Diaphragm valves are an essential part of many industrial processes, and are commonly used in applications where precise control over fluid flow is required. These valves consist of a flexible diaphragm that separates the valve body from the fluid being controlled and are available in a variety of materials, sizes, and configurations. In this article, we will discuss the basic principles of diaphragm valves, their construction and working, types and applications, advantages and disadvantages, and maintenance requirements.
Construction and Working
Diaphragm valves consist of a valve body, which houses a flexible diaphragm, and a bonnet, which secures the diaphragm to the valve body. The diaphragm is usually made of rubber, neoprene, or other elastomers, and is designed to be flexible enough to deform under pressure, allowing fluid to pass through the valve. When the valve is closed, the diaphragm seals the valve body, preventing fluid from passing through.
The operation of a diaphragm valve is controlled by a mechanism that presses the diaphragm against the valve body, either opening or closing the valve. The most common type of mechanism used in diaphragm valves is the handwheel or actuator. The handwheel is connected to a stem, which is attached to the diaphragm, and when turned, moves the diaphragm up or down, opening or closing the valve. The actuator is a more complex mechanism that is controlled by an electrical signal or pneumatic pressure and is used in automated control systems.
Diaphragm Valve Parts
A diaphragm valve has the following components:
- A strong and rigid Valve Body
- A Bonnet to cover the top of the diaphragm valve
- A Diaphragm
- A Compressor to operate the diaphragm
- Stem (Rising or non-rising type)
- Actuator (Manual, Electric, Pneumatic, Hydraulic, or Thermal)
- Position Indicators
Types of Diaphragm Valves
There are several types of diaphragm valves, each with its own unique design and application. They are classified based on valve construction and application.
Based on valve body and diaphragm design, there are two types of diaphragm valves; Weir diaphragm valves and Straight through diaphragm valves. Fig. 1 (Pic Courtesy: https://www.globalspec.com/) shows a schematic of both types of diaphragm valves.
Weir Diaphragm Valves
Weir diaphragm valves are designed with a raised lip, or weir, around the edge of the valve body. The diaphragm is positioned over the weir, and when the valve is opened, the fluid flows over the weir and through the valve. This is the most popular design of diaphragm valves. Weir diaphragm valves are usually preferred for handling gases and clean and homogeneous liquids.
Straight through Diaphragm Valves
Straight-through diaphragm valves have a flat bottom valve body, with the diaphragm positioned directly over the fluid flow path. They have a comparatively short service life and are preferred for handling semi-solid media such as slurries, sludges, and viscous fluids.
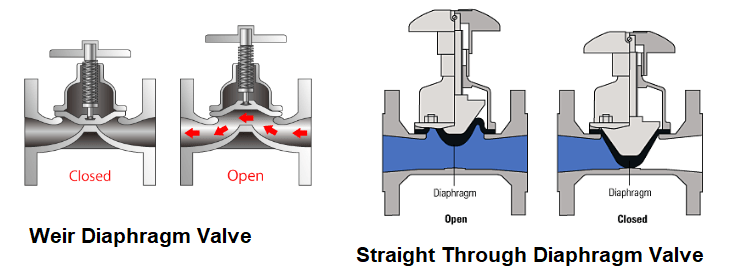
Based on the application, the following types of diaphragm valves are popular:
Sanitary Diaphragm Valves
Sanitary diaphragm valves are widely used in applications that need a high degree of fluid purity and cleanliness. Typical industries include winemaking, dairy, beverages, food, and pharmaceutical processing. By creating an aseptic environment for the flowing media, these type of diaphragm valves eliminates the thriving of bacteria, fungi, and viruses.
Biotech Valves
Biotech valves are special types of diaphragm valves that handle fluids containing microorganisms, cells, and other biological matter. These valves are mostly found in pipelines involving bioreactors, fermenters, filtration, and chromatography skids that are typically used in the biotechnology fields such as medicine, agriculture, the pharmaceutical industry, and food science.
Hygienic Valves
Hygienic valves are specifically designed diaphragm valves such as to eliminate the possibility of fluid stagnation. They are used to handle products intended for human consumption. Hygienic valves are widely used in the food and beverage industries.
Process Valves
This type of diaphragm valve is used to regulate the flow rates of liquid and gaseous fluids in process industries.
Zero Static Valves
Zero static valves are mainly used in the pharmaceutical industry. They are multi-port valves that allow process fluids to be transferred, drained, sampled, or diverted without inducing a major impact on critical systems such as Water for Injection (WFI) or Purified Water.
