What is Flange Insulation Gasket Kit?
The most common problematic area for a Piping/Pipeline System design is flanges. So we have to be doubly sure to seal it properly to prevent flange leakage. At the same time, It must also be insulated cathodically so that stray currents which are known behind the undue corrosion and eventual metallic breakdown be prevented. Insulating gasket sets or Flange insulation kits play an important role in such cases.
- They are designed for electrically insulating the flanges.
- They act as an insulator between dissimilar metallic flanges.
- Also, they are used to isolate sections of pipework (dissimilar metals) electrically in the cathodic protection systems; thus preventing the electrostatic charge flow along the pipelines as they remove the possibility of galvanic cell system creation.
Major Applications of Insulating Gasket Kit
Insulating gasket kits can be used in all such places where galvanic corrosion protection and electrical insulation are needed. Common Application areas are piping/pipeline systems with seawater environments, offshore installations, chemical installations, oil refinery pipelines, etc.
Components of Flange Insulation Gasket Kit
Each flange insulation Kit (Refer to Fig. 1) constitutes of
- one central flat or oval section gasket,
- one insulation sleeve per bolt and
- two insulating steel washers per bolt and
- two plated steel washers per bolt.
All these components are produced using special materials possessing chemical stability, dielectric properties, and low water absorption so that the purpose is solved. The full sets are packed individually and labeled clearly mentioning the flange size, rating, type, and material combination. Insulation kits are generally available upto 24 inches, but custom-made higher nominal sizes can be produced on the requirement.
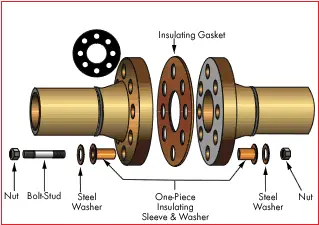
Assembling of the flange insulation gasket kit components
The polyethylene insulating sleeve and the mounting stud are the main components of the insulating gasket kit. Contrary to the conventional nut and bolt system of flanged joints, the insulation kit uses a stud with a washer and nut on each end of the flange joint. The insulating sleeve is then inserted into the bolt holes using one insulator on each side of the flange. So, Two insulators per bolt hole are inserted into the flange. Then the mounting stud is inserted into the insulating sleeves until threads on each end of the stud are visible outside of the flange. A flat steel washer is slid onto the stud at each end, and a nut is threaded onto each end of the stud and tightened.
As a nut is tightened on each end of the stud, the flange insulation kit becomes much stronger than the typical nut-and-bolt type connection. In the traditional manner of nut-bolt tightening, all of the clamping force is applied to the single set of threads on the bolt while in the case of a double-ended stud such as in a flange insulation kit, the clamping force is divided equally between the threads on each end of the stud as well as inside both nuts. The stud is protected and insulated from any electric charge and corrosion. This creates a flanged connection that will not corrode or fail due to a chemical reaction between two dissimilar metals.
Types of Flange Insulating Gaskets
Four major types of gasket isolation kits are available in the market those are designated as F, E, D, & O. Each type of flange kit fits flanges with a specific type of flange face (RF, FF, RTJ).
F Type Gasket
Type F type gaskets are produced to fit the raised face flanges. The inside diameter of the bolt-hole circle is made slightly smaller than the external diameter of the gasket which assures automatic positioning of the gasket. To avoid the accumulation of foreign materials, Special band protectors can be used for the joint assembly to strengthen the cathodic isolation further. These are manufactured from 1/8″ thick fabric-based phenolic sheets either without coating or a with a nitrile rubber coating on the two faces. Type F gaskets are also available in non-asbestos fibers with high isolation capacity.
E Type gasket
In full-face type, Type “E” Gaskets, the outside diameter of the gasket matches the external diameter of the flanges. So the gasket completely covers the whole flange surface. There are produced with precision-located bolt holes and are easy to position in the center. This design will prevent foreign material accumulation between the flange faces and thus enhances the isolation properties of the kit. Type E flange insulation kits are available in phenolic, neoprene-faced phenolic, and high-temperature materials.
D Type Gasket
Type “D” Gaskets are manufactured to fit into the ring groove of RTJ flanges (style R, RX, and BX). They are available in medium weave reinforced phenolic and other materials are sized to ANSI specifications available in a basic oval as well as an octagonal shape. This type of gasket is known as an “API ring joint”.
O Type gasket
Type O Gaskets are extra special as they feature an additional sealing element on both sides of the device, generally, PTFE, Nitrile, or Viton Rubber, and are available in both ring and full-face designs (type E and F).
Insulating gasket Material
- All materials should be selected to assure long-term effective sealing and electrical insulation of the flanged joints.
- To take advantage of the best characteristics, sometimes, gaskets are made with combinations of materials.
Normal Gasket materials are G3, G7, Nitrile-Face, Plain Phenolic, G10, Neoprene-faced Phenolic, Klinger, Teflon, Durlon, etc. Popular Sleeve materials are Phenolic, Mylar, Polyethylene, Minlon, or Nomex. Common washer materials are Phenolic, Steel, G7, G3, or G10 available as a single washer and sleeve kit, a one-piece washer kit, a double washer kit, or a one-piece double washer kit (Minlon)
Sleeves and Washers of Flange Insulation Gasket Kits
One-piece sleeves and washers
One-piece sleeves and washers are available molded from acetal resin. They should generally be used as single washer sets since they are molded to specific lengths and are in many instances longer than the thickness of a single flange. They are available for bolt diameters of ½” to 1-1/2″ (12.7 mm to 38.1 mm), and are limited to applications where the flange temperature does not exceed +180^oF (+80^oC).
