Vibration measurement is the process of quantifying the magnitude, frequency, and direction of oscillatory motion in a physical system. This can be done using various sensors, such as accelerometers, to measure the vibrations in a particular object or structure.
Vibration measurements are important in a variety of industries, including automotive, aerospace, and civil engineering, as excessive vibration can cause damage to machinery and structures over time. By measuring vibrations, engineers and technicians can identify potential problems early on and take corrective actions to prevent further damage or failure.
Vibration measurements are typically analyzed using tools such as signal processing and spectral analysis to identify the root cause of the vibrations and develop solutions to mitigate them.
Requirements for Vibration Measurement
There are several reasons why we need to measure vibration:
- Prevent damage: Excessive vibration can cause damage to machinery and structures over time. By measuring vibrations, engineers and technicians can identify potential problems early on and take corrective actions to prevent further damage or failure.
- Improve performance: Vibration measurements can help engineers and technicians identify opportunities to improve the performance of a system. For example, by identifying the source of unwanted vibrations, they can make design changes or adjustments to reduce or eliminate those vibrations, which can lead to improved performance and efficiency.
- Ensure safety: Vibrations can be hazardous to human health, and in some cases, can cause injury or even death. By measuring vibrations, engineers and technicians can ensure that structures and equipment are safe for people to use and operate.
- Meet regulatory requirements: In some industries, there are regulatory requirements for vibration levels in equipment and structures. By measuring vibrations, engineers and technicians can ensure that they meet these requirements and avoid any legal or financial penalties.
Overall, vibration measurement is essential in many industries to ensure the safe, reliable, and efficient operation of machinery and structures
How is Vibration Measured?
Vibration can be measured using a variety of techniques, but the most common method is through the use of sensors called accelerometers. Accelerometers are devices that measure the acceleration of a vibrating object, which can then be used to calculate the vibration amplitude and frequency.
Accelerometers are typically attached to the surface of the object being measured using adhesive or mounting screws. They can be designed to measure vibration in one, two, or three dimensions, depending on the nature of the vibration being measured.
Once the accelerometer is attached to the object, it produces an electrical signal that is proportional to the acceleration of the object. This signal is then amplified and filtered to remove any noise or interference and then recorded or displayed on a computer or other data acquisition system.
Vibration measurements can be analyzed using various tools and techniques, including time-domain analysis, frequency-domain analysis, and statistical analysis. These techniques help engineers and technicians identify the characteristics of the vibration, such as the frequency, amplitude, and direction, and develop appropriate solutions to address any issues.
Measured vibration data can be used in several ways depending on the application and the specific parameters being measured. Here are some common ways to use vibration data:
- Maintenance and monitoring: Vibration data can be used to monitor the condition of machinery and equipment (Learn more about vibration monitoring by clicking here) and to detect any changes in vibration that may indicate equipment failure or performance degradation. This helps to minimize downtime, improve equipment reliability, and optimize maintenance schedules.
- Design and testing: Vibration data can be used in the design and testing of mechanical systems and structures to ensure that they are safe, durable, and reliable under various environmental and load conditions.
- Performance optimization: Vibration data can be used to optimize the performance of machinery and equipment by identifying areas where vibration levels are high and implementing changes to reduce or eliminate the sources of vibration.
- Quality control: Vibration data can be used in quality control processes to ensure that products meet the required specifications and do not have any defects or issues related to vibration.
- Research and development: Vibration data can be used in research and development projects to better understand the behavior and performance of mechanical systems and structures under various conditions.
