What is a Thermowell?
Thermowells are cylindrical pressure-tight fittings used to protect the temperature sensors such as thermocouples, thermistors, and bimetal thermometers which are inserted into a pipe or vessel in industrial applications. A thermowell is basically a tube closed at one end and mounted in the process stream. The thermowell acts as a barrier between the sensing element and the process medium. It protects the sensing element against corrosive process media and fluid pressure and velocity.
Thermowells also increase the sensor longevity, allow sensor replacement without draining the system and eliminate the probability of contamination. Thermowells are designed for both high and low-pressure applications.
Thermowells find wide applications in many industrial sectors including refining, cosmetics, petrochemical, food processing, chemicals, Power, pharmaceutical, and other process industries.
Importance of Thermowells
Thermowells play a crucial role in the successful measurement of temperature in industrial processes.
- They Protect the sensor.
- Thermowells ensure that process temperature is passed to the sensor (proper heat transfer).
- Improved heat transfer, results in better accuracy.
- Allow the removal of the sensing element while maintaining a closed system.
Types of thermowell
Thermowells in the piping industry can be classified based on various parameters as listed below:
Depending on the stem design shape, four types of thermowell are available:
- Straight Thermowell
- Stepped thermowell
- Tapered Thermowell, and
- Built-up thermowells
Straight Thermowell
Straight thermowell has the same diameter for the entire insertion length. They are simple to fabricate and possess good rigidity and offer protection against corrosion and erosion.
Stepped Thermowell
Stepped thermowell have stepped diameters; Normally at the tip, they have a smaller (typically 1/2″) diameter while a larger diameter (Typically 3/4″) at the top. Due to decreased thermal inertia at the process end, these thermowells allow smoother velocities and respond more rapidly to temperature changes than their straight counterparts.
Tapered Thermowell
The tapered thermowell has varying diameters (smooth continuous taper) over its full insertion length. Tapered thermowell is suitable for high-velocity heavy-duty applications and possesses a fast response time.
Built-up Thermowell
Built-up thermowells are suitable for very long process insertion lengths. They are available in all the above types but a length of pipe is welded between the tip and process connection to give the long insertion length.
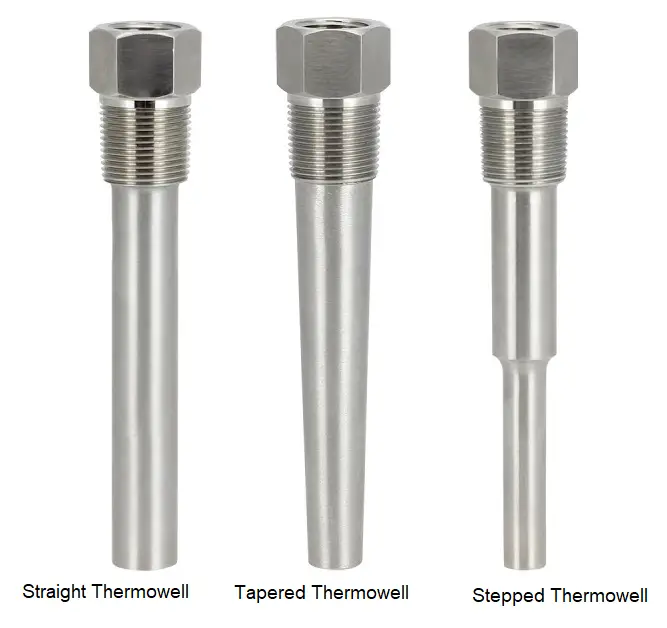
Depending on material types, Two types of Thermowells can be found:
- Pipe Fabricated.
- Bar stock thermowells.
Depending on thermowell end connections, five types of thermowells are available. they are
- Threaded thermowells
- Weld-In thermowells
- Socket Weld thermowells
- Van Stone or Lap Joint flanged thermowells
- Flanged thermowells
Threaded Thermowell
The threaded type thermowell is generally the least costly and most versatile. Threaded thermowells are normally used for non-corrosive applications. They are screwed into the pipe. Their material is such that it can be welded or brazed to provide additional strength.
Weld-in Thermowell
Weld-in thermowell connections are preferred for food and pharmaceutical industries where contaminants from threads must be avoided.
