When it comes to transporting fluids, gases, and other materials, the choice of piping material plays a crucial role in ensuring efficiency, durability, and safety. There are two types of piping materials that are used for designing piping systems; metallic and non-metallic piping. Out of these, metallic piping stands out as a reliable and versatile choice and is widely used in various industries. In this article, we’ll dive into the world of metallic piping, exploring its types, advantages, applications, and considerations.
What is Metallic Piping?
Metallic piping refers to a system of pipes and tubes used to transport various fluids, gases, or materials within industrial, commercial, and residential settings. The term metallic means the pipes are made from metals. Metallic pipes are constructed from various metallic materials such as carbon steel, stainless steel, alloy steel, copper, brass, aluminum alloy, nickel alloys, and more, depending on the specific requirements of the application.
Metallic piping systems are designed to withstand a wide range of conditions, including high pressures, extreme temperatures, and corrosive environments. They are utilized in diverse industries such as oil and gas, chemical and petrochemical processing, power generation, construction, mining, food generation, shipbuilding, and many others.
The design and installation of metallic piping involve considerations such as material selection, pipe diameter, wall thickness, fittings, valves, supports, and insulation. Metallic Pipes play a critical role in ensuring the safe and efficient transportation of fluids while adhering to industry standards and regulations. Proper maintenance and inspection of metallic piping are essential to ensure the longevity and reliability of these systems over time.
Types of Metallic Piping
When it comes to metallic piping, there are several types of materials that are commonly used to meet different requirements based on factors like the fluid being transported, temperature and pressure, environmental conditions, and industry standards. Here are some of the most common types of metallic piping:
Carbon Steel Piping:
Carbon steel pipes are widely used due to their affordability and versatility. They are suitable for a range of applications including water, oil, and gas transportation. However, Carbon Steel pipes are susceptible to corrosion and may require protective coatings or linings. They are categorized into different grades and specifications based on their composition and properties. Here is a list of some common types of carbon steel pipe materials:
- ASTM A53 Grade A/B: Standard specification for seamless and welded black and hot-dipped galvanized steel pipes. Used for various applications including water, gas, and steam conveyance.
- ASTM A106 Grade A/B/C: Specification for seamless carbon steel pipe for high-temperature service. Used in power plants, refineries, and process industries where elevated temperatures and pressures are encountered.
- ASTM A333 Grade 6: Specification for seamless and welded steel pipe for low-temperature service. Suitable for applications in cryogenic conditions, such as liquefied natural gas (LNG) plants.
- API 5L Grade A/B/X42/X52/X60/X65/X70/X80: Specification for line pipe used in the transportation of oil, gas, and other fluids. Different grades correspond to varying levels of strength and durability.
- ASTM A53 Type F/E: Electric-resistance welded (ERW) and furnace-welded pipe. Commonly used in plumbing, water supply, and other non-critical applications.
- ASTM A795: Standard specification for black and hot-dipped zinc-coated (galvanized) welded and seamless steel pipe for fire protection use.
- ASTM A671/A672: Specification for electric-fusion-welded steel pipe for atmospheric and lower temperatures and pressure applications.
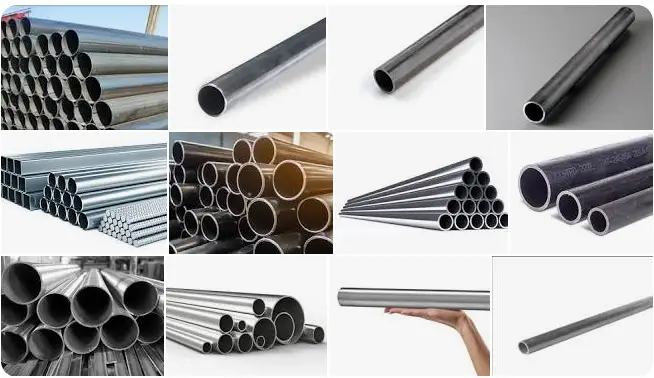
Stainless Steel Piping:
Stainless steel pipes are highly corrosion-resistant and come in various grades, each offering different levels of resistance to chemicals and extreme temperatures. They are commonly used in industries like food processing, pharmaceuticals, and petrochemicals. Here’s a list of common stainless steel pipe materials:
Austenitic Stainless Steels (Series 300):
- 304/304L (UNS S30400/S30403): A versatile and widely used stainless steel grade with good corrosion resistance and formability. Commonly used in a wide range of applications including plumbing, food processing, and architectural uses.
- 316/316L (UNS S31600/S31603): Contains molybdenum for improved corrosion resistance, particularly in chloride-rich environments. Commonly used in marine, chemical, and pharmaceutical industries.
Ferritic Stainless Steels (Series 400):
- 409 (UNS S40900): Offers good heat resistance and is commonly used in automotive exhaust systems and applications where high-temperature resistance is required.
- 430 (UNS S43000): Known for its corrosion resistance and formability, often used in decorative applications and automotive trims.
Martensitic Stainless Steels (Series 400):
- 410 (UNS S41000): Offers good strength and moderate corrosion resistance. Used in applications requiring hardness and wear resistance, such as cutlery, surgical instruments, and valves.
- 420 (UNS S42000): Known for its higher carbon content, it provides improved hardness and corrosion resistance compared to 410. Used in applications like surgical instruments and dental tools.
