In the intricate network of industries that power our modern world, few substances hold as much importance as petroleum. As a source of fuel, raw materials, and energy, petroleum plays a vital role in sustaining our daily lives. But have you ever wondered about the unsung heroes that store this invaluable resource? Enter the petroleum tank – a crucial element in the petroleum supply chain that often goes unnoticed, yet is pivotal in ensuring the seamless distribution of liquid gold.
The Backbone of Energy Storage
Petroleum tanks serve as the backbone of energy storage, providing a safe and efficient means to house vast quantities of crude oil, refined products, and other derivatives. As the main product is oil, petroleum tanks are also popular as oil tanks. These tanks come in various shapes, sizes, and configurations, each designed to meet specific storage requirements. From massive cylindrical tanks dotting the landscapes of oil refineries to the more inconspicuous tanks nestled underground, each serves a distinct purpose.
Parts of a Petroleum Tank
Understanding the components of a petroleum tank is essential to grasp its functionality. Most tanks consist of the following key elements:
- Shell: The outer cylindrical structure that contains petroleum. It is constructed using sturdy materials to withstand the immense pressure exerted by the stored liquid.
- Roof: Designed to prevent external elements such as rainwater and debris from contaminating the stored petroleum. Floating roofs are commonly used to adjust the volume of the tank’s contents.
- Bottom: The base of the tank that supports the weight of the stored petroleum. It is designed to prevent leakage and seepage into the ground.
- Fittings and Valves: An intricate network of pipes, valves, and fittings facilitate the inflow, outflow, and monitoring of stored petroleum.
- Secondary Containment: In many modern tanks, a secondary containment system acts as a safeguard, preventing any potential spills or leaks from reaching the environment.
Types of Petroleum Tanks
Petroleum tanks come in various types, each designed to fulfill specific storage and operational requirements. The choice of tank type depends on factors such as the type of petroleum product being stored, the location of the tank, safety considerations, and environmental regulations. Fig. 1 below shows typical examples of storage tanks.
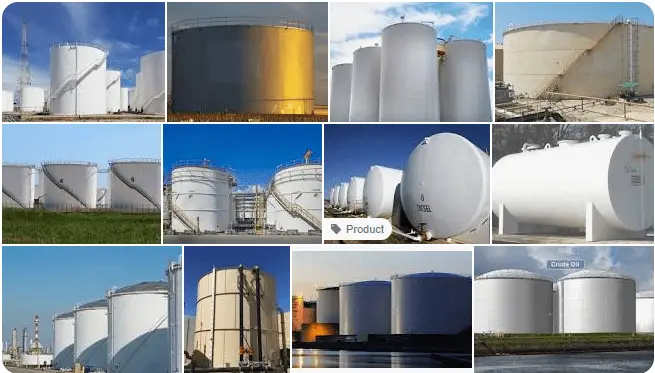
Here are some of the common types of petroleum tanks:
Above-Ground Storage Tanks (ASTs):
These tanks are situated on or above the ground surface and are commonly used in refineries, distribution terminals, and industrial facilities. They are easily accessible for inspection, maintenance, and cleaning. ASTs can have either fixed or floating roofs, and they are cost-effective to install and maintain.
Underground Storage Tanks (USTs):
Buried beneath the ground surface, USTs are often used at gas stations, residential areas, and places where space is limited. They offer advantages such as space conservation and reduced aesthetic impact. USTs are particularly useful for storing smaller quantities of petroleum products, like gasoline and diesel.
Floating Roof Oil Tanks:
These tanks have a floating roof that rests on the surface of the stored liquid. The roof moves up and down with the changing volume of the liquid due to temperature fluctuations. Floating roof tanks are commonly used for storing volatile petroleum products, like crude oil and gasoline, as the floating roof helps reduce vapor emissions and minimize the risk of fires and explosions.
