Process piping plays a crucial role in various industries, enabling the safe and efficient transportation of fluids such as liquids, gases, and slurries. From chemical plants and refineries to pharmaceutical facilities and food processing units, process piping systems form the backbone of numerous industrial operations. This article provides a comprehensive overview of process piping, its components, materials, installation techniques, and maintenance practices, highlighting its significance in industrial fluid transportation.
What is Process Piping?
Process piping refers to a network of interconnected pipes, fittings, valves, and other components used to transport fluids within an industrial facility. These systems facilitate the movement of various substances, including water, chemicals, petroleum products, gases, steam, air, refrigerants, and many more. Process piping is designed to handle specific fluid types and meet stringent safety and performance standards.
In general, from an engineering perspective, a process piping system can be defined as a system of piping components designed following the guidelines mentioned in the ASME B31.3 code. Broadly, any piping system designed based on the ASME B31.3 code and used for transporting fluids under various temperatures, pressure, and environmental conditions is termed process piping. On the other hand, the piping system designed based on the ASME B31.1 code is termed power piping.
ASME B31.3 defines process piping as the piping used to carry substances in petroleum refineries; chemical, pharmaceutical, textile, paper, ore processing, semiconductor, and cryogenic plants; onshore and offshore petroleum and natural gas production facilities; food and beverage processing facilities; and related processing plants and terminals. So, as you can find process piping has a large number of applications in industrial facilities.
Components of Process Piping
Process Piping consists of a large variety of piping components. Some of the most widely used piping components for process piping are:
- Pipes: The primary element of any process piping system, pipes are available in different materials such as carbon steel, stainless steel, copper, and plastic. The choice of material depends on factors such as fluid properties, temperature, pressure, and corrosion resistance requirements.
- Fittings: Fittings are used to connect pipes, change direction, and control fluid flow. Common types include elbows, tees, reducers, and couplings. Like pipes, fittings are available in various materials and configurations to suit specific needs. More details about pipe fittings are provided here.
- Valves: Valves regulate the flow and control the pressure of fluids in process piping systems. They can be manual or automated and are crucial for process control and safety. Common valve types include gate valves, globe valves, ball valves, and check valves.
- Flanges: Flanges provide a means for connecting pipes and equipment, forming a secure joint. They are available in different standards, sizes, and pressure ratings, ensuring compatibility and leak-free connections.
Note that various equipment like pressure vessel, pumps, compressors, turbines, heat exchangers, etc forms the complete system to operate the facility successfully but they are not part of process piping. They are used in process piping to complete the process piping system for performing the function of the system. A typical example of a process piping system is shown in the image below:
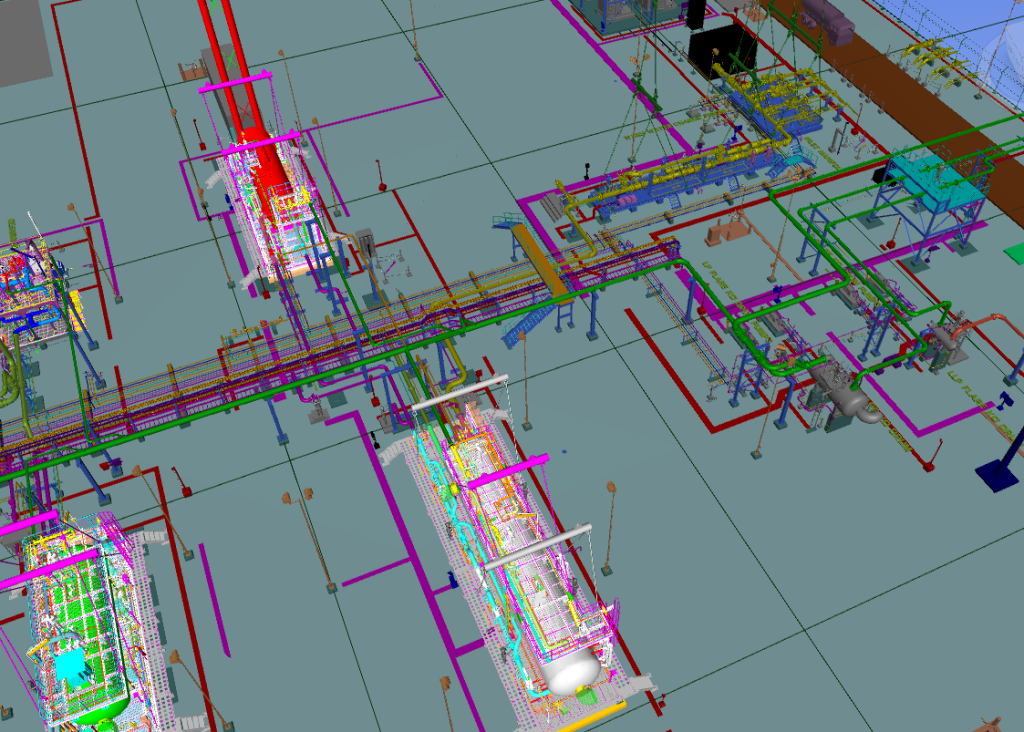
Materials for Process Piping
The choice of materials for process piping depends on factors such as fluid characteristics, temperature, pressure, and the environment. Common materials include:
- Carbon Steel: Suitable for general-purpose applications, carbon steel offers good strength and affordability but may be prone to corrosion in certain environments.
