Bolted joints are one of the most common elements in piping design. Whenever flanged joints are used, bolted connections play an important role in keeping flanges together and avoiding flange leakage problems. So Bolting is an important component of piping systems.
In general, Boltings seem petty things for a whole lot of piping system design. Therefore, they tend to be “forgotten” when it comes to detailing their features, especially the length.
It is true that with nowadays technology of 3D modeling, it will be automatically calculated. However, this is only applicable when it is a normal joint consisting of Flange-Gasket-Flange. In some other cases, Piping Engineers need to put more attention to details and define the length manually.
It would be one of the “failures” if these lengths cannot be rectified upfront and only discovered when installation comes in hand. Imagine if you are doing a big-scale project, it will definitely delay the progress. And unfortunately, just because of these “petty” things.
Let’s see what are the bolting design features that Piping Engineers required to define and check in order to have technically complied boltings.
Bolting Features to be Checked in Bolted Connection
While deciding on a bolted joint or bolted connection the following bolting design features must be thoroughly checked to ensure a leak-free long-lasting piping system.
- Service – Defining Bolts Material
- Size & Quantity
- Washer Requirement
- Inline Items
- Length
- Coating – Common practice
Fluid Service to Define Bolt Materials
Like any other piping items, the bolt material will be based on the service that they will be used for. This will be defined when Piping Engineers are preparing their Piping Material Specifications. No ratings are required for boltings as they are not pressure-containing parts.
Other than the OWNER’s specification and requirement, another reference that can be taken into account is API 6A. Below attached is an example and guideline on boltings material to be used based on its service;
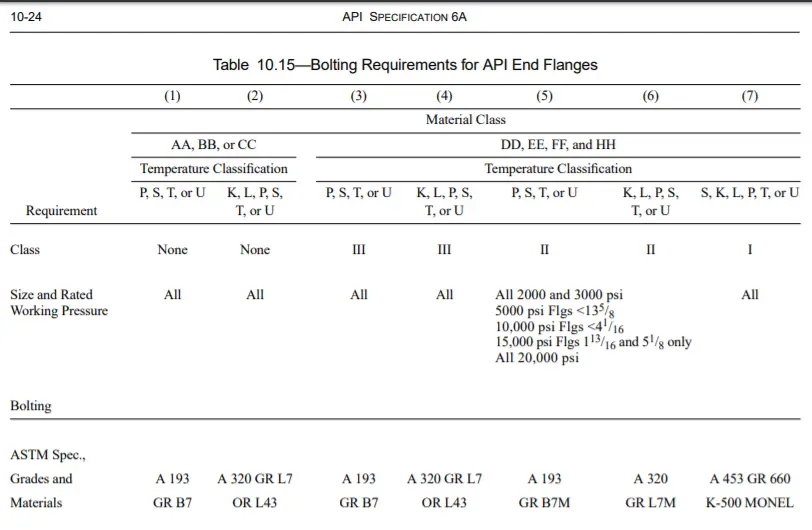
ASME B16.5 also showed materials for boltings as below;
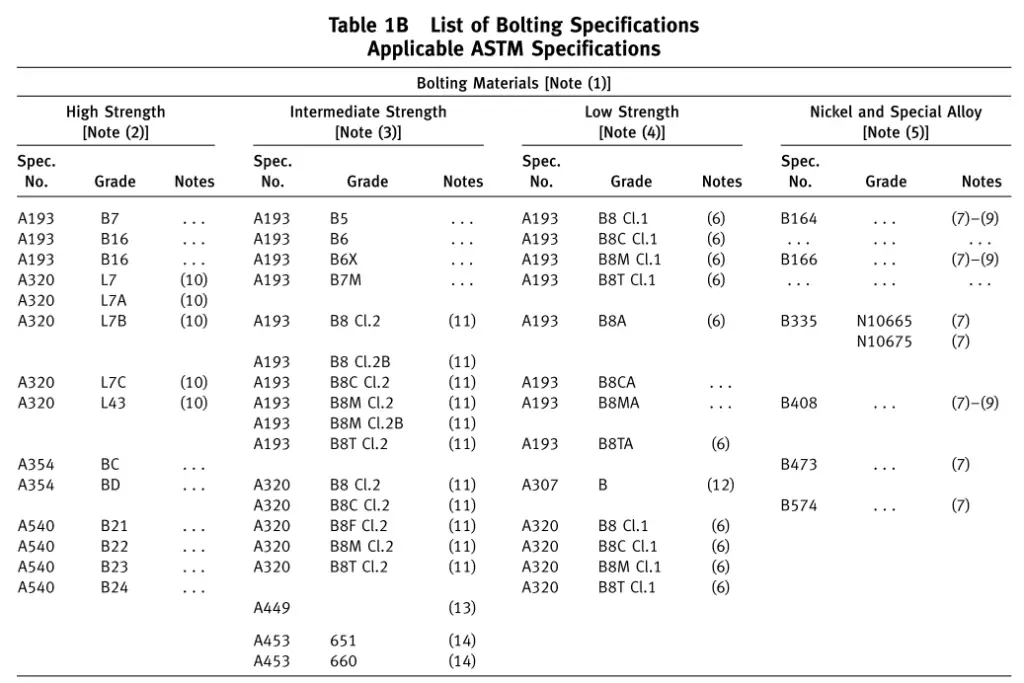
Size and Quantity of Bolts
The size of the boltings will relate to the size of the flange, and quantity will relate to the flange rating. Flange with sizes from 1/2″ up to 24″ will refer to ASME B16.5 and ASME B16.47 for larger sizes. From the table, the size, quantity, and standard length (normal joint of Flange-Gasket-Flange) will be provided.
The length would largely depend on the Flange class rating as the thickness of the flange differs when the rating increase. Examples of Class 150 and Class 300 are shown in Fig. 3 and Fig. 4 below;
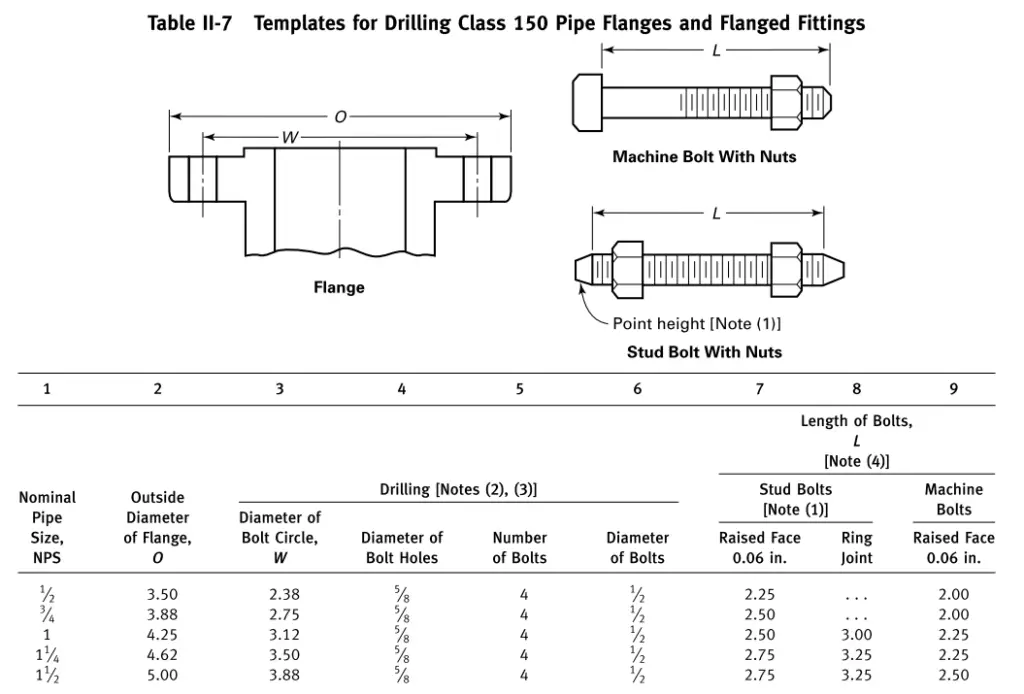
