Pipe straps are essential components that ensure the stability and reliability of piping installations. These simple but effective piping elements are widely used in the world of plumbing and piping systems. This article will explore the myriad aspects of pipe straps, exploring their design, engineering, materials, and applications, while also touching on best practices for installation and maintenance.
What Are Pipe Straps?
Pipe straps are mechanical components used to secure and support piping systems. They are typically made from metal or durable plastic and are designed to hold pipes in place, preventing movement due to thermal expansion, vibration, or external forces. These straps are crucial in maintaining the integrity and safety of a plumbing or piping system.
Importance of Pipe Straps in Piping Systems
The importance of pipe straps cannot be overstated. They provide structural support, help to distribute weight, and minimize the risk of damage to pipes caused by movement. Properly installed pipe straps contribute to the longevity of piping systems and enhance safety in various applications, from residential to industrial settings. The main benefits of using a pipe strap for securing the pipes are explained below:
Benefits of Using Pipe Straps
Pipe straps provide a multitude of advantages across various applications, ensuring that piping systems operate efficiently and have an extended lifespan. Here are the key benefits of using pipe straps:
1. Support and Stability
Prevents Pipe Movement: Pipe straps firmly secure pipes in place, preventing unwanted shifting, sagging, or excessive vibration. This is particularly crucial in settings where pipes bear heavy loads or experience constant motion.
Structural Integrity: By stabilizing pipes, these straps enhance the overall structural integrity of the piping system, reducing the risk of leaks, breakage, or misalignment.
2. Vibration and Noise Reduction
Minimizes Vibration: In applications where pipes encounter vibrations, such as HVAC systems or industrial machinery, pipe straps help absorb these movements, thereby mitigating wear on both the pipe and its supports.
Reduces Noise: Cushioned pipe straps, specifically, excel at dampening vibrations and minimizing noise generated by the flow of fluids or gases through the pipes.
3. Prevents Sagging
Maintains Proper Pipe Alignment: Properly spaced pipe straps prevent sagging, particularly in horizontal installations. Sagging can lead to blockages, decreased flow efficiency, and stress points that may ultimately cause pipe failure.
Supports Heavy Pipes: In systems with large or heavy pipes, such as those found in industrial settings, pipe straps are essential for bearing the weight and preventing stress on joints and connections.
4. Protection Against Damage
Reduces Friction: Pipe straps prevent friction between pipes and surrounding surfaces, helping to minimize wear and prolong the life of both the pipes and the structure.
Prevents Corrosion: Straps made from corrosion-resistant materials, like stainless steel or plastic, offer added protection in harsh environments, such as outdoor or chemical settings, thereby extending the lifespan of the pipes.
5. Flexibility for Thermal Expansion
Accommodates Pipe Expansion: In systems where temperature fluctuations cause pipes to expand and contract, adjustable pipe straps allow for slight movement, preventing stress fractures or leaks.
Reduces Stress on Pipe Joints: By permitting expansion and contraction, pipe straps alleviate excessive stress on pipe joints, reducing the likelihood of failures due to thermal changes.
6. Versatile Installation Options
Applicable in Various Systems: Pipe straps are adaptable for a wide range of piping systems, including plumbing, electrical, HVAC, and industrial applications, making them invaluable in both residential and commercial settings.
Suitable for Different Surfaces: They can be attached to various surfaces—walls, ceilings, floors, or structural beams—allowing for versatile installation options.
7. Cost-Effective Solution
Affordable and Easy to Install: Pipe straps are relatively inexpensive and straightforward to install, offering a cost-effective solution for securing pipes.
Reduces Maintenance Costs: By enhancing stability and preventing damage, pipe straps decrease the need for frequent maintenance and repairs, ultimately saving time and money.
8. Compliance with Building Codes
Meets Regulatory Standards: In many industries and jurisdictions, building codes mandate the use of pipe straps to ensure the safety and durability of piping systems. Properly installed pipe straps help ensure compliance with these regulatory standards.
In summary, pipe straps are essential for supporting and stabilizing piping systems. They improve the longevity of pipes, reduce maintenance costs, and guarantee the safe and reliable operation of plumbing, electrical, and mechanical systems across various industries.