Diaphragm Valve Symbol
The specific symbol used for a diaphragm valve may vary depending on the standard being used and the specific application. In general, the diaphragm valve is denoted by any of the following symbols as mentioned in Fig. 2
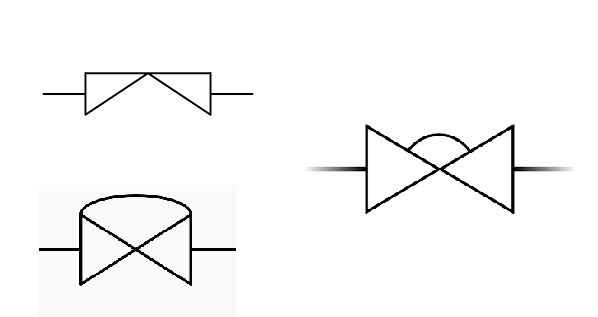
Materials of Construction of Diaphragm Valves
Diaphragm valves are available in a variety of materials of construction, depending on the specific application requirements. The most common materials used for diaphragm valves include:
- PVC (Polyvinyl Chloride): PVC is a thermoplastic material that is commonly used for low-pressure applications. It is resistant to a wide range of chemicals and is relatively inexpensive. However, it has a limited temperature range and may become brittle over time.
- CPVC (Chlorinated Polyvinyl Chloride): CPVC is a thermoplastic material that is similar to PVC but has better resistance to high temperatures and corrosive chemicals. It is commonly used for industrial applications that require a higher level of chemical resistance.
- PP (Polypropylene): PP is a thermoplastic material that is highly resistant to a wide range of chemicals and has a relatively high-temperature range. It is commonly used for applications involving corrosive liquids and gases.
- PVDF (Polyvinylidene Fluoride): PVDF is a thermoplastic material that is highly resistant to a wide range of chemicals and has a high-temperature range. It is commonly used for applications involving highly corrosive and aggressive fluids.
- Stainless Steel: Stainless steel is a highly durable and corrosion-resistant material that is commonly used for high-pressure and high-temperature applications. It is available in a range of grades and alloys to meet specific application requirements.
- Hastelloy: Hastelloy is a nickel-based alloy that is highly resistant to corrosion and chemical attack. It is commonly used for applications involving highly corrosive and aggressive fluids.
- Titanium: Titanium is a highly durable and corrosion-resistant metal that is commonly used for applications involving highly corrosive and aggressive fluids. It is also lightweight and has a high strength-to-weight ratio.
In addition to the materials listed above, diaphragm valves can also be constructed from other materials such as brass, bronze, stainless steel, cast iron, ductile iron, cast steel, and other metals, depending on the specific application requirements. The selection of the materials of construction for diaphragm valves is critical to ensure proper operation and longevity in the specific application.
Selection of a Diaphragm Valve
When selecting a diaphragm valve, there are several important parameters that should be considered to ensure that the valve is suitable for the specific application. Some of the key parameters to consider when selecting a diaphragm valve include:
- Valve size: The size of the valve should be chosen based on the flow rate and pressure requirements of the application. Diaphragm valves are available in a range of sizes, from small valves suitable for laboratory use to large valves for industrial applications.
- Materials of construction: The materials used to construct the valve should be selected based on the specific application requirements. Factors to consider include the fluid being handled, the temperature and pressure of the application, and the potential for corrosion or chemical attack.
- Diaphragm material: The material used for the diaphragm should be selected based on the specific fluid being handled and the pressure and temperature of the application. Common diaphragm materials include rubber, PTFE, and other plastics.
- Valve actuation: Diaphragm valves can be manually operated or automated. The method of actuation should be chosen based on the specific application requirements, including the frequency of operation and the need for precision control.
- End connections: The end connections of the valve should be selected based on the specific piping configuration of the application. Diaphragm valves are available with a range of end connections, including threaded, flanged, and tri-clamp connections.
- Flow control: The valve should be selected based on the specific flow control requirements of the application. Some diaphragm valves are designed for precise flow control, while others are designed for on/off applications.
- Maintenance and repair: The valve should be selected based on its ease of maintenance and repair. Diaphragm valves should be easy to disassemble and reassemble for cleaning and maintenance, and replacement parts should be readily available.
By considering these parameters, it is possible to select a diaphragm valve that is well-suited for the specific application, ensuring optimal performance and longevity.
Applications of Diaphragm Valves
Diaphragm valves are commonly used in a variety of industries, including pharmaceuticals, food and beverage, chemical processing, and water treatment. They are used in applications where precise control over fluid flow is required, and where contamination of the fluid must be minimized. Some of the most common applications of diaphragm valves include:
- Pharmaceutical Manufacturing: Diaphragm valves are used in pharmaceutical manufacturing to control the flow of fluids during the production of drugs and other pharmaceutical products. They are used to control the flow of liquids and gases and to prevent contamination of the product by foreign particles.