Fixed Roof Oil Tanks:
These tanks have a permanent, non-floating roof. They are often used to store more stable products, such as heavy crude oils and asphalt. Fixed roof tanks can have cone roofs, dome roofs, or umbrella roofs. While they may not offer the same level of vapor emission control as floating roof tanks, they can still be equipped with vapor recovery systems to mitigate emissions.
Cone Roof Tanks:
These tanks have a cone-shaped roof that is sloped downward toward the center. They are commonly used for storing materials that do not require a floating roof but still need protection from environmental elements.
Dome Roof Tanks:
Dome roof tanks have a rounded, geodesic-shaped roof. These tanks are known for their structural strength and are often used for storing large volumes of petroleum products.
Spherical Tanks:
Spherical tanks are unique in design, resembling large spheres. They are used for storing liquids under high pressure, making them suitable for liquefied petroleum gas (LPG) and other pressurized products.
Horizontal Storage Tanks:
These tanks are oriented horizontally and are often used for above-ground storage of liquids. They can be used for various petroleum products, including crude oil and refined products.
Bunded Oil Tanks:
A bunded oil tank is a type of storage tank designed to provide an extra layer of protection against leaks, spills, and environmental contamination. It consists of two layers or walls – an inner tank that holds the oil and an outer ‘bund’ (a protective barrier) that surrounds the inner tank. In the event of a leak or spill from the inner tank, the outer bund is designed to contain the oil, preventing it from reaching the environment. Unlike secondary containment bunded spill pallets, which catch drips and leaks from oil drums and other containers, Bunded oil tanks are an all-in-one storage and bund solution. Bunded oil tanks are widely used for storing various types of oils, including heating oil, diesel, and other petroleum products. They are a safety measure to prevent oil-related incidents and minimize the risk of environmental damage.
Single Skin Oil Tanks:
Single-skin oil tanks are basic, single-layer storage tanks designed to hold oil. Unlike bunded tanks, they lack an outer protective layer (bund) to contain potential leaks or spills. While single-skin tanks are simpler and less expensive to install, they offer less environmental protection. Any leaks or spills from a single skin tank have a higher chance of directly impacting the surrounding area, potentially leading to soil and groundwater contamination. Due to their limitations in terms of environmental safety, single-skin tanks are becoming less common, especially in areas with stringent regulations.
Double Skin Oil Tanks:
Double-skin oil tanks, also known as twin-wall tanks or double-walled tanks, are similar to bunded tanks but with an additional layer of insulation between the inner tank and the outer skin. The primary purpose of the insulation is to provide an added safeguard against temperature fluctuations, which can help maintain the quality of the stored oil. Like bunded tanks, double-skin tanks provide a higher level of protection against leaks and spills compared to single-skin tanks. They are often used for storing sensitive petroleum products and are a preferred choice in regions with strict environmental regulations.
Open Top Oil Tanks:
An open-top oil tank refers to a type of storage tank that lacks a fully enclosed roof, resulting in an exposed opening at the top. These tanks are typically used for storing non-hazardous materials, as the lack of a sealed roof makes them unsuitable for containing volatile or hazardous substances. Open-top tanks are often used for applications such as storing water, wastewater, or certain industrial liquids. They are not commonly used for storing petroleum products due to the potential for vapor emissions, environmental contamination, and safety concerns associated with open access to the stored material.
Secondary Containment Tanks:
Some tanks, regardless of their primary design, incorporate secondary containment systems to provide an extra layer of environmental protection. These systems capture any potential leaks or spills, preventing them from reaching the surrounding environment.
Codes and Standards for Petroleum Tanks
Designing and constructing petroleum tanks involves adherence to various codes and standards to ensure safety, environmental protection, and compliance with industry best practices. Here are some important design codes and standards commonly used for petroleum tanks:
API 650: Welded Steel Tanks for Oil Storage:
Published by the American Petroleum Institute (API), this standard provides requirements for the design, fabrication, assembly, and inspection of welded steel tanks used for the storage of petroleum liquids, including crude oil and various refined products. It covers aspects such as materials, design loads, tank shell and bottom design, corrosion protection, and more.