Precipitation Hardening Stainless Steels:
- 17-4 PH (UNS S17400): Offers a combination of high strength and good corrosion resistance. Commonly used in aerospace, chemical, and petrochemical industries.
Super Austenitic Stainless Steels:
- 254 SMO (UNS S31254): Offers excellent corrosion resistance in a wide range of environments, including seawater and acidic solutions. Used in chemical processing, desalination plants, and more.
Nitronic Stainless Steels:
- Nitronic 50 (UNS S20910): Known for its high strength and excellent corrosion resistance. Used in applications requiring wear resistance, such as pumps, valves, and marine equipment.
Alloy Steel Piping:
Alloy steel pipes are designed to handle high temperatures and pressures. They are used in industries such as power generation, where pipes need to withstand the conditions of steam and high-pressure gases.
Alloy steel pipes are used in various industries where enhanced strength, toughness, and resistance to wear and corrosion are required. These pipes are made from alloying elements such as chromium, molybdenum, nickel, and others, combined with carbon steel to achieve specific properties. Here’s a list of common alloy steel pipe materials:
Chromium-Molybdenum Alloys:
- A335 P5 (UNS K41545): Contains 5% chromium and 0.5% molybdenum, offering good high-temperature strength and corrosion resistance. Used in power generation and petroleum refining.
- A335 P9 (UNS S50400): Contains 9% chromium and 1% molybdenum, providing improved corrosion resistance and high-temperature strength. Used in power plants and chemical industries.
- A335 P11 (UNS K11597): Contains 1.25% chromium and 0.5% molybdenum, offering good creep and oxidation resistance at elevated temperatures. Used in power generation and petrochemical industries.
- A335 P22 (UNS K21590): Contains 2.25% chromium and 1% molybdenum, suitable for applications requiring increased resistance to corrosion and high-temperature strength.
Nickel-Chromium Alloys:
- A335 P91 (UNS K91560): Contains 9% chromium and 1% molybdenum, with the addition of 1.85% nickel and 0.25% vanadium. Offers excellent high-temperature strength and creep resistance. Used in power plants and refineries.
Low Alloy Steels:
- A333 Gr. 3/6 (UNS K03003/K03006): Contains low levels of alloying elements for improved low-temperature toughness. Used in low-temperature applications such as cryogenic industries.
- A335 P2 (UNS K11547): Contains 0.5% molybdenum and 0.5% chromium. Offers good strength and creep resistance at elevated temperatures.
High-Strength Low-Alloy (HSLA) Steels:
- A335 P5c (UNS K41245): A modified P5 alloy with reduced carbon content, offering improved weldability and thermal stability.
Other Alloy Steel Grades:
- A335 P15 (UNS K11578): Contains 9% chromium and 1% molybdenum, with the addition of 3% vanadium. Used in high-temperature applications.
- A213 T91 (UNS S62900): A variant of P91 alloy used in seamless tubes for high-temperature applications.
- A213 T92 (UNS K92460): Contains 9% chromium, 1.9% molybdenum, and 0.7% vanadium. Offers excellent creep and thermal fatigue resistance.
Copper Piping:
Copper pipes are known for their excellent thermal conductivity and corrosion resistance. They are often used in plumbing systems for residential and commercial buildings, as well as in HVAC systems. Here’s a list of common copper alloy pipe materials:
Copper-Nickel Alloys:
- C70600 (90/10 Copper-Nickel): Contains approximately 90% copper and 10% nickel. Offers excellent resistance to seawater corrosion and is used in marine and offshore applications.
- C71500 (70/30 Copper-Nickel): Contains approximately 70% copper and 30% nickel. Provides a balance of corrosion resistance and strength, used in heat exchangers, condensers, and seawater systems.
Bronze Alloys:
- C51000 (Phosphor Bronze): Contains approximately 94% copper, 6% tin, and a small amount of phosphorus. Offers excellent corrosion resistance and is used in electrical connectors and springs.
- C61400 (Aluminum Bronze): Contains approximately 81% copper, 9% aluminum, 4% iron, and 4% nickel. Offers high strength and corrosion resistance, used in marine applications.
Copper-Silicon Alloys:
- C65100 (Low-Silicon Bronze): Contains approximately 98.5% copper and 1.5% silicon. Used in applications requiring good electrical conductivity and resistance to corrosion.
Copper-Iron Alloys:
- C70620 (90/10 Copper-Iron): Contains approximately 90% copper and 10% iron. Offers good corrosion resistance and is used in heat exchangers and condensers.
Nickel-Silver Alloys:
- C73500 (Nickel Silver): Contains copper, nickel, and zinc. Offers a silvery appearance and is used in musical instruments, decorative items, and jewelry.
Brass Piping:
Brass pipes are a combination of copper and zinc, offering good corrosion resistance and aesthetic appeal. They are commonly used in plumbing, industrial applications, and decorative purposes.
Brass Alloys:
- C26000 (Cartridge Brass): Contains approximately 70% copper and 30% zinc. Offers good corrosion resistance and is commonly used in plumbing and decorative applications.
- C36000 (Free-Cutting Brass): Contains approximately 60% copper and 40% zinc, with a small percentage of lead for improved machinability. Used in fittings and fasteners.
