Refineries and petrochemical plants obtain feedstocks and dispatch products in a number of ways. The most common methods are by pipeline, road, rail, and sea. A marine import/export facility is a very important item for a refinery or petrochemical plant. Under-design of the marine facilities can result in process plant throughput being constrained. Over-design can lead to a substantial increase in capital cost, which can have a significant effect on the overall economics of a Project.
Whereas the majority of process unit operations are continuous processes, marine loading/unloading is always a batch operation. It is therefore most important that all the requirements and activities associated with the start-up and shutdown of each type of loading/unloading operation are covered in the specification/design of marine facilities. This article will assist process engineers with the design of facilities for importing feedstocks and exporting products by sea. This document covers the key process design issues associated with the design/specification of marine systems, including jetties/berths, single-point moorings, and the associated loading systems.
Marine System design guidelines
The following guidelines can be followed during the design of a marine system
At an early stage of the design of a marine facility, an estimate of the throughput of each material to be handled and the capacities of tankers that will transport them must be agreed upon by all parties, as a starting point for the design work. This information is fundamental to the design.
Initial Estimate of Number of Berths Required- When throughput/tanker size data has been agreed upon, it is recommended that an initial estimate is made of the number of berths required.
Types of Berth
Berths can be divided into the following categories:
- Single Point Mooring (SPM): Feedstocks/products are pumped via sub-sea pipeline(s) from/to a tanker that has moored up to a floating buoy, located off-shore.
- Single Berth: One berth, either on a jetty or on the quayside, normally with multiple loading arms for one tanker to load/unload products/feedstocks
- Multiple Berths, forming a harbor: A number of berths, normally on a jetty, enabling several tankers to load/unload products/feedstocks simultaneously
- SPMs are favored when the maximum tanker size is such that dredging and/or a very long jetty structure would be required to provide sufficient draught i.e. when large tankers have to be accommodated. Single berths are seen most often in deep water locations and in river estuaries.
Location of Shipping Tanks / Pumps
In some cases, a Client may not have finalized the location of the product (or feedstock) tank farm before the design work starts. In such cases, it should be noted that pumping to/from tankers is generally at much higher flow rates than the rates at which feedstocks/products are consumed/produced by a process plant. Hence the pumps/pipelines etc. serving marine systems are generally much larger than the pumps/pipelines connecting process plants to storage tanks. For this reason, in cases where there is a significant distance between a process plant and the supporting marine facilities, it is more economic to locate the shipping tanks/pumps close to the marine facilities, rather than close to the process plant.
Segregation of Feedstocks / Products
It is important to ensure that marine loading facilities are designed to segregate products/feedstocks. Segregation is best achieved by designing dedicated marine facilities for each material. But this is often impractical or uneconomic. At a multiproduct berth, it is normal for loading arms to be used for several similar products. If economics dictate that pipelines must be multi-product (e.g. when the marine loading facility is a long way from the export tanks), flushing or pigging facilities (or a system to detect and slop the interface material) are required.
Types of Tankers/ Tanker Types in a Marine System
Broadly speaking tankers can be classified as either conventional, pressurized, refrigerated, or semi-refrigerated. For all tanker types, onshore pumps are used for loading, and onboard pumps are used for unloading. Key features of these types of tanker are as follows:
A conventional tanker carries fluids with true vapor pressures of less than one atmosphere minus a suitable safety margin. This margin tends to vary slightly between clients and carriers, but usually, the maximum vapor pressure is approximately 0.75 atm. The tanker comprises a number of compartments that can be filled or emptied independently. Most tankers also have slop tanks, separate from the product tanks. Tankers carrying highly flammable or oxidizable materials often have inerting facilities, by which exhaust gases from the tanker’s engines are passed into the vapor space in the tanks.
Pressurized liquid gas tankers usually have fewer storage compartments than conventional tankers. The smaller one might comprise a single-pressure container. It is usual for pressurized liquid gas tankers to use a vapor connection for the transfer of displaced vapor at both the import and export locations.
Refrigerated gas tankers are usually bigger than pressurized tankers. They generally have more compartments and can withstand little pressure. The refrigeration plant on board is usually designed to counter heat in leak only, hence only liquids that are fully cooled can be loaded.
Semi-refrigerated tankers are sometimes used, and these combine the attributes of both pressurized and refrigerated tankers.
It should be noted that the maximum operating pressure of pressurized and semi-refrigerated tankers varies from vessel to vessel. The metallurgy of refrigerated and semi-refrigerated tankers governs the minimum temperature allowed and hence the products that can be handled.
