Emergency showers and eyewash stations are installed in chemical and petrochemical plants as a safety requirement to provide on-the-spot decontamination in case of accidental chemical exposure. Eyewash stations allow workers to flush away hazardous injury-causing substances. Emergency showers and eyewash stations are required backup preparation to minimize the effects of accidental exposure to chemicals.
In response to the increased use of hazardous chemicals, Eyewashes and safety showers were developed. They are emergency systems used in both public and private industries to protect an employee from injury in the case of contact with chemical compounds, hazardous chemicals, or fire. These safety systems are used in four basic ways as mentioned below:
- Dilution—diluting the chemicals that are on the skin or in the eyes to a nonharmful level.
- Extinguishment—putting out fires of clothing on the body.
- Irrigation—flushing the chemicals out of the eyes or of the skin.
- Warming/cooling—warming or cooling the body or eyes because of a change in temperature due to chemical exposure.
Industry Statistics over the years show that each year a huge number of workers are afflicted by chemical exposures to the eyes. This ensures the requirements of eyewash stations in plants. Hence, Few countries made it a mandatory requirement to install Emergency Eyewash and safety showers at workplaces in industrial plants handling toxic substances. The Occupational Safety and Health Administration (OSHA), 29 CFR 1910.151 (c), requires that:
“Where the eyes or body of any person may be exposed to injurious corrosive materials, suitable facilities for quick drenching or flushing of the eyes and body shall be provided within the work area for immediate emergency use”
Locating Eyewash and Safety Shower Facilities
Installation of an emergency eyewash facility complying with ANSI/ISEA Z358.1 at the correct location is an important technical safety requirement for most oil and gas facilities. The appropriate selection, placement, maintenance, and use of emergency eyewash and safety shower equipment reduces the cost of workplace injuries to a great extent.
Established medical criteria say that during corrosive or caustic exposure to the skin and eye, a 15 minutes water flush in the body and eyes provides emergency first aid. Following these criteria, The ANSI/ISEA Z358.1-2014 standard provides the dimensional and performance requirements for safety shower and eyewash equipment. It ensures that the units shall provide sufficient flow of flushing fluid (mostly water) at a safe temperature (15 Deg to 36 Deg C) and a spray pattern without being injurious.
Industrial Practice is to install emergency shower and eyewash stations in all areas like
- High dust areas
- Battery charging areas
- Dipping operations
- Laboratories
- Hazardous substances dispensing areas
- Spraying operations
After a chemical exposure, the first few seconds (normally the first 15 seconds) are highly critical. So eyewash and safety shower facilities should be located as near to the hazard location as possible. If the time taken to reach the safety shower is more, the chemical can interact with the body part and permanent scarring may result. There should not be any partition wall or barrier between the hazard site and eyewash facilities.
Types of Eyewash and Safety Shower Equipment
ANSI standard provides three basic types of Eyewash and Safety Shower Equipment:
- Emergency shower
- Eyewash station and
- Combination of Safety shower and eyewash station
Emergency Shower
An emergency safety shower is a piece of equipment capable of delivering an adequate flow of flushing fluid, dispersed in a pattern to maximize the rinsing of the body for a minimum of 15 minutes. Flushing fluid can come from overhead, the side(s), or both. However, The flow pattern should meet the minimum height and dimensional requirements of the ANSI/ISEA Z358.1. Safety showers are of two types
Plumbed Emergency Showers:
- This is permanently connected to a source of flushing fluid (overhead tank).
- Plumbed emergency showers can be wall-mounted, floor-mounted, or ceiling mounted.
Self-contained Emergency Showers:
- Such emergency showers contain their own flushing fluid.
- After each use, the fluid is refilled.
