Galvanizing pipes is a fundamental process in the metalworking industry that significantly enhances the durability and lifespan of steel and iron components. Galvanizing a pipe refers to the process of coating the pipe with a layer of zinc to protect it from corrosion and rust. This protective zinc layer significantly enhances the pipe’s durability and longevity by preventing the steel or iron from directly coming into contact with moisture and other corrosive elements in the environment.
What is a Galvanizing Pipe?
The galvanizing pipe is the process of applying a protective zinc coating to steel or iron. The primary purpose is to prevent rust and corrosion, thereby enhancing the material’s durability. Zinc serves as a sacrificial anode; when exposed to moisture and corrosive elements, it corrodes preferentially, thus protecting the underlying steel.
The composition of zinc coatings is crucial for performance. The main phases include:
- Zinc: Provides the primary protective layer.
- Zinc-Iron Alloys: Formed during the galvanizing process, these alloys enhance adhesion and corrosion resistance.
Applications of Galvanized Pipes
Galvanized pipes are widely used in various applications. Some of the typical uses are
- Plumbing: Galvanized pipes are commonly used in plumbing systems for water supply lines due to their resistance to rust and corrosion.
- Construction: These pipes are used in various structural applications, including scaffolding, fencing, and handrails.
- Agriculture: Galvanized pipes are used in irrigation systems and for constructing animal enclosures due to their durability in outdoor environments.
- Industrial: They are used in industries where pipes are exposed to harsh conditions, such as chemical plants and oil refineries.
- Automotive: Exhaust systems and structural components.
What are the advantages of Galvanized Pipes?
Galvanized pipes offer several advantages due to their protective zinc coating, which shields the underlying steel or iron from corrosion. Here are the key benefits of using galvanized pipes:
1. Corrosion Resistance
- Protective Barrier: The zinc coating acts as a physical barrier, preventing moisture and oxygen from reaching the steel or iron beneath, thus reducing the risk of rust and corrosion.
- Sacrificial Protection: Zinc corrodes more readily than steel. This sacrificial anode effect ensures that even if the zinc layer is damaged, the zinc will corrode first, protecting the steel from rust.
2. Longevity and Durability
- Extended Lifespan: Galvanized pipes have a much longer service life compared to non-galvanized pipes, often lasting several decades depending on the environment.
- Enhanced Strength: The metallurgical bond formed during the galvanization process adds a layer of strength to the pipes.
3. Low Maintenance
- Reduced Need for Repairs: The corrosion-resistant properties of galvanized pipes mean they require less frequent maintenance and repairs, leading to lower long-term maintenance costs.
- Minimal Surface Treatment: Unlike other types of pipes that may need regular painting or coating to prevent rust, galvanized pipes generally do not need such treatments.
4. Cost-Effectiveness
- Lower Long-Term Costs: While the initial cost of galvanized pipes may be higher, the extended lifespan and reduced maintenance needs make them a cost-effective option over time.
- Economic Installation: Galvanized pipes are easier to install and handle compared to other corrosion-resistant materials, leading to lower labor costs.
5. Versatility
- Wide Range of Applications: Galvanized pipes can be used in various applications, including plumbing, construction, agriculture, and industrial systems.
- Suitable for Harsh Environments: They are ideal for use in environments exposed to moisture, chemicals, and other corrosive elements.
6. Quick and Efficient Process
- Hot-Dip Galvanizing: This process is relatively quick and can coat complex shapes and sizes efficiently, ensuring uniform protection across the entire surface of the pipe.
- Immediate Use: Once galvanized, pipes are ready for use without the need for additional surface preparation or coating.
7. Environmental Benefits
- Recyclability: Both zinc and steel are recyclable materials, making galvanized pipes an environmentally friendly choice.
- Sustainable Protection: By extending the lifespan of steel pipes and reducing the need for replacements, galvanization helps conserve resources and reduce waste.
8. Aesthetic Appeal
- Uniform Appearance: The galvanization process provides a smooth, uniform finish that is often more aesthetically pleasing compared to other protective coatings.
- Long-Lasting Finish: The appearance of galvanized pipes remains consistent over time, even in outdoor or harsh environments.
What are the Methods of Producing Galvanizing Pipes?
Producing galvanized pipes involves coating steel or iron pipes with a layer of zinc to protect them from corrosion. There are several methods to achieve this, each with its own specific advantages and applications. The primary methods of producing galvanized pipes include:
Hot-Dip Galvanizing Pipes:
Hot-dip galvanizing is the most common and widely used method for galvanizing pipes. The Process of Hot-Dip Galvanizing consists of:
- Surface Preparation: The steel pipes are cleaned through a series of processes, including degreasing, pickling (acid cleaning to remove rust and scale), and fluxing (applying a flux solution to prevent oxidation).
- Galvanizing: The cleaned pipes are immersed in a bath of molten zinc, typically at a temperature of around 450°C (842°F).
- Cooling and Inspection: After immersion, the pipes are withdrawn from the zinc bath, cooled in a quenching tank, and then inspected for coating thickness and quality.