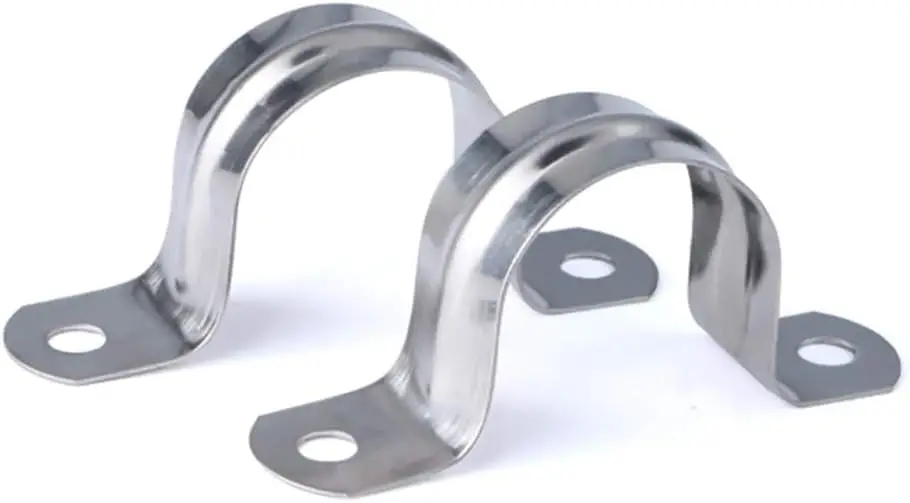
Types of Pipe Straps
Pipe straps come in various designs, each tailored for specific applications:
- U-Bolt Straps: Commonly used for round pipes, these straps consist of a U-shaped bolt that wraps around the pipe, secured by nuts on either side.
- Flat Straps: These are flat strips of metal that can be adjusted to fit different pipe sizes. They are often used in residential applications.
- Band Straps: Circular bands that wrap around the pipe, providing a tight fit.
- Adjustable Straps: Designed to accommodate pipes of varying diameters, these straps can be easily modified for different applications.
- Single-Hole Pipe Straps: Single-hole pipe straps feature a single fastening point, making them ideal for lightweight applications or where minimal support is needed. Commonly found in residential plumbing or for small-diameter pipes, these straps are easy to install and adjust, requiring fewer fasteners, which simplifies the installation process.
- Two-Hole Pipe Straps: Two-hole pipe straps incorporate two fastening points, providing enhanced stability and secure support for pipes. They are frequently utilized in larger-diameter pipe installations or areas that require additional support, such as industrial piping or electrical conduit systems. This design offers greater support and stability compared to single-hole straps, making them suitable for more demanding applications.
- Cushioned Pipe Straps: Cushioned pipe straps come equipped with a rubber lining that absorbs vibrations and protects the pipe from wear. These straps are commonly used in mechanical systems, HVAC applications, or installations where reducing vibration and noise is crucial, as well as for pipes carrying fluids or gases at high velocities. Their cushioning effect helps prevent damage from vibrations or friction, reduces noise, and extends the lifespan of both the pipe and the strap.
- Insulated Pipe Straps: Insulated pipe straps are designed with insulating materials to prevent heat transfer between the pipe and its surroundings. They are employed in systems where maintaining pipe temperature is critical, such as refrigeration, HVAC, or hot water lines. By helping to maintain the desired temperature, these straps reduce heat loss and prevent condensation on cold pipes, ensuring efficient operation.
- Heavy-Duty Pipe Straps: Heavy-duty pipe straps are constructed from thicker or stronger materials like stainless steel or heavy-gauge galvanized steel, making them suitable for supporting large, heavy pipes in industrial settings. These straps are commonly used in industrial and commercial systems where secure fastening of large pipes is essential, such as water mains, gas lines, or ventilation ducts. Their robust design ensures they can withstand heavy loads and resist environmental factors like corrosion and extreme temperatures.
Key Design Features
The design of pipe straps must account for several key features:
- Adjustment Mechanism: The ability to adjust the size is crucial for accommodating different pipe diameters.
- Surface Treatment: To prevent corrosion and wear, straps often undergo surface treatments such as galvanization or powder coating.
- Ease of Installation: Straps should be designed for quick installation without compromising strength.
Load-Bearing Capacities
Load-bearing capacity is a critical design aspect. Pipe straps must be able to support not just the weight of the pipes, but also the contents within them, environmental loads, and any dynamic forces such as vibrations. Engineers calculate the required load-bearing capacity based on:
- Pipe Material and Size
- Fluid Weight (for pipes carrying liquids)
- Environmental Conditions
Materials Used in Pipe Straps
The choice of material for pipe straps greatly influences their performance and durability. The choice of material often depends on the type of pipe being secured, the surrounding conditions, and the required level of support. Here are some common materials used in the manufacture of pipe straps:
- Steel: Known for its strength and durability, steel is often used for industrial applications. Carbon steel and stainless steel are popular choices.