A special feature is a washer centering ring that positions the steel washer on the unit properly to avoid uneven pressures on the washers.
Insulating Washers
Standard insulating washers are made of high-strength phenolic and provide tough, positive insulation at temperatures of +3000F ( +1500C). They are available for bolt sizes from ½” (12.7 mm) through 3 ½” (88.9 mm) and are made to fit over the insulating sleeves. Fiberglass reinforced high temperature phenolic insulating washers are available on special order in the same sizes as the standard insulating washers
Insulating Sleeves
Insulating sleeves are available in Mylar, polyethylene, phenolic, and Nomex. They are through 3-1/2″ (88.9 mm) and are designed to fit easily over the flange bolts, and may be used with standard-sized bolts and bolt holes even with some misalignment. Insulating sleeves are used with separate insulating washers and have a standard wall thickness of 1/32″ (0.79 mm). They are available for standard American bolt sizes from ½” (12.7 mm) to 3 ½” (88.9 mm), as well as metric bolt sizes from 12 mm and larger.
Steel Washers
Steel washers are designed to fit over the insulating sleeve or retainer ring on the one-piece sleeves and washers. The outside diameter is sized to fit within the bolt facing on ANSI standard flanges. They are of 1/8″ (3.2 mm) thick plated hot-rolled steel. Pyrox insulating sleeves and washers are also available.
Flange Insulation Gasket Kit Installation procedure
The Gasket ID (inside diameter) is normally made slightly smaller than the flange ID. While installing ensure that the gasket is properly centered over the bore. It will prevent the build-up of foreign material between the flange faces during pigging.
Single washer insulating sets are recommended for underground flanges. This should be installed on the unprotected side of the flange, which will provide cathodic protection for the studs as well as the nuts. For above-ground flanges, It is suggested to use Double washers for ease in testing.
The use of alignment pins is always suggested which will ensure proper alignment of flanges and gaskets. The size of each Pin shall be a minimum of 3/32″ (2.38 mm) larger than the bolt.
A diagram showing a recommended bolt tightening sequence is normally supplied with each insulating gasket set.
Common Vendors for Insulating Gasket Kits
Common vendors who manufacture and supply insulating gaskets are
- PSI
- Pikotek
- Central Plastics
- Garlock
- Trojan
- Lemons
- Advanced Products and Systems
Information needed for Ordering Flange Insulating Kits
To order an insulating gasket kit, the following information needs to be provided:
- Flange Specification (ANSI/ASME, DIN, API, MSS SP44, BSI, AWWA Standard)
- Nominal Pipe Size, Pressure Rating, and Bore Size
- Operating Pressure, Temperature, and Media
- Gasket type (D/E/F/O)
- Required Seal Material
- Isolating Sleeve Material
- Isolating Washer Material
- Metal Washer Material
- Quantity
Few more Resources for you…
Methods for Checking Flange Leakage
Guidelines on selection of various types of Flanges
Few points on Gaskets for leak Proof Flanged joints
PROCEDURE FOR FLANGE-BOLT TIGHTENING OF VARIOUS SIZES OF FLANGES
Functions of Gaskets for leak-proof Flanged joints
Hi There, I like the idea here to reduce/eliminate galvanic corrosion.
I’m doing a steam pipe project where my black pipe/steam pipe will contact a stainless steel fitting. Any ideas/recommendations?
Thanks, Ed
Hi Anup, thanks for sharing the knowledge, is there any standard about the design and manufacture of insulation kits? Thanks.
Hi Anup.
I work on aviation fuel systems where we have installed a number of insulating gaskets (Type F) in situations where we have dissimilar metals, thereby preventing galvanic corrosion. My belief is that all flanges on petroleum installations have to be bonded and therein lies my concern.
What I’m trying to understand is how bonding between flanges to ensure electrical continuity can be applied in harmony with an insulating gasket without defeating the protection that the gasket kits are designed to provide. Essentially, if we apply an electrical bond between the two flange faces directly beneath the two opposing insulating washers on any single bolt, then I see this as a pathway across which galvanic corrosion could occur thereby rendering the insulating kit redundant. If however we fit the bond between the insulating washers and the steel plated washers, then the bond becomes insulated from the two opposing flange faces and therefore isolated, running the risk of having different potentials on the two sides of the flanged joint.
Do you have any thoughts on this please?
Regards.
Wayne.
ELECTRIC ISOLATING KIT
– ELECTRIC ISOLATING KIT FOR RTJ FLANGE R37 (INCLUDING SLEEVE FOR BOLTS, WASHER, GASKET R37) SUITABLE FOR FLANGE SIZE 4-1/16″ API 6A 3000 PSI
– QTY: 10
It is not essential all the areas, where critical equipment’s or instrument to connected.i.e where we canot replace the spool or instrument or any costly.
reasons
1) tightening is always not possible incase of insulating kits.
2) when spiral wound gasket with ss inner/ss-outer ring or ss-inner/cas-outer ring both cases
al ready one end ss another end cs,in the middle we are using ss-inner ring gasket.
no need insulation kits,only bolts to be changed different materials.
3) practical problems of leakages can be avoided.kits will give chances of leakage and replacement cost.