Reciprocating pumps are used where the delivery pressure of the fluid is quite large. In this article, we will discuss on Single-acting Reciprocating Pump. As the name itself indicates that it has a single component of the suction valve, delivery valve, suction pipe, and delivery pipe along with a single piston.
Let’s dive into the article of Reciprocating Pump along with its Introduction, Definition, Diagram, Parts, Working Principle, Advantages, Disadvantages, and Applications.
Introduction of Reciprocating Pump:
Reciprocating Pump is a Positive Displacement type pump that works on the principle of movement of the piston in forwarding and backward directions whereas the Centrifugal pump uses the kinetic energy of the impeller to supply the liquid from one place to another place.
Who Invented Reciprocating Pump?
A Greek inventor and mathematician Ctesibius invents Reciprocating Pump in 200 BC.
Definition of Reciprocating Pump:
It is a machine that converts mechanical energy into hydraulic energy.
Reciprocating pumps are in use where a certain quantity of fluid (mostly sump) has to be transported from the lowest region to the highest region by the application of pressure.
For Example,
When you go to the water servicing of the bike, you can see that the water that is being used is collected from the sump only, and by the application of pressure via a nozzle, water is sprayed onto the vehicle.
Reciprocating Pump Diagram:
The diagram of the Reciprocating Pump was displayed below.
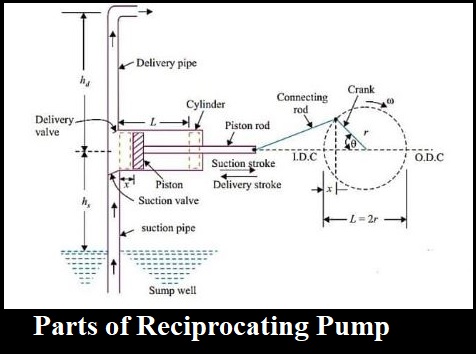
Parts of Reciprocating Pump:
The Parts of the Reciprocating Pump are as follows.
- Water Sump
- Strainer
- Suction Pipe
- Suction Valve
- Cylinder
- Piston and Piston rod
- Crank and Connecting rod
- Delivery valve
- Delivery pipe
An Explanation for the parts of the Reciprocating Pump:
The explanation for the parts of the Reciprocating pump is as follows.
Water Sump:
It is the source of water. From the sump, water is to be transported to the delivery pipes by the usage of the piston.
Strainer:
It acts as a mesh that can screen all the dirt, dust particles, etc. from the sump. If there is no strainer, then the dirt or dust also enters into the cylinder which can jam the region and affects the working of the pump.
Suction Pipe:
The main function of the suction pipe is to collect the water from the sump and send it to the cylinder via a suction valve. The suction pipe connects the water sump and the cylinder.
Suction Valve:
It is a non-return valve which means it can take the fluid from the suction pipe and send it to the cylinder but cannot reverse the water back to it. In this sense, the flow is unidirectional.
This valve opens only during the suction of fluid and closes when there is a discharge of fluid to the outside.
Cylinder:
It is a hollow cylinder made of cast iron or steel alloy and it consists of the arrangement of a piston and piston rod.
Piston and Piston rod:
For suction, the piston moves back inside the cylinder and for discharging of fluid, the piston moves in the forward direction.
The Piston rod helps the piston to move in a linear direction i.e. either the forward or the backward directions.
Crank and Connecting rod:
For rotation, the crank is connected to the power source like an engine, motor, etc. whereas the connecting rod acts as an intermediate between the crank and piston for the conversion of rotary motion into linear motion.
Delivery Pipe:
The function of the delivery pipe is to deliver the water to the desired location from the cylinder.
Delivery valve:
Similar to the suction valve, a delivery valve is also a Non-return valve. During suction, the delivery valve closes because the suction valve is in opening condition and during Discharge, the suction valve is closed and the delivery valve Is opened to transfer the fluid.
These are the various components of the Reciprocating pump. Let’s understand the working principle of it.