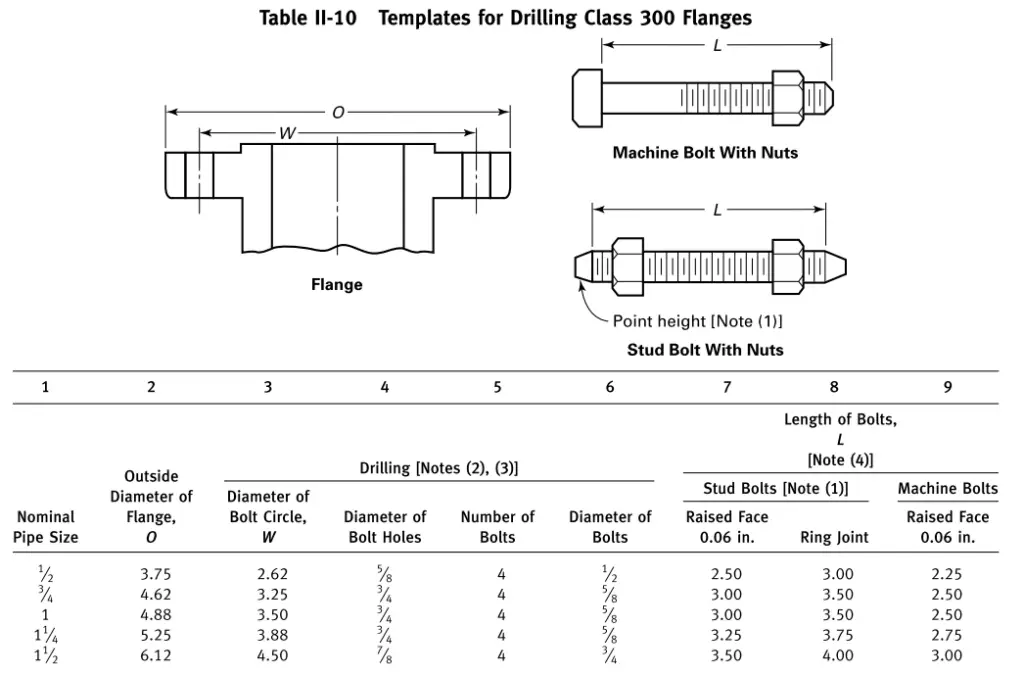
This length has been calculated with all considerations as in Nonmandatory Appendix C. We will cover this calculation again.
Washer Requirement for Bolted Connections
A common practice the boltings do not require a washer. Thus, when will washers be required? Washers in bolted joints are used:
- When used with an insulation gasket kit. This is to provide an engagement grip to the non-metal washers.
- When the non-metal flange is used to avoid flange damage due to the force exerted.
- Special case if the bolt holes are bigger and may cause loose boltings.
Type of Washers
ASME B18.21.1 provides the following types of washers:
- Plain (Flat) Washers
- Helical Spring Washers
- Tooth Lock (Internal, External) Washers
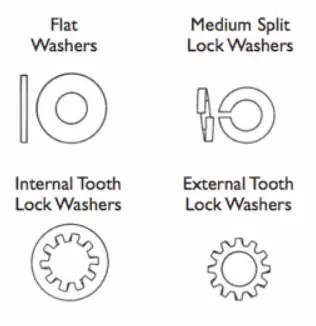
Bolting considerations for Inline Items
Normal flange joints will consist of Flange-Gasket-Flange, and usually by 3D modeling setup; this has been auto-calculated to define the length of the bolt. However, whenever inline items involved Vendor data incorporation, it is wise to check manually and implement it inside the 3D setup. Actual thickness to be incorporated to avoid the insufficient length of the bolt.
Examples of inline items that require Final Vendor Data to be incorporated;
- Valves (manual & control valves) – sometimes its end-to-end dimension as per Manufacturer’s Standard.
