A “HEAT EXCHANGER” is a device that transfers heat between two or more fluids, keeping them separate while allowing the transfer of thermal energy. There are various types of heat exchangers, but the fundamental components and their uses remain similar across most designs. In this article, we will learn about the major parts of a heat exchanger, their functions, and certain problems associated with those components.
Every heat exchanger, in general, consists of the following component parts. All these parts cumulatively function to work as heat exchanger and transfer heat from one fluid to another.
- Tubes/Channels
- Shell/Casing
- Tube Sheets/Header
- Fluid Inlets and Outlets/Nozzles
- Baffles/Fins
- Pass Partitions/Dividers
- Heat Transfer Surface
- Turbulators
- Insulation and Cladding
- Gaskets/Seals
- Flanges
- By-pass valves
- Distributors and Collectors
- Sight Glasses
- Drain Valves
- Pressure and Temperature Sensors
- Bypass Dampers
The image in Fig. 1 shows some of the heat exchanger components for a shell and tube heat exchanger.
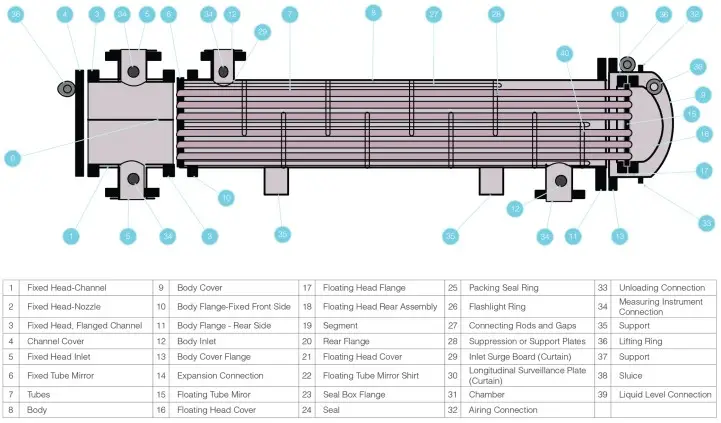
Tubes/Channels
Heat exchangers consist of a network of tubes or channels through which the fluid flows. These tubes or channels provide a pathway for the fluids to exchange heat. They can be straight or coiled, depending on the design of the heat exchanger.
Shell/Casing
The shell or casing encloses the tubes or channels and provides structural support to the heat exchanger. It also serves as a chamber to contain one of the fluids, known as the shell side.
Tube Sheets/Header
Tube sheets are metal plates that support and hold the tubes or channels in place. They seal the ends of the tubes and prevent fluid leakage. In some designs, there may be an inlet and outlet header connected to the tube sheets to facilitate fluid distribution.
Fluid Inlets and Outlets
Heat exchangers have separate inlets and outlets for each fluid. These ports allow the entry and exit of the fluids into and out of the heat exchanger. The fluids may flow in parallel or counterflow configurations, depending on the desired heat transfer characteristics.
Baffles/Fins
Baffles or fins are used to enhance heat transfer by increasing the surface area available for heat exchange. They are typically attached to the tubes or channel walls. Fins can be either solid plates or extended surfaces, such as corrugated or spiral designs, which promote better heat transfer between the fluids.
Pass Partitions/Dividers
In some heat exchangers, pass partitions or dividers are installed to guide the fluid flow. They separate the shell side into multiple compartments or channels, ensuring proper flow distribution and preventing short-circuiting of the fluid.
Heat Transfer Surface
The heat transfer surface refers to the area where the thermal energy exchange occurs between the fluids. It is typically the inner surface of the tubes or channels. The larger the heat transfer surface area, the more efficient the heat exchange process.
Turbulators
Some heat exchangers employ additional components such as Turbulators inside the tubes. Turbulators disrupt the fluid flow to enhance mixing and heat transfer rates.
Insulation and Cladding
In certain applications, heat exchangers may be insulated to minimize heat loss or to maintain temperature control. Insulation materials such as thermal blankets or coatings are used to reduce heat transfer through the shell or other external surfaces.