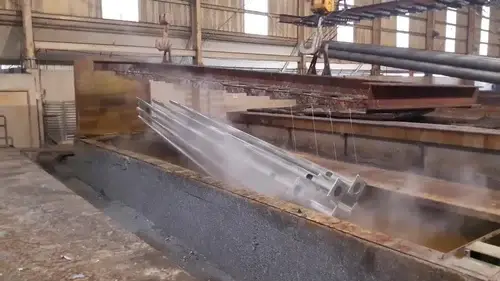
Advantages of Hot-Dip Galvanizing process are
- Thick, Durable Coating: Provides a robust and uniform zinc coating.
- Long-Term Protection: Offers excellent corrosion resistance and longevity.
- Adherence: Forms a metallurgical bond between zinc and steel, enhancing adhesion and durability.
Electro-Galvanizing (Electroplating):
Electro-galvanizing involves the application of zinc through an electrochemical process. It consists of
- Surface Preparation: Similar to hot-dip galvanizing, the steel pipes are cleaned to remove impurities.
- Electroplating: The pipes are submerged in an electrolyte solution containing zinc ions. An electric current is passed through the solution, causing zinc to be deposited onto the surface of the steel pipes.
- Post-Treatment: The coated pipes may undergo additional treatments, such as passivation, to enhance corrosion resistance.
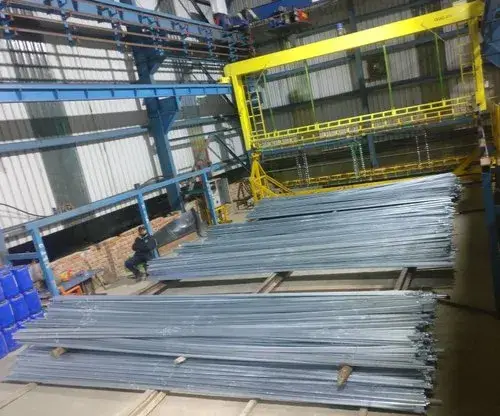
The major Advantages of Electro-Galvanizing are:
- Smooth Finish: Produces a smooth, aesthetically pleasing finish.
- Precision: Allows for precise control of the coating thickness.
- Low Temperature: The process is performed at room temperature, reducing the risk of thermal distortion.
Zinc Spraying (Thermal Spraying):
Zinc spraying, or metallizing, involves spraying molten zinc onto the surface of steel pipes. It’s process is
- Surface Preparation: The pipes are cleaned, often by abrasive blasting, to create a suitable surface for zinc adhesion.
- Spraying: Zinc is melted and then sprayed onto the surface of the pipes using a spray gun. This can be done with either flame spraying or arc spraying techniques.
- Finishing: The coated pipes may be further processed to achieve the desired thickness and surface finish.
The major advantages of zinc spraying are
- Versatility: Can be applied to large structures that cannot be dipped in a galvanizing bath.
- On-Site Application: Suitable for on-site repairs and touch-ups.
- Thickness Control: Allows for variable coating thickness as needed.
Sherardizing:
Sherardizing, also known as vapor galvanizing, is a process where zinc powder is used to coat steel pipes. The process consists of:
- Preparation: Steel pipes are cleaned and then placed in a rotating drum along with zinc powder and sometimes other additives.
- Heating: The drum is heated to around 300-450°C (572-842°F). Zinc vaporizes and diffuses onto the surface of the pipes, forming a zinc-iron alloy coating.
- Cooling: The coated pipes are cooled and then inspected for quality.
Its main advantages are:
- Uniform Coating: Produces a uniform zinc-iron alloy coating.
- Good Adhesion: The coating adheres well to the steel surface.
- Low Temperature: Lower process temperature compared to hot-dip galvanizing.
Continuous Galvanizing:
Continuous galvanizing is a method used primarily for producing galvanized steel sheets, which can then be formed into pipes. The process includes:
- Continuous Line: Steel strips are continuously cleaned, annealed, and then passed through a molten zinc bath.
- Forming: The galvanized strips are formed into pipes using tube mills.
- Post-Treatment: Pipes are subjected to additional treatments such as passivation or painting.
The main advantages of this process are
- High Efficiency: Suitable for high-volume production.
- Consistent Quality: Provides uniform coating thickness and quality.
- Cost-Effective: Efficient use of materials and energy.
Disadvantages of Galvanizing Pipes
While galvanizing offers many advantages, it also has some drawbacks:
- Initial Cost: The galvanizing process can be more expensive than non-coated alternatives.
- Limited High-Temperature Resistance: Zinc coatings can degrade at high temperatures, making them unsuitable for certain applications.
- Zinc Whiskers: In some cases, galvanizing can lead to the formation of zinc whiskers—hair-like projections that can interfere with mechanical components.
- Environmental Concerns: The process generates waste and emissions that need to be managed responsibly.
Maintenance of Galvanized Pipes
To ensure the longevity of galvanized pipes, proper maintenance is essential:
- Regular Inspections: Check for any signs of rust, damage, or wear. Address issues promptly to prevent further deterioration.
- Cleaning: Remove any debris, soil, or contaminants that can retain moisture and accelerate corrosion.
- Touch-Up Coating: For areas where the galvanizing has worn away or been damaged, applying zinc-rich paint can provide additional protection.
Galvanizing pipes is a proven method to enhance the durability and lifespan of steel components. Understanding the processes, advantages, and potential drawbacks will enable you to make informed decisions for your projects. Whether in construction, plumbing, or industrial applications, galvanized pipes offer a reliable solution for corrosion resistance and long-term performance.