Bolts and Nuts are fasteners for joining two parts. Even though bolted joints are not permanently similar to welded joints, still they are used in industries to a large extent wherever there is a need for separation of the parts. Process, Power, and Steel Industries can not be thought of without Nuts and Bolts. But one of the major problems with Bolted joints is external corrosion due to the working environment.
How to Protect Bolts from Corrosion
Corrosion of nuts and bolts is a major concern for industries. One of the major causes of bolt failure and loose bolt is Extreme Corrosion. The use of Corrosion Resistant material is one option to prevent bolting corrosion but that translates into huge costs. So this is normally not suggested for Carbon or alloy steel piping. Use of bolt cap is another option that can be used for bolt sizes between 1/2 inch to 6 inches. But the most cost-effective way to increase bolt life from corrosion is by using corrosion-resistant coatings. In this article, I will highlight some important points for coating selection.
Types of Bolt Coatings
Various coating methods (Fig. 1) are used in industries. However, the most frequently used methods along with governing coating standards are listed below:
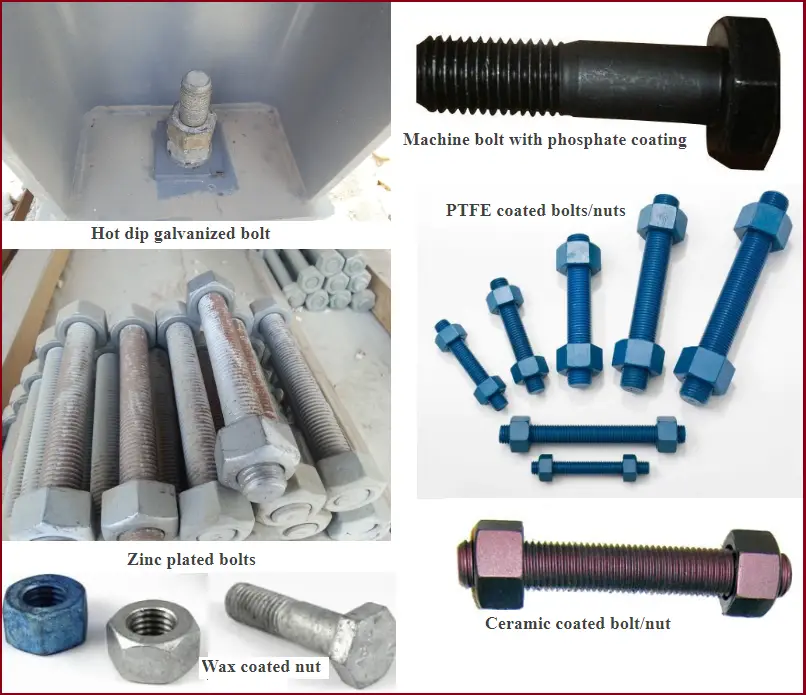
- Hot Dip Galvanized: ASTM A 153/ ASTM F 2329/ ISO 10684
- Zinc Plating: ASTM B633/ ISO 2081
- Zinc‐Aluminum: ASTM F 1136/ EN ISO 10683/ EN 13858
- Zinc‐Nickel: ASTM B 841/ ISO 15726
- Cadmium: ASTM B 766/ ISO 2082
- Phosphate: ASTM F1137/ ISO 9717
- Aluminum particle Filled (Ceramic): ASTM F 1428
- PTFE: Normally Manufacturer Standard
Coating Material Selection Chart
Refer to Fig. 2 below. The image provides a quick guide for selecting coatings based on their application and operating temperature range. Refer to the General Notes and Special Notes mentioned at the bottom of the image while selecting the coating materials.