- Stainless Steel: Known for its excellent corrosion resistance, stainless steel is widely used in industries where hygiene and durability are critical, such as pharmaceuticals and food processing.
- Alloy Steel: Alloy steel pipes are made by combining carbon steel with other elements, such as chromium, molybdenum, and nickel, to enhance their mechanical properties and corrosion resistance. In the chemical and petrochemical industries where applications involve high temperature and pressure, alloy steel materials are suitable.
- Copper: Frequently used for water and gas distribution, copper is valued for its corrosion resistance, thermal conductivity, and ease of installation. Click here to learn other non-ferrous piping materials
- Plastic: Materials like PVC, CPVC, and PTFE are used for non-corrosive applications, offering benefits such as chemical resistance, lightweight, and ease of installation.
Click here to learn process piping materials in detail
Codes and Standards for Process Piping
Even though ASME B31.3 is the main governing code for process piping, various other codes and standards are referred to design different components of the piping system. Table 326.1 of ASME B31.3 lists all such codes and standards. The same table is reproduced below for reference.
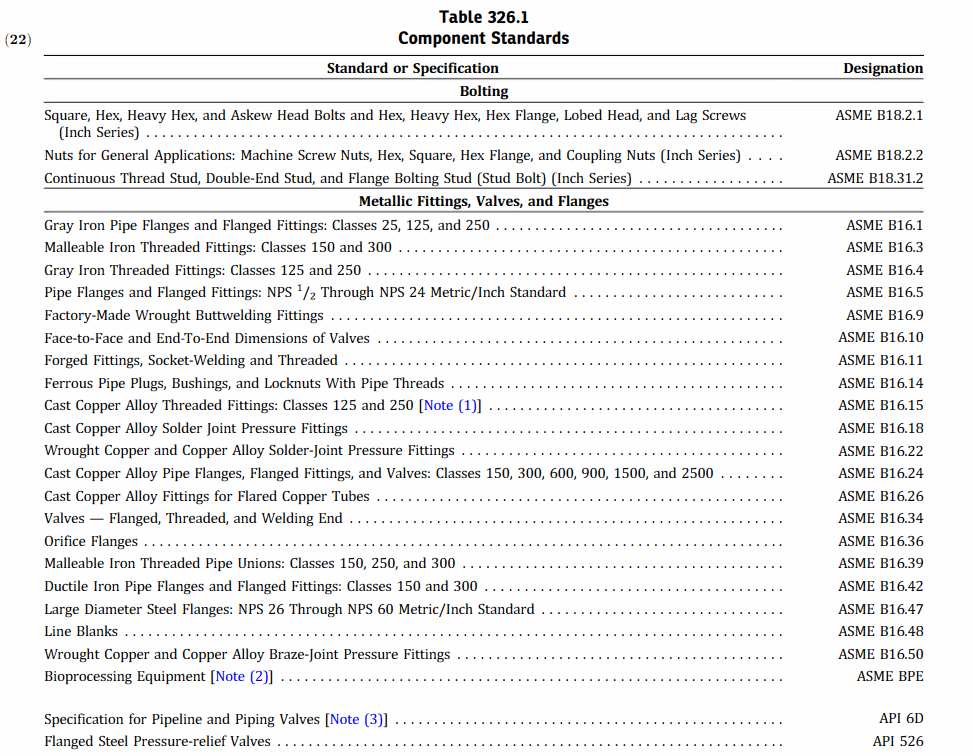
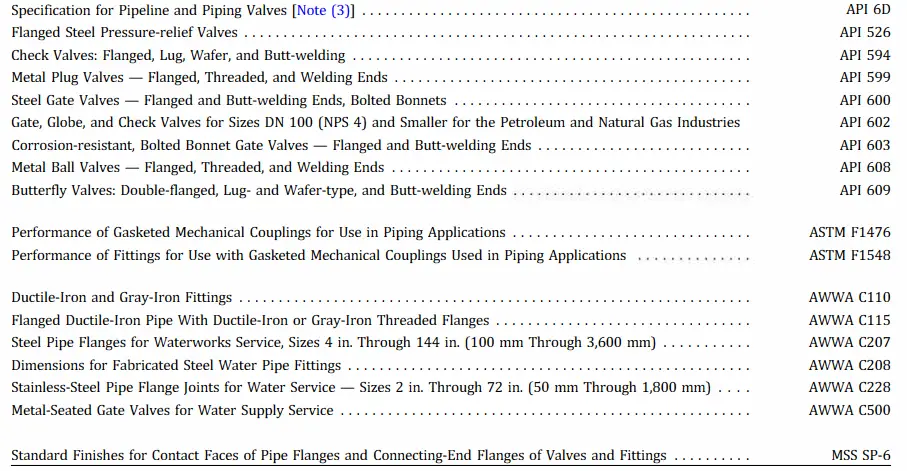
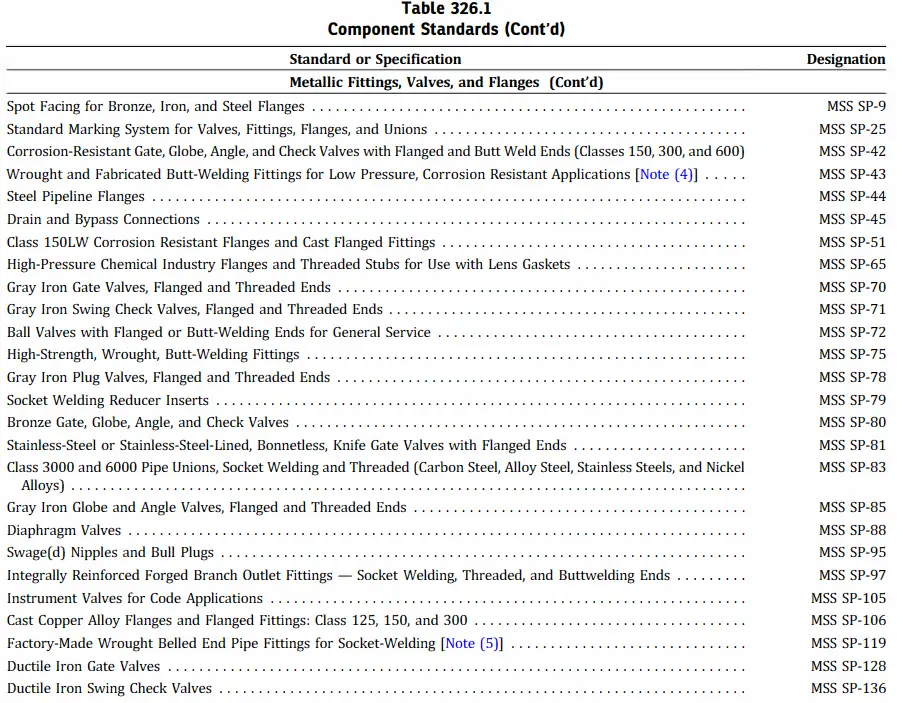
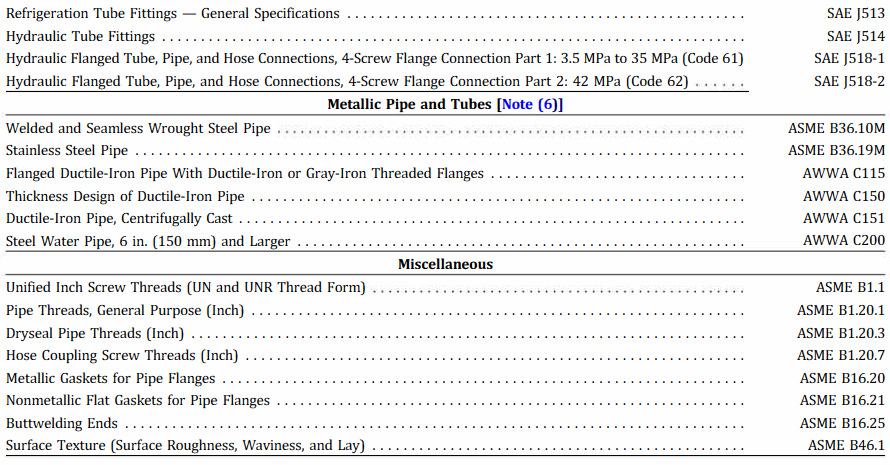
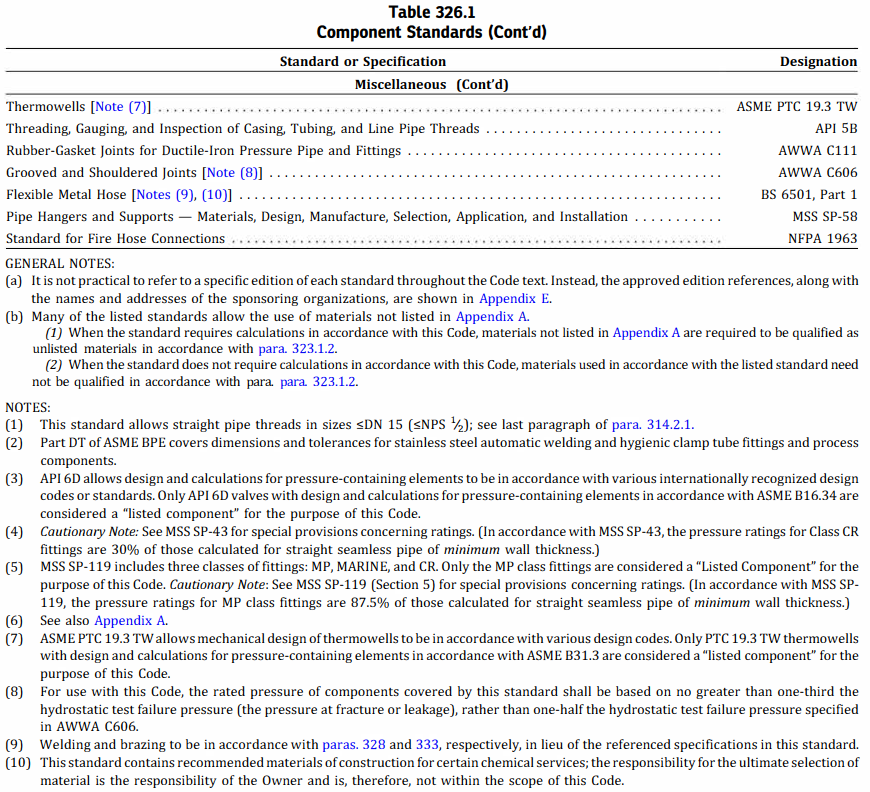
Installation Techniques and Standards
Process piping installation requires adherence to specific guidelines and industry standards to ensure safety and reliability. Proper installation techniques involve activities like pipe routing, cutting, threading, welding, and pressure testing. Standards such as ASME B31.3, ASME B31.1, and API 570 outline best practices for the design, fabrication, inspection, and testing of process piping systems.
Maintenance and Safety Considerations
Regular maintenance is crucial for the optimal performance and longevity of process piping systems. This includes inspection for leaks, corrosion, and mechanical damage, as well as cleaning and periodic replacement of components. Safety considerations involve implementing appropriate measures to prevent leaks, spills, and accidents, including the use of safety barriers, pressure relief devices, and emergency shutdown systems.
Process Piping vs Power Piping: Differences between Power Piping and Process Piping
The following table provides the key differences between Process piping and Power Piping.