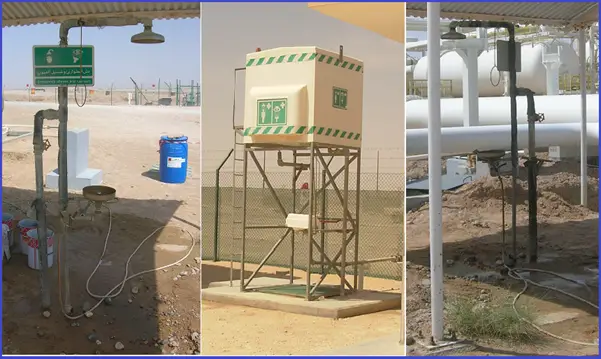
Eyewash Stations
Eyewash stations are equipment that can supply adequate fluid to rinse both eyes for a 15-minute duration. The velocity of the flow has to be low enough so that the user can comfortably hold his eyes open. These equipment are installed in areas where impairment of the eye tissue is likely but the possibility of full-body exposure is minimal. Generally, These devices are produced to deliver a minimum 3.0 GPM stream of fluid targeting the ocular cavity, eyes, and face. To provide a gentler rinse, Some fixtures divert the central stream of fluid into several smaller streams or droplets while others provide a directed stream of water to the eye cavities. Similar to Safety Showers, eyewash equipment can also be grouped into two categories:
Plumbed Eyewash Station Unit
They are installed in a fixed position to supply the flushing fluid of adequate volume and pressure complying with the manufacturer’s specifications. The eyewash nozzles must be protected with integrated covers from airborne contaminants.
Self-contained Eyewash Station Unit
They contain a large volume reservoir of flushing fluid within the unit. They can be permanently fixed in place or portable units designed to be easily moved from one location to another.
Safety Shower and Eyewash Station combination
Where there is a risk of exposure to the body, eye, and facial together, Emergency shower and eyewash combination units are typically considered.
Sometimes, Some additional supplemental elements are used in different plants. These are Personal Wash Units, Drench Hoses, Primary Emergency Fixtures, Backflow Preventers, Dust Covers, Foot Controls, Freeze Protection Units, Modesty Curtains, etc.
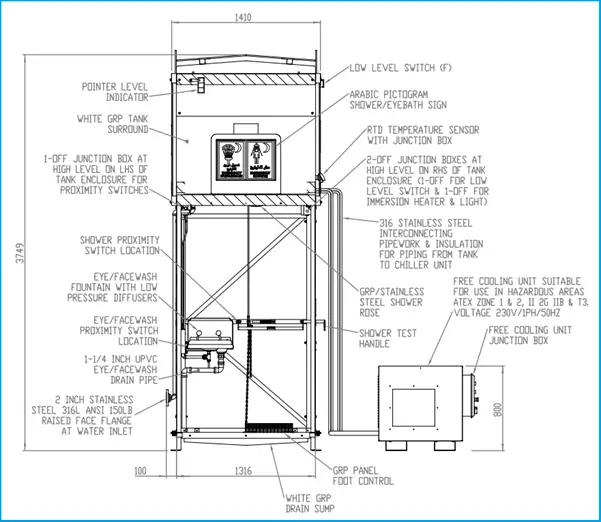
Other types of safety shower and eye wash stations that the ANSI standard refers to are:
- Personal eyewash
- Eye/Face wash, and
- Hand-held drench hose
Radioactive or highly toxic materials may require a total decontamination shower. These are booth-type showers with numerous spray nozzles. Such units may be combined with central overhead sprayers. A complete safety station combines the eye/face wash fountain with a drench shower. A very useful addition to an eyewash fountain is a face spray ring that sprays the face gently to remove contaminants.
Plant layout, Installation, and Maintenance Considerations for Safety Shower and Eyewash Station
- Safety shower & eyewash stations shall be designed as per ISEA/ANSI Z358.1. and they shall comply with minimum requirements as per DEP 80.47.10.32.
- The Safety Shower station shall be a foot-operated type and the eyewash station shall be hand operated type.
- Both Units should be fitted with appropriate lighting.
- An overhead tank that stores the flushing fluid should have a visual level indicator.
- The safety shower and eyewash skid shall be insulated to maintain the temperature of supplied potable water between 150 C and 360 C.
- Safety showers shall be provided in areas where flammable products are handled and personnel may be exposed to the product.
- Safety showers and eyewash stations shall be positioned not more than 15 m (50 ft) away from the potential hazard and be on the same grade level.