Marine System Tanker Capacities/ Capacities of tankers
It should be noted that when designing a terminal, the number and volume of feed/product tanks are required to depend to a great extent on the range of tanker capacities that have to be accommodated. The capacity of a tanker that carries material at ambient conditions is generally given in Dead Weight Tonnes (DWT). The capacity of a tanker that carries refrigerated or pressurized material is generally given as a volume. Typical ranges of tanker capacities are as follows:
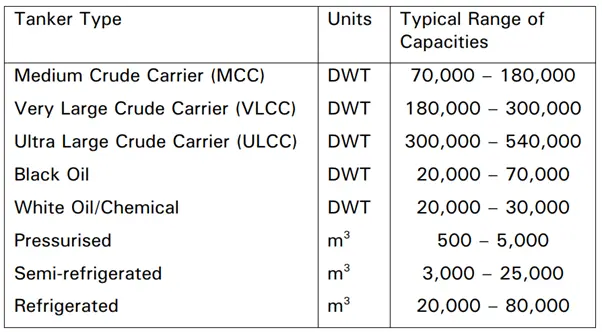
Tanker Loading and Unloading Rates:
Typical loading/unloading rates for tankers are as follows:
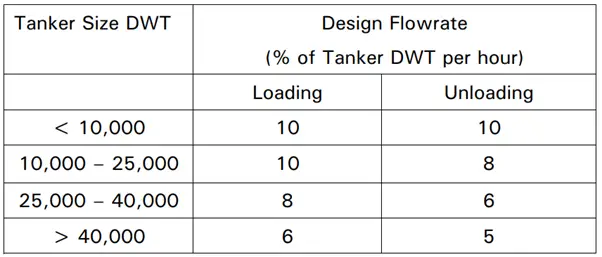
Even if the design loading/unloading rates for the specified tankers are appreciably less than the figures given above, it is recommended that these design loading/unloading rates are used (for the purposes of hydraulic design, but not for the purposes of calculating the berth occupancy) to give the marine terminal flexibility and provide a robust design.
Berth Turnaround Time for Marine System design
The Berth Turnaround Time is a term often used to describe the total elapsed time from the moment a tanker starts its approach to a berth, to the moment that the tanker is clear of the port area, thereby allowing another tanker to begin its approach. Realistic time intervals for a tanker using a berth or jetty are as follows:
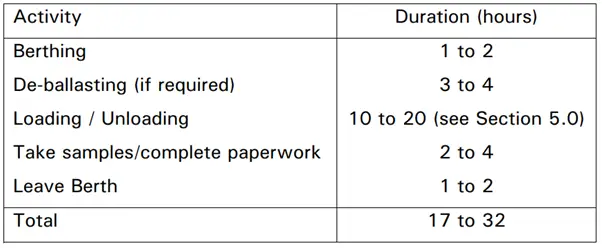
Demurrage/ Berth Occupancy
Demurrage is a charge paid by the Refinery/Petrochemical plant operator to the ship operator/owner in the event of a tanker being delayed. Examples of circumstances in which demurrage fees are payable include:
- A tanker arrives at a marine facility on schedule, but there is no berth available for the tanker.
- A tanker starts loading as scheduled, but for reasons outside the tanker captain’s control, the loading operation takes longer than the pre-agreed maximum time.
Demurrage fees are charged on a daily basis and can become a very significant operating cost. During the design of a marine facility, berth occupancies should be calculated for various scenarios, in order to reduce/minimize demurrage charges. In practice, it is not possible to avoid incurring some demurrage charges, without over-designing the marine facility. As a very rough guide, the following demurrage costs can be used, but the actual costs should be provided by the Client or a marine consultant.
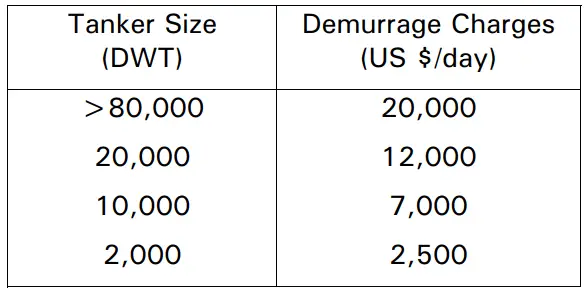
Single Point Mooring (SPM) Systems
SPMs provide a useful method of loading/unloading tankers from/to onshore facilities when it is not practicable to build a jetty. Jetties tend to be impracticable in shallow water (e.g. in estuaries or on continental shelves) when loading/unloading deep-drafted vessels. SPMs are also appropriate in deepwater locations.
