In the world of pipe fittings and connections, there are numerous options available to ensure the safe and efficient transport of fluids. One such option is the Threadolet. Threadolets are a versatile and widely used pipe fitting that plays a crucial role in various industries, including oil and gas, petrochemical, and manufacturing. In this comprehensive guide, we will delve into the world of Threadolets, exploring their design, applications, advantages, and installation procedures.
What is a Threadolet?
A Threadolet is a self-reinforced branch connection pipe fitting that allows for the connection of a smaller diameter pipe to a larger one. It features a threaded connection on one end and a welded connection on the other. Threadolets are designed to reduce stress concentrations and offer a smooth transition between the main pipe and the branch pipe, minimizing turbulence and pressure drop.
Threadolets are often used when connecting small-diameter pipes, instrument lines, or control lines to a larger pipe or vessel. They are particularly useful in applications where a strong, leak-free connection is essential. Threadolet pipe fittings are developed by the Company named Bonney Forge and because of that, they are also well known as Bonney Forge Threadolet. Fig. 1 provides an example of a threadolet.
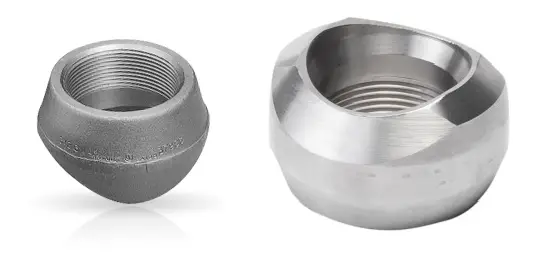
Types of Threadolets
Based on the pressure-temperature rating class there are two types of threadolets. They are:
- Class 3000 threadolets, and
- Class 6000 threadolets
Threadolet Dimensions
Threadolet dimension basically means Outer and Inner diameter, Length of the hub, and thread dimensions. MSS-SP-97 provides the dimensional requirements for threadolet branch connections. Typical threadolet connections for each of the above-mentioned pipe classes are given below. Refer to these tables (Tables 1 and 2) along with the image in Fig. 2 below.
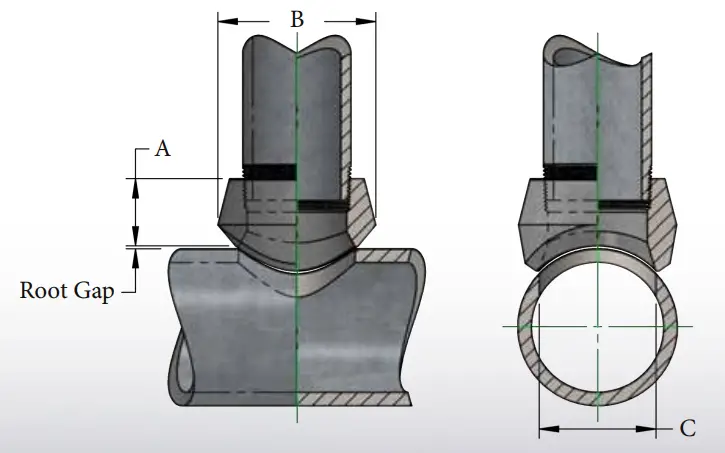
Class 3000 Threadolet Dimensions
The dimensions of class 3000 threadolets are given in Table 1.
Dimensions (Inches) | Dimensions (mm) | |||||||
Outlet Size (NPS) | A | B | C | Weight in LB | A | B | C | Weight in KG |
1/8 | 3/4 | 1 | 5/8 | 0.100 | 19.05 | 25.40 | 15.88 | 0.05 |
1/4 | 3/4 | 1 | 5/8 | 0.100 | 19.05 | 25.40 | 15.88 | 0.05 |
3/8 | 13/16 | 1 1/4 | 3/4 | 0.200 | 20.64 | 31.75 | 19.05 | 0.09 |
1/2 | 1 | 1 7/16 | 15/16 | 0.250 | 25.40 | 35.72 | 23.81 | 0.11 |
3/4 | 1 1/16 | 1 3/4 | 1 3/16 | 0.350 | 26.99 | 43.66 | 29.37 | 0.16 |
1 | 1 5/16 | 2 1/8 | 1 7/16 | 0.600 | 33.34 | 50.80 | 36.51 | 0.27 |
1 1/4 | 1 5/16 | 2 9/16 | 1 3/4 | 0.900 | 33.34 | 65.09 | 44.45 | 0.41 |
1 1/2 | 1 3/8 | 2 7/16 | 2 1 | 1.000 | 34.93 | 72.23 | 50.80 | 0.45 |
2 | 1 1/2 | 3 1/2 | 2 9/16 | 1.750 | 38.10 | 88.11 | 65.09 | 0.79 |
2 1/2 | 1 13/16 | 4 1/16 | 3 | 3.000 | 46.04 | 103.19 | 76.20 | 1.36 |
3 | 2 | 4 13/16 | 3 11/16 | 4.350 | 50.80 | 122.24 | 93.66 | 1.97 |
3 1/2 | 2 1/8 | 5 1/4 | 4 | 5.750 | 53.98 | 132.56 | 101.60 | 2.61 |
4 | 2 1/4 | 6 | 4 3/4 | 7.100 | 57.15 | 151.61 | 120.65 | 3.22 |
5 | 2 5/8 | 7 5/16 | 5 9/16 | 12.000 | 66.68 | 185.74 | 141.29 | 5.44 |
6 | 2 3/4 | 8 5/8 | 6 11/16 | 15.300 | 69.85 | 219.08 | 169.86 | 6.94 |
Class 6000 Threadolet Dimensions
The dimensions for class 6000 threadolet connections are provided in Table 2.
