A desalination plant is a facility that converts salt water from the sea into water suitable for human consumption, as well as for industrial or irrigation purposes. Desalination can be achieved by two types of processes: thermal or transmembrane. Semi-permeable membrane desalination is the most widely used technology in the industry because it requires much less energy than thermal desalination and is therefore more cost-effective.
This article will focus on this second type. This is the most widely used reverse waterproofing process in use today in many countries around the world.
The high demand for drinking water and the high energy potential available have enabled the development of sustainable methods of energy production based on seawater desalination, making it an increasingly attractive and necessary technology. There are several technologies used on an industrial scale to desalinate seawater. Among all the technologies, seawater reverse osmosis is the most widely used worldwide.
It is now a mature technology and can be found in many coastal areas of the world where natural water resources are limited. Advances in research and development related to this technology are ongoing. One of the latest innovations aims to significantly reduce energy consumption and minimize adverse effects on membranes.
Reverse Osmosis Process Description
To understand the purpose and process of reverse osmosis, we must first understand the natural process of osmosis.
Osmosis is a natural phenomenon. It is one of the most important processes in nature and occurs when two solutions with different solute concentrations are separated by a semi-permeable membrane (allowing only the solvent to pass through). This phenomenon occurs spontaneously without any energy input.
Thus, two solutions with different salt concentrations tend to equalize their concentrations. The solvent from the lower-concentration solution tends to flow through the semi-permeable membrane into the higher-concentration solution until the concentration is uniform.
The driving force of this solvent flow depends on the osmotic pressure and is related to the difference in solute concentration between the two solutions. Specifically, it is defined as the equilibrium pressure that is established between solution and solute. Therefore, the osmotic pressure of a pure solvent is zero. When equilibrium is established between two solutions of different concentrations, the equilibrium pressure is equal to the osmotic pressure difference.
The process of reverse osmosis involves osmosis in the opposite direction. Osmosis occurs spontaneously without energy, so energy must be supplied to make it occur in the opposite direction.
Solvent transfer occurs from the concentrated solution to the more dilute solution. Reproducing this phenomenon in seawater on an industrial scale requires a pump (needed to generate pressure) and a semi-permeable membrane to allow the solvent to pass through.
A reverse osmosis membrane is a semi-permeable membrane that allows water molecules to pass through, but not various compounds that are not required for the end use of the water. In addition, it can also contain bacteria.
The buoyancy must be higher than osmotic for the water to be desalinated. When the concentrated solution is pressurized, water molecules pass through the semi-permeable membrane while contaminants are retained.
A desalination plant can be divided into four stations.
- Pumping, storage, and screening.
- Pre-treatment and high-pressure pump
- Process: Reverse Osmosis.
- Post-treatment
Seawater Pumping
Seawater recovery systems for desalination plants include open or closed intakes.
Open water intakes draw water directly from the sea. They are the most vulnerable to overflows and, for obvious reasons, present a higher risk of contamination. Therefore, the quality of the water obtained may vary.
In contrast, water from a closed intake (a well) is not an inexhaustible source of water, and although it is more uniform and of higher quality, it can be assumed that its capacity decreases significantly with relative frequency.
Thus, from the point of view of flow assurance, the open intake has an obvious advantage, as the difficulty of securing the production flow in well water is high.
A disadvantage of large-capacity plants is that they require large areas for permeable marine boreholes, which limits the supply rate. Therefore, the first step in the water treatment process is to pump water from the natural environment to the plant.
If the natural soil is not suitable, water must be pumped to the plants. The function of the pumping station is to send water to the desalination plant. The factor that ensures this pressure peak for the water supply to the plant is the hydraulic pump, whose operating point is determined by the flow rate required for the installation process as well as the pressure.
