Pump Priming is a manual or automatic process by which air present in a pump and its suction line is removed by filling liquid. In the pump-priming process, the pump is filled with the liquid to be pumped and that liquid forces to remove the air, gas, or vapor present. With the exception of a few self-primed pumps, mostly all pumps are primed. Before starting a pump, Pump Priming is the most important first step and it avoids the majority of the pump problems.
The majority of the pump problems are started by not priming a pump or not doing it properly. Problems associated with lack of priming usually cause financial impact due to pump maintenance and the downtime of the piping system due to a malfunctioning pump. So for proper reliable operation pump must be primed.
Reason for Pump Priming
During starting a pump, if air, gas, or vapor exists inside the pump casing, the pump will not be able to function properly. The pump will be subjected to the risk of damage. The air or gas present inside the pump will make it gas bound and the pump won’t be pumping the desired liquid. The pump will get overheated and it will damage the pump internals.
To reduce the risk of pump damage and reliable operation, the gas present in the pump must be removed. So, the pump must be fully primed.
When is Pump Priming Required?
The main objective of priming a pump is to remove the gas present. So, if the air or other gases are present inside the pump casing and suction line, it must be primed before starting. But if the pump suction line and the casing are already filled with liquid during start-up, priming is not required. The main reason behind locating most centrifugal pumps below the liquid source level is that the pump remains primed automatically. Refer to Fig. 1 below that clearly explains the requirement of priming a pump.
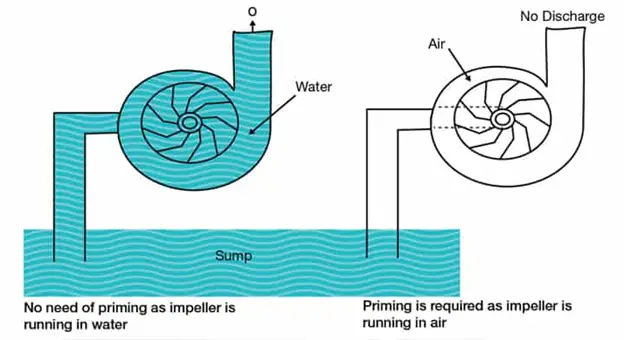
In general, Centrifugal Pumps need priming. Submersible Pumps or vertical sump pumps do not require priming. Positive displacement pumps are considered self-primed pumps.
Pump Priming: Centrifugal vs Positive Displacement Pumps
Normally, Centrifugal pumps need priming and Positive Displacement Pumps (Rotary Pumps, Reciprocating Pumps) do not require priming. However, for the first-time operation, all pumps need priming to avoid overheating and failure in dry running conditions.
In a centrifugal pump, the liquid is pushed from suction to discharge. The pump works by the transfer of rotational energy from the impeller to the liquid. In between the suction and discharge sides of the pump, there are no seals. For this reason, when the liquid level is below that of the impeller, centrifugal pumps are ineffective with gases and incapable of evacuating air from a suction line. So centrifugal pumps must be primed for proper working.
On the other hand, all positive displacement pumps use close-tolerance parts to prevent fluid from returning from the discharge to the suction side. Hence, a positive displacement pump is capable of venting air from its suction line to some extent.
