The full form of FRP is fiberglass-reinforced plastic which is a composite material consisting of a polymer matrix reinforced with fibers. So, an FRP pipe is a pipe manufactured of FRP material by contact molding or filament winding method. Various types of resins like thermosetting polyester, epoxy, phenolic resin, etc are used to get specific FRP pipe properties in the final product. The most widely used reinforcement is the glass fiber “E-glass”. As a corrosion-resistant alternative to metallic piping, the FRP piping system has found worldwide application. By selecting FRP as the pipe material, the need for internal lining, external coating, and cathodic protection can easily be eliminated. FRP piping system is available in a wide range of sizes starting from 1 inch to 144 inches.
Applications of FRP Pipes
Due to its high durability, corrosion resistance, and moderate strength, the use of FRP pipes is increasing day by day. FRP piping systems are used in various industries like:
- Potable Water and desalination industries
- Chemical, Petrochemical, Oil & Gas industries.
- Ducting and Vent piping
- Irrigation and Sanitary services
- Water distribution and transmission
- Slurry piping
- Power plants, etc.
Properties of FRP Piping
The main properties that make FRP Pipes an ideal selection for various industries worldwide are
- Excellent corrosion resistance
- Excellent strength-to-weight ratio. Note that, the strength-to-weight ratio of FRP pipes is higher than steel or other metallic pipes.
- Lightweight which makes it easy for handling and transport.
- Dimensional stability
- Non-toxicity
- Low coefficient of friction (>25% better than steel) that ensures excellent flow characteristics.
- Good abrasion resistance
- Suitable for both aboveground and buried piping
- Resistance to biological attacks like bacteria
- Non-conductive to electricity and
- Low maintenance cost
Typical mechanical properties of the FRP piping system are provided in the table below:
Mechanical Properties of FRP Pipe | Typical Range |
Tensile Strength | 14 to 550 Mpa |
Tensile Modulus | 3.5 to 34.5 Gpa |
Flexural Strength | 28-480 Mpa |
Flexural Modulus | 6.9 to 34.5 Gpa |
Poisson’s Ratio | 0.3 |
Thermal Co-efficient | 14 to 54 mm/mm/0C |
Specific gravity | 1.2 to 2.3 |
Compressive Strength | 69-275 Mpa |
Joining of FRP Pipes
As the FRP pipe lengths are limited by transportation and handling, they are required to be joined. Also, various FRP Pipe fittings need to be joined as per the requirement. The joining system of the FRP pipe should be such that it does not leak for the intended service condition at the operating pressure. Depending on the specific joint configuration and design conditions, the FRP pipe joints may be restrained or unrestrained.
Unrestrained FRP Pipe Joints
Joints that can withstand the internal pressure but can not withstand the longitudinal tensile loads are known as Unrestrained FRP Pipe joints. Examples of such joints are Coupling joints, bell and spigot joints, mechanical coupling joints with elastomeric seals, flanged joints, butt joints with laminated overlay, etc.
Restrained FRP Pipe joints
Such pipe joints are capable of withstanding both internal pressure and longitudinal tensile loads. For these joints, supplemental restraining elements are added to restrict the longitudinal loads. Threaded joints, bell, and spigot joints with laminated overlay or adhesive bonds are examples of Restrained FRP pipe joints.
Note that FRP pipe joint tightness must be ensured following ASTM D4161.
FRP Pipe Fittings
Various FRP pipe fittings are available for proper piping layout needs. Common FRP pipe fittings are
- Long radius and short radius FRP Pipe Elbows (22.5 Degrees, 30 Degrees, 45 Degrees, 60 Degrees, 90 Degrees, 180 Degrees)
- Tee Connections (Equal Tee and Reducing Tee)
- FRP Pipe flanges
- Steel backing flanges
- Flanged elbows
- Smooth flow-reducing elbow
- Special radius bend
- Lateral connection
- Cross connections
- Wye Connections
- Reducers (Eccentric and Concentric)
- Flanged reducers
Codes and Standards for FRP Pipes
Frequently used Codes and Standards that govern the FRP piping details are
- ISO 7370
- ANSI/AWWA C950
- AWWA M45
- ISO 14692
- AWWA C590
- ISO 10467
- BS 5480
- ISO 10639
- ASTM D2996, ASTM D2997, ASTM D5421, ASTM D4024, ASTM D5685
Specification of FRP Pipes
While ordering FRP pipes the following data need to be provided to the vendor:
- Pipe Diameter
- Design and Operating temperature of the service fluid.
- Design, operating, Surge, vacuum, and test pressures.
- Live loads in case of buried piping.
- Maximum/minimum buried depth and trench Widths.
- Details of Soil properties and trench preparation.
Supporting of FRP Piping System
FRP piping systems must be supported properly to avoid excessive sagging. Maximum acceptable sagging is the lower of 12.5 mm or 0.5% of span length. The manufacturer’s guidelines with respect to the supporting shall be followed. Usually, clamped supports with an elastomeric pad are used for support.
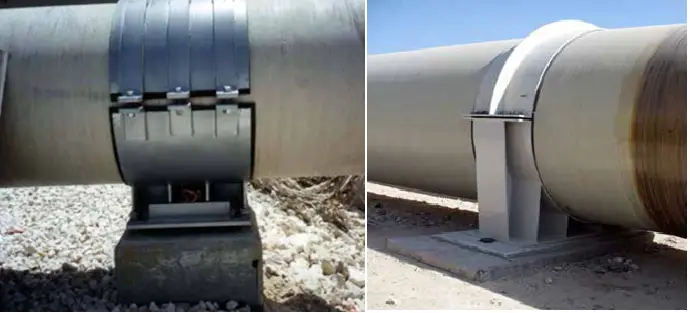
Drawbacks of FRP Piping
The main drawbacks of FRP piping systems are
- FRP pipe is not recommended for carrying fluid with temperatures more than 1000 C
- Slight degradation from UV rays is found to occur which can be reduced by using pigments, dyes, UV stabilizers, fillers, etc in the resin system.
FRP vs GRP: Difference between FRP and GRP
FRP stands for fiber-reinforced plastic while GRP stands for Glass reinforced plastic. So, from the name, it is clear that there is a change in the reinforcing fiber. But, both FRP and GRP are normally used to indicate the same plastic piping products.
FRP vs Steel: Differences between FRP and Steel
As FRP Pipes have superior corrosion resistance capabilities and over the long term it is economic, Steel pipes are replaced by FRP pipes. So, in this section, it will be great to find the differences between FRP and Steel.
- Steel pipes are isotropic while FRP pipes are anisotropic and the properties change with respect to direction.
- FRP pipes are more flexible than Steel pipes due to the lower modulus of elasticity.
- FRP piping systems are designed considering a higher factor of safety than steel piping. The usual factor of safety in the design of FRP pipes varies in the range of 5 to 10.
Other major differences between FRP and Steel pipes are provided in Table 2 below:
Property | FRP | CS | Remarks |
Density | 1850 kg/cu.m | 7800 kg/cu.m | Loads on support are less in the case of FRP pipe as compared to Steel. Handling and transportation of FRP are easier than Steel pipes. |
Co-efficient of thermal expansion | 27 X 10-6 mm/mm 0C | 11 X 10-6 mm/mm 0C | Expansion is almost 2.5 times of Carbon Steel Pipe. So more thermal growth in the case of the FRP Piping system. |
* This value may change from vendor to vendor | |||
Modulus | Axial= 12000 N/sq.mm | Elastic= 211365 N/sq.mm | Considerable difference in the strength of FRP & CS. Anchor loads are less in FRP Pipes as compared to steel pipes. |
Shear= 11400 N/sq.mm | |||
Tensile Strength | 80-135 MPa | 456 MPa | Mechanical Strength is higher for Steel material as compared to FRP. |
Yield Strength | 70-135 MPa | 227 MPa | The yield strength of FRP is lesser than that of Steel. |
Allowable Stress | 4,000 PSI to 20,000 PSI | 20,000 PSI | The strength of the GRE varies drastically and hence proper vendor data is a must. |
Corrosion resistance | Superior | Inferior | The corrosion resistance of carbon steel is much lower than that of FRP pipes. |
Joints | Threaded or glued | Welded | FRP joints are to be checked for higher axial loads and pressure |
FRP vs HDPE: Differences between FRP and HDPE Pipes
The main differences between FRP and HDPE pipes are listed in Table 3 below:
FRP Pipe | HDPE Pipe |
FRP is Orthotropic composite material | HDPE is isotropic material. |
The cost of FRP pipe is very high | The cost of HDPE pipes is considerably lower than FRP Pipes. |
Lower thermal expansion coefficient | The thermal expansion coefficients of HDPE pipes are extensively higher as compared to FRP pipes. |
FRP pipes have a comparatively higher temperature range than HDPE Pipes | Lowe temperature range |
Fabrication time is comparatively longer | Quicker fabrication. |
The strength and Elastic modulus for FRP pipes are higher than HDPE | Lower strength and elastic modulus. |
Easy installation at the site | Costly complex equipment is required for installation. |
Highly skilled professionals are required for site work of FRP piping systems | HDPE pipe works can be done by semi-skilled operators. |
Much lighter in weight due to lower all thickness even though the density of FRP is normally higher than HDPE | Heavier due to higher wall thickness. |
A fire-retardant version of FRP pipes can be made. | HDPE pipes are highly flammable |
The initial cost of FRP pipes is normally higher than the metallic piping systems. But when comparing the total cost over the complete service life FRP Pipes come as a winner due to their long service life.
Stress Analysis of FRP Piping System
In piping stress analysis guides or flexibility specifications, FRP lines are considered critical irrespective of their sizes. So, a proper stress analysis must be performed to investigate the stresses, loads, displacements, supports, etc to decide if the FRP piping system will work smoothly throughout its design life. I have developed an online course explaining step-by-step procedures for FRP piping stress analysis. You can check it out here.
Very useful information
Could you please include Inspection, examination and testing requirements
Thank you very much for this informative Mr. Anup.
what should be the FRP pipes thickness for different pressure ratings
Well compiled. Thank you for sharing
Have you ever heard of transitioning from HDPE to Fiberglass? I currently have a underground HDPE water system that will enter the bottom of a Fiberglass tank. Currently, the design is to stub up the HDPE into the fiberglass tank and resign/wrap the HDPE pipe as a seal for the bottom of the tank. I cannot find much information on transitioning from HDPE to fiberglass without a flange. Do you have any thoughts on this connection?
Hello Mr. Anup Kumar Dey,
Very nice text you wrote congrats!
I’m having some trouble because I need to inject chlorine to tackle some issues with marine growth that get from sea. However, once I inject chlorine I will, for sure, compromise my carbon steel pipes lifetime. I was wondering if I replace the lines from carbon steel to FRP if I could avoid subtantially this corrosion issue. long history short: Can FRP pipes resist to chlorine corrosion?
Can you confirm how well FRP will do with natural gas?
What gas pressures can it sustain?
What joints work well for gas?
Hi Anup,
Very well summarised FRP piping…
I have been using FRP piping in ongoing Project to the great extent mainly in sea water and cooling water. Internal Lined FRP also being used in severe corrosive chemical in same project. If required, I will connect you to get more information.
Thanks
THANKS