Dimensions (Inches) | Dimensions (mm) | |||||||
Outlet Size (NPS) | A | B | C | Weight in LB | A | B | C | Weight in KG |
1/4 | 1 1/8 | 1 3/8 | 9/16 | 0.300 | 28.58 | 34.13 | 14.29 | 0.14 |
3/8 | 1 1/8 | 1 3/8 | 9/16 | 0.300 | 28.58 | 34.13 | 14.29 | 0.14 |
1/2 | 1 1/4 | 1 3/4 | 3/4 | 0.450 | 31.75 | 43.66 | 19.05 | 0.20 |
3/4 | 1 7/16 | 2 | 1 | 0.750 | 36.51 | 49.61 | 25.40 | 0.34 |
1 | 1 9/16 | 2 7/16 | 1 5/16 | 1.250 | 39.69 | 61.91 | 33.34 | 0.57 |
1 1/4 | 1 5/8 | 2 3/4 | 1 1/2 | 1.600 | 41.28 | 69.06 | 38.10 | 0.73 |
1 1/2 | 1 11/16 | 3 1/4 | 1 15/16 | 1.950 | 42.86 | 82.55 | 49.21 | 0.88 |
2 | 2 1/16 | 4 1/16 | 2 3/4 | 5.000 | 55.03 | 102.39 | 69.85 | 2.27 |
Threadolet Materials
Threadolets, like other pipe fittings, are manufactured from a variety of materials to suit different applications. The choice of material depends on factors such as the type of fluid being transported, temperature and pressure conditions, corrosion resistance requirements, and specific industry standards. Below are some common materials used for Threadolets:
Threadolet Material | Material Specification |
Carbon Steel | ASTM A105 |
Staniless Steel | ASTM A182 Gr F-304, F-316, F-309, F-321, F-317 |
DSS | ASTM A182 Gr UNS-F44, F45, F51, F53, F55, F60, F61 |
LTCS | ASTM A350 Gr LF2, LF3 |
Alloy Steel | ASTM A182 Gr F1, F5, F9, F11, F22, F91 |
Nickel Alloy | UNS N10276, UNS 2200, UNS 2201, UNS 8020, UNS 6600, UNS 8825 |
Copper Nickel | ASTM SB 61, 62, 151, 152 |
Applications of Threadolets
Threadolets find applications in a wide range of industries due to their versatility and ability to create strong, reliable connections. Some common applications include:
- Oil and Gas Industry: Threadolets are extensively used in the oil and gas sector for connecting control lines, instrumentation, and small-diameter pipes to main pipelines and equipment.
- Chemical and Petrochemical Industry: Threadolets are employed to connect auxiliary lines, such as sampling lines and vent lines, to process pipelines and vessels.
- Power Plants: Threadolets are used in power generation plants to connect various instrumentation and control lines to the main steam and water lines.
- Manufacturing Industry: Threadolets are utilized for connecting coolant lines and lubrication systems in manufacturing processes.
Advantages of Threadolets
The popularity of Threadolets can be attributed to several key advantages:
- Strength and Reliability: Threadolets create strong and leak-free connections, reducing the risk of pipe failures and leaks.
- Versatility: Threadolets can be used in a wide range of applications and are available in various sizes and materials.
- Reduced Stress Concentrations: The design of Threadolets helps distribute stress evenly, reducing the risk of stress-related failures.
- Easy Installation: Threadolets are relatively easy to install, making them a cost-effective choice for many applications.
Installation of Threadolets
Installing Threadolets requires precision and expertise. Here are the basic steps involved:
- Determine the appropriate location for the Threadolet on the main pipe.
- Prepare the surface by cleaning and beveling the area where the Threadolet will be welded.
- Weld the Threadolet onto the main pipe using the appropriate welding technique and filler material.
- Connect the branch pipe to the threaded end of the Threadolet using a suitable thread sealant or tape.
- Perform pressure testing and inspection to ensure the integrity of the connection.
Conclusion
Threadolets are a crucial component in the world of pipe fittings, enabling the safe and efficient connection of smaller pipes to larger ones in a wide range of industries. Their strength, reliability, and versatility make them a preferred choice for many applications. Understanding the different types, design considerations, and installation procedures of Threadolets is essential for ensuring their proper use and performance in various industrial settings.