Pump Priming Methods
The pump can be primed by layout considerations or using external arrangements. A few of the external pump priming methods are:
- Natural Priming
- Manual Priming
- Priming a pump with Vacuum Pump
- Pump Priming with Jet Pump
- Pump Priming using a Separator
- Priming a pump by Installing a Foot Valve
- Pump Priming with Ejector
Natural Pump Priming:
Natural pump priming can be achieved by maintaining the impeller eye below the surface of the water. So, naturally, water will flow into the suction pipe and casing removing all the air present by gravitational force as shown in Fig. 2
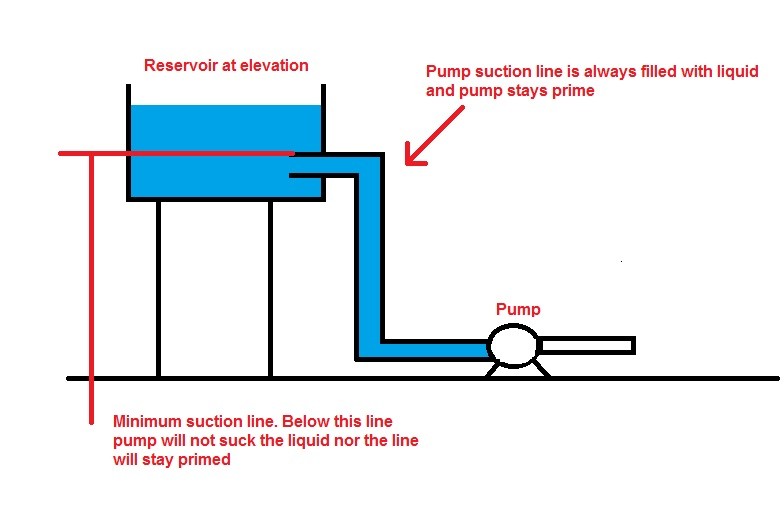
Manual Pump Priming Method:
In the manual method (Fig. 3) of pump-priming, pumping liquid is filled in the pump suction by manually pouring liquid directly into the suction using a funnel. The pump is manually primed due to gravity feed and the air present escapes through the air vent valve.
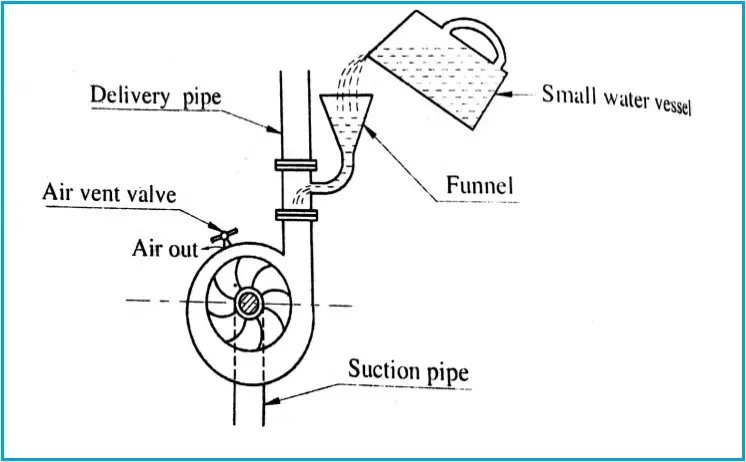
Priming with a Vacuum Pump:
To prime, the main centrifugal pump, An additional small-size vacuum pump or a self-priming pump, or a positive displacement pump is used. The discharge line of the main pump is connected to the suction line of the positive displacement priming pump that evacuates all the air in the primary pump and suction piping.
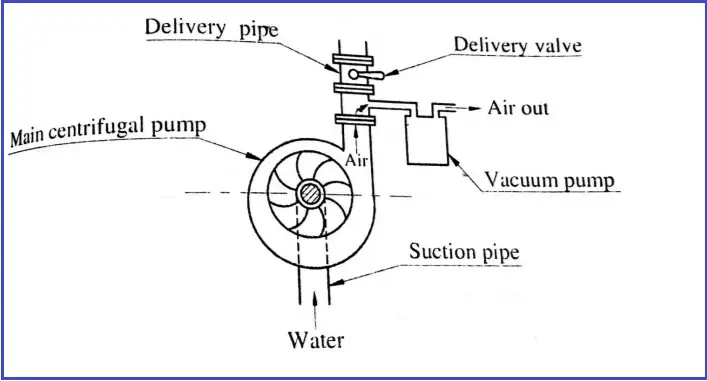
Priming with Jet Pump:
Water available at the high head is allowed to flow through a nozzle in this method of pump priming. The nozzle is designed in such a way that at the jet outside the nozzle, the pressure is less than the atmospheric pressure which causes water to be sucked from the sump.