Socket Weld Thermowell
Socket Weld Thermowells are directly welded into the pipe. Its strong connection helps these thermowells to use as a permanent connection. Applications involving very high temperature and pressure use socket-welded thermowell connections.
Van Stone Thermowell
For high-pressure applications, the Van Stone thermowell is ideal. They are usually machined from a solid bar and are placed in a sandwich position between the nozzle and cover flange. Vanstone flange surface is with a phonographic spiral serration.
Flanged Thermowell
A flanged thermowell is designed with a flange at the top end. This type of thermowell is connected to the pipe using nuts and bolts. Flanged thermowell connections are mostly used in high-temperature applications that require frequent replacements.
Flanged thermowells are used in a wide range of industrial applications where temperature measurement is critical. The flange design allows for easy installation and removal of the thermowell without interrupting the process or requiring any special tools.
Some common applications of flanged thermowells include:
- Chemical processing: Flanged thermowells are used to measure the temperature of various chemicals in reactors, vessels, and pipelines.
- Oil and gas: Flanged thermowells are used in oil refineries, pipelines, and gas processing plants to measure the temperature of crude oil, natural gas, and other hydrocarbons.
- Food and beverage: Flanged thermowells are used in food and beverage processing plants to measure the temperature of liquids, such as milk, beer, and juice.
- HVAC: Flanged thermowells are used in heating, ventilation, and air conditioning (HVAC) systems to measure the temperature of air and water.
- Power generation: Flanged thermowells are used in power plants to measure the temperature of steam and other fluids used in power generation.
- Pharmaceutical: Flanged thermowells are used in pharmaceutical manufacturing processes to measure the temperature of various chemicals, drugs, and biological products.
Overall, flanged thermowells are used in any process where temperature measurement is critical and the protection of the temperature sensor is required from harsh process conditions.
There are two other types of thermowell connections; Scruton thermowell and Sanitary thermowell.
Scruton Thermowell
To avoid damages that can be caused due to the mechanical load and critical condition of the process, the Scruton thermowell is designed. They save time and cost on re-work at the site.
Sanitary Thermowell
A sanitary thermowell is used for isolation and protection of the sensing element of any temperature instrument. To avoid bacterial build-up, Sanitary thermowells are built with hygienic connection.
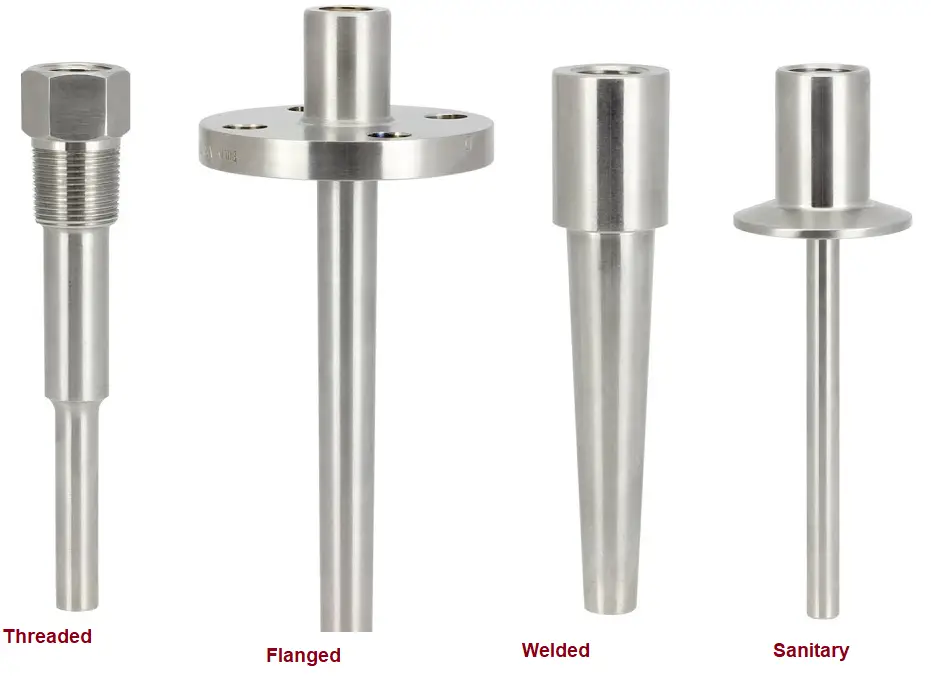
Materials of Thermowells
The right material increases the longevity of a thermowell. Material selection of thermowell will depend on the chemical, temperature, and flow rate of the process fluid. With an increase in temperature and fluid concentration, the corrosive effects of chemicals normally increase. At the same time, suspended particles of the fluid will cause erosion. So all these parameters need to be addressed while selecting thermowell material. Some of the most frequently used thermowell materials are listed below:
- Carbon Steel
- Brass
- SS 316 / SS 304
- SS316 with Teflon / Zirconium Coated or Tantalum / Titanium steathing.