Nickel Alloy Piping:
Nickel alloys are known for their exceptional resistance to corrosion, high temperatures, and harsh chemicals. They are often used in industries such as chemical processing, petrochemicals, oil and gas, aerospace, and many more.
Here’s a list of common nickel alloy pipe materials:
Inconel Alloys:
- Inconel 600 (UNS N06600): Offers good resistance to high-temperature oxidation and corrosion. Used in heat exchangers, furnace components, and chemical processing.
- Inconel 625 (UNS N06625): Provides excellent resistance to a wide range of corrosive environments, including seawater and acidic solutions. Used in marine, aerospace, and chemical industries.
- Inconel 718 (UNS N07718): Known for its high-temperature strength and corrosion resistance. Used in aerospace, oil and gas, and turbine components.
Hastelloy Alloys:
- Hastelloy C276 (UNS N10276): Offers exceptional resistance to a wide range of corrosive environments, including strong acids and chlorides. Used in chemical processing, pollution control, and pulp and paper industries.
- Hastelloy C22 (UNS N06022): Provides excellent corrosion resistance in oxidizing and reducing environments. Used in petrochemical, chemical, and pharmaceutical industries.
Monel Alloys:
- Monel 400 (UNS N04400): Known for its excellent corrosion resistance in seawater and other aggressive environments. Used in marine applications, chemical processing, and aerospace.
- Monel K500 (UNS N05500): Offers higher strength and hardness compared to Monel 400. Used in oil and gas, marine engineering, and electronic components.
- Alloy 20 (UNS N08020): Provides good resistance to sulfuric acid and other corrosive chemicals. Used in chemical and pharmaceutical industries.
- Nickel 200/201 (UNS N02200/N02201): Offers good corrosion resistance and electrical conductivity. Used in chemical processing, electronics, and aerospace.
Nimonic Alloys:
- Nimonic 75 (UNS N06075): Known for its high-temperature strength and creep resistance. Used in gas turbine components and aerospace applications.
- Nimonic 80A (UNS N07080): Offers excellent mechanical properties at high temperatures. Used in aircraft engine components and industrial furnace applications.
- Alloy X (UNS N06002): Offers high-temperature strength and oxidation resistance. Used in gas turbine components and petrochemical applications.
Haynes Alloys:
- Haynes 230 (UNS N06230): Known for its excellent thermal stability and oxidation resistance. Used in high-temperature applications, including gas turbine components.
- Haynes 625 (UNS N06625): Provides high strength and corrosion resistance at elevated temperatures. Used in aerospace, chemical processing, and marine applications.
Incoloy Alloys:
- Incoloy 800/800H/800HT (UNS N08800/N08810/N08811): Offers good corrosion resistance and high-temperature strength. Used in heat exchangers, furnace components, and power plants.
- Incoloy 825 (UNS N08825): Provides excellent resistance to corrosive environments, particularly sulfuric and phosphoric acids. Used in chemical processing, pollution control, and marine applications.
Titanium Piping:
Titanium pipes are lightweight, strong, and highly resistant to corrosion, especially in aggressive environments. They find applications in industries like chemical processing, desalination plants, and marine engineering.
Titanium Alloys:
Though not purely nickel alloys, some titanium-nickel alloys, like Ti-6Al-4V, offer good corrosion resistance and are used in aerospace and medical applications.
Duplex and Super Duplex Stainless Steel Piping:
These are specialized stainless steel alloys with a combination of high strength and excellent corrosion resistance. They are used in industries where resistance to chloride-induced stress corrosion cracking is crucial, such as offshore and marine applications.
Duplex Stainless Steels (Series 200 and 300):
- 2205 (UNS S32205/S31803): A duplex stainless steel with high corrosion resistance and good mechanical properties. Commonly used in chemical processing, oil and gas, and marine applications.
- 2507 (UNS S32750): Offers even higher corrosion resistance than 2205 and is used in aggressive environments, such as offshore and seawater applications.
Super Duplex Stainless Steels:
- Zeron 100 (UNS S32760): Offers exceptional corrosion resistance and high strength, making it suitable for demanding applications in chemical, petrochemical, and marine industries.
Monel Piping:
Monel is a nickel-copper alloy that is resistant to corrosion by many agents, including seawater, acids, and alkalies. It’s commonly used in applications involving marine and chemical environments.
Inconel and Incoloy Piping:
These are high-performance nickel-chromium alloys with exceptional resistance to oxidation, corrosion, and high temperatures. They are utilized in industries such as aerospace, chemical processing, and gas turbine components.
Hastelloy Piping:
Hastelloy alloys are known for their excellent resistance to a wide range of aggressive chemicals. They are used in applications involving strong acids, chlorine, and other corrosive environments.
Zirconium Piping:
Zirconium pipes are highly resistant to corrosion, even in hot, acidic, and alkaline environments. They are used in industries like nuclear power, chemical processing, and aerospace.
Aluminum Alloy Piping
Aluminum alloy pipes are chosen for their lightweight nature, excellent corrosion resistance, and versatility. These alloys are used in various industries, including aerospace, automotive, construction, and more. Here’s a list of common aluminum alloy pipe materials:
- 6061 Aluminum Alloy: This is one of the most commonly used aluminum alloys. It offers good strength and corrosion resistance, making it suitable for structural applications, such as in aerospace, automotive components, and marine equipment.