Aspect | Process Piping | Power Piping |
---|---|---|
Purpose | Transporting fluids (liquids, gases, slurries) | Transporting steam, water, and other utilities |
Fluid Type | Wide range of fluids (chemicals, petroleum, etc.) | Limited to steam, water, and other utilities |
Pressure Rating | Lower pressure ratings | Higher pressure ratings |
Material Selection | Wide range of materials (carbon steel, stainless steel, etc.) | Specific materials (carbon steel, alloy steel, etc.) for high-temperature and high-pressure applications |
Code Standards | ASME B31.3 (Process Piping Code) | ASME B31.1 (Power Piping Code) |
System Design | Emphasizes process control and fluid movement | Emphasizes energy transfer and power generation |
Safety Considerations | Primarily focuses on fluid containment and chemical compatibility | Focuses on pressure control, thermal expansion, and high-temperature operation |
Inspection | Inspected for leaks, corrosion, and mechanical damage | Inspected for pressure integrity and weld quality |
Industry Applications | Chemical plants, refineries, pharmaceuticals, food processing, etc. | Power plants, utilities, therm |
It’s important to note that while there are distinct differences between process piping and power piping, there may be some overlap in certain applications, especially in facilities that have both process and power systems. Therefore, adherence to appropriate codes and standards is crucial to ensure the safe and efficient operation of piping systems in each specific context.
Differences between Process Piping and Plumbing: Plumbing vs Process Piping
Here’s a tabular format outlining the major differences between process piping and plumbing:
Aspect | Process Piping | Plumbing |
---|---|---|
Purpose | Transporting fluids (liquids, gases, slurries) | Supplying and distributing water, gas, and sewage |
Fluid Type | Wide range of fluids (chemicals, petroleum, etc.) | Water, gas, sewage |
Pressure Rating | Varies based on application and industry | Generally lower pressure ratings |
Material Selection | Wide range of materials (carbon steel, stainless steel, etc.) | Commonly uses copper, PVC, PEX, and other plumbing-specific materials |
Code Standards | ASME B31.3 (Process Piping Code) or specific industry standards | Local plumbing codes and regulations |
System Design | Emphasizes process control and fluid movement | Emphasizes water supply, drainage, and fixture connections |
Safety Considerations | Focuses on containment, chemical compatibility, and industrial safety measures | Focuses on health and sanitation, backflow prevention, and fixture functionality |
Installation | Often involves larger pipe sizes and complex layouts | Involves smaller pipe sizes and simpler layouts |
Fixtures and Equipment | Primarily focused on industrial equipment and machinery | Focuses on sinks, faucets, toilets, showers, and other household fixtures |
Licensing and Certification | Requires specialized training and certifications for working in industrial settings | Requires specific plumbing licenses and certifications for compliance with local regulations |
Conclusions
Process piping serves as the lifeline of industrial fluid transportation, enabling the efficient movement of liquids, gases, and slurries in diverse industries. Understanding the key components, materials, installation techniques, and maintenance practices associated with process piping is essential for ensuring the safe and reliable operation of industrial facilities. By selecting the appropriate materials, following industry standards, and conducting regular maintenance, companies can optimize the performance of their process piping systems while minimizing the risk of leaks, failures, and accidents.
With advancements in technology and the increasing complexity of industrial processes, process piping continues to evolve. New materials, such as composite pipes and advanced alloys, are being introduced to improve performance and reduce costs. Innovative installation techniques, such as prefabrication and modular construction, are gaining popularity for their efficiency and time-saving benefits.
Moreover, the integration of automation and control systems into process piping allows for real-time monitoring and remote control, enhancing safety and process efficiency. These advancements enable companies to improve their productivity, reduce downtime, and meet stringent regulatory requirements.
In conclusion, process piping is a critical component of industrial fluid transportation systems. It enables the safe and efficient movement of fluids within industrial facilities, serving as the backbone of various industries. By understanding the key components, materials, installation techniques, and maintenance practices associated with process piping, companies can ensure the reliable operation of their systems, optimize productivity, and enhance safety. Embracing technological advancements and adhering to industry standards will contribute to the continuous improvement of process piping systems, supporting the growth and success of industrial operations.
Hi Anup, Thanks for sharing this good information to understand more about process piping, Just an excellent summary to prepare for an interview.
It’s nice that you mentioned how industrial process piping plays a crucial role in various industries, enabling the safe and efficient transportation of fluids such as liquids, gases, and slurries. I was watching a documentary about a factory last night and I quickly noticed how important pipes are for industrial operations. Thankfully, it seems there are expert services being offered now for any industrial piping needs.