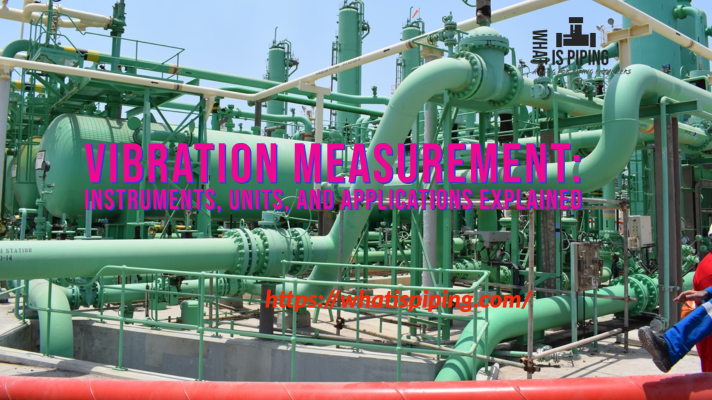
Unit of Vibration Measurement
The unit of vibration measurement depends on the specific parameter being measured. The most common unit of vibration measurement is acceleration, which is typically measured in meters per second squared (m/s2) or g’s (where 1 g = 9.81 m/s2).
Other common units of vibration measurement include:
- Velocity: measured in meters per second (m/s) or inches per second (in/s)
- Displacement: measured in meters (m) or inches (in)
- Frequency: measured in Hertz (Hz) or cycles per second (CPS)
Each of these units represents a different aspect of the vibration being measured. Acceleration measures the rate of change of velocity, velocity measures the rate of change of displacement, and displacement measures the amount of movement from a stationary position. Frequency represents the number of oscillations or cycles per unit of time.
It’s important to note that the unit of vibration measurement will depend on the specific application and the parameters being measured. Engineers and technicians will choose the appropriate unit of measurement based on the requirements of their particular application.
How to Quantify Vibration?
There are several ways to quantify vibration, depending on the specific application and the parameters being measured. Here are some common methods:
- Amplitude: Amplitude is the measure of the maximum displacement, velocity, or acceleration of a vibrating object from its equilibrium position. It is typically measured in units such as meters (for displacement), meters per second (for velocity), or meters per second squared (for acceleration).
- Frequency: Frequency is the number of oscillations or cycles per unit of time. It is typically measured in units such as Hertz (Hz) or cycles per second (CPS).
- Power Spectral Density (PSD): PSD is a measure of the distribution of energy across different frequencies in a vibration signal. It is typically expressed in units such as g^2/Hz, where g is the acceleration due to gravity.
- Root Mean Square (RMS): RMS is a measure of the average energy of a vibration signal over time. It is typically expressed in units such as g (for acceleration) or mm/s (for velocity).
- Crest Factor: The crest factor is the ratio of the peak amplitude of a vibration signal to its RMS value. It is typically used to assess the severity of high-frequency vibration signals.
- Kurtosis: Kurtosis is a measure of the peakedness of a vibration signal. It is typically used to assess the presence of high-frequency or impulsive vibration signals.
Vibration Measurement Instruments
There are several types of instruments used to measure vibration. Each vibration measuring tool has its own limitations and so it must be carefully selected. The most common instruments include:
- Accelerometers: Accelerometers are the most commonly used instruments for measuring vibration. They measure the acceleration of a vibrating object, which can then be used to calculate the vibration amplitude and frequency.
- Velometers: Velometers measure the velocity of a vibrating object. They are typically used to measure low-frequency vibrations.
- Displacement probes: Displacement probes measure the displacement of a vibrating object. They are typically used to measure high-frequency vibrations.
- Proximity probes: Proximity probes measure the distance between a vibrating object and a stationary surface. They are typically used to measure the vibration of rotating machinery.
- Laser vibrometers: Laser vibrometers use laser beams to measure the vibrations of an object without physical contact. They are typically used to measure vibrations in delicate or hard-to-reach objects.
- Tachometers: Tachometers measure the rotational speed of a shaft or motor. They are typically used to measure the vibration of rotating machinery.
- Spectrum analyzers: Spectrum analyzers are used to analyze the frequency content of a vibration signal. They are typically used to identify the source of unwanted vibrations and develop appropriate solutions.
Applications of Vibration Measurement
Vibration measurement has a wide range of applications across various industries. Here are some examples:
- Industrial machinery: Vibration measurement is commonly used in the maintenance and monitoring of industrial machinery to detect any changes in vibration that may indicate equipment failure or performance degradation. This helps to minimize downtime, improve equipment reliability, and optimize maintenance schedules.
- Aerospace: Vibration measurement is critical in aerospace applications, where it is used to monitor the structural integrity of aircraft components and ensure that they remain within safe limits during operation.
- Automotive: Vibration measurement is used in the design and testing of automobiles, where it is used to evaluate the ride comfort of the vehicle and to detect any potential issues with the suspension or steering systems.
- Civil engineering: Vibration measurement is used in civil engineering applications, such as bridge and building design, to ensure that structures are safe and stable under various environmental and load conditions.
- Medical devices: Vibration measurement is used in the development and testing of medical devices, such as surgical instruments and implantable devices, to ensure that they operate within safe limits and do not cause harm to patients.
- Consumer electronics: Vibration measurement is used in the design and testing of consumer electronics, such as smartphones and laptops, to ensure that they are durable and reliable under various usage conditions.
- Oil and Gas Industries
Industry Standards for Oil and Gas Vibration Measurement
There are several industry standards for piping vibration measurement, including:
- API 618/API 674 – This standard specifies the vibration limits for reciprocating compressors and pumps used in the petroleum, petrochemical, and natural gas industries.
- ISO 10816 – this standard provides guidelines for the measurement and evaluation of vibration in industrial machinery. It specifies the allowable vibration levels for various types of machines, including pumps, fans, and compressors.
- ASME PTC 19.3 – this standard provides guidelines for the measurement of vibration in piping systems. It includes procedures for measuring vibration levels, identifying the sources of vibration, and evaluating the severity of vibration.
- ANSI/HI 9.6.4 – this standard provides guidelines for the measurement and evaluation of vibration in centrifugal pumps. It specifies the allowable vibration levels for different pump types and operating conditions.
- NEMA MG 1-2018 – this standard provides guidelines for the measurement and evaluation of vibration in electric motors. It specifies the allowable vibration levels for different motor types and operating conditions.
- Energy Institute Guidelines
Overall, these industry standards provide guidelines for measuring and evaluating vibration in various types of machinery and equipment, including piping systems. They help to ensure that equipment is operating safely and reliably and that any potential issues related to vibration are identified and addressed in a timely manner
Vibration Meter
A vibration meter is a portable device that is used to measure the vibration of a mechanical system or structure. It typically consists of a sensor, display unit, and software for analyzing the vibration data.
The sensor is usually an accelerometer that is attached to the surface of the object being measured. It measures the acceleration of the object, which can then be used to calculate the vibration amplitude and frequency. Some vibration meters may also include other sensors, such as velocity sensors or displacement probes, to provide additional information about the vibration characteristics.
The display unit of a vibration meter typically shows the vibration measurement in real-time, allowing the operator to monitor the vibration levels and make any necessary adjustments. Some vibration meters may also include additional features, such as the ability to store and analyze vibration data over time, or the ability to connect to a computer or other data acquisition system for more detailed analysis.
Vibration meters are commonly used in the maintenance and monitoring of industrial machinery, where they are used to detect any changes in vibration that may indicate equipment failure or performance degradation. They are also used in various other industries, including aerospace, automotive, and civil engineering, to measure and analyze vibrations in machinery and structures.
Hi there, hope you are doing well. We have a trouble passing the vibration test of a machine operating at 60,000 rpm and it contains many rotating group. Accelerometer senser is directly mounted on top of the machine. The limit is 5G but we often get around 8-10G. We have somehow eliminated the possibility of causing vibration from the rotating group. We are wondering if the test setup is contributing to the excess vibration. The parts that are part of the test setup is not mounted well on to the machine especially the part where the air flow is transferred to the machine. Would you be able to help us in figuring this out whether the test setup could be contributing to the vibration?