- Graphite
- Chromium/molybdenum steels
- Incoloy
- Inconel
- Monel
- Hastelloy
- Haynes Alloy
- Titanium
- Aluminum
However, the most widely used thermowell material is stainless steel as it is cost-effective and highly resistant to heat and corrosion. For pressurized vessels, Chromium/molybdenum steel is used. Cobalt, nickel, chromium, and tungsten constitute the Haynes alloy that is widely used for sulphidising, carburizing, and chlorine-containing environments. The use of carbon steel thermowell is only limited to low-temperature pressure applications due to its very low resistance to corrosion.
Thermowell Insertion Length
The length from the connection point to the thermowell tip is known as the insertion length of the thermowell (U dimension in Fig. 4). For better accuracy, the thermowell insertion length should be long enough. This will allow the entire temperature-sensitive portion of the measurement device to extend into the medium being measured.
For measuring the liquid temperatures using a temperature sensor, the device must be extended into the solution for the length of the temperature-sensitive portion plus a minimum of one inch (25 mm). For gaseous or air service, it should be immersed for the length of the temperature-sensitive segment plus an additional three inches. The temperature-sensitive section of a thermocouple or thermistor is short; therefore, the insertion length of the thermowell can be shorter for these devices. Whereas, the temperature-sensitive section of bimetal thermometers, RTDs, and liquid in glass thermometers is between 1″ and 2″ hence, the thermowells must be immersed at least 2½” in liquid for accurate measurements.
Thermowell Installation
Lagging is used when the thermowell is installed through an insulation media on a pipeline or equipment.
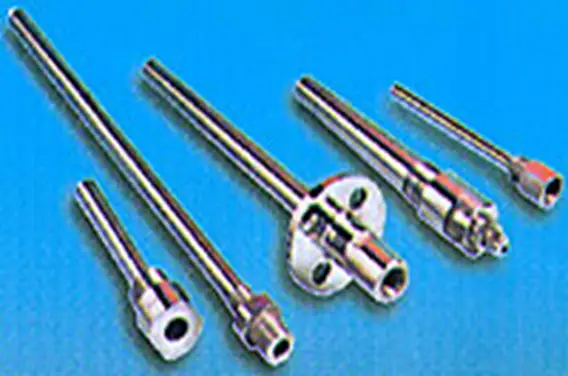
An improperly specified thermowells, will result in:
- Failure due to poor welding practices.
- Poor compatibility with the temperature and media.
- Inadequate temperature transfer.
- Incompatibility with the process velocity leads to failure due to vibration.
- The gap between the OD of the thermocouple sheath and the ID of the thermowell must be very close.
- The bore of the thermowell must be uniform and linear.
Design of Thermowells
- The design of the thermowell should cater to process media, pressures, temperatures, velocity, specific gravity, etc.
- Proper MOC (Material of construction).
- Wall thickness Vs response time.
- Bore diameter, Insertion length, Taper requirements, Overall length, etc.
- Vortex shedding
- Calculate the Vibration using Wake Frequency methods.
