thank you people for giving us clear detailed information