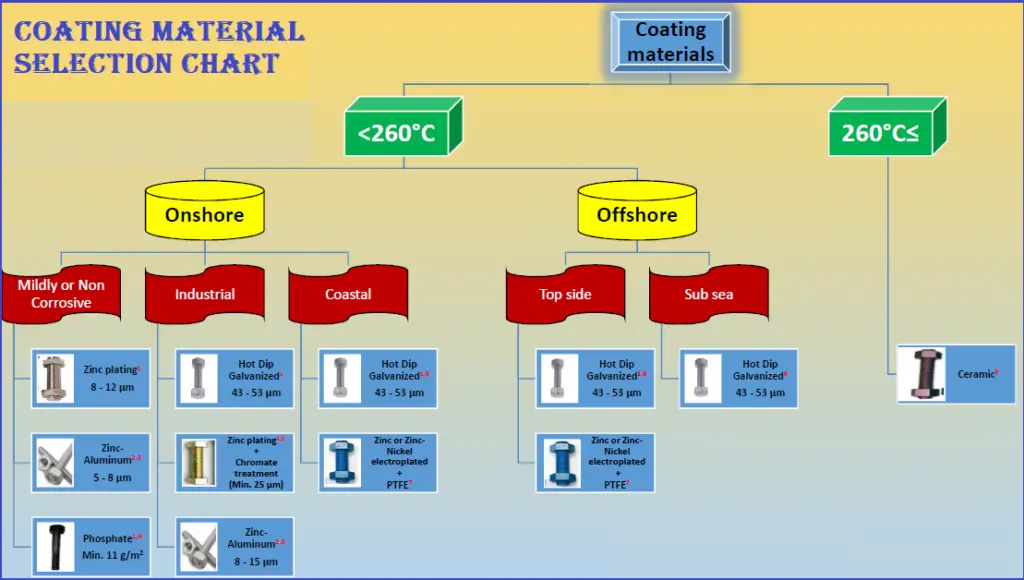
General Notes for Coating Selection Chart
- This chart is just a recommendation, other coatings may be used based on successful experience.
- These coatings are normally applicable to carbon or low alloy steel bolting. CRA bolting is not included in the chart.
- In the selection of coatings, their cost has been also considered.
- Hydrogen embrittlement may occur on fasteners caused by hydrogen, introduced from chemical cleaning, pickling, or coating process e.g. electrolytic plating and Hot Dip Galvanized. Such coatings may need pretreatment/post-treatment.
- Fasteners should be avoided in splash zone applications. However, when this is unavoidable, fasteners shall be made of seawater-resistant material, e.g. alloy 625/725 or similar.
- Cadmium coating is still being used; however, due to the hazardous nature of the plating
process and exposure to the environment, it is being phased out. - Wax-based systems may be used as maintenance systems.
- For Hot Dip Galvanized coating, the Dip spin procedure should be applied.
Special Notes for Coating Selection Chart
Refer to the Numbers mentioned in Fig. 2.
- Zinc-plated, Hot-dip Galvanized, and phosphate coatings should not be used at continuous temperatures above 200˚C.
- Zinc/Aluminum coating is normally known under registered trademarks such as DACROMET, GEOMET, etc.
- Zinc/Aluminum coating may be used up to 300˚C by manufacturer approval.
- Phosphate coatings are normally used as a pretreatment to other coatings but may be used in noncorrosive or mildly corrosive areas especially when a sealer is used.
- Zinc plating + chromate treatment may be used in the coastal area for short-term applications (less than 10 years) or for long-term applications when they are painted.
- Hot Dip galvanized coating may be painted to the extent of its life in marine atmospheres.
- Most PTFE coating can be used up to 230˚C, but they may be used up to 260˚C by manufacturer approval.
- For subsea applications, the coating of low alloy bolting materials protected by CP is unnecessary. However, thin metal (hot spun galvanized or zinc‐nickel electroplate) is often specified to preserve the bolt surface prior to or during installation.
- Ceramic coating for marine applications shall be top-coated. The average coating thickness shall be 20‐30 μm. The base coat can be aluminum particles dispersed in a liquid binder of chromate /phosphate compounds. The top coat can be ceramic oxide pigments dispersed in a liquid binder of chromate/phosphate compounds.
Few more Resources for you..
FORMS OF CORROSION: An article
How to Select a Bolt: A definite Guide
Corrosion under insulation: A Presentation
PROCEDURE FOR FLANGE-BOLT TIGHTENING OF VARIOUS SIZES OF FLANGES
Corrosion Protection for Offshore Pipelines
Collar Bolts To Maintain Removable Bundles in Heat Exchangers
Corrosion Monitoring Techniques & Surveys: A short Presentation
Flange Insulating Gasket Kits for Industrial Application