Floor gratings, commonly known as grates or grating panels, are versatile and essential components in many industrial, commercial, and even residential settings. These unassuming structures play a significant role in enhancing safety, improving efficiency, and adding a touch of aesthetic appeal to various environments. In this blog article, we will explore what floor gratings are, their diverse applications, the materials they are made from, and the advantages they offer.
What are Floor Gratings?
Floor gratings are rigid, open-mesh structures typically manufactured from metal, fiberglass, or plastic materials. They consist of a series of parallel bars or crossbars, forming a grid-like pattern, allowing air, light, and fluids to pass through while providing a sturdy walking surface.
Types of Floor Gratings
Welded Steel Gratings:
These gratings are made by welding steel bars together to create a durable and robust structure. They are commonly used in industrial settings, such as factories, manufacturing plants, and warehouses, due to their strength and load-bearing capabilities.
Press-Locked Gratings:
Press-locked gratings are manufactured by inserting crossbars into pre-punched holes of bearing bars and then permanently locking them in place. They are preferred for architectural applications, pedestrian walkways, and platforms.
Bar Gratings:
Bar gratings are constructed using individual bearing bars that are either flat or serrated. They are widely used in industrial environments, as well as outdoor settings, where drainage and slip resistance are crucial.
Fiberglass Gratings:
These gratings are composed of reinforced fiberglass plastic. They are corrosion-resistant and suitable for environments where chemical exposure is a concern, such as chemical plants and offshore platforms.
Plastic Gratings:
Plastic gratings are lightweight and corrosion-resistant. They find applications in food processing plants, marine settings, and other environments where metal may corrode or rust.
Applications of Floor Gratings
- Industrial Flooring: Floor gratings are extensively used in industries to create elevated walkways, platforms, and catwalks. They provide a safe surface for workers to navigate around heavy machinery and equipment.
- Drainage Systems: Gratings with gaps between bars allow liquids to pass through, making them ideal for drainage systems in areas prone to water accumulation, such as industrial kitchens, parking lots, and outdoor pathways.
- Fire Escapes: Fire escapes and emergency staircases often utilize floor gratings for their strength and durability. The open design allows debris and water to fall through, ensuring safe evacuation routes.
- Commercial Buildings: Many commercial buildings incorporate floor gratings in their designs to create stylish and functional entryways, lobby floors, and mezzanine levels.
- Transportation: In transportation settings, floor gratings are used in subway stations, train platforms, and airports to promote ventilation and drainage.
- Offshore and Marine: Fiberglass and plastic gratings are commonly used in offshore and marine environments due to their resistance to corrosion and chemicals.
Advantages of Floor Gratings
- Safety: Gratings provide slip-resistant surfaces, reducing the risk of accidents, especially in environments where liquids or debris are common.
- Durability: Steel and fiberglass gratings have excellent durability, withstanding heavy loads and harsh conditions for extended periods.
- Aesthetics: Gratings can add a touch of modernity and sophistication to architectural designs, making them popular in contemporary building projects.
- Ventilation and Drainage: The open-mesh design allows air and liquids to pass through, preventing water accumulation and promoting air circulation.
- Easy Maintenance: Floor gratings are relatively easy to clean and maintain, contributing to cost-effective solutions for various applications.
Materials for Floor Gratings
Floor gratings are available in various materials, each with its unique properties and advantages. The choice of material depends on the specific application and the environment in which the gratings will be used. Here are some common materials used for floor gratings:
Steel Floor Gratings:
Steel gratings are the most widely used type and are known for their exceptional strength and durability. They are often made from carbon steel, stainless steel, or galvanized steel. Carbon steel gratings are suitable for most industrial applications, while stainless steel gratings are preferred for environments where corrosion resistance is essential, such as chemical plants or coastal areas. Galvanized steel gratings have a protective zinc coating, providing resistance against corrosion and rust. Fig. 1 below shows a typical example of Steel Grating Floors.
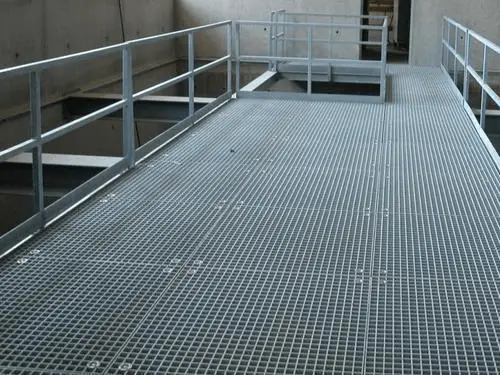
Aluminum Floor Gratings:
Aluminum gratings are lightweight and corrosion-resistant, making them an excellent choice for applications where weight reduction and resistance to atmospheric corrosion are essential. They are commonly used in pedestrian walkways, architectural projects, and transportation settings.
Fiberglass Floor Gratings:
Fiberglass gratings are composed of reinforced fiberglass plastic. They are highly corrosion-resistant, making them ideal for environments exposed to chemicals, moisture, and extreme temperatures. These gratings are commonly used in chemical plants, offshore platforms, and marine environments.