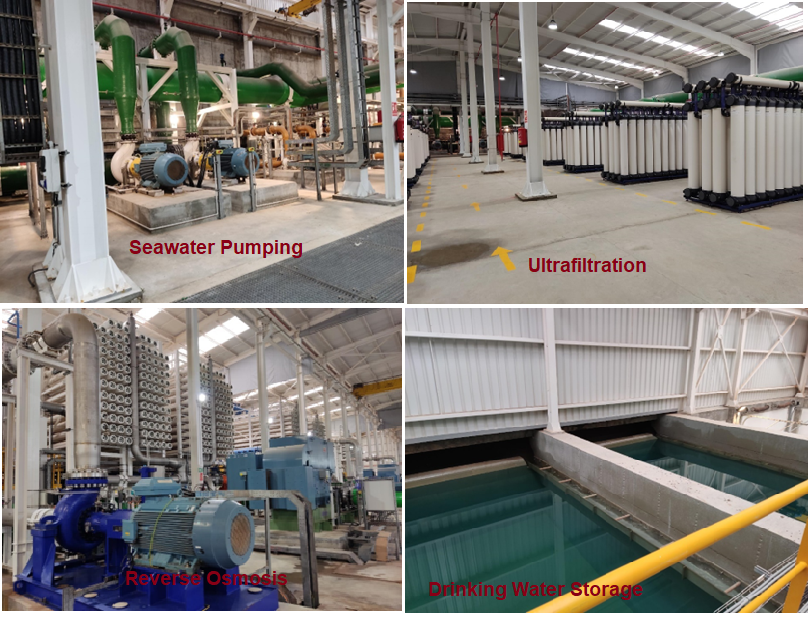
Pre-treatment
Reverse osmosis desalination requires a very thorough pre-treatment of the seawater to prevent suspended solids from settling on the membrane. This rapidly reduces the flux produced.
The purpose of pre-treatment is varied. First, it keeps the module free of blockages from suspended solids, microorganisms, and salt deposits, among others. On the other hand, the water must be given characteristics compatible with the nature of the membranes: chlorine content, pH, temperature, etc.
Depending on the type of reverse osmosis module, all particles larger than 10-50 µm must be retained. This is done by using coarse pre-filtration followed by sand filtration to remove larger suspended solids.
Subsequently, biocide treatment and acidification are required to prevent microbial growth on the membrane and to avoid carbonate precipitation. Finally, the cartridge filtration method can retain particles as small as tens of microns, which cannot be retained by sand filters.
The process used is appropriately selected according to the water quality of the feed water. Nowadays, the removal of contaminants by ultrafiltration (UF) membranes is the most widely used process, as it offers the best balance between contaminant removal and product penetration. The main pre-treatment steps are:
- – Chlorination
- – Clarification: Coagulation Flocculation Sedimentation
- – Prevention of scaling
- – Discolouration – Cartridge filtration
These procedures are carried out using self-cleaning filters, ultrafiltration, and chemical dosing systems.
- Ferric chlorine: Coagulation of small particles at the UF inlet.
- Sulphuric acid: UF and RO washing systems
- Bisulfite: Chlorine neutralization at the RO inlet.
- Antiscalant: Prevents precipitation on RO membranes.
- Sodium hypochlorite: Drinking water tank disinfection
- Sodium hydroxide: PH adjustment for drinking water
A high-pressure pump pumps seawater into the RO module where the membrane is located.
Desalination and energy recovery.
At this point, the water has already gone through all the preliminary pre-treatment stages, where it underwent Physicochemical conditioning to minimize the risk of blockages in the desalination equipment due to the precipitation of poorly soluble salts and the accumulation of suspended particles. It has also been conditioned to balance its mineral content and reduce its highly corrosive nature.
Before entering the reverse osmosis membrane, the treated seawater is pressurized with a high-pressure pump, typically between 45 and 90 bar, depending on the temperature and salinity of the water. At this point, it is possible to separate the salts by obtaining a stream of potable water on one side and what is known as “reject” on the other. Pumps are used to increase the transmembrane pressure.
Pumps are used to increase the transmembrane pressure. Pumps or an agitation system allow the water to be treated to circulate within or between the modules. Separation is achieved in the membrane modules.
Two types of systems can be distinguished, depending on how the transmembrane pressure is applied.
Pressure filter system
A basic reverse osmosis desalination system consists of a high-pressure pump feeding brine to a set of spirally wound membranes. The substance enters the membrane and exits the assembly without pressure, while the concentrate is kept under pressure by a pressure regulating valve and finally exits the system when it is opened.
Submerged membrane systems
Semi-permeable reverse osmosis membranes for seawater treatment are usually made of polyamide compounds, but some also use cellulose acetate.
Polyamide membranes are characterized by a higher specific water content and a higher salt-holding capacity than cellulose acetate membranes. Polyamides are stable over a wide pH range but are susceptible to oxidative degradation by chlorine.
Semi-permeable membranes are used to withstand various working pressures in the industry and must be arranged according to specifications.
The production capacity of a desalination plant is obtained by installing several basic production units or modules in parallel. Thus, a module is nothing more than a set of membranes of a specific configuration that form the basic unit to produce permeate water.
