What is a Collar Bolt?
Collar bolts are a type of fastener that is extensively used to hold the bundle in the exact place for removable bundle heat exchangers. This ensures the channel removal without interrupting or breaking the seal between the shell and tube sheet. Figure 0 shows a typical schematic diagram of a collar bolt assembly.

Collar Bolts in Standards
TEMA Standard
The new part (RCB-11.8) was added in the tenth edition of the TEMA (Tubular Exchanger Manufacturer Association) standard, covering the recommendations of the collar bolts in the removable bundles with B-Type bonnet as shown in Figure-1.
Collar stud shall be used on units with removable tube bundles only when specified by the purchaser. Normally, It is recommended for B-Type of bonnets. The Outer Diameter (OD) of the static tube sheet should match the mating flange OD, and shall be through-bolted. It is preferable to have every fourth stud in the bolt circle (with a minimum of 4) as collar type I for type II as shown in Figure 2 below.

Collar bolts are only used to maintain the gasket integrity and position when the channel is removed and torqued prior to pressurizing.
As an alternative to collar studs, every fourth bolt hole in the tube sheet may be drilled and tapped to the size of the stud bolt. The studs in the threaded holes shall be double nutted on the shell side or provided with machined flats to allow the tube side nut without rotating the stud.
API 660 Standard
In API 660, Para 7.5.2.4: A full-diameter stationary tube sheet shall be provided for removable tube bundle exchangers with bonnets (Figure 2). The tube sheet shall be provided with collar studs or tapped tube sheet holes for a minimum of 25 % of the bolts (4 minimum). Hydrostatic testing of the shell side shall be allowed with the bonnet removed and all bolting installed in place.
When collar bolts/drilled-and-tapped holes are used, at least four shall be provided and the location of them shall be identified on the drawings and by stamped markings on the external diameter of the tube sheet.
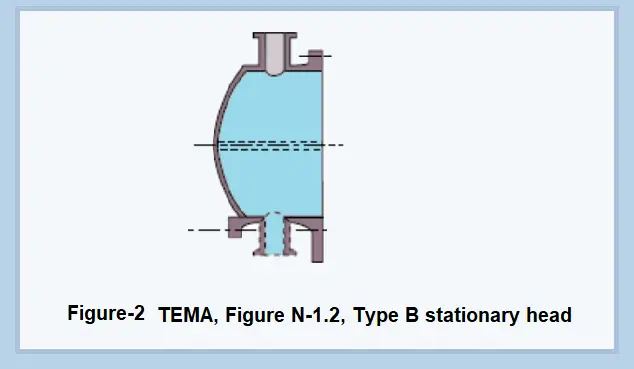
PIP VEV1100M
As per PIP VEFV1100M Vessel/Shell &Tube Heat Exchanger Standard Details, the standard arrangement and configuration for collar bolt dimensions are produced in Figure 3 below.
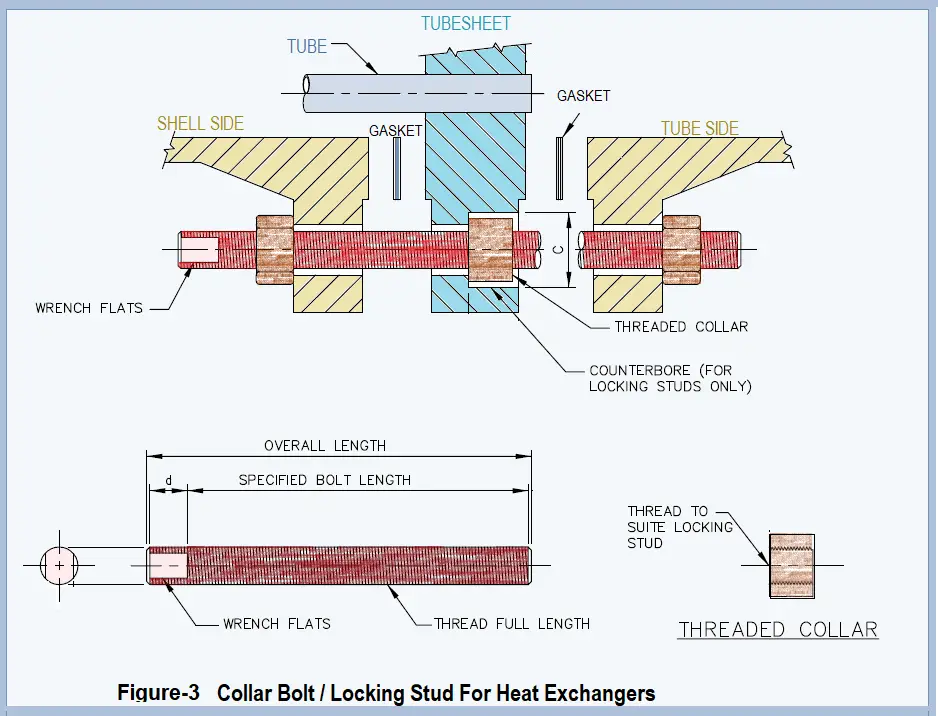
HEI
Surface condensers are designed to the requirements of HEI (Heat Exchange Institute) per the typical configuration shown in Figure 4. Here, both tube sheets are fixed. Also, without the removal of one of the tube sheets, the gasket between the tube sheet and shell flanges cannot be attended to.