The concept of the SPM is simple. The tanker approaches the mooring from the down current. The bow is made fast to the buoy. With the main engines stopped, the tanker now hangs from the buoy with the bow into the current as required. If there is a change of current (or wind) direction, the tanker swings freely around the buoy (known as weather vaning).
Floating hoses from the buoy are hoisted to the tanker’s manifolds and connected, thus permitting loading/unloading. The buoy is connected by the subsea pipeline to the storage facilities. The hoses have to be connected to the pipeline by a swivel so full 360º movement of the tanker can be accommodated without interfering with hose operation.
Jetty Topside Facilities
Jetty topside facilities generally include some/all of the following equipment items/systems:
- Loading arms and associated hydraulic facilities
- Surge alleviation systems
- MOVs
- ESDs
- stripping pumps
- slops/drainage collection systems
- vapor return facilities
- VOC handling systems
- fire detection/protection equipment
- operator shelter/control room
Marine Loading Arms
Loading arms are made up of several sections of pipe, connected by swivel joints. The section on the shore side of the ‘apex’ of the loading arm is known as the inboard arm and the section on the tanker side of the ‘apex’ is known as the outboard section. See the following Figure for a diagram of a loading arm.
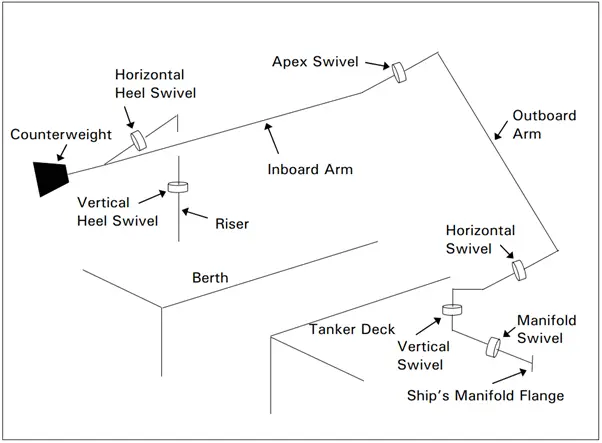
Metering Systems
When loading/unloading tankers, accurate metering is normally a requirement, for both custodial and regulatory reasons. Metering with sufficient accuracy can be achieved using either tank gauging or certain types of flowmeter.
Deballasting Facilities
Most tankers have to be partially filled with ballast water when they are not carrying cargo, in order to make the tankers seaworthy i.e. stable in rough weather. Seawater is generally used as ballast water.
Surge
Marine loading/unloading systems are often designed to pump at high flow rates over large distances. Hence surge pressures (eg due to the closure of a MOV or a pump trip) can be large. It is most important that during detailed design, a surge analysis is carried out on each marine loading pipeline. Peak surge pressures should be calculated for all likely scenarios, to check that the design pressure of pipework/equipment (plus an allowance for short-term over-pressure) is not exceeded, even in the worst case.
VOC Recovery/Disposal
When loading products that are stored at ambient conditions, it is common for the displaced vapor to be simply vented into the atmosphere, thereby emitting volatile organic compounds (VOCs) into the environment. For very low vapor pressure products, the number of VOCs emitted by a tanker when loading is small if not negligible. But for a high vapor pressure product, such as motor gasoline and naphtha, a significant amount of product can be lost to the atmosphere, such as VOCs.
Drainage at Births
It is common to have a curbed area at each berth, in order to catch any material which may leak from, for example, the couplings on loading arms. The curbed area drains into a sump tank located below the berth on the jetty structure. The sump tank includes pumps that return the drainings to a slop oil tank or a ballast water tank or alternative disposal onshore.
Fire Detection and Protection
Remote-controlled monitors and hydrants are commonly provided at each berth, to fight a fire and to protect equipment from the effects of the fire. The fire may be at the berth/on the jetty or on the tanker at the berth. It is normal practice for a jetty/berth to have water sprays/water curtains to protect the structure/equipment and to provide means of escape for personnel in case of fire. It is common to provide valved connections on a fire main in the vicinity of a jetty, to enable a fire tug to connect up and pump water into the system, as a standby.
you can support in design and construction drawings for 4 MLA Jetty
Very nice productive article to give and explain loading arms.