- 6063 Aluminum Alloy: Known for its excellent extrudability, 6063 is often used for architectural and decorative applications, as well as in the construction of doors and windows.
- 7075 Aluminum Alloy: Recognized for its high strength-to-weight ratio, 7075 is used in applications requiring strong structural components, such as aircraft frames, bike frames, and high-performance equipment.
- 2024 Aluminum Alloy: Offering good machinability and high strength, 2024 is often used in aerospace applications, including aircraft structures and components.
- 5083 Aluminum Alloy: Known for its exceptional resistance to seawater corrosion, 5083 is used in marine applications, such as boat hulls and components.
- 5086 Aluminum Alloy: Similar to 5083, 5086 is also used in marine applications, offering good corrosion resistance and weldability.
- 3003 Aluminum Alloy: Offering moderate strength and good formability, 3003 is often used in various general-purpose applications, including pipes for HVAC systems.
- 3004 Aluminum Alloy: Known for its high strength and good formability, 3004 is used in applications requiring higher structural integrity, such as pressure vessels and storage tanks.
- 2014 Aluminum Alloy: With excellent machinability, 2014 is often used in applications requiring intricate shapes and forms, such as structural components and parts requiring high precision.
- 7005 Aluminum Alloy: Offering high strength and good corrosion resistance, 7005 is used in bicycle frames, sporting goods, and other high-stress applications.
- 5754 Aluminum Alloy: Known for its excellent corrosion resistance, 5754 is used in marine and automotive applications.
- 6013 Aluminum Alloy: Offering improved strength and formability, 6013 is used in automotive structural components and other applications requiring lightweight solutions.
Cast Iron Piping
Cast iron pipes have been historically used for their durability and strength in various applications, particularly in plumbing and sewage systems. Different types of cast iron pipes are used based on their composition and intended use. Here’s a list of common cast iron pipe materials:
- Gray Cast Iron Pipes: Gray cast iron pipes are widely used for water supply and sewage systems due to their corrosion resistance and good mechanical properties. They have a gray appearance due to the graphite flakes in their microstructure.
- Ductile Iron Pipes (Nodular Cast Iron): Also known as nodular cast iron or spheroidal graphite iron, ductile iron pipes are more flexible and have higher tensile strength compared to traditional gray cast iron pipes. They are used in water distribution, wastewater, and stormwater systems.
- Cast Iron Soil Pipes (CISP): Cast iron soil pipes are used for drainage, waste, and vent systems in buildings. They have a higher wall thickness compared to water distribution pipes to handle higher pressures and support building loads.
- Cast Iron Pressure Pipes: These pipes are used for high-pressure water supply systems and are designed to withstand the internal pressure caused by the water flow. They are often used in municipal water distribution networks.
- Cast Iron Culvert Pipes: Culvert pipes are used for road and highway drainage, allowing water to flow underneath roadways. Cast iron culvert pipes provide structural integrity and durability for these applications.
- Cast Iron Specialties: Apart from pipes, cast iron is also used to produce various specialty items such as fittings, couplings, valves, and other components used in plumbing and drainage systems.
List of ASTM Metallic Pipes and Bolting Materials as per ASME B31.3
ASME B31.3 provides a comprehensive list of all ASTM metallic pipe materials. The ASTM Metallic Pipe and Bolting Material list is Produced below in Table 1 and Table 2. Table 1 provides the ASTM designation for Ferrous Pipe Materials, whereas Table 2 provides the ASTM designation for Non-ferrous Metallic Pipe Materials.
ASTM Designation | Title |
A36 | Carbon Structural Steel |
A47 | Ferritic Malleable Iron Castings |
A48 | Gray Iron Castings |
A53 | Pipe, Steel, Black and Hot-Dipped, Zinc-Coated, Welded and Seamless |
A105 | Carbon Steel Forgings for Piping Applications |
A106 | Seamless Carbon Steel Pipe for High-Temperature Service |
A126 | Gray Iron Castings for Valves, Flanges, and Pipe Fittings |
A134 | Pipe, Steel, Electric-Fusion (Arc)-Welded (Sizes NPS 16 and Over) |
A135 | Electric-Resistance-Welded Steel Pipe |
A139 | Electric-Fusion (Arc)-Welded Steel Pipe (NPS 4 and Over) |
A179 | Seamless Cold-Drawn Low-Carbon Steel HeatExchanger and Condenser Tubes |