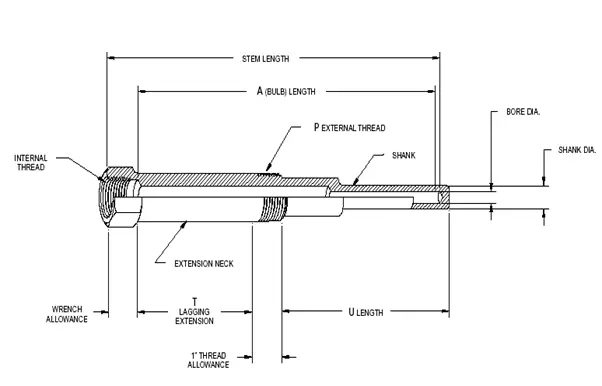
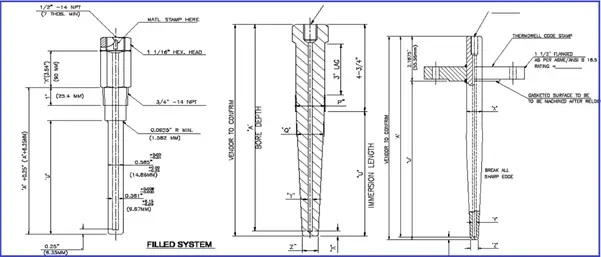
Thermowell Installation Requirements
Refer to Fig. 6 and Fig. 7
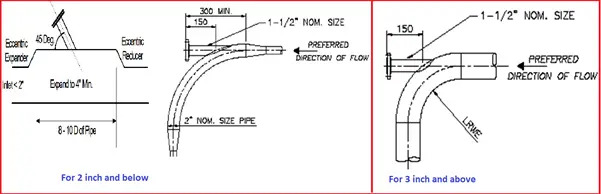
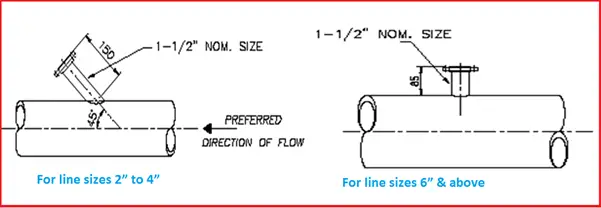
Selection of a Thermowell
The key parameters to consider while selecting a thermowell are:
- Process connection size and type.
- Process insertion length
- Lagging length
- Extension length
- Sensor length
- Interior diameter (bore) for the sensor or thermometer
- Internal threads for the sensor or thermometer
- The shape of the thermowell (straight, stepped, tapered, built-up)
- Material of construction
Thermowell Design Code
Piping Designers follow ASME PTC 19.3 for guidelines regarding thermowells.
Thermowell Working Principle
The working principle of a thermowell is based on the concept of thermal conductivity, where heat flows from a region of high temperature to a region of low temperature. A thermowell is a protective casing that is used to house a temperature sensor, such as a thermocouple or a resistance temperature detector (RTD). The thermowell is inserted into the process being measured, and the temperature sensor measures the temperature of the process fluid or environment.
The thermowell is designed to protect the temperature sensor from harsh process conditions, such as high pressure, high temperature, and corrosive fluids. The thermowell is typically made of durable material, such as stainless steel or ceramic, and has a closed end that protects the temperature sensor from direct contact with the process fluid. The thermowell also has an opening that allows the temperature sensor to come in contact with the process fluid and measure the temperature.
The thermowell works by allowing the heat from the process fluid to flow through the wall of the thermowell and come into contact with the temperature sensor. The thermal conductivity of the thermowell material is chosen such that it allows for efficient heat transfer while also providing adequate protection for the temperature sensor. The thermowell also serves to isolate the temperature sensor from the process fluid, allowing for accurate temperature measurement even in harsh process conditions.
Overall, the thermowell working principle is based on the concept of thermal conductivity, where the thermowell material allows for efficient heat transfer while protecting the temperature sensor from harsh process conditions.
Thermowell Vibrations
As thermowells are immersed in the process flow, a bending force will be experienced by them. Additionally, depending on the fluid velocity and thermowell diameter, a certain vibrational frequency will be generated leading to thermowell vibration. In general, such vibrations are of small magnitude and considered negligible. But, the thermowell must have sufficient stiffness and rigidity to absorb those vibrations. In such a scenario, tapered thermowells are preferred as they have more stiffness. However, if the generated frequency approaches the natural frequency of the thermowell, it can cause severe unacceptable vibrations. ASME PTC 19.3 provides formulas to determine if a thermowell is acceptable for a given application. Many thermowell manufacturers have generated a velocity rating table that recommends the maximum fluid velocity for their thermowells to avoid resonance.
