Pressure vessel fabrication refers to the process of manufacturing containers designed to hold fluids or gases at varying pressures, often under high or elevated pressure conditions. These vessels are found in a wide range of industries, including petrochemical, pharmaceutical, aerospace, nuclear, food, and more. The process of pressure vessel fabrication involves planning, studying pressure vessel general arrangement and fabrication drawings, selecting appropriate materials, assembling, welding, testing, and inspecting these vessels to ensure they meet specific safety and performance standards.
Pressure vessels are crucial components in various industrial processes where the containment of substances under pressure is essential for the successful operation of various applications. Pressure vessel fabrication must adhere to strict engineering and quality control standards to ensure the vessels’ integrity and safety in their intended use at different pressures and temperature conditions. It is a complex and highly specialized field that requires precision, skill, and adherence to strict quality standards. In this blog post, we will explore the process and key considerations of pressure vessel fabrication. Fig. 1 below shows an example of typical pressure vessel fabrication.
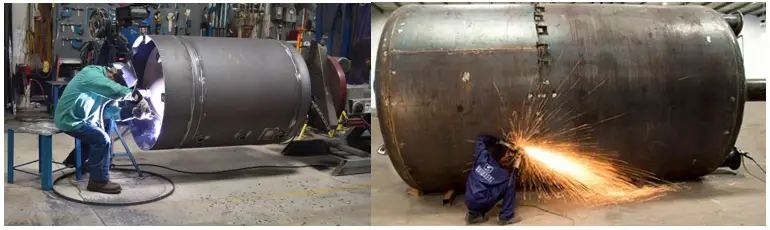
Key Considerations in Pressure Vessel Fabrication Process
Pressure vessels often work under a range of varying pressure and temperature. So, its fabrication must be proper so that the equipment performs the intended operation for its design life without failure. The fabrication of a pressure vessel is a complex process and it involves several critical considerations.
Pressure Vessel Fabrication Drawing
Pressure vessel fabrication drawings are detailed technical drawings that provide a visual representation of the design, dimensions, and specifications of a pressure vessel. These drawings serve as a crucial reference for the designers, inspectors, and fabricators during the manufacturing and quality assurance process. Pressure vessel fabrication drawings are typically created by experienced engineers and designers using Computer-Aided Design (CAD) software to ensure precision and adherence to design codes and standards.
The fabrication drawing shows all details required for equipment fabrication such as dimensions, part detailing, weld details, nozzle schedules, bill of material, design data, equipment plan view, elevation view, sectional views, etc. Here’s what is typically found in a pressure vessel fabrication drawing:
- Pressure Vessel Design Code
- Vessel Geometry that includes detailed illustrations of the vessel’s shape, dimensions, cross-sections, and overall geometry. The fabrication drawings provide the vessel’s diameter, height, and specific features like nozzles, manholes, or flanges.
- Material Specifications to inform the pressure vessel fabricator about the material, grade, and thickness to be used in the fabrication process.
- Welding Details like the type of welds, welding locations where welding is required, weld joint details, and weld size requirements are typically included.
- Information related to Pressure Vessel Nozzles and Openings like nozzle positions, sizes, and types of nozzles and openings, including details like flange ratings and orientations.
- Pressure and Temperature Ratings for the vessel’s design
- Reinforcement and Supporting details
- Instrumentation and Accessories such as pressure gauges, safety valves, sight glasses, and level indicators that may be attached to the vessel.
Once the pressure vessel fabrication drawing is generated, the fabricators produce the pressure vessel following the below-mentioned steps:
1. Material Preparation:
Material preparation is a crucial first step in pressure vessel fabrication. It involves the following activities:
- Material Selection: The material requirement of each component is mentioned in the vessel fabrication drawing. The selection of appropriate materials is done by the material engineers based on factors such as the type of substance to be stored, operating temperature, and pressure conditions. Some of the common pressure vessel materials are carbon steel, stainless steel, LTCS, alloy steel, and exotic alloys.
- Cutting and Shaping: Selected materials are then cut, shaped, and prepared for assembly according to the vessel’s design specifications. This includes cutting sheets or plates into the required shapes and sizes.
- Edge Preparation: The edges of the material pieces are often prepared to ensure proper fit-up and weld quality. This may involve beveling or chamfering the edges.
2. Welding:
Welding is a critical process in pressure vessel fabrication. Skilled welders are responsible for joining the prepared material pieces to create the vessel’s shell and heads. The welding process includes:
- Welding Techniques: The use of appropriate welding techniques such as shielded metal arc welding (SMAW), gas tungsten arc welding (GTAW), or submerged arc welding (SAW), depending on the materials and design.
- Weld Joint Preparation: Preparing the joints for welding, which may involve bevelling or chamfering, and ensuring proper alignment.
- Quality Control: Continuous monitoring of the welding process to ensure high-quality and defect-free welds.
3. Heat Treatment:
Heat treatment is often applied to pressure vessel components after welding to relieve residual stresses and enhance material properties. The heat treatment process usually involve:
- Stress Relieving: Controlled heating and cooling to reduce stresses induced during welding, which can help prevent cracking and improve material properties.
- Normalizing: A heat treatment process that refines the grain structure and improves material uniformity.
4. Testing:
Testing is a critical aspect of pressure vessel fabrication to ensure the vessel’s integrity and safety. Common tests include:
- Non-Destructive Testing (NDT): Some of the common NDT methods are radiography, ultrasonic testing, magnetic particle testing, and dye penetrant testing. They detect defects and ensure the welds are sound.
- Hydrostatic Testing: Filling the vessel with a liquid, usually water, and pressurizing it to verify its performance and to check for leaks or deformations.
5. Surface Finishing:
After testing, the pressure vessel undergoes surface finishing, which includes:
- Cleaning: Removing any contaminants, oils, or residues from the vessel’s surface to prepare it for surface treatments.
- Painting or Coating: Applying paint or protective coatings to the vessel’s exterior to prevent corrosion and enhance its appearance.
6. Final Inspection and Documentation:
Before the vessel is ready for delivery, it undergoes a final inspection to ensure compliance with design specifications and industry standards. This step includes:
- Visual Inspection: A thorough visual examination of the vessel’s components and welds.
- Documentation: Preparing comprehensive documentation that includes material certificates, welder qualifications, NDT reports, and other quality-related documents.
7. Delivery and Installation:
Once the pressure vessel has passed all quality control checks and inspections, it is prepared for delivery to the client’s site. This involves:
- Transportation: Safely moving the vessel to the installation site, which may require specialized equipment and transportation methods.
- Installation: Installing the pressure vessel at the intended location, often involving the connection of piping, instrumentation, and safety mechanisms for it to be fully operational.
To ensure the successful fabrication and safe operation of pressure vessels, each of these steps plays a crucial role, especially when industries prioritize safety and performance. Adherence to design specifications and industry standards is essential throughout the entire fabrication process.
Video Tutorial on Fabrication of Pressure Vessel
Refer to the following video, that explains the process of a typical vessel fabrication process clearly.