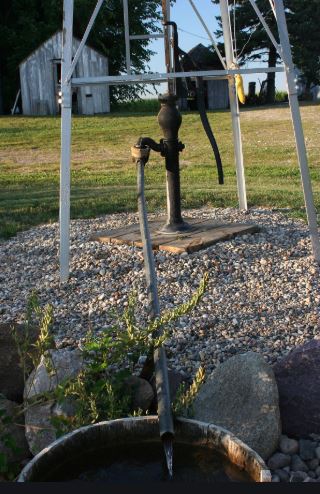
Working Principle of Reciprocating Pump:
When the power supply is given to the reciprocating pump, the crank rotates through an electric motor.
The angle made by the crank is responsible for the movement of the piston inside the cylinder. By referring to the above diagram, the piston moves towards the extreme left of the cylinder when the crank meets position A i.e. θ=0.
Similarly, the piston moves towards the extreme right of the cylinder when the crank meets position C i.e. θ=180.
A partial vacuum in the cylinder takes place when the piston movement is towards the right extreme position i.e. (θ=0 to θ=180.) and that makes the liquid enter into the suction pipe.
This is due to the presence of atmospheric pressure on the sump liquid which is quite less than the pressure inside the cylinder. Therefore, due to the difference in pressure, the water enters the cylinder through a non-return valve.
The water which stays in the volume of the cylinder has to be sent to the discharge pipe via the discharge valve and this can be done when the crank is rotating from C to A i.e. (θ=180 to θ=360) which moves the piston in the forward direction.
Due to the movement of the piston in a forward direction, the pressure increases inside the cylinder which is greater than the atmospheric pressure.
This results in the opening of the delivery valve and closing of the suction valve.
Once the water comes into the delivery valve, it cannot move back to the cylinder because it is a unidirectional valve or non-return valve.
From there, it enters into the delivery pipe so that it can be sent to the required position.
Therefore, in this way, the water is sucked and discharged from the sump to the desired location through the piston inside the cylinder.
Reciprocating Pump Advantages:
The advantages of Reciprocating Pump are as follows.
- No priming is needed in the Reciprocating pump compared to the Centrifugal pump.
- It can deliver liquid at high pressure from the sump to the desired height.
- It exhibits a continuous rate of discharge.
- It can work due to the linear movement of the piston whereas the centrifugal pump works on the rotary velocity of the impeller.
Reciprocating Pump Disadvantages:
The disadvantages of Reciprocating Pumps are as follows.
- The maintenance cost is very high due to the presence of a large number of parts.
- The initial cost of this pump is high.
- The flow rate is less
- Viscous fluids are difficult to pump.
Applications of Reciprocating Pump:
The applications of the Reciprocating Pump are as follows.
- Gas industries
- Petrochemical industries
- Oil refineries
- Vehicle water servicing centers etc.
This is a detailed explanation of the Reciprocating Pump. If you have any doubts, feel free to ask in the comments section. Click here to learn about the differences between a reciprocating pump and a centrifugal pump.
References [External Links]:
Few more useful articles for you.
Types of Pumps used in Process Plants
API 610 Pumps vs ANSI / ASME B73.1 Centrifugal Pumps
Articles related to Pumps
Articles related to Compressors
Hallo Mohammed,
This is a good description.
I would just add a few points regarding the cons:
-reciprocating pumps respect to centrifugal create pulsations on the line that usually need be mitigated by pulsation dampers.
-there are a few more consideration while calculating NPSH since also the Acceleration head should be considered
The max delivery pressure depends on the power of the driver, in fact a PSV on discharge side is mandatory for preserving the integrity of discharge line.
For what concerns the application I also would consider that Reciprocating pumps are very used for chemical dosage due to the precision of flow regulation (with manual regulation of the stroke)
best regards,
Gabriele
Hello everyone
Zafil Ahmad
This is the good knowledge to pump to the maintenance field and I think to the keep it knowledge OK bye to all
Regards
Zafil Ahmad
Hello sir ;
This is a good and complete explanation thanks a lot. But I want to go back and look the paragraph that says
” This is due to presence of atmospheric pressure on the sump liquid which is quite less than the pressure inside the cylinder ”
I think for that case when the piston moves backward and vacuum is created inside the cylinder the pressure inside the cylinder decreases and the atmospheric pressure on the sump liquid becomes greater. THANK YOU SIR