Wake frequency calculation following the guidelines of ASME PTC 19.3 standard is performed to prove that the thermowell has the strength to handle hydrostatic pressure limit and dynamic static stress in relation to process conditions. Prior to the manufacturing of thermowell, these types of calculations ensure that the thermowells can cope with the stress and strain produced by any kind of process media.
Information required for Purchasing Thermowell
The following information must be supplied to the thermowell manufacturer/vendor while placing an order.
- Process Connection Size
- Thermowell Insertion Length
- Lagging extension
- Shank configuration
- Process Connection type
- Nominal Bore
- Thermowell Material
- Process Design temperature and pressure
Disadvantages of Thermowell
The main disadvantages of a thermowell are:
- Compared to a naked sensor, slightly slower response to temperature changes.
- Resistance to flow medium.
- Increased cost for purchasing a thermowell.
Differences between a Thermowell and a Thermocouple: Thermowell vs Thermocouple
A thermowell and a thermocouple are both used for temperature measurement, but they are different in their design, function, and application. Here are some of the main differences between the two:
- Design: A thermowell is a protective tube that is inserted into a process or fluid to provide a barrier between the sensor and the environment. A thermocouple, on the other hand, is a sensor that measures temperature by generating a small voltage in response to a temperature difference.
- Function: The purpose of a thermowell is to protect the temperature sensor, usually a thermometer or a thermocouple, from damage or corrosion in harsh environments, high pressures, or high-velocity fluid flows. The thermowell provides a barrier between the sensor and the environment while allowing the sensor to detect the temperature of the process fluid. A thermocouple, on the other hand, is a sensor that directly measures temperature by generating a voltage in response to a temperature difference.
- Application: Thermowells are typically used in process industries such as oil and gas, chemical processing, and food and beverage production. They are often used to protect temperature sensors that are installed in pipelines, tanks, and vessels. Thermocouples, on the other hand, can be used in a wide range of applications, including temperature monitoring in HVAC systems, laboratory equipment, and industrial processes.
In summary, a thermowell is a protective barrier that surrounds a temperature sensor, while a thermocouple is a temperature sensor that directly measures temperature. They have different functions and applications but can both be used for temperature measurement in various industries and applications.
Thermowell Probe
A thermowell probe is a temperature measurement device that consists of a temperature sensor, such as a thermocouple or a resistance temperature detector (RTD), housed inside a protective tube called a thermowell. The thermowell is typically made of metal and is inserted into a process or fluid, providing a barrier between the temperature sensor and the environment. The thermowell is designed to protect the temperature sensor from damage or corrosion caused by harsh process conditions such as high temperatures, high pressures, and corrosive fluids.
The thermowell probe allows temperature measurement without directly exposing the temperature sensor to the process fluid or environment. The thermowell can be removed and replaced if necessary without affecting the process or equipment, making it a useful tool in many industries, including chemical, oil and gas, and food and beverage production. The selection of a thermowell probe depends on factors such as the process conditions, the type of temperature sensor used, and the required accuracy and response time.
Thermowell Temperature Sensor
A thermowell temperature sensor is a device that measures temperature using a thermowell as a protective barrier between the temperature sensor and the process fluid or environment. The temperature sensor can be a thermocouple or a resistance temperature detector (RTD) and is typically housed inside the thermowell, which is inserted into the process or fluid being measured. The thermowell protects the temperature sensor from damage caused by harsh process conditions such as high temperatures, high pressures, and corrosive fluids.
The thermowell temperature sensor is commonly used in industries such as chemical processing, oil and gas, and food and beverage production, where accurate temperature measurement is essential for maintaining the quality and safety of products and processes. The thermowell temperature sensor can be installed directly into pipelines, tanks, and vessels, allowing temperature measurement of liquids, gases, and solids. The thermowell can be designed to meet various requirements, such as high temperature and pressure ratings, different materials of construction, and various process connections. The selection of a thermowell temperature sensor depends on factors such as the process conditions, the type of temperature sensor used, and the required accuracy and response time.
SS 316 = Stainless Steel, grade 316
Why flanged Thermowell have minimum 300 # even in 150 # Class pipe.
do you have wake frequency calculation in excel sheet. ?can you post it in your blog.