- Galvanized Steel: These pipe straps are coated with a protective layer of zinc, which helps guard against rust and corrosion. Galvanized steel is commonly used in both indoor and outdoor applications where moisture is a concern, such as plumbing and HVAC systems. Known for its high strength and moderate corrosion resistance, galvanized steel is ideal for general-purpose uses.
- Stainless Steel: Renowned for its exceptional corrosion resistance, stainless steel is suited for harsh or extreme environments. It is frequently employed in industrial, marine, and chemical processing applications where pipes may be exposed to corrosive substances or saltwater. Its durability and long-lasting nature make it a top choice for high-stress conditions.
- Aluminum: Lightweight and corrosion-resistant, aluminum is often used in HVAC systems.
- Plastic: Polypropylene and PVC straps are used for applications where corrosion is a concern. Lightweight and corrosion-resistant, plastic pipe straps are typically made from PVC or polypropylene. They are commonly found in residential plumbing, electrical conduit systems, and light-duty applications where high strength isn’t critical. While they resist corrosion well, plastic straps may not be as strong as metal alternatives and can degrade over time due to extreme temperatures or UV exposure.
- Copper: Copper pipe straps offer excellent corrosion resistance and are often used with copper piping for aesthetic consistency. They are primarily found in plumbing systems in high-end residential or commercial buildings. Although copper is durable, it can tarnish over time, but this does not compromise its structural integrity.
- Cushioned Pipe Straps: Featuring a layer of cushioning material, such as rubber or neoprene, these straps protect pipes from vibration and noise. They are commonly used in mechanical systems and HVAC installations, where minimizing vibration or noise is essential. The cushioning extends the lifespan of both the strap and the pipe by reducing wear and tear.
Corrosion Resistance
Corrosion resistance is a vital consideration, especially in environments where moisture or chemicals are present. Stainless steel and galvanized steel provide excellent resistance, while plastic options can also be beneficial in corrosive environments.
Impact of Temperature and Environment
The operating temperature and environmental conditions can significantly impact the performance of pipe straps. For example, materials need to withstand high temperatures in industrial settings or resist freezing in colder climates. Selecting the right material based on these factors is essential for ensuring long-term performance.
Engineering Principles Behind Pipe Straps
Stress and Load Distribution
Understanding how stress and load are distributed across a piping system is crucial for proper design. Pipe straps must be engineered to evenly distribute loads to prevent localized stress points that can lead to failure.
Fatigue and Durability
Piping systems often experience dynamic loads due to thermal expansion, vibration, and fluid flow. Engineers consider fatigue factors when designing pipe straps to ensure they can endure repetitive stress over time without failing.
Compliance with Standards and Codes
Pipe strap design and installation must comply with various standards and codes, such as the American National Standards Institute (ANSI) and the American Society of Mechanical Engineers (ASME). Compliance ensures that the straps are safe and effective for their intended applications.
Installation Guidelines
Tools and Equipment Required
Proper installation requires specific tools, including:
- Wrenches (for tightening bolts)
- Drill and drill bits (for mounting)
- Measuring tape (to ensure proper spacing)
- Level (to check alignment)
Step-by-Step Installation Process
- Preparation: Gather all necessary tools and materials. Ensure the work area is clean and accessible.
- Measurement: Measure the distance between mounting points and determine the correct strap size.
- Drilling: If needed, drill holes for mounting screws or anchors.
- Placement: Position the strap around the pipe and align it with the mounting points.
- Securing: Tighten the bolts or screws securely, ensuring the strap is snug against the pipe without causing damage.
- Inspection: Check the alignment and make adjustments as necessary.
Common Mistakes to Avoid
- Incorrect Sizing: Using a strap that is too small can lead to damage, while one that is too large may not provide adequate support.
- Over-tightening: Over-tightening can deform the strap or damage the pipe, leading to future problems.
- Ignoring Environmental Factors: Not considering the environment can lead to premature failure of the strap.
Maintenance and Inspection
Regular Maintenance Practices
Routine maintenance is crucial for the longevity of pipe straps. Recommended practices include:
- Regular visual inspections to