When it comes to construction projects, whether it’s a towering skyscraper, oil and gas facility, chemical and petrochemical complex, a residential building, or a simple home renovation, ensuring the strength and stability of the structure is paramount. One crucial element that contributes to the overall integrity and reliability of concrete structures is the use of anchors. Anchors play a vital role in connecting various components, reinforcing structural elements, and providing stability in concrete applications. In this article, we will delve into the world of anchors in concrete, exploring their types, functions, and the importance of proper installation techniques.
What are Concrete Anchors and How Do They Work?
Anchors, in the context of concrete construction, are devices or systems designed to attach or connect elements to a concrete surface. They are typically embedded into the concrete to provide a secure and lasting connection. Concrete anchors serve as a reliable attachment to secure objects in place. Anchors can distribute loads, resist forces, and prevent movement or failure of structural components. By creating a bond between the concrete and the anchor, they enhance the overall strength and stability of the structure.
A concrete anchor works by creating a secure connection between a concrete surface and another object or structural element. It prevents movement, rotation, or detachment of the attached component, enhancing the overall strength and stability of the structure. The working mechanism of a concrete anchor depends on its type, but the fundamental principle is to generate a bond that distributes and resists applied loads. The concrete anchors work in such a way that they provide a means for securing objects without damaging the concrete itself. They are found in various shapes and sizes, ensuring that for any project requirements, there is a suitable concrete anchor available. Fig. 1 below shows a typical example of concrete anchors.
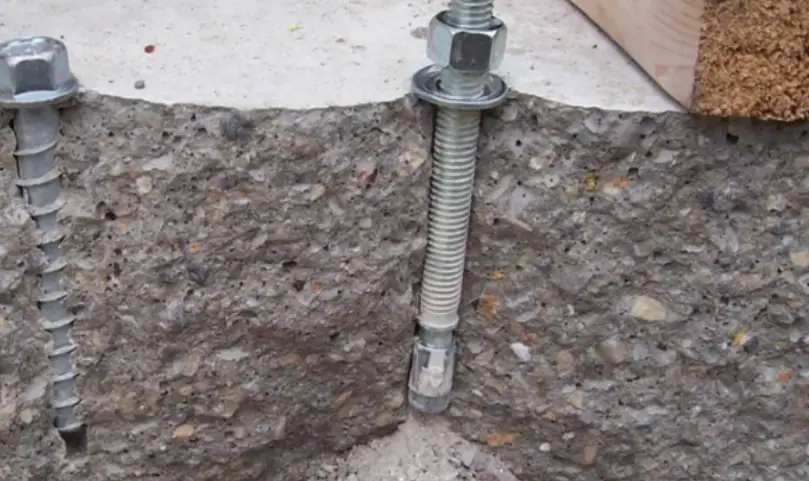
Types of Concrete Anchors
There are various types of concrete anchors used in the construction industry to cater to different needs. Broadly, the following concrete anchor types are widely used for industrial applications:
- Sleeve Anchors
- Wedge Anchors
- Acoustical Wedge Anchors
- Drop in Anchors
- Double Expansion Shield Anchors
- Lag Shield Expansion Anchors
- Hammer Drive Pin Anchors
- Split Drive Anchor
- Threaded Rod Anchor
- Strike Anchor
- Plastic Toggle Anchors
- Lag Anchor
- Tapcon Concrete Anchor
- Kaptoggle Hollow Wall Anchors
- Machine Screw Angles Anchors
- Masonry Screws
- Sammys Screws
- Toggle Wing Hollow Wall Anchors
Sleeve Anchors:
Sleeve anchors are versatile anchors suitable for a wide range of applications. They consist of a threaded bolt with a cone-shaped expander sleeve and a nut. When the anchor is inserted into a pre-drilled hole in the concrete, tightening the nut pulls the cone-shaped sleeve against the walls of the hole, causing it to expand and create a secure connection. Sleeve concrete anchors are easy to install and provide a durable and reliable solution.
Wedge Anchors:
Wedge anchors are designed for heavy-duty applications that require high load capacity. They consist of a threaded bolt with a wedge-shaped expansion clip at the bottom and a nut and washer. During installation, the anchor is inserted into a pre-drilled hole, and as the nut is tightened, the wedge-shaped clip expands, creating a secure grip between the anchor and the concrete. Due to their solid, lasting hold on even the most abrasive surfaces, Wedge anchors are extremely safe for use in permanent applications requiring incredible strength and long-lasting resistance.
Acoustical Wedge Anchors:
Acoustical wedge anchors are specifically designed for attaching acoustic panels and other similar materials to concrete surfaces. They feature a specially designed wedge-shaped clip that provides a strong grip and helps minimize vibration transmission.
Drop-in Anchors:
Drop-in anchors are internally threaded cylindrical anchors. They are placed into a pre-drilled hole in the concrete and then a threaded rod or bolt is inserted into the anchor. As the bolt is tightened, it expands the anchor and creates a secure connection.
Double Expansion Shield Anchors:
Double expansion shield anchors consist of a tubular-shaped shield with two expansion cones and a machine screw. When the anchor is inserted into a pre-drilled hole and the screw is tightened, the expansion cones expand radially, providing a secure hold within the concrete.
Lag Shield Expansion Anchors:
Lag shield expansion anchors are used to attach wood or metal components to concrete. They consist of a short, hollow cylindrical shield and a lag screw. The shield is inserted into a pre-drilled hole, and when the lag screw is driven into the shield, it expands and forms a tight grip within the concrete.
Hammer Drive Pin Anchors:
Hammer drive pin anchors, also known as hammer drive anchors or nail-in anchors, are simple and quick to install. They consist of a metal pin or nail with a nail head and a preassembled expansion sleeve. The pin is hammered into a pre-drilled hole, and as it goes in, the sleeve expands and secures the anchor in place.
Split Drive Anchor:
Split drive anchors feature a split cylindrical body with a wedge-shaped end and a lip. The anchor is inserted into a pre-drilled hole, and as a nail or screw is driven into the anchor, it causes the split body to expand, providing a secure hold in the concrete.
Threaded Rod Anchor:
Threaded rod anchors, as the name suggests, are used to attach threaded rods to concrete surfaces. They consist of a threaded sleeve or a nut with an internally threaded section that is embedded into the concrete. The threaded rod is then screwed into the anchor to create a secure connection.
Strike Anchor:
Strike anchors are heavy-duty anchors that provide excellent holding strength. They feature a cylindrical body with a cone-shaped end and a metal pin. The anchor is inserted into a pre-drilled hole, and a hammer or striking tool is used to drive the pin into the anchor, causing the cone-shaped end to expand and create a strong connection.
Plastic Toggle Anchor:
Plastic toggle anchors, also known as butterfly anchors, are used for light-duty applications. They consist of a plastic sleeve with two spring-loaded wings. When the anchor is inserted into a pre-drilled hole and the screw is tightened, the wings open behind the wall, providing stability and holding the anchor in place.
Lag Anchor:
Lag anchors are used for attaching wood or metal components to concrete surfaces. They consist of a lag screw threaded into a shield or an anchor body. The shield is inserted into a pre-drilled hole, and as the lag screw is tightened, it pulls the shield against the walls of the hole, creating a secure connection.
Tapcon Concrete Anchor:
Tapcon concrete anchors are specifically designed for fastening materials to concrete, brick, or block. They consist of a hardened steel screw with threads specially designed for concrete. These anchors are self-tapping, meaning they can be directly drilled into the material without the need for pre-drilling. As the screw is driven into the concrete, it creates threads and forms a strong bond.
Kaptoggle Hollow Wall Anchors:
Kaptoggle hollow wall anchors are primarily used for attaching objects to hollow walls, such as drywall. They consist of a spring-loaded toggle mechanism that expands behind the wall when the screw is inserted. The toggle provides stability and prevents the anchor from pulling out of the wall.
Machine Screw Angle Anchors:
Machine screw angle anchors, also known as Zamac anchors, are versatile anchors suitable for various materials, including concrete. They consist of a zinc alloy anchor body with a pre-assembled screw. The anchor is inserted into a pre-drilled hole, and as the screw is tightened, it expands the anchor, creating a secure hold.
Masonry Screws:
Masonry screws, often made of hardened steel, are designed for fastening materials to concrete, brick, or block. They feature a threaded shank and a hexagonal or Phillips’s head for easy installation using a screwdriver or drill. These screws are self-tapping and create their own threads as they are driven into the masonry.
Sammys Screws:
Sammy’s screws, also known as vertical anchoring systems, are used for attaching objects to concrete or steel surfaces. They consist of a threaded screw with a pointed end and a pre-assembled anchor body. The screw is driven through the object and into the anchor, which expands behind the surface, providing a secure connection.
Toggle Wing Hollow Wall Anchors:
Toggle wing hollow wall anchors are specifically designed for hollow walls, such as drywall. They consist of a spring-loaded toggle mechanism attached to a threaded bolt. When the anchor is inserted into the wall and the bolt is tightened, the wings on the toggle expand, gripping the backside of the wall and providing stability.
Each of these concrete anchor types offers unique features and advantages, allowing for a wide range of applications and ensuring secure and reliable connections between various materials and concrete surfaces. It is important to select the appropriate anchor type based on the specific requirements of the project to ensure optimal performance.
Materials for Concrete Anchors
Concrete anchors are available in a variety of materials, each chosen based on the specific application requirements and environmental conditions. The common materials used for concrete anchors include:
- Steel: Steel is one of the most common materials for concrete anchors due to its strength, durability, and resistance to corrosion. Steel anchors can withstand heavy loads and provide long-lasting performance. They are often made of carbon steel, stainless steel, or coated steel to enhance corrosion resistance.
- Zinc Alloy: Zinc alloy anchors, commonly known as Zamac anchors, are widely used for light to medium-duty applications. They offer good corrosion resistance and are cost-effective. Zinc alloy anchors are often used in drywall, masonry, and other non-structural applications.
- Brass: Brass anchors are known for their corrosion resistance and aesthetic appeal. They are commonly used in applications where appearance is important, such as decorative fixtures or architectural elements. Brass anchors may be preferred in indoor or low-corrosion environments.
- Nylon: Nylon anchors are lightweight, non-metallic anchors that offer excellent resistance to corrosion, chemicals, and electrical conductivity. They are commonly used in applications where insulation or non-conductive properties are required, such as electrical installations or areas with potential contact with water or chemicals.
- Plastic: Plastic anchors, typically made of high-density polyethylene (HDPE) or other durable plastics, are lightweight and resistant to corrosion. They are commonly used for light-duty applications or in areas where electrical insulation is necessary. Plastic anchors are often used in drywall, lightweight fixtures, or low-load applications.
- Epoxy: Epoxy anchors utilize an adhesive system made of epoxy resin. The epoxy material provides exceptional strength, chemical resistance, and adhesion to both the anchor and the concrete. Epoxy anchors are commonly used in high-load or critical applications where a strong bond is required, such as structural connections or heavy equipment installations.
It’s important to consider the material compatibility with the concrete and the specific environmental conditions in which the anchor will be installed. Proper material selection ensures the anchor’s longevity, reliability, and resistance to corrosion or degradation over time.
Importance of Proper Anchor Installation
Proper anchor installation is critical to ensure the effectiveness and reliability of the anchoring system. Here are a few key considerations for installation:
- Load Capacity: Anchors must be selected based on the expected load requirements. It is essential to choose anchors that can withstand the anticipated loads to prevent failures or structural compromises.
- Concrete Condition: The condition and quality of the concrete play a significant role in anchor performance. Factors such as compressive strength, age, moisture content, and the presence of cracks can affect the anchor’s ability to form a secure bond. It is crucial to assess the concrete condition and address any issues before anchor installation.
- Correct Hole Preparation: The size and depth of the hole for anchor installation must be accurate. It is important to follow manufacturer guidelines and industry standards for hole diameter, depth, and cleanliness to ensure optimal anchoring performance.
- Installation Techniques: Anchors should be installed using the appropriate tools and techniques. This includes ensuring proper torque or tension, avoiding overtightening, and following any specific installation procedures provided by the anchor manufacturer.
Applications of Anchors in Concrete
Anchors find extensive use in a wide range of concrete applications:
- Structural Connections: Anchors play a crucial role in connecting structural components such as columns, beams, and walls, providing stability and load transfer.
- Façade and Cladding Systems: Anchors are used to attach cladding systems to the concrete structure, ensuring their secure attachment and resistance to wind loads and other external forces.
- Mechanical and Electrical Installations: Anchors are essential for securing mechanical equipment, HVAC systems, electrical panels, and piping to concrete surfaces.
- Safety Systems: Anchors are utilized in the installation of safety equipment, such as guardrails, handrails, and lifeline systems, ensuring the protection of workers and preventing accidents.
- Interior Fixtures: Anchors are commonly employed in the installation of fixtures like shelves, cabinets, and wall-mounted TVs, providing stability and preventing accidental tipping or falling.
- Concrete Reinforcement: In certain cases, anchors are used to reinforce concrete structures by connecting additional steel elements or reinforcing bars, enhancing the overall strength and durability.
Maintenance and Inspection
Regular maintenance and inspection of anchors are crucial to ensure their continued effectiveness and reliability. Periodic assessments should be conducted to check for signs of corrosion, degradation, or loosening. If any issues are identified, appropriate actions such as anchor replacement or repair should be taken promptly to maintain the structural integrity of the concrete.
Conclusions
Anchors play an indispensable role in concrete construction, contributing to the strength, stability, and reliability of structures. Whether it’s for connecting structural components, attaching fixtures, or reinforcing concrete elements, the proper selection and installation of anchors are crucial for ensuring optimal performance. By understanding the different types of anchors, following recommended installation techniques, and conducting regular maintenance, builders, and engineers can create concrete structures that stand the test of time, providing safety and durability for years to come.