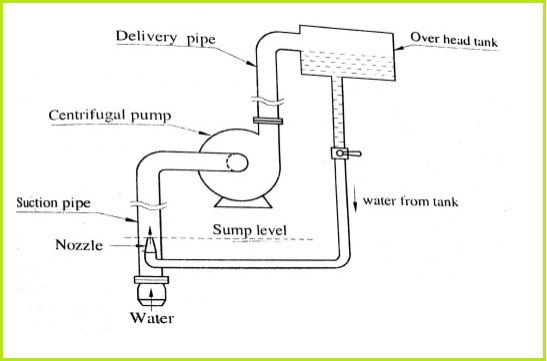
Priming with Separator:
On the discharge side of the pump, an air-water separation chamber or separator is provided for pump priming with a separator. A bent suction pipe portion is provided at the inlet of the pump that always maintains some liquid in the pump. Through pump discharge or an air vent, Air is separated and expelled and the liquid falls back into the separation chamber due to higher density.
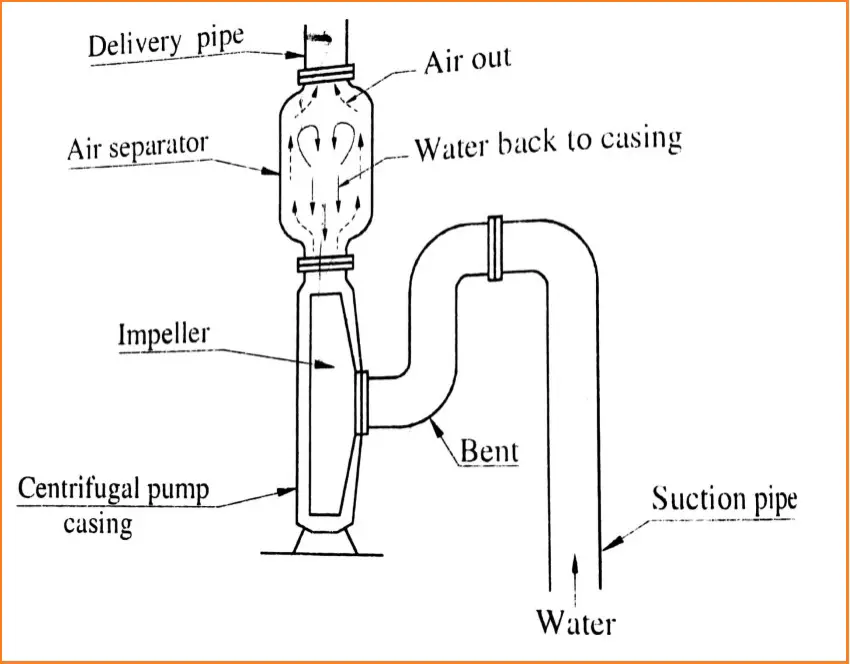
Priming by Installing Foot Valve:
A foot valve that acts like a non-return valve is installed in the suction piping in this pump-priming method. The foot valve does not allow the liquid to drain from the pump casing and suction line once the pump operation is stopped. So, while starting the pump for the next operation, the pump is already primed and can work.

Priming with Ejector:
In this pump-priming method, an ejector (Fig. 7) is provided on the pump suction (or discharge) side. These Ejectors create a vacuum inside the pump suction line forcing the liquids to draw from the sump up to the pump elevation. However, Ejectors require energy input for their work.
Prevention of Pump Operation without Priming
Various methods are used to prevent a pump to operate without being primed. The basis behind such methods is to trigger some alarm or auto shutdown of the pump when the pump is not liquid-filled or primed. One example of such a scenario is provided below.