- Food and Beverage Processing: Diaphragm valves are used in food and beverage processing to control the flow of fluids during the production of food and beverages. They are used to control the flow of liquids and gases and to prevent contamination of the product by bacteria and other contaminants.
- Chemical Processing: Diaphragm valves are used in chemical processing to control the flow of chemicals during the production of various chemicals and compounds. They are used to control the flow of highly corrosive and toxic substances and to prevent contamination of the environment and personnel.
- Water Treatment: Diaphragm valves are used in water treatment plants to control the flow of water and other liquids during the treatment process. They are used to control the flow of chemicals and other additives and to prevent contamination of the water supply.
Advantages and Disadvantages
Diaphragm valves offer several advantages over other types of valves, including:
- Precise Flow Control: Diaphragm valves offer precise control over fluid flow, making them ideal for applications where accurate flow rates are critical.
- Low Maintenance: Diaphragm valves are easy to maintain, requiring minimal maintenance and replacement parts.
- Corrosion Resistance: Diaphragm valves are available in a variety of materials, including plastic and stainless steel, which offer excellent corrosion resistance.
- Minimal Pressure Drop: Diaphragm valves have a minimal pressure drop across the valve, which means they can be used in applications where high flow rates are required.
However, diaphragm valves also have some disadvantages, including:
- Limited Temperature Range: Diaphragm valves are typically not suitable for use in high-temperature applications, as the diaphragm material may degrade.
- Limited Pressure Range: Diaphragm valves may not be suitable for use in high-pressure applications, as the diaphragm may rupture.
- Limited Flow Capacity: Diaphragm valves may not be suitable for applications requiring high flow rates, as the valve body may become blocked or the diaphragm may rupture.
Maintenance Requirements
Diaphragm valves are generally low-maintenance, requiring only periodic cleaning and inspection. The diaphragm should be inspected regularly for signs of wear or damage and should be replaced as needed. The valve body should be cleaned periodically to remove any debris or buildup that may interfere with the operation of the valve. In addition, any actuator or control mechanism should be inspected and tested regularly to ensure proper operation.
Leading manufacturers of Diaphragm Valves
There are several leading manufacturers of diaphragm valves, each with its own unique product offerings and strengths. Some of the top manufacturers of diaphragm valves include:
- Gemu: Gemu is a German-based company that specializes in the manufacture of high-quality diaphragm valves for a wide range of applications. Their products are known for their durability, reliability, and precision.
- Saunders: Saunders is a UK-based company that produces a range of diaphragm valves for applications in industries such as chemical processing, pharmaceuticals, and water treatment. Their valves are known for their high performance, long service life, and ease of maintenance.
- GF Piping Systems: GF Piping Systems is a Swiss-based company that offers a comprehensive range of diaphragm valves for industrial applications. Their valves are known for their excellent chemical resistance, easy maintenance, and long service life.
- Aquasyn: Aquasyn is a US-based company that specializes in the manufacture of diaphragm valves for the biopharmaceutical industry. Their valves are designed for high-purity applications and are known for their exceptional cleanliness, reliability, and ease of maintenance.
- Alfa Laval: Alfa Laval is a Swedish-based company that offers a range of diaphragm valves for use in industries such as food and beverage, pharmaceuticals, and chemicals. Their valves are known for their high performance, reliability, and ease of installation.
These are just a few examples of the leading manufacturers of diaphragm valves. When selecting a diaphragm valve supplier, it is important to consider factors such as product quality, reputation, service and support, and overall value for money.
Diaphragm Valve Price
The price of a diaphragm valve can vary widely depending on several factors, including the size and type of the valve, the materials of construction, and the manufacturer. In general, smaller diaphragm valves suitable for laboratory or research applications may cost a few hundred dollars, while larger industrial diaphragm valves may cost several thousand dollars or more.
Additionally, automated or electronically actuated diaphragm valves may cost more than manually operated valves, and valves constructed from specialty materials may also carry a premium price tag.
It’s important to keep in mind that the cost of a diaphragm valve should not be the only factor considered when selecting a valve. It’s also important to consider the performance, reliability, and longevity of the valve, as well as the cost of maintenance and any associated equipment or installation costs.
Overall, it’s best to work with a reputable supplier who can help you select a diaphragm valve that meets your specific application requirements and budget.
Conclusion
Diaphragm valves are a versatile and reliable type of valve that is used in a variety of industrial applications. They offer precise control over fluid flow, are easy to maintain, and are available in a variety of materials and configurations. While they may not be suitable for use in high-temperature or high-pressure applications, they are an ideal choice for applications requiring precise control over fluid flow and low maintenance requirements. By understanding the basic principles of diaphragm valves, their construction and working, types and applications, advantages and disadvantages, and maintenance requirements, industrial professionals can select and operate these valves effectively to meet their specific process needs.