A181 | Carbon Steel Forgings, for General-Purpose Piping |
A182 | Forged or Rolled Alloy and Stainless Steel Pipe Flanges, Forged Fittings, and Valves and Parts for High-Temperature Service |
A193 | Alloy-Steel and Stainless Steel Bolting for High Temperature or High-Pressure Service and Other Special Purpose Applications |
A194 | Carbon Steel, Alloy Steel, and Stainless Steel Nuts for Bolts for High Pressure or High-Temperature Service, or Both |
A197 | Cupola Malleable Iron |
A203 | Pressure Vessel Plates, Alloy Steel, Nickel |
A204 | Pressure Vessel Plates, Alloy Steel, Molybdenum |
A213 | Seamless Ferritic and Austenitic Alloy-Steel Boiler, Superheater, and Heat-Exchanger Tubes |
A216 | Steel Castings, Carbon, Suitable for Fusion Welding, for High-Temperature Service |
A217 | Steel Castings, Martensitic Stainless, and Alloy, for Pressure-Containing Parts, Suitable for HighTemperature Service |
A234 | Piping Fittings of Wrought Carbon Steel and Alloy Steel for Moderate and High-Temperature Service |
A240 | Chromium and Chromium-Nickel Stainless Steel Plate, Sheet, and Strip for Pressure Vessels and for General Applications |
A268 | Seamless and Welded Ferritic and Martensitic Stainless Steel Tubing for General Service |
A269 | Seamless and Welded Austenitic Stainless Steel Tubing for General Service |
A270 | Seamless and Welded Austenitic and Ferritic/Austenitic Stainless Steel Sanitary Tubing |
A276 | Stainless Steel Bars and Shapes |
A278 | Gray Iron Castings for Pressure-Containing Parts for Temperatures Up to 650°F (350°C) |
A283 | Low and Intermediate Tensile Strength Carbon Steel Plates |
A285 | Pressure Vessel Plates, Carbon Steel, Low- and Intermediate-Tensile Strength |
A299 | Pressure Vessel Plates, Carbon Steel, Manganese-Silicon |
A302 | Pressure Vessel Plates, Alloy Steel, Manganese-Molybdenum and Manganese-Molybdenum-Nickel |
A307 | Carbon Steel Bolts and Studs, 60,000 PSI Tensile Strength |
A312 | Seamless, Welded, and Heavily Cold-Worked Austenitic Stainless Steel Pipes |
A320 | Alloy-Steel and Stainless Steel Bolting for Low-Temperature Service |
A333 | Seamless and Welded Steel Pipe for Low-Temperature Service and Other Applications with Required Notch Toughness |
A334 | Seamless and Welded Carbon and Alloy-Steel Tubes for Low-Temperature Service |
A335 | Seamless Ferritic Alloy-Steel Pipe for High-Temperature Service |
A350 | Carbon and Low-Alloy Steel Forgings, Requiring Notch Toughness Testing for Piping Components |
A351 | Castings, Austenitic, for Pressure-Containing Parts |
A352 | Steel Castings, Ferritic, and Martensitic, for Pressure-Containing Parts, Suitable for Low-Temperature Service |
A353 | Pressure Vessel Plates, Alloy Steel, Double-Normalized and Tempered 9% Nickel |
A354 | Quenched and Tempered Alloy Steel Bolts, Studs, and Other Externally Threaded Fasteners |
A358 | Electric-Fusion-Welded Austenitic Chromium-Nickel Stainless Steel Pipe for High-Temperature Service and General Applications |
A369 | Carbon and Ferritic Alloy Steel Forged and Bored Pipe for High-Temperature Service |
A376 | Seamless Austenitic Steel Pipe for High-Temperature Service |
A381 | Metal-Arc-Welded Carbon or High-Strength Low-Alloy Steel Pipe for Use With High-Pressure Transmission Systems |
A387 | Pressure Vessel Plates, Alloy Steel, Chromium-Molybdenum |
A395 | Ferri tic Ductile Iron Pressure-Retaining Castings for Use at Elevated Temperatures |
A403 | Wrought Austenitic Stainless Steel Piping Fittings |
A409 | Welded Large Diameter Austenitic Steel Pipe for Corrosive or High-Temperature Service |
A420 | Piping Fittings of Wrought Carbon Steel and Alloy Steel for Low-Temperature Service |
A426 | Centrifugally Cast Ferritic Alloy Steel Pipe for High-Temperature Service |
A437 | Stainless and Alloy-Steel Turbine-Type Bolting Material Specially Heat Treated for High-Temperature Service |
A451 | Centrifugally Cast Austenitic Steel Pipe for High-Temperature Service |
A453 | High-Temperature Bolting, with Expansion Coefficients Comparable to Austenitic Stainless Steels |
A479 | Stainless Steel Bars and Shapes for Use in Boilers and Other Pressure Vessels |
A487 | Steel Castings Suitable for Pressure Service |
A494 | Castings, Nickel and Nickel Alloy |
A515 | Pressure Vessel Plates, Carbon Steel, for Intermediate- and Higher-Temperature Service |
A516 | Pressure Vessel Plates, Carbon Steel, for Moderate- and Lower-Temperature Service |
A524 | Seamless Carbon Steel Pipe for Atmospheric and Lower Temperatures |
A536 | Ductile Iron Castings |
A537 | Pressure Vessel Plates, Heat-Treated, Carbon-Manganese-Silicon Steel |