Plate Heat Transfer Surface
In addition to tubes or channels, some heat exchangers utilize plate-like structures as the heat transfer surface. These plates may have extended surfaces or fins to increase the heat transfer area and improve efficiency.
Gaskets/Seals
Gaskets or seals are used to ensure a tight and leak-free connection between the various components of the heat exchanger, such as tube sheets, headers, or flanges. They help maintain the separation between the fluids and prevent cross-contamination.
Nozzles/Flanges
Heat exchangers have openings or nozzles with flanges for connecting external piping systems. These nozzles provide access points for fluid entry and exit, as well as connections for additional equipment like pumps, valves, or temperature sensors.
Bypass Valves
Some heat exchangers may include bypass valves that allow a controlled portion of the fluid to bypass the heat exchanger. Bypass valves are useful for regulating the heat transfer rate or for system maintenance purposes.
Distributors and Collectors
In large heat exchangers, distributors, and collectors are used to evenly distribute the fluid across the tubes or channels and to collect the fluid from multiple tubes or channels back into a common outlet. These components ensure proper flow distribution and maximize heat transfer efficiency.
Sight Glasses
Sight glasses or windows are transparent sections in the heat exchanger’s casing or piping that allow visual inspection of the fluid flow, level, or any potential issues like fouling or blockages.
Drain Valves
Heat exchangers are equipped with drain valves to remove accumulated condensate, sediment, or other impurities. Drain valves facilitate maintenance, prevent corrosion, and maintain optimal heat transfer efficiency.
Pressure and Temperature Sensors
Heat exchangers may include pressure and temperature sensors at various points to monitor operating conditions and ensure safe and efficient operation. These sensors provide feedback for process control and may be connected to a control system.
Bypass Dampers
In some heat exchangers, particularly air-to-air heat exchangers or HVAC systems, bypass dampers are used to control the flow of air through the heat exchanger. These dampers regulate the amount of heat transferred, depending on the desired temperature or air quality.
Each of these components plays a crucial role in facilitating efficient heat transfer between the fluids in a heat exchanger. The specific design and configuration of these components depend on the type and purpose of the heat exchanger, as well as the properties of the fluids involved. These are additional components commonly found in heat exchangers, depending on the specific application and design requirements. Heat exchangers can vary significantly in their construction, configuration, and additional features based on factors such as heat transfer capacity, fluid type, operating conditions, and industry-specific requirements.
Associated Problems with Heat Exchanger Components
Here is the list of Heat Exchangers components and their associated problems.
Tubes/Channels:
- Corrosion or erosion of the tube material leads to leaks or reduced heat transfer efficiency.
- Fouling or scaling on the tube surfaces, reducing heat transfer rates and increasing pressure drop.
- Tube vibration or damage due to fluid flow-induced stresses, resulting in fatigue or failure.
Shell/Casing:
- Corrosion or erosion of the shell material leads to structural integrity issues.
- Insufficient shell thickness, causing deformation or leakage.
- Inadequate insulation or cladding, resulting in heat loss or inefficient operation.
Tube Sheets/Header:
- Tube sheet corrosion or erosion leads to tube loosening or leakage.
- Improper tube sheet alignment or sealing causes fluid bypass or leakage.
- Tube sheet fouling, reducing heat transfer effectiveness and increasing pressure drop.
Fluid Inlets and Outlets:
- Improperly sized or designed inlet/outlet connections, causing flow maldistribution or pressure drop.
- Leakage or sealing issues at the connection points, resulting in fluid mixing or loss.
Baffles/Fins:
- Fouling or scaling on the baffle or fin surfaces, reducing heat transfer efficiency.
- Damage or dislocation of baffles or fins due to fluid flow-induced stresses, impacting heat transfer effectiveness.
- Inadequate spacing or design of baffles or fins, leading to flow blockage or bypass.
Pass Partitions/Dividers:
- Improper placement or design of pass partitions, causing flow maldistribution or pressure drop.
- Leakage or sealing issues at the partition interfaces, lead to fluid mixing or bypass.
Heat Transfer Surface:
- Fouling, scaling, or corrosion on the heat transfer surface, reduces heat transfer rates.