Plastics Grating Floor:
Plastic gratings, often made from materials like polypropylene (PP) or polyvinyl chloride (PVC), are lightweight, cost-effective, and resistant to chemicals. They find applications in food processing plants, swimming pool areas, and places where metal gratings may corrode.
Stainless Steel Mesh:
Stainless steel mesh gratings are composed of thin, interconnected wires, forming a mesh-like structure. They offer excellent corrosion resistance, making them suitable for marine and coastal environments, as well as architectural and decorative applications.
Galvanized Iron:
Galvanized iron gratings have a layer of zinc coating, providing moderate corrosion resistance. They are commonly used in areas where steel gratings might be prone to rust.
Brass Gratings:
Brass gratings are known for their aesthetic appeal, thanks to their golden color. They find applications in architectural projects where both functionality and visual appeal are essential.
Each material has its pros and cons, so it’s crucial to consider factors such as load-bearing capacity, corrosion resistance, cost, and aesthetic requirements when choosing the most suitable material for a specific floor grating application.
Steel Floor Gratings
Steel floor gratings are a type of floor grating made from steel, known for their robustness, durability, and versatility. They consist of a series of parallel steel bars or flat bars, connected together by perpendicular crossbars, forming a grid-like pattern. The design creates an open-mesh structure that allows for the passage of air, light, and fluids while providing a secure and slip-resistant walking surface.
Construction of Steel Floor Gratings:
- Bearing Bars: The bearing bars are the primary load-bearing elements of the grating and are usually flat or round bars. These bars are aligned parallel to one another and spaced at regular intervals to form the main walking surface of the grating.
- Crossbars: The crossbars, also known as cross-rods or transverse bars, are placed perpendicular to the bearing bars. They are attached to the bearing bars by welding, pressure-locking, or swage-locking to create a rigid and stable structure.
Load Carrying Capability of Steel Grating Floors
The load-carrying capability of steel grating floors varies depending on several factors, including the type of steel grating, its dimensions, the spacing of bearing bars and crossbars, and the material thickness. The load capacity is crucial to ensure the safety and structural integrity of the floor grating in various applications.
To determine the load-carrying capability of a steel grating floor, engineers consider two main factors:
- Uniform Load Capacity: This refers to the maximum distributed load that the entire surface of the grating can support without experiencing permanent deformation or failure. The uniform load capacity is typically expressed in pounds per square foot (PSF) or kilonewtons per square meter (kN/m²). The spacing between bearing bars and crossbars, as well as their dimensions and material properties, significantly influence this capacity.
- Concentrated Load Capacity: This refers to the maximum load that a small area of the grating can bear without causing permanent deformation or failure. Concentrated load capacity is crucial for assessing the ability of the grating to handle point loads or heavy equipment placed on specific locations.
To ensure safety, steel grating manufacturers and engineers adhere to industry standards and codes, such as ANSI/NAAMM MBG 531 or DIN 24537-1, which provide guidelines for calculating load capacities based on factors like grating type, bar dimensions, span, and material properties.
Keep in mind that different types of steel gratings, such as welded, press-locked, or swage-locked, may have varying load-carrying capabilities. Additionally, the material thickness and the size of the bearing and crossbars play a significant role in determining the load capacity of a specific steel grating floor.
When designing a steel grating floor for a specific application, engineers consider the intended usage, the type and weight of equipment or materials that will be placed on it, and any potential dynamic loads that may occur during the operation. This comprehensive analysis ensures that the chosen steel grating floor can safely support the intended loads and function effectively in its designated environment.
Advantages of Steel Floor Gratings:
Steel grating floors provide numerous advantages with respect to other materials. Some of these are
- High Strength: Steel floor gratings are renowned for their exceptional strength and load-bearing capacity, making them suitable for heavy machinery, industrial equipment, and vehicles.
- Durability: Steel is a durable material that can withstand harsh conditions, including high temperatures, chemicals, and extreme weather, without significant degradation.
- Slip Resistance: The open-mesh design of steel gratings provides excellent slip resistance, reducing the risk of accidents caused by wet or slippery conditions.
- Ventilation and Drainage: Steel gratings allow air, light, and fluids to pass through freely, ensuring proper ventilation and efficient drainage in various environments.
- Easy Maintenance: Steel gratings are relatively easy to clean and maintain, making them a cost-effective flooring solution in industrial and commercial settings.
- Customizable: Steel floor gratings are available in various sizes, configurations, and surface finishes, allowing for customization to suit specific application requirements.
In conclusion, steel floor gratings are a popular choice for industrial, commercial, and architectural applications due to their strength, durability, and versatility. Whether used in manufacturing plants, walkways, or fire escapes, these gratings provide a safe and functional surface while offering the benefits of ventilation and drainage.
Conclusion
Floor gratings are invaluable components in numerous industries and settings, providing safety, efficiency, and aesthetic benefits. From industrial flooring to architectural designs and drainage systems, their versatility makes them indispensable. Whether you’re looking to enhance safety, improve ventilation, or add a stylish element to a space, floor gratings offer an excellent solution. As technology advances, we may see even more innovative materials and designs that further improve the functionality and appeal of floor gratings in the years to come.