Steel pipes are widely used in the process-piping industries. Various grades of steel pipes are available in processing plants. In this article, we will discuss some of those in brief.
Carbon Steel Pipes
(Temperature Range -29 degree centigrade(C) to 427 degrees C)
This is the most common and cheapest material used in process plants. Carbon steels are used in most general refinery applications. It is routinely used for most organic chemicals and neutral or basic aqueous solutions at moderate temperatures. Carbon steels are extensively used in a temperature range of (-) 29 degrees centigrade to 4270 centigrade
Low-Temperature Carbon steel (LTCS) pipes
(LTCS-Temp range -45.5 degrees C to 427 degrees C)
LTCS can be used at a low temperature of (- 45.5) degrees centigrade. Killed Carbon Steel is defined as those which are thoroughly deoxidized during the melting process. Deoxidation is accomplished by the use of silicon, manganese, and aluminum additions to combine with dissolved gases, usually, oxygen, during steelmaking. This results in cleaner, better-quality steel which has fewer gas pockets and inclusions. Killed carbon steel is specified for major equipment in the following services to minimize the possibility or extent of hydrogen blistering and hydrogen embrittlement:
- where hydrogen is a major component in the process stream.
- where hydrogen sulfide H2S is present with an aqueous phase or where liquid water containing H2S is present.
- Process streams containing any amount of Hydrofluoric acid (HF), boron trifluoride (BF3), or (BF) compounds; or
- Monoethanolamine (MEA) and diethanolamine (DEA) in solutions of greater than 5 weight percent.
Low Alloy Steel Pipe
(Temperature range -29 degrees C to 593 degrees C)
Low Alloy Steel pipes contain one or more alloying elements to improve the mechanical or corrosion-resisting properties of carbon steel. Nickel increases toughness and improves low-temperature properties & corrosion resistance. Chromium and silicon improve hardness, abrasion resistance, corrosion resistance, and resistance to oxidation. Molybdenum provides strength at elevated temperatures. Some of the low alloy steels are listed below.
Carbon 1/2% Moly and Manganese 1/2% Moly:
These low alloy steels are used for higher temperature services and most frequently for intermediate temperatures for their resistance to hydrogen attack. They have the same maximum temperature limitation as killed steel (ASME Code 1000 deg. F) but the strength above 700 deg.F is substantially greater.
1% chrome 1/2% Moly and 1 1/4% Chrome 1/2% Moly:
These alloys are used for higher resistance to hydrogen attack and sulfur corrosion. They are also used for services where temperatures are above the rated temperature for C 1/2 Mo steel.
2 1/4 Chrome 1% Moly and 3% chrome 1% Moly:
These alloys have the same uses as 1 1/4% Cr but have greater resistance to hydrogen attack and higher strength at elevated temperatures.
5% chrome 1/2% Moly:
This alloy is used most frequently for protection against combined sulfur attacks at temperatures above 550 deg.F. Its resistance to hydrogen attack is better than 2 1/4% Cr_ 1% Moly.
9% Chrome 1% Moly:
This alloy is generally limited to heater tubes. It has a higher resistance to high sulfur stocks at elevated temperatures. It also has a maximum allowable metal temperature in oxidizing atmospheres.
Stainless Steel Pipes
(Temperature range -257 degrees C to 538 degrees C)
They are heat & corrosion-resistant, noncontaminating, and easily fabricated into complex shapes. There are three groups of Stainless steel.
- Martensitic Stainless Steel
- Ferritic Stainless Steel and
- Austenitic Stainless Steel
Martensitic stainless steel pipes
Martensitic alloys contain 12-20 percent chromium with a controlled amount of carbon and other additives. Type 410 is a typical member of this group. These alloys can be hardened by heat treatment, which can increase tensile strength. Corrosion resistance is inferior to Austenitic Stainless steel and these are generally used in mildly corrosive environments.
Ferritic stainless steel pipes
Ferritic steels contain 15-30 percent chromium with low carbon content(0.1 percent). The higher chromium content improves its corrosion resistance. A typical member of this group is Type 430. The strength of these can be increased by cold working but not by heat treatment. Type 430 is widely used in nitric acid plants. In addition, it is very resistant to scaling and high temp oxidation up to 800-degree cent.