In some kinds of pumps, a float switch in a chamber connected to the suction line is usually used. When the chamber level is above the impeller’s eye of the pump, the float switch allows the pump to operate without a problem. However, If the liquid falls below a predetermined safe level, the float switch forces the pump to stop using its control mechanism. Thus it prevents the pump to start to sound an alarm, or lighting a warning lamp for necessary action.
What is a Self-Priming Pump?
A self-priming pump is a specially designed end suction centrifugal pump with an external casing that always “floods” the inner pump or volute. The self-priming pump has the ability to evacuate air from the suction side at startup and then it operates similarly to a normal pump. The external casing is filled with liquid and the pump is always ready to start. When the impeller of a self-priming pump rotates inside the casing, a low-pressure area (below atmospheric pressure) is formed at the eye of the impeller. As a result, the liquid is pushed up the suction pipe by atmospheric pressure along with the air present in the suction pipe.
This air is mixed with the recirculating fluid inside the casing. The air then separates from the liquid and is discharged from the casing. Once, all the air from the suction pipe is removed, the pump operates dynamically like any other centrifugal pump. So, A self-priming pump can lift fluid from a level below the pump and evacuates the air of the suction line without using other external auxiliary devices.
There are three types of self-priming pumps. they are:
- Liquid Primed Self priming Pumps
- Compressed Air Primed Self-priming Pumps, and
- Vacuum Primed Self-priming Pumps
Liquid Primed Self Priming Pumps: They have their own in-built “Priming Chamber” that is filled with liquid in order to “self-prime” the pump. This initial liquid charging must be done for a liquid-primed self-priming pump to prime and work. External auxiliary devices are not required for liquid-primed self-priming pump operation. A Liquid Primed Self Priming Pump works in two phases of operation; “Priming Mode” and “Pumping Mode”.
Compressed Air Primed Self Priming Pumps: In Compressed Air Primed Self Priming Pumps, a jet blows the compressed air into a tapered tube. This creates a vacuum so that the air from the pump casing and suction line is drawn in with the compressed air and exhausted into the atmosphere. A check valve seals out the air from the discharge. Water or other pumping liquid then replaces the air and the pump starts pumping. The potential build-up of solids is also prevented by this type of self-priming pump.
Vacuum Primed Self Priming Pumps: Vacuum Primed Self Priming Pumps consist of a vacuum pump and positive sealing float box installed at the pump discharge. This forces you to pull a vacuum on the pump until it is full of water.
Self Priming Pump Precautions
- Note that, a self-priming pump, too, needs priming for its first operation. A priming chamber or some portion of the volute must be filled prior to start-up.
- The discharge line should not be blocked or pressurized.
- The suction line must be air-tight. Otherwise, the pressure will not be reduced and fluid will not be drawn up the suction line.
- To reduce the priming time, the volume of the suction piping shall be minimized.
- If the liquid contains any solids, a strainer shall be required to keep solids from accumulating in the priming chamber and displacing the priming liquid.
- The pump suction piping should be designed to avoid high points where air can be trapped/accumulated, thus preventing priming.
Advantages of self-priming Centrifugal Pumps
The main advantages that self-priming pumps provide are:
- Can handle a variety of liquids
- Work well with slurries, corrosive liquids, and suspended solids
- Self-priming centrifugal pumps will continue to pump liquids even after the pump is not submerged in a liquid tank or vessel
- As the steps involving pump priming on start-up are eliminated, they are ideal for frequent and intermittent pumping operations.
Disadvantages of self-priming Centrifugal Pumps
The main disadvantages of self-priming pumps are:
- They can’t operate without the presence of the initial priming liquid in the prime chamber.
- Due to the presence of a liquid reservoir, this type of centrifugal pump is usually larger than a standard model, which may cause issues in applications where space is limited.
- To avoid depletion of the pump’s liquid reservoir during self-priming operations, They are required to be as close as possible to production lines.
Anup, this article is very helpful to me. Thank you for preparing this excellent guide and sharing with us.
nice article, my friend