Control valves are critical components in many industrial systems. They regulate the flow of fluids and gases to ensure optimal performance and safety. However, their operation and performance can be affected by several phenomena. Choked flow, cavitation, and flashing are certain similar phenomena that impact the control valve design and operation. Understanding these phenomena is crucial for the effective design, operation, and maintenance of control valves. In this article, we will discuss these three issues, explaining their causes, effects, and potential solutions.
What is Choked Flow?
To Understand choked flow, it’s essential to learn the concept of pressure drop “differential pressure.” in a control valve.
The pressure drop is the driving force behind the flow within the valve. A pressure drop across the valve indicates that the fluid is moving from upstream to downstream. There would be no flow through the valve if there were no pressure difference between the upstream and downstream, or if the pressures were equal.
Every valve with flowing media experiences a pressure drop, generating the flow. Whether the pressure drop increases or decreases the flow rate depends on whether the drop becomes higher or lower.
Here’s the general rule of fluid flow through a valve:
- Higher differential pressure = more flow.
- Lower differential pressure = less flow.
- If the pressure drop gets higher, there will be more flow across a valve (to some point).
- If the pressure drop gets lower, there will be less flow across a valve.
However, this increased flow due to increased pressure drop cannot continue indefinitely. At a certain point, you will encounter what is known as choked flow. There comes a point where, if you continue to increase the pressure drop by lowering the downstream pressure, the flow rate will no longer increase. The fluid will reach its maximum velocity at the vena contracta (the point in the valve where the diameter of the flow is at its smallest, and fluid velocity is at its maximum), and beyond that point, it will enter a state known as “choked flow.”
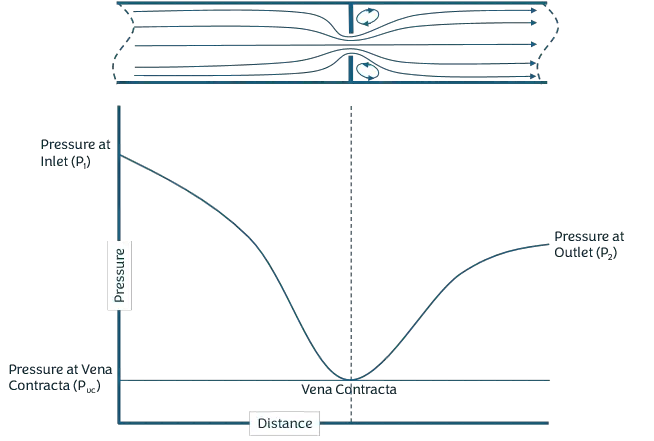
The greater the pressure drop, the more flow you can achieve through a given orifice size. If you want to increase the volume using the same valve and equipment while experiencing choked flow, it won’t be possible.
To resolve choked flow in your valve, you need to reduce the pressure differential. If you’re concerned about insufficient flow through the valve while it’s in choked flow, consider either increasing the valve trim size or boosting the upstream pressure.
It’s crucial to note that once you’re experiencing choked flow, lowering the downstream pressure to increase the pressure differential won’t help in boosting the flow rate.
Increasing the upstream pressure, however, adds more energy to push the fluid or gas through the valve, which can raise the flow rate by enhancing the pressure drop.
In summary, during choked flow, you can push more fluid or gas through the valve, but you can’t pull more through.
What is Cavitation in Control Valves?
Cavitation refers to the creation and subsequent collapse of air or gas bubbles within a liquid. These bubbles form when the liquid experiences a sudden drop in pressure, causing it to fall below its vapor pressure. The bubbles then collapse as the pressure returns to normal. This entire process can occur in a very brief period, shortly after the vena contracta.
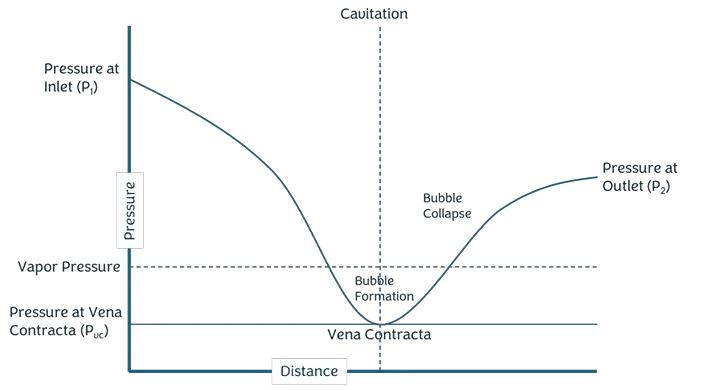
To prevent cavitation in your valves, consider the following three steps:
- Reduce the pressure drop across the valve.
- Position the valve in a cooler section of the process to lower the vapor pressure.
- Ensure the valve is correctly sized, as cavitation frequently occurs when a valve is oversized.
Cavitation is common with high-pressure drops and high velocities. If you’re dealing with a high-pressure drop, be aware that flashing may also be an issue.
What is Flashing in Control Valves?
Cavitation is more often observed in liquids, whereas flashing occurs more frequently in gas production. Flashing takes place when the pressure on liquid hydrocarbons is lowered enough for them to flash into vapor. For instance, if you rapidly reduce the pressure of your oil emulsion from 600 PSI to 100 PSI, it can cause the oil condensate to vaporize. This means the valuable oil in your production could be lost permanently.
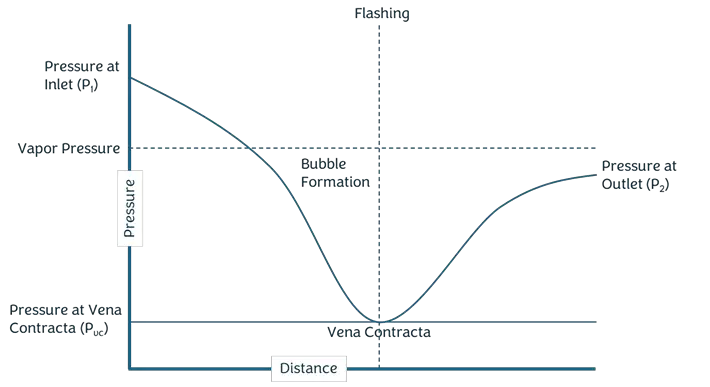