Austenitic stainless steel pipes
Austenitic steels are the most corrosion-resistant of the three groups. These steels contain 16-26 percent of chromium and 6-22 percent nickel. Carbon is kept low (0.08 percent max) to minimize carbide precipitation. Welding may cause chromium carbide precipitation, which depletes the alloy of some chromium and lowers its corrosion resistance in some specific environments, notably nitric acid. The carbide precipitation can be eliminated by heat treatment(solution annealing). To avoid precipitation special steels stabilized with titanium, niobium, or tantalum have been developed (Types 321,347 & 348). Another approach to the problem is the use of low-carbon stainless steel such as types 304L & 316L with .03 percent max carbon.
The addition of molybdenum to austenitic alloy (types 316, 316L) provides generally better corrosion resistance and improved resistance to pitting. The chromium-nickel steels, particularly the 18-8 alloys, perform best under oxidizing conditions since the resistance depends on an oxide film on the surface of the alloy. Reducing conditions and chloride ions destroy this and bring on the rapid attack. Chloride ions tend to cause pitting and crevice corrosion. When combined with high tensile stresses they can cause stress-corrosion cracking.
Click here to learn about the differences between carbon steel and stainless steel
A detailed list of commonly used steels in hydrocarbon industries is given in the following table:
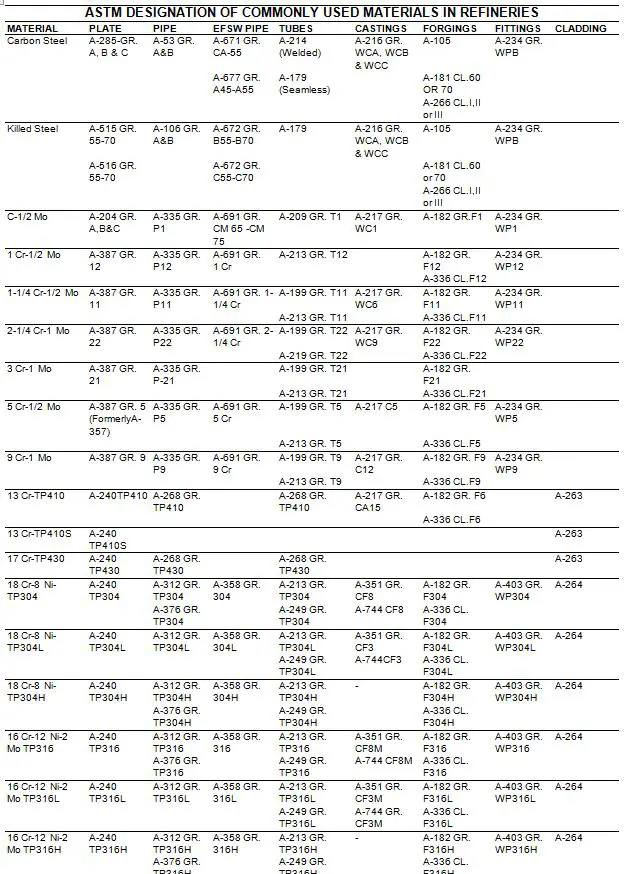
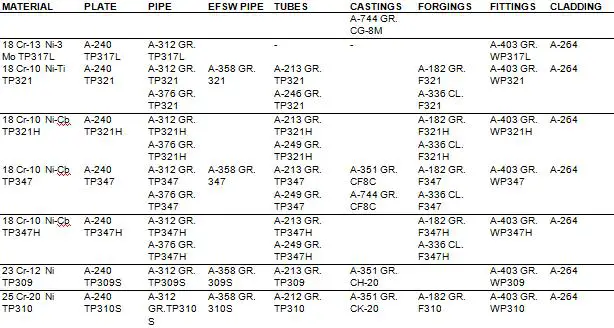
Click here to know about Common Non-Ferrous Materials used in Process Piping Industry
“The detailed list of commonly used steels in hydrocarbon industries is given in following table” which is not displaying. Kindly resubmit
Updated. Pls check now. Thanks a lot.
Only wanna tell that this is very helpful , Thanks for taking your time to write this.
One of the methods of contrast with earthquakes is seismic retrofitting of pipelines.
Therefore, pipeline should be strengthened..
We are in a stainless steel Tubes & Pipe processing business , mechanical & electropolishing mainly for Food , Pharma & Beverages Industry .
We are located in south mumbai .
may i know the reference for “Carbon steels are extensively used in a temperature range of (-) 29 degree centigrade to 427-degree centigrade ” statement?
I didn’t know before that stainless steel has three different types. I will keep that in mind when browsing for steel tubes to use someday. I’d like to make sure that I can find the right reinforcing tubes that I can use for my personal projects at home.
Can you please share the temperature chart for different temperatures and Selection criteria of SS Materials.
Thanks a lot