API 620: Design and Construction of Large, Welded, Low-Pressure Storage Tanks:
Another API standard, API 620, focuses on the design and construction of larger, low-pressure welded storage tanks. It covers aspects like design pressure, temperature, materials, and welding procedures for tanks that operate at pressures up to 15 psi (103 kPa).
API 653: Tank Inspection, Repair, Alteration, and Reconstruction:
API 653 provides guidelines for the inspection, repair, alteration, and reconstruction of above-ground storage tanks used for petroleum products. It outlines requirements for maintaining the integrity and safety of existing tanks, including assessment methods, repair techniques, and guidelines for returning tanks to service after modifications.
UL 142: Standard for Steel Aboveground Tanks for Flammable and Combustible Liquids:
Published by Underwriters Laboratories (UL), this standard covers requirements for the construction and testing of above-ground steel tanks used for storing flammable and combustible liquids, including many petroleum products. It addresses aspects like materials, welding, leakage prevention, and more.
NFPA 30: Flammable and Combustible Liquids Code:
Developed by the National Fire Protection Association (NFPA), NFPA 30 provides guidelines for the storage, handling, and use of flammable and combustible liquids, including petroleum products. It covers a wide range of topics, including tank design, installation, ventilation, and fire protection.
EN 14015: Specification for the Design and Manufacture of Site-Built, Vertical, Cylindrical, Flat-Bottomed, Above Ground, Welded, Steel Tanks for the Storage of Liquids at Ambient Temperature and Above:
This European standard provides requirements for the design and construction of site-built, above-ground storage tanks for various liquids, including petroleum products. It covers aspects such as materials, design considerations, fabrication, and testing.
ASME Boiler and Pressure Vessel Code (Section VIII, Division 1):
This code, developed by the American Society of Mechanical Engineers (ASME), provides guidelines for the design and construction of pressure vessels, including some types of tanks used in the petroleum industry. While it is not specific to petroleum tanks, certain provisions may apply depending on the tank’s characteristics.
ISO 28300: Petroleum, Petrochemical, and Natural Gas Industries – Venting of Atmospheric and Low-Pressure Storage Tanks:
This international standard provides guidance on the venting requirements for atmospheric and low-pressure storage tanks used in the petroleum, petrochemical, and natural gas industries. Proper venting helps prevent overpressure and vacuum conditions in tanks.
Materials for Petroleum Storage Tanks
Petroleum storage tanks are constructed using a variety of materials, each chosen based on factors such as the type of petroleum product being stored, the tank’s size, location, intended use, and regulatory requirements. Here are some common materials used for building petroleum storage tanks:
- Steel: Steel is one of the most widely used materials for constructing petroleum storage tanks. It is known for its strength, durability, and suitability for a wide range of petroleum products. Tanks made from carbon steel or stainless steel are common in the industry. Carbon steel tanks are often coated or lined with protective materials to prevent corrosion and extend their lifespan. Stainless steel tanks are preferred when storing corrosive or high-temperature petroleum products.
- Fiberglass Reinforced Plastic (FRP): FRP tanks are corrosion-resistant and lightweight, making them suitable for storing a variety of petroleum products. They are particularly useful for storing chemicals and acids that may corrode traditional steel tanks. FRP tanks can be designed to withstand a wide range of temperatures and are often used for underground storage due to their resistance to soil corrosion.
- Concrete: Concrete tanks are commonly used for above-ground storage of petroleum products, especially in industrial settings. They are durable, fire-resistant, and can be constructed to various sizes and shapes. Concrete tanks may be reinforced with steel to enhance their structural integrity.
- Composite Tanks: Composite tanks combine the benefits of different materials. For instance, a tank might have a steel shell with a corrosion-resistant inner lining made of a material like FRP. These tanks provide the strength of steel while minimizing the risk of corrosion or contamination.
