In industries where safety is paramount, like oil and gas, monitoring environmental conditions is essential. One such tool that plays a critical role in these industries is the wind sock. This seemingly simple fabric tube serves as an effective indicator of wind direction and speed, ensuring the safety and efficiency of operations in high-risk environments.
This comprehensive guide will help you understand the importance of wind socks in the oil and gas industries, their role in maintaining safety, how they work, the materials used in their construction, installation, and maintenance, and standards and regulations.
What is a Wind Sock? Defining a Wind Sock
A wind sock, sometimes called a wind cone, is a conical tube designed to indicate wind direction and relative wind speed. Wind socks are used in meteorology, aviation, and chemical plants for safety reasons. Made from light, resilient materials such as nylon or PVC, wind socks are often brightly colored or have reflective surfaces to enhance visibility. They are usually white, orange, or red for maximum contrast against most backgrounds.
The open end of a wind sock faces the wind, aligning with the wind direction – if the wind is coming from the north, the sock points south. The wind speed is indicated by the angle at which the sock stands relative to the mounting pole; a fully extended sock often denotes high winds.
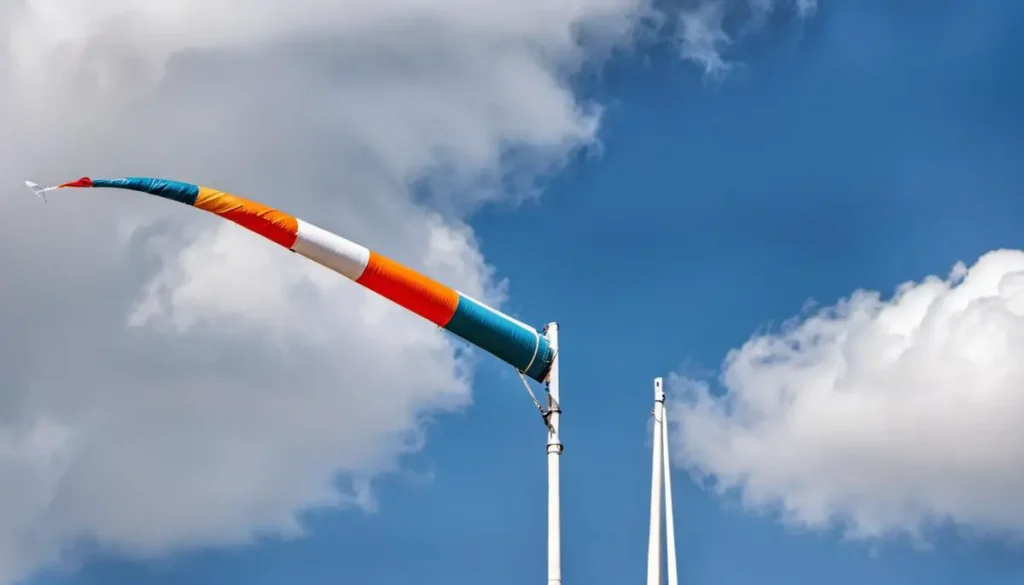
Also known as a wind indicator or windbag, a Windsock is a simple yet effective tool designed to provide real-time information about wind direction and speed. Typically made of durable, weather-resistant materials such as nylon or vinyl, wind socks are mounted on a tall mast or pole at various strategic locations within oil and gas facilities. Their distinctive shape, resembling a truncated cone, allows them to respond to even slight changes in wind direction and intensity.
The Importance of Wind Socks in the Oil and Gas Industries
Ensuring Safety in High-Risk Environments
The oil and gas industries are notorious for operating in some of the most dangerous environments. Whether it’s offshore platforms, onshore drilling rigs, or refineries, these facilities handle highly flammable and hazardous materials. Accidents, such as gas leaks, chemical spills, and fires, are ever-present risks.
In such environments, being able to quickly and accurately determine wind direction and speed can make the difference between life and death. During an emergency, such as a gas leak or chemical release, knowing which way the wind is blowing allows personnel to take appropriate action—whether that means evacuating in a safe direction or containing the release. Windsocks provide an immediate, low-tech, and highly visible method of obtaining this crucial information.
Fire Prevention and Response
Flammable gases and liquids are the backbone of the oil and gas industries. Even a minor leak or spark can lead to catastrophic fires. Wind socks are vital for fire prevention, as wind speed and direction determine the behavior of flames and gas clouds. By monitoring these variables, fire teams can assess where a fire might spread and how to position firefighting resources effectively.
Monitoring Hazardous Gas Dispersal
Oil and gas facilities often emit various gases, some of which may be harmful or toxic when released into the atmosphere. In the event of a gas release, wind socks help operators track where the gas cloud might travel, allowing them to deploy protective measures and evacuate areas in the wind’s path. This real-time monitoring is essential in preventing harm to workers, nearby communities, and the environment.
How Wind Socks Work
Basic Design and Operation
A wind sock consists of a tapered, cylindrical fabric tube mounted on a pole, free to rotate with the wind. The wide end of the tube is open to allow air to enter, while the narrow end points in the direction of the wind’s flow. The concept behind a wind sock is simple—when the wind blows, it fills the fabric tube, causing it to extend in the direction of the wind.
The length and position of the wind sock also provide a rough indication of wind speed. When the wind is strong, the sock stands out straight; when it’s weak, the sock droops. The angle of the sock can help estimate wind speed, with fully extended wind socks indicating stronger winds.
Material Considerations
Wind socks are typically made from durable fabrics, often nylon or polyester, to withstand harsh environmental conditions. These materials are chosen for their durability, flexibility, and resistance to UV radiation, chemicals, and extreme weather. In oil and gas facilities, where exposure to corrosive substances is common, these materials are crucial to ensuring longevity and reliability.