A553 | Pressure Vessel Plates, Alloy Steel, Quenched and Tempered 7, 8, and 9% Nickel |
A563 | Carbon and Alloy Steel Nuts |
A571 | Austenitic Ductile Iron Castings for Pressure-Containing Parts Suitable for Low-Temperature Service |
A587 | Electric-Resistance-Welded Low-Carbon Steel Pipe for the Chemical Industry |
A645 | Pressure Vessel Plates, 5% and 5 1/2% Nickel Alloy Steels, Specially Heat Treated |
A671 | Electric-Fusion-Welded Steel Pipe for Atmospheric and Lower Temperatures |
A672 | Electric-Fusion-Welded Steel Pipe for High-Pressure Service at Moderate Temperatures |
A675 | Steel Bars, Carbon, Hot-Wrought, Special Quality, Mechanical Properties |
A691 | Carbon and Alloy Steel Pipe, Electric-Fusion-Welded for High-Pressure Service at High Temperatures |
A694 | Carbon and Alloy Steel Forgings for Pipe Flanges, Fittings, Valves, and Parts for High-Pressure Transmission Service |
A696 | Steel Bars, Carbon, Hot-Wrought or Cold-Finished, Special Quality, for Pressure Piping Components |
A707 | Forged Carbon and Alloy Steel Flanges for Low-Temperature Service |
A789 | Seamless and Welded Ferritic/Austenitic Stainless Steel Tubing for General Service |
A790 | Seamless and Welded Ferritic/Austenitic Stainless Steel Pipe |
A813 | Single- or Double-Welded Austenitic Stainless Steel Pipe |
A814 | Cold-Worked Welded Austenitic Stainless Steel Pipe |
A815 | Wrought Ferritic, Ferritic/Austenitic, and Martensitic Stainless Steel Piping Fittings |
A860 | Wrought High-Strength Ferritic Steel Butt-Welding Fittings |
A928 | Ferritic/Austenitic (Duplex) Stainless Steel Pipe Electric Fusion Welded with Addition of Filler Metal |
A992 | Structural Steel Shapes |
A995 | Castings, Austenitic-Ferritic (Duplex) Stainless Steel, for Pressure-Containing Parts |
A1010 | Higher-Strength Martensitic Stainless Steel Plate, Sheet, and Strip |
A1011 | Steel, Sheet and Strip, Hot-Rolled, Carbon, Structural, High-Strength Low-Alloy, High-Strength Low-Alloy with Improved Formability, and Ultra-High Strength |
A1053 | Welded Ferritic-Martensitic Stainless Steel Pipe |
F3125 | High Strength Structural Bolts, Steel and Alloy Steel, Heat Treated, 120 ksi (830 MPa) and 150 ksi (1040 MPa) Minimum Tensile Strength |
ASTM Designation | Title |
B21 | Naval Brass Rod, Bar, and Shapes |
B26 | Aluminum-Alloy Sand Castings |
B42 | Seamless Copper Pipe, Standard Sizes |
B43 | Seamless Red Brass Pipe, Standard Sizes |
B61 | Steam or Valve Bronze Castings |
B62 | Composition Bronze or Ounce Metal Castings |
B68 | Seamless Copper Tube, Bright Annealed |
B75 | Seamless Copper Tube |
B88 | Seamless Copper Water Tube |
B96 | Copper-Silicon Alloy Plate, Sheet, Strip, and Rolled Bar for General Purposes and Pressure Vessels |
B98 | Copper-Silicon Alloy Rod, Bar, and Shapes |
B127 | Nickel-Copper Alloy (UNS N04400) Plate, Sheet, and Strip |
B148 | Aluminum-Bronze Sand Castings |
B150 | Aluminum Bronze Rod, Bar, and Shapes |
B152 | Copper Sheet, Strip, Plate, and Rolled Bar |
B160 | Nickel Rod and Bar |
B161 | Nickel Seamless Pipe and Tube |
B162 | Nickel Plate, Sheet, and Strip |
B163 | Seamless Nickel and Nickel Alloy Condenser and Heat Exchanger Tubes |
B164 | Nickel-Copper Alloy Rod, Bar, and Wire |
B165 | Nickel-Copper Alloy (UNS N04400) Seamless Pipe and Tube |
B166 | Nickel-Chromium-Aluminum Alloy, Nickel-Chromium-Iron Alloys, Nickel-Chromium-Cobalt-Molybdenum Alloy, Nickel-Iron-Chromium-Tungsten Alloy, and Nickel-Chromium-Molybdenum-Copper Alloy Rod, Bar, and Wire |
B167 | Nickel-Chromium-Iron Alloys (UNS N06600, N06601, N06603, N06690, N06693, N06025, N06045, and N06696), Nickel-Chromium-Cobalt-Molybdenum Alloy (UNS N06617), and Nickel-Iron-Chromium-Tungsten Alloy (UNS N06674) Seamless Pipe and Tube |
B168 | Nickel-Chromium-Iron Alloys (UNS N06600, N06601, N06603, N06690, N06693, N06025, N06045, and N06696), Nickel-Chromium-Cobalt-Molybdenum Alloy (UNS N06617), and Nickel-Iron-Chromium-Tungsten Alloy (UNS N06674) Plate, Sheet and Strip |
B169 | Aluminum Bronze Sheet, Strip, and Rolled Bar |
B171 | Copper-Alloy Plate and Sheet for Pressure Vessels, Condensers, and Heat Exchangers |
B187 | Copper, Bus Bar, Rod, and Shapes and General Purpose Rod, Bar, and Shapes |
B209 | Aluminum and Aluminum-Alloy Sheet and Plate |
B210 | Aluminum and Aluminum-Alloy Drawn Seamless Tubes |
B211 | Aluminum and Aluminum-Alloy Rolled or Cold Finished Bar, Rod, and Wire |
B221 | Aluminum and Aluminum-Alloy Extruded Bars, Rods, Wire, Profiles, and Tubes |
B241 | Aluminum and Aluminum-Alloy Seamless Pipe and Seamless Extruded Tube |