- Polyethylene (Plastic): Polyethylene tanks are lightweight, corrosion-resistant, and suitable for storing non-hazardous petroleum products such as water, lubricants, and some types of fuels. They are often used for smaller storage needs, especially in residential or non-industrial settings.
- Coatings and Linings: Regardless of the tank’s main construction material, various coatings and linings can be applied to protect against corrosion, chemical reactions, and other environmental factors. Epoxy, polyurethane, and other specialized coatings are often used to extend the life of the tank and ensure the stored petroleum remains uncontaminated.
Petroleum Oil Tank Specification
Specifying a petroleum tank involves providing detailed information and requirements to ensure that the tank is designed, constructed, and installed to meet your specific needs and comply with industry standards and regulations. Here’s a step-by-step guide on how to specify a petroleum tank:
- Define Your Requirements: Start by clearly defining your requirements. Determine the type of petroleum product you will be storing (crude oil, gasoline, diesel, etc.), the desired tank capacity, the intended location (above ground, underground), and any specific environmental or safety considerations.
- Consult Regulations and Standards: Research and familiarize yourself with relevant industry standards and local regulations governing petroleum storage tanks. This could include standards from organizations like the American Petroleum Institute (API), the National Fire Protection Association (NFPA), and environmental agencies in your region.
- Select Tank Type and Material: Choose the appropriate tank type (e.g., above-ground, underground, bunded, double skin) based on factors such as safety, environmental protection, and product characteristics. Select a suitable tank material (steel, fiberglass, concrete, etc.) based on compatibility with the stored petroleum and potential corrosion concerns.
- Determine Design Parameters: Specify design parameters such as tank dimensions, capacity, shape, and any additional features like fittings, valves, vents, and access points. Consider factors like wind loads, seismic activity, and temperature variations that may affect the tank’s design.
- Include Safety Features: Ensure the tank is designed with safety features such as pressure relief devices, overfill protection, leak detection systems, and fire suppression equipment. Specify any secondary containment requirements for environmental protection.
- Coatings and Linings: If needed, specify the type of coatings or linings required to protect the tank from corrosion or chemical reactions with the stored petroleum. Consider factors like the corrosiveness of the product and potential interactions.
- Installation and Location: Define installation requirements, including the tank’s location, foundation specifications, anchoring methods, and any additional infrastructure needed for proper operation (e.g., piping, pumps).
- Inspection and Maintenance: Specify access points and provisions for regular inspection, maintenance, and cleaning. Ensure the tank design allows for easy monitoring of the tank’s condition and product levels.
- Documentation and Records: Request detailed documentation from the tank manufacturer or supplier, including engineering drawings, material certifications, quality control procedures, and warranties. Ensure that all relevant records are provided for compliance and future reference.
- Review and Approval Process: Establish a review and approval process to ensure that the tank design meets your specifications and regulatory requirements. Involve relevant stakeholders, such as engineers, safety experts, and regulatory authorities, as needed.
- Budget and Timeline: Clearly define your budget and project timeline expectations to ensure that the tank specification aligns with your financial and scheduling constraints.
- Communication: Maintain clear and open communication with the tank manufacturer or supplier throughout the process to address any questions, concerns, or modifications that may arise.
Ensuring Safety and Environmental Protection
Safety is paramount in the petroleum industry, and petroleum tanks are no exception. Rigorous engineering, strict maintenance protocols, and advanced monitoring systems work in tandem to prevent accidents, leaks, and environmental contamination. Regular inspections, leak detection mechanisms, and emergency response plans contribute to minimizing risks associated with petroleum storage.
Conclusion
Petroleum tanks may not always be in the limelight, but they are the unsung guardians of the precious liquid that powers our world. These tanks stand as silent sentinels, ensuring the availability of petroleum products while upholding safety standards and environmental protection. Understanding the significance of petroleum tanks shines a light on the intricacies of an industry that impacts every facet of our lives, from transportation to manufacturing to energy generation.
THANKS