- Gaskets – especially insulation gaskets, the thickness may exceed the standard 3 mm that the usual 3D system would assign for spiral wound gasket (after compressed). Extra care for a joint that consists of multiple gaskets joint.
- Spade, Spacer, Spectacle Blind
- Instrument Items – other than Control Valves, all instrument items that are connected to piping shall be checked. Sometimes it came with non-standard flange thickness or upper-Class rating that requires an extra length of bolts.
Bolt Length Calculation and Considerations
Appendix C of ASME B16.5 provides an example of how the bolt length has to be calculated and what considerations need to be taken;
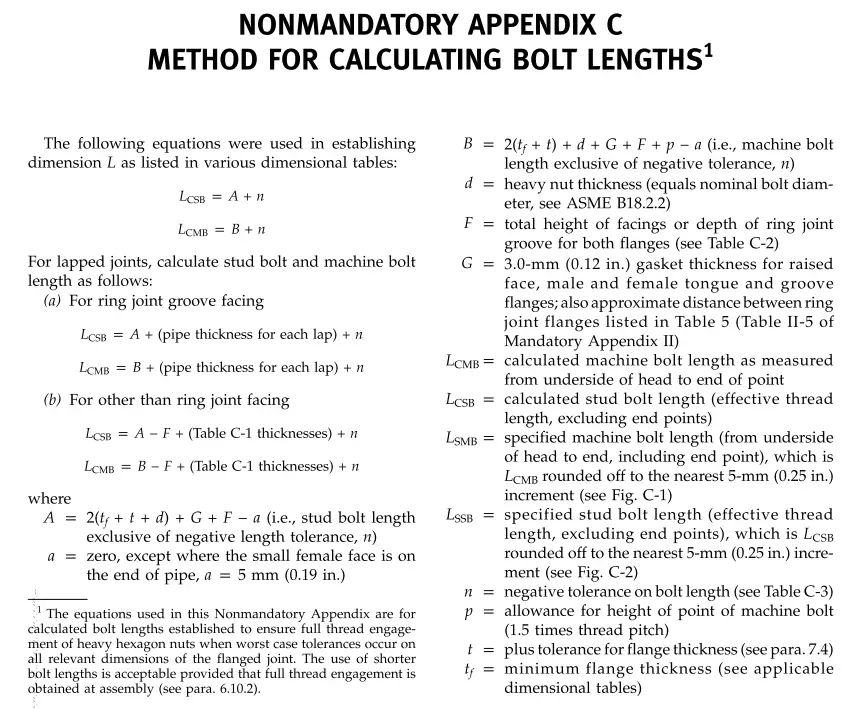
For the size of bolts more than 1″, the bolt tensioning requirements shall also be considered. For this, add another 1D or 1 thickness of nut for the total length.
The following Bolt tensioning video tutorial explains clearly the requirement of the above-mentioned 1D or 1 thickness of the nut.
Bolt Coatings on Bolted Connections
Coatings on bolts can be said quite common nowadays. Even some OWNER would specify ALL bolts shall be coated. As stated before, even though bolts are seemed petty, non-pressure-containing parts; bolts will be sitting in the weather dry and wet maintaining the force of tightening for the pressure-containing parts. To ensure the strength are efficient, corrosion is one of the major things to be avoided.
The most popular coating that is used is Fluorocarbon Coating (Xylan, PTFE, Teflon).
But, there were other types of coatings such as;
- Galvanized (Hot Dip, Mechanical)
- Electroplating (Cadmium, Zinc)
It is important to ensure the requirement of the project on the bolt coating. Some projects may be delayed just because this one little thing (but important) has been missed out of consideration.
Few more related articles for your consideration.
Guide for Coating Selection for External Bolting to Reduce Corrosion
How to Select a Bolt: A definite Guide
Difference between ASME B 16.47 Series A and Series B Flanges
Collar Bolts To Maintain Removable Bundles in Heat Exchangers
Methods for Checking Flange Leakage
Useful article
Wow! Nice and good article, I’m looking forward to your next posts.
Thanks!
Thanks a lot