- An initial hazard assessment of where safety showers are required shall be made and documented.
- For cold climate locations, where the stagnant part of the safety shower water supply line could freeze and block the water supply to the outlet, these sections could be provided with heat tracing.
- Except for self-contained stand-alone systems, the overall design should allow for regular line flushing to prevent the build-up of bacteria.
- The water supply line should have no unnecessary valves that could accidentally be closed.
- If the supply pressure can fluctuate, the water supply to the eyewash shall be provided with a regulating valve.
- Effluent from the safety shower should be collected or contained for treatment.
- Materials of emergency showers shall be such that they will not corrode in the presence of the flushing fluid. Normally Stainless Steel is used with water as a flushing fluid.
- The equipment must withstand exposure to ambient airborne contaminants in the area of installation.
- Both types of equipment must be maintained to keep them in proper working condition. Equipment owners should be aware of the maintenance schedules found in the ANSI/ISEA Z358.1. standard.
- All equipment must be inspected annually to ensure the device conforms to installation requirements.
- The equipment must be on the same level the user is working on. If doors are provided in between the hazard and the fixture, they should swing in the direction of travel.
- The path to the station must not be obstructed by other hazards to make the path clear for the injured employee.
- The drench shower or eyewash should be placed immediately adjacent to the hazard when highly corrosive chemicals are used.
- If there are possibilities to affect multiple workers, fixtures with sufficient quantity should be installed to avoid one worker to wait 15 minutes while another is drenched.
- All fixtures should be identified with a highly visible sign (Fig. 3).
- Employees (workers) must be trained about the location and proper use of the shower and eyewash stations.
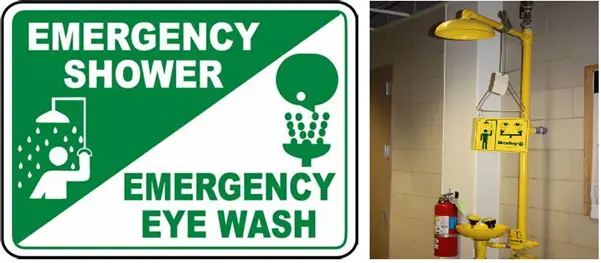
Data Required for Ordering Emergency Shower and Eye Wash Station
While creating the Material Requisition (MR) for Safety Shower & Eye Wash device, a datasheet needs to be prepared with the following data at a minimum:
- Unit Description: Separate safety shower and eyewash or combined modular unit.
- Design temperature and Pressure: Considering the ambient effect of the region.
- Service Fluid: Normally Potable Water
- Compatible Piping Specification: Normally SS pipe
- Design Standard: ISEA / ANSI Z358.1
- End connections: Mostly flanged
- Connected pipe size: Normally 2 inch
- Drain Outlet connection: Normally 2 inch
- Device Material: Mostly Stainless Steel
- Overhead tank capacity
- Any other consideration
Eye and Face Personal Protective Equipment
In general industry or Construction; almost in any work environment, chemical usage may occur. These chemicals can be in the form of hot or corrosive liquids, vapors, gases, and in some cases solids. Such chemicals normally cause physical or chemical burns to the eyes or skin, eye or skin irritation, and distraction or temporary blindness. Using Eye and Face Personal Protective Equipment can be an effective measure against such environments. Based on chemical types, the following types of Eye and Face Personal Protective Equipment can be used:
- For Highly corrosive or toxic by eye or skin absorption liquids, vapors, gases, or airborne particles: Ventilated acid fume hood, full face respirator, or special protective suits.
- For Hot, strongly irritative, and/or corrosive liquids, vapors, gases, or airborne particles: Chemical goggles and face shields or special chemical hoods.
- For Moderate irritants: Chemical goggles and face shield.
- For Slight irritants: Chemical goggles or face shields are used with safety glasses with side shields.
Few more Resources for you..
Piping Design and Layout
Piping Stress Analysis
Piping Materials
Articles related to Piping Interface Departments
Where are you getting so useful technical information daily ?? Really you are great… !!!