- Inadequate surface area for heat transfer, resulting in lower efficiency or capacity.
- Thermal stresses or fatigue on the heat transfer surface, lead to cracking or failure.
Fins/Turbulators:
- Fouling or scaling on the fin or Turbulator surfaces, impeding heat transfer efficiency.
- Damage or dislocation of fins or Turbulators due to fluid flow-induced stresses, affecting heat transfer effectiveness.
- Improper design or spacing of fins or Turbulators, causing flow blockage or pressure drop.
Insulation and Cladding:
- Degradation or damage to the insulation material leads to increased heat loss or inadequate temperature control.
- Inadequate insulation thickness or coverage, resulting in heat loss or inefficient operation.
- Corrosion or erosion of the cladding material, compromising protection or aesthetics.
It’s important to note that these problems are potential issues that can arise in heat exchangers, and proper design, maintenance, and monitoring can help mitigate them. The specific problems encountered may vary based on factors such as operating conditions, fluid characteristics, and maintenance practices.
Potential Solutions to the Problems Associated with Heat Exchanger Components
Here are potential solutions for the problems associated with each component of a heat exchanger:
Tubes/Channels:
- Regular inspection and maintenance to identify and address corrosion or erosion issues.
- Implementing proper water treatment or using corrosion-resistant materials for the tubes.
- Periodic cleaning or descaling of the tube surfaces to remove fouling or scaling.
Shell/Casing:
- Applying corrosion-resistant coatings or materials for the shell.
- Ensuring an adequate shell thickness during the design phase.
- Using high-quality insulation or cladding to minimize heat loss.
Tube Sheets/Header:
- Employing corrosion-resistant materials for the tube sheets.
- Ensuring proper alignment and sealing of the tubes during installation.
- Regular cleaning or descaling of the tube sheet surfaces to prevent fouling.
Fluid Inlets and Outlets:
- Properly sizing and designing the inlet/outlet connections to ensure uniform flow distribution.
- Ensuring proper sealing at the connection points to prevent leakage.
- Regular inspection and maintenance to address any issues with the connections.
Baffles/Fins:
- Implementing regular cleaning or maintenance procedures to remove fouling or scaling on the baffle or fin surfaces.
- Ensuring robust design and construction of baffles or fins to withstand fluid flow-induced stresses.
- Optimal spacing and design of baffles or fins to avoid flow blockage or bypass.
Pass Partitions/Dividers:
- Proper design and placement of pass partitions to ensure uniform flow distribution.
- Ensuring effective sealing at the partition interfaces to prevent fluid mixing or bypass.
- Regular inspection and maintenance to address any issues with the pass partitions.
Heat Transfer Surface:
- Regular cleaning or descaling of the heat transfer surface to remove fouling or scaling.
- Increasing the surface area through the use of extended surfaces or fins for better heat transfer efficiency.
- Using corrosion-resistant materials for the heat transfer surface.
Fins/Turbulators:
- Implementing regular cleaning or maintenance procedures to remove fouling or scaling on the fin or Turbulator surfaces.
- Ensuring robust design and construction of fins or Turbulators to withstand fluid flow-induced stresses.
- Proper spacing and design of fins or Turbulators to avoid flow blockage or pressure drop.
Insulation and Cladding:
- Regular inspection and maintenance of insulation to identify and address any degradation or damage.
- Ensuring adequate insulation thickness and coverage to minimize heat loss.
- Using corrosion-resistant materials or coatings for the cladding.
It’s important to note that the solutions provided are general guidelines and may need to be adapted based on specific requirements, operating conditions, and industry standards. Regular maintenance, monitoring, and adherence to best practices are key to ensuring the optimal performance and longevity of heat exchangers.
Dear Sirs,
Can you please comment on the necessity to have a drain/vent hole in the pass partition plate of an air cooled heat exchanger ?
What is an adequate hole diameter ? The designer specified 2 x 20 mm dia. holes for a single partition plate in our to-be -built heat exchanger and I have a major concern for efficiency los due to liquid bypass via these large holes
Thank you for your kind help,
Regards,