B247 | Aluminum and Aluminum-Alloy Die Forgings, Hand Forgings, and Rolled Ring Forgings |
B265 | Titanium and Titanium Alloy Strip, Sheet, and Plate |
B280 | Seamless Copper Tube for Air Conditioning and Refrigeration Field Service |
B283 | Copper and Copper-Alloy Die Forgings (Hot-Pressed) |
B333 | Nickel-Molybdenum Alloy Plate, Sheet, and Strip |
B335 | Nickel-Molybdenum Alloy Rod |
B345 | Aluminum and Aluminum-Alloy Seamless Pipe and Seamless Extruded Tube for Gas and Oil Transmission and Distribution Piping Systems |
B348 | Titanium and Titanium Alloy Bars and Billets |
B361 | Factory-Made Wrought Aluminum and Aluminum-Alloy Welding Fittings |
B363 | Seamless and Welded Unalloyed Titanium and Titanium Alloy Welding Fittings |
B366 | Factory-Made Wrought Nickel and Nickel Alloy Fittings |
B367 | Titanium and Titanium Alloy Castings |
B371 | Copper-Zinc-Silicon Alloy Rod |
B381 | Titanium and Titanium Alloy Forgings |
B407 | Nickel-Iron-Chromium Alloy Seamless Pipe and Tube |
B408 | Nickel-Iron-Chromium Alloy Rod and Bar |
B409 | Nickel-Iron-Chromium Alloy Plate, Sheet, and Strip |
B423 | Nickel-Iron-Chromium-Molybdenum-Copper Alloy Rod (UNS N08825, N08221, and N06845) Seamless Pipe and Tube |
B424 | Nickel-Iron-Chromium-Molybdenum-Copper Alloy Plate, Sheet, and Strip |
B425 | Ni-Fe-Cr-Mo-Cu Alloy (UNS N08825, UNS N08221, and UNS N06845) Rod and Bar |
B435 | UNS N06002, UNS N06230, UNS N12160, and UNS R30556 Plate, Sheet, and Strip |
B443 | Nickel-Chromium-Molybdenum-Columbium Alloy (UNS N06625) and Nickel-Chromium-Molybdenum-Silicon Alloy (UNS N06219) Plate, Sheet, and Strip |
B444 | Nickel-Chromium-Molybdenum-Columbium Alloys (UNS N06625 and UNS N06852) and Nickel-Chromium-Molybdenum-Silicon Alloy (UNS N06219) Pipe and Tube |
B446 | Nickel-Chromium-Molybdenum-Columbium Alloy (UNS N06625), Nickel-Chromium-Molybdenum-Silicon Alloy (UNS N06219), and Nickel-Chromium-Molybdenum-Tungsten Alloy (UNS N06650) Rod and Bar |
B462 | Forged or Rolled Nickel Alloy Pipe Flanges, Forged Fittings, and Valves and Parts for Corrosive High-Temperature Service |
B463 | UNS N08020 Alloy Plate, Sheet, and Strip |
B464 | Welded UNS N08020 Alloy Pipe |
B466 | Seamless Copper-Nickel Pipe and Tube |
B467 | Welded Copper-Nickel Pipe |
B474 | Electric Fusion Welded Nickel and Nickel Alloy Pipe |
B491 | Aluminum and Aluminum-Alloy Extruded Round Tubes for General-Purpose Applications |
B493 | Zirconium and Zirconium Alloy Forgings |
B514 | Welded Nickel-Iron-Chromium Alloy Pipe |
B515 | Welded UNS N08120, UNS N08800, UNS N08810, and UNS N08811 Alloy Tubes |
B517 | Welded Nickel-Chromium-Iron-Alloy (UNS N06600, UNS N06603, UNS N06025, and UNS N06045) Pipe |
B523 | Seamless and Welded Zirconium and Zirconium Alloy Tubes |
B550 | Zirconium and Zirconium Alloy Bar and Wire |
B551 | Zirconium and Zirconium Alloy Strip, Sheet, and Plate |
B564 | Nickel Alloy Forgings |
B572 | UNS N06002, UNS N06230, UNS N12160, and UNS R30556 Rod |
B574 | Low-Carbon Nickel-Chromium-Molybdenum, Low-Carbon Nickel-Molybdenum-Chromium, Low-Carbon Nickel-Molybdenum-Chromium-Tantalum, Low-Carbon Nickel-Chromium-Molybdenum-Copper, and Low-Carbon Nickel-Chromium-Molybdenum-Tungsten Alloy Rod |
B575 | Low-Carbon Nickel-Chromium-Molybdenum, Low-Carbon Nickel-Chromium-Molybdenum-Copper, Low-Carbon Nickel-Chromium-Molybdenum-Tantalum, Low-Carbon Nickel-Chromium-Molybdenum-Tungsten, and Low-Carbon Nickel-Molybdenum-Chromium Alloy Plate, Sheet and Strip |
B581 | Nickel-Chromium-Iron-Molybdenum-Copper Alloy Rod |
B582 | Nickel-Chromium-Iron-Molybdenum-Copper Alloy Plate, Sheet, and Strip |
B584 | Copper Alloy Sand Castings for General Applications |
B619 | Welded Nickel and Nickel-Cobalt Alloy Pipe |
B620 | Nickel-Iron-Chromium-Molybdenum Alloy (UNS N08320) Plate, Sheet, and Strip |
B621 | Nickel-Iron-Chromium-Molybdenum Alloy (UNS N08320) Rod |
B622 | Seamless Nickel and Nickel-Cobalt Alloy Pipe and Tube |
B625 | UNS N08925, UNS N08031, UNS N08932, UNS N08926, UNS N08354, UNS N08830, and UNS R20033 Plate, Sheet, and Strip |
B626 | Welded Nickel and Nickel-Cobalt Alloy Tube |
B649 | Ni-Fe-Cr-Mo-Cu-N Low-Carbon Alloys (UNS N08925, UNS N08031, UNS N08034, UNS N08354, and UNS N08926), and Cr-Ni-Fe-N Low-Carbon Alloy (UNS R20033) Bar and Wire,and Ni-Cr-Fe-Mo-N Alloy (UNS N08936) Wire |
B658 | Seamless and Welded Zirconium and Zirconium Alloy Pipe |
B668 | UNS N08028 Seamless Pipe and Tube |
B675 | UNS N08367 Welded Pipe |
B688 | Chromium-Nickel-Molybdenum-Iron (UNS N08367) Plate, Sheet, and Strip |
B690 | Iron-Nickel-Chromium-Molybdenum Alloy (UNS N08367) Seamless Pipe and Tube |