Energy recovery
A reverse osmosis plant uses a large amount of energy to reach the pressure levels required for the process. This stage of the desalination plant consumes the most energy.
The pressure drop across the reverse osmosis membrane is approximately 1.5-2 bar, depending on the number of cells per pressure pipe. As mentioned, reverse osmosis desalination generally converts only 45% of the energy used into a pure water stream, and the rest is discarded as a high-pressure waste stream.
Thanks to the energy recovery system, it is possible to reuse the energy from this stream. This stream is sent to an energy recovery system, which transfers its energy directly to a part of the water supply.
There are two main concepts in energy extraction.
Turbine:
Driven by the high-pressure waste stream exiting the diaphragm, it rotates a shaft connected to a high-pressure pump motor, which reduces the amount of electrical energy required to pressurize the feed stream of the osmosis process.
Pressure exchange:
Uses the positive displacement principle to pressurize seawater in direct contact with saltwater by removing the reverse osmosis membrane.
The water removed by reverse osmosis is sent to the PX unit, where its pressure is transferred directly to a part of the water supply with an efficiency of more than 95 %. This feed water leaves the controlled heat recovery unit and passes through a booster pump to compensate for hydraulic losses in the piping, the heat recovery unit, and the membrane.
Seawater flows to the outlet of the high-pressure pump but does not pass through it. This is important because the high-pressure pump can be sized to pump only a flow rate equal to the sorbent volume instead of the entire feed stream, as well as reducing the electrical energy required.
Pressure exchangers increase the efficiency of desalination plants by harnessing waste energy. By pressurizing part of the water supply, high-pressure pumps can be downsized by up to 60 %. This not only saves energy consumption but also capital investment costs.
Reverse Osmosis Principle
The reverse osmosis process, as explained above, consists of making the solvent (water) pass through the semi-permeable membrane from the side where the most concentrated solution is (seawater, with dissolved salts) to the opposite side, without the salts passing through, by exerting pressure on the liquid.
This pressure depends on the degree of desalination to be achieved. In this way, you get two flows. One is a low salinity flow called “permeate” and the other is a high salinity flow called “reject”.
It should be remembered that during the phenomenon of osmosis, only water molecules from the low-concentration solution spontaneously cross the membrane to bind to the high-concentration water to restore the balance of concentrations.
This is followed by the phenomenon of reverse osmosis or hyperfiltration, where pressure is applied to the new concentrated solution to “force” the water through the membrane. This process produces fresh water with very good results, as the membrane retains between 95% and 100% of the particles in the water. This percentage varies depending on the quality of the membrane.
Post-treatment
In most cases, all or part of the produced water is intended for human consumption and must comply with local drinking water regulations. Further processing (ion exchange, electro-deionization) is required.
Some countries do not have quality standards for drinking water. In such cases, the recommendations of the World Health Organisation (WHO) can serve as a reference for the international community. The WHO classifies drinking water quality standards into five groups. Those of interest to the desalinated water producer relate to:
Physical properties: temperature, clarity, odor, suspended solids (SS) content. Chemical properties: salinity, chlorine, pH, etc.
For each criterion, the WHO assigns a guideline value. A key factor in desalination is the desired final salinity. However, sometimes more specific criteria are required, such as B, Br, and heavy metal content, and may require adjustment or further treatment.
At this point, enrichment of the end-use water is sought through remineralization. This can be:
Remineralization by addition of CaCl2 and NaHCO3
This method essentially consists of adding a solution of sodium bicarbonate and calcium chloride directly to the permeate in well-defined doses to obtain equilibrium water. Remineralization by this method is easy and fast, but the conservation of the product is problematic. In large plants, this remineralization process requires large quantities of reagents. This requires the provision of sufficient reagents and space to ensure that these products are not exhausted.
Remineralization by passage through a calcite bed
In this remineralization process, water is filtered through the calcite layer from the bottom up and the resulting water is remineralized. Remineralization by this method is effective, simple, and therefore easy to operate.
Remineralization of infiltrated water by the addition of Ca(OH)2
The osmosis water (the permeate) is remineralized by injecting the prepared Ca(OH)2 lime water into a lime solution to obtain balanced water.
Water storage and waste disposal
Drinking water produced in factories must be stored in buffer water tanks upstream of the municipal water distribution network. On the other hand, the discharged water can be further treated and discharged into the sea, minimizing the impact.
Further Studies and Online Video Courses
If you still have queries, the following video courses will surely give you an enhanced experience: