Corrosion allowance in the piping industry refers to the additional thickness of a pipe or other equipment that is added to account for the expected corrosion during its service life. Corrosion is a natural process that occurs when metal is exposed to a corrosive environment such as water, acids, and chemicals. Corrosion can cause the metal to deteriorate and weaken, which can lead to leaks, equipment failures, and safety hazards. Corrosion allowance is widely popular by its acronym CA.
To prevent corrosion-related failures, piping systems are designed with a corrosion allowance, which is typically a small additional thickness added to the pipe wall. The corrosion allowance is based on the expected corrosion rate of the material in the specific service environment and the expected service life of the piping system.
The corrosion allowance is typically specified by the piping design engineer in the piping material class and is based on industry standards and codes. The additional thickness of the pipe ensures that even if corrosion does occur, the pipe will still have sufficient wall thickness to maintain its strength and integrity, and the expected service life will not be compromised. The corrosion allowance is an important factor in ensuring the reliability and safety of piping systems.
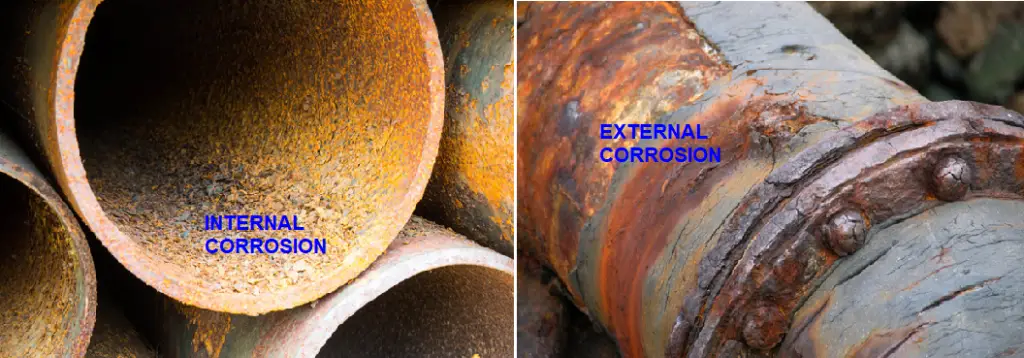
Factors Affecting Corrosion Allowance
The corrosion allowance in piping systems typically depends on several factors, including:
- Material: The type of material used for the piping system, such as carbon steel, stainless steel, or other alloys, can impact the corrosion rate and thus the necessary corrosion allowance.
- Service environment: The corrosiveness of the service environment, such as exposure to saltwater, acids, or chemicals, can impact the corrosion rate and determine the necessary corrosion allowance.
- Operating temperature and pressure: Higher operating temperatures and pressures can increase the corrosion rate and thus require a higher corrosion allowance.
- Flow rate and velocity: The flow rate and velocity of the fluid through the piping system can impact the corrosion rate and determine the necessary corrosion allowance.
- Service life: The expected service life of the piping system can also impact the corrosion allowance, as a longer service life may require a higher corrosion allowance to account for potential corrosion over time.
These factors are typically evaluated by the piping and process engineer and used to determine the appropriate corrosion allowance for the specific piping system. The corrosion allowance is an important consideration in ensuring the reliability and safety of the piping system over its expected service life.
Corrosion Allowance for Steel
The corrosion allowance for steel in piping systems depends on several factors, including the type of steel, the service environment, the operating conditions, and the expected service life. The corrosion allowance for steel is typically specified by industry standards and codes, such as ASME B31.3, which provide guidelines for the design and construction of process piping systems.
According to ASME B31.3, the minimum corrosion allowance for carbon steel piping in typical process applications is 1.6 mm (1/16 inch). However, the actual corrosion allowance required may vary depending on the specific service conditions and is typically determined by the piping design engineer with the help of the process engineer.
For more corrosive service environments, such as those involving saltwater or acidic solutions, a higher corrosion allowance may be required. Additionally, the expected service life of the piping system may also impact the necessary corrosion allowance.
It is important to note that the corrosion allowance is intended to provide a margin of safety for the piping system and should be carefully considered in the design and construction of the system. The corrosion allowance is an important factor in ensuring the reliability and safety of piping systems over their expected service life.
Usually, the corrosion allowance for stainless steel, DSS, and PE/Roto-lined carbon steel pipes are considered zero. However, in certain conditions, SS or DSS material can have corrosion allowance.
Clause 8.2 of ISO 21457 provides commonly used corrosion allowance values for pipes. As per that standard, the usual corrosion allowance values are:
- 1.0 mm to 1.5 mm for non-corrosive service;
- 3.0 mm for mildly corrosive service;
- 6.0 mm for severely corrosive service.
Effect of Corrosion Allowance in Pipe Stress Analysis
The corrosion allowance can affect pipe stress analysis in several ways:
Wall thickness: The corrosion allowance adds to the pipe’s wall thickness, which can impact the pipe’s stress levels. In cases where the pipe is designed to operate close to its maximum allowable stress, the additional wall thickness due to the corrosion allowance can result in a reduction in the available stress capacity.
If you observe ASME B31.3 code equations closely, you can find that sustained stresses are calculated by reducing the corrosion allowance from the nominal pipe thickness. However, during expansion stress calculation, the corrosion allowance is not subtracted.
Weight and support requirements: The additional weight of the corrosion allowance can impact the pipe’s support requirements. In some cases, additional supports or modifications to existing supports may be required to account for the additional weight.
It is important to consider the impact of the corrosion allowance on pipe stress analysis and design the piping system accordingly. Because of this corrosion allowance is an important input parameter in piping stress analysis. The piping design engineer should take into account the specific service conditions and expected service life of the piping system to determine the appropriate corrosion allowance and ensure that the system can withstand the applied loads without exceeding the allowable stresses.
Please is corrosion allowance factored into original thickness or it is separate from the original.
If a pipe has an original thickness schedule of sch40 which for example is 7.11 will it read higher than this due to corrosion allowance?
Within 7.11, the corrosion allowance is already considered… 7.11 mm considers calculated design thickness plus corrosion allowance plus mechanical allowances.
Is there a limit for the corrosion allowance for carbon steel? I mean can I increase the CA to values like 10 or 12 mm to avoid cladding for example? what is the ration behind limiting the CA to such levels of 6 mm (or in some particular cases to 8 mm)
May I know corrosion allowance in structural steels?