B704 | Welded UNS N06625, UNS N06219 and UNS N08825 Alloy Tubes |
B705 | Nickel-Alloy (UNS N06625, N06219 and N08825) Welded Pipe |
B709 | Iron-Nickel-Chromium-Molybdenum Alloy (UNS N08028) Plate, Sheet, and Strip |
B725 | Welded Nickel (UNS N02200/UNS N02201) and Nickel Copper Alloy (UNS N04400) Pipe |
B729 | Seamless UNS N08020, UNS N08026, and UNS N08024 Nickel-Alloy Pipe and Tube |
B804 | UNS N08367 and UNS N08926 Welded Pipe |
B861 | Titanium and Titanium Alloy Seamless Pipe |
B862 | Titanium and Titanium Alloy Welded Pipe |
E112 | Standard Test Methods for Determining Average Grain Size |
Advantages of Metallic Piping
- Strength and Durability: Metallic piping is renowned for its exceptional strength and durability. It can withstand high pressures, extreme temperatures, and even harsh environmental conditions. This makes it an ideal choice for industrial applications where reliability is paramount.
- Resistance to Corrosion: Many metallic materials used in piping, such as stainless steel and certain alloys, exhibit excellent resistance to corrosion. This characteristic extends the lifespan of the piping, reduces maintenance needs, and ensures the purity of transported fluids.
- Wide Temperature Range: Metallic piping maintains its structural integrity across a broad range of temperatures. This is particularly advantageous for industries that deal with both cryogenic substances and high-temperature processes.
- Fire Resistance: In applications where fire safety is critical, metallic piping is preferred due to its inherent fire-resistant properties. It doesn’t contribute to the spread of flames, making it suitable for environments with elevated fire risk.
- Low Thermal Expansion: Metallic pipes have relatively low coefficients of thermal expansion compared to other materials like plastics. This characteristic reduces the risk of leaks and ensures consistent performance in fluctuating temperatures.
Applications of Metallic Piping
- Oil and Gas Industry: Metallic piping plays a pivotal role in the oil and gas sector, where it is used to transport crude oil, natural gas, and refined products. The industry’s demanding conditions require piping that can withstand high pressures, corrosive substances, and extreme temperatures.
- Chemical Processing: Chemical plants require piping that can handle a diverse range of corrosive chemicals and fluids. Metallic piping, especially those made from corrosion-resistant alloys, provides the necessary durability and safety for such applications.
- Power Generation: Metallic piping is crucial in power generation facilities, including nuclear, coal, gas, and renewable energy plants. These pipes transport steam, water, and other fluids to power turbines and other equipment, often under high pressures and temperatures.
- Construction and Infrastructure: Metallic piping is used in plumbing systems, HVAC (heating, ventilation, and air conditioning) systems, and fire suppression systems within residential, commercial, and industrial buildings. Its durability and fire-resistant properties make it a reliable choice for these applications.
- Mining Industry: In mining operations, metallic piping is employed to transport various materials, including slurry, tailings, and processing fluids. Its robustness and resistance to abrasion suit the challenging conditions of the mining environment.
Considerations and Maintenance
While metallic piping offers numerous advantages, there are a few considerations to keep in mind:
- Cost: Metallic piping can be costlier to install than some alternatives, particularly plastics. However, its longevity and reliability often justify the initial investment.
- Corrosion Prevention: While metallic pipes are generally corrosion-resistant, the selection of the right alloy and the implementation of proper coatings or linings can further enhance their lifespan.
- Inspection and Maintenance: Regular inspection and maintenance are essential to ensure the continued performance of metallic piping systems. This includes monitoring for signs of corrosion, leakage, and structural integrity.
Conclusion
Metallic piping continues to be a foundational component in various industries due to its strength, durability, and versatility. From oil and gas to chemical processing and power generation, its applications are vast and essential. When choosing piping materials, considering the specific requirements of the application, the potential challenges, and the long-term benefits can help industries harness the advantages of metallic piping for safe and efficient material transport systems.