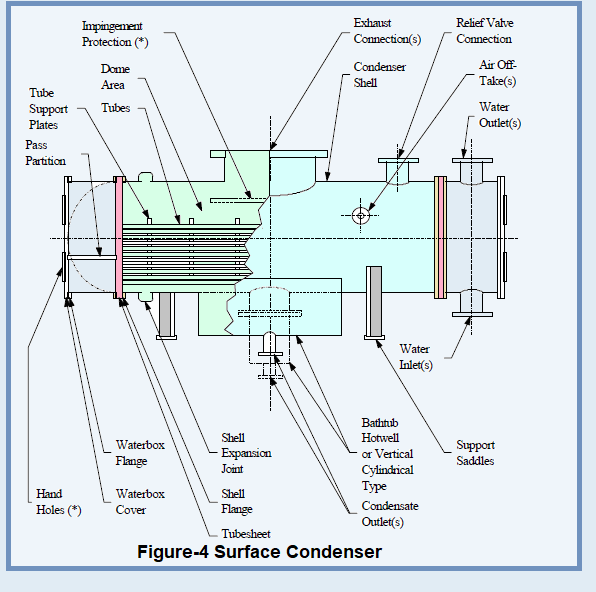
Surface Condenser without Collar Bolts
A manual of one of the most famous and reputable surface condensers manufacturers in the world alerts the following:
“It is important not to break this seal between the tube sheet and the shell flange. The tubes are expanded into each tube sheet holding them firmly in place, and the shell seal cannot be replaced without retubing the entire condenser. To prevent breaking the joint, it is important that all nuts be removed from the water box flange side and not from the shell flange side. Do not loosen or remove the stake studs and double nuts on the shell side.”
Finding a leak in the shell side causes a huge impact on the plant as it breaks the vacuum. In such a configuration, the collar bolts must be used.
Despite the illustrated advantages of the use of the collar bolts, there is a debate about the disadvantages as it might be a cause for trouble instead of enhancing the exchanger’s maintainability. In the following section, the main advantages and disadvantages of the use of collar bolts are summarized.
Advantages of the use of collar bolts
The main objective and advantage of the collar bolts is better maintainability considering that each time the channel is removed, the bundle shall be removed for replacing the gasket between the tube sheet and shell to avoid leakage after pressurizing the exchanger. Bundle gasket replacement is time-consuming and increases MTTR (Mean Time To Repair/Restore).
Disadvantages of the use of the collar bolts
- Some field experience showed that it is nonmandatory to remove the bundle if the channel is removed. This opinion is built on some special experience in using cam profile gaskets and the application of initial proper stress to reach the desired gasket stress.
- In case of using tapped holes and the bolts get stuck and the attendance for the holes machining and replacement of the bolts would be time-consuming and might be beyond the readiness of the maintenance crew for the task.
- Marking or stamping of the collar bolts has to be adequate to avoid misleading the maintenance crew otherwise, they may remove collar bolts by mistake.
- Relative higher cost due to the bigger tube sheet size and the aching required for the bolt holes in the tube sheet.
Few more resources for you..
Shell & Tube Heat Exchanger Piping: A brief Presentation
An article on Plate Heat Exchanger with Steam
A typical Check List for Reviewing of Shell & Tube Heat Exchanger Drawings
Basics of Shell and Tube Heat Exchangers: A brief presentation
A brief presentation on Air Cooled Heat Exchangers
Basic Considerations for Equipment and Piping Layout of Air Cooled Heat Exchanger Piping
References
- [1] API Std 660 – Shell-and-Tube Heat Exchangers
- [2] TEMA Tenth Edition, 2019 (Standards Of The Tubular Exchanger Manufacturers Association)
- [3] PIP VEFV1100M Vessel/S&T Heat Exchanger Standard Details
- [4] Explore The World Of Piping – EWP https://www.wermac.org/equipment/collarbolt.html)
Dear Sir or Madam:
We are looking for 122 WASHERS HARDENED FOR TUBESHEET COLLAR BOLTS DIAMETER
1-7/8″
Many thanks,
German Spicker, Ph.D.
Fis SAS
Hello, thank you very much for your educational content. I have a question, please help me.
What is the mockup welds test acceptance criteria for tube-to-tubesheet welds according to paragraph QW-193.1.3 Macro-Examination?
I mean, if two or three of the 40 macro tests are failed in the macro test, the entire Mockup test will be declared failed?
Thank you for your help and guidance
M. Taghavi