Pole and Mounting System
The mounting system for wind socks includes a pole with a rotating mechanism, allowing the sock to pivot with the changing wind direction. The poles are often made of weather-resistant metals such as stainless steel or aluminum, ensuring they remain stable in high winds and corrosive environments.
In the oil and gas industry, the height of the wind sock’s pole is carefully chosen to ensure the sock is visible from a distance. In high-risk areas, wind socks may be illuminated or painted in bright colors to enhance visibility during low-light conditions.
Applications of Wind Socks in the Oil and Gas Industries
Offshore Drilling Platforms
Offshore platforms are constantly exposed to extreme weather conditions, making wind monitoring crucial for safe operations. Wind socks help personnel assess wind direction and speed, allowing for the safe handling of equipment and materials. They are also essential during helicopter landings and takeoffs, where wind conditions must be monitored for pilot safety.
Onshore Drilling Rigs
Onshore drilling sites are often located in remote areas where wind patterns can shift rapidly. Wind socks are installed to monitor wind conditions, which are crucial during activities such as venting gas or transporting flammable materials. During emergencies like gas blowouts, wind socks provide vital information to guide evacuation and emergency response efforts.
Refineries and Processing Plants
Refineries handle volatile chemicals, gases, and liquids, making wind monitoring a critical aspect of everyday safety protocols. Wind socks help operators monitor wind conditions during flaring (burning off excess gases), ensuring that the wind direction is favorable to prevent hazardous gases from being blown toward sensitive areas or neighboring communities.
Installation and Maintenance of Wind Socks in the Oil and Gas Industry
Installation Best Practices
When installing a wind sock in an oil and gas facility, several factors must be considered to maximize its effectiveness:
- Location: Wind socks should be installed in open areas free from obstructions, such as tall buildings or trees, which may alter wind patterns. In offshore platforms, they are often placed on elevated structures to ensure they catch the full force of the wind.
- Height: Wind socks are typically installed at heights where they are visible from all operational areas. On drilling rigs or platforms, they may be installed on towers or masts, while in refineries, they are mounted on poles strategically placed around the facility.
- Rotation Mechanism: The wind sock must rotate freely with the wind to ensure accurate readings. Therefore, the rotating mechanism should be well-maintained and free from obstructions.
- Visibility Enhancements: To enhance visibility, wind socks may be painted in bright colors or equipped with lighting systems, especially in facilities that operate 24/7 or in areas where weather conditions frequently reduce visibility.
Maintenance Considerations
Wind socks in the oil and gas industries are subjected to harsh environmental conditions, including extreme temperatures, UV exposure, chemical exposure, and high winds. To ensure that the wind sock continues to function correctly, regular maintenance is necessary. This includes:
- Inspecting the Fabric: Wind socks should be regularly checked for signs of wear and tear. UV rays, chemicals, and wind can cause the fabric to degrade over time, reducing its accuracy in indicating wind speed and direction. Replacing the sock when it becomes damaged is essential for continued safety.
- Lubricating the Rotation Mechanism: The rotating mechanism that allows the wind sock to move with the wind should be inspected and lubricated regularly to prevent rust and ensure smooth operation.
- Cleaning: Wind socks may accumulate dust, debris, and chemical residues over time. Regular cleaning, especially in industrial environments, can prolong the lifespan of the wind sock and improve its visibility.
Standards and Regulations Governing Wind Socks in the Oil and Gas Industry
International and National Standards
Several international and national standards govern the use of wind socks, ensuring that they meet the necessary safety requirements for use in high-risk industries like oil and gas.
- ISO Standards: The International Organization for Standardization (ISO) provides guidelines for the design, installation, and maintenance of wind indicators, including wind socks, to ensure they are fit for use in hazardous environments.
- OSHA Guidelines: In the United States, the Occupational Safety and Health Administration (OSHA) outlines safety protocols for the use of wind socks in hazardous industries. OSHA’s guidelines focus on ensuring that wind socks are visible, well-maintained, and used in conjunction with other safety equipment, such as gas detectors and emergency shutoff systems.
- Industry-Specific Regulations: In the oil and gas industry, companies may have their own internal safety standards that dictate the use of wind socks. These standards are often more stringent than national or international regulations, reflecting the specific risks associated with working in the industry.
Compliance with Environmental Regulations
In addition to safety regulations, the oil and gas industry must comply with environmental regulations governing emissions and pollution control. Wind socks play a role in these efforts by helping operators monitor wind conditions and mitigate the spread of harmful gases or chemicals into the atmosphere.
Challenges and Limitations of Wind Socks in the Oil and Gas Industries
While wind socks are indispensable in many situations, they do have certain limitations:
Limited Precision
Wind socks provide a rough estimate of wind speed and direction, but they lack the precision of more advanced instruments, such as anemometers or wind vanes. In highly controlled environments, wind socks may be supplemented with more sophisticated tools for accurate measurements.
Wear and Tear in Harsh Conditions
In the oil and gas industry, wind socks are subjected to constant exposure to the elements. Harsh weather conditions, chemicals, and UV radiation can degrade the materials, requiring frequent replacements and maintenance. While wind socks are a low-cost solution, the long-term cost of maintenance can add up in extreme environments.
Visibility Issues
Wind socks rely on visibility, meaning they may be less effective during nighttime operations or in low-visibility conditions, such as fog, heavy rain, or snow. This limitation is typically mitigated by adding lighting systems or using highly visible colors, but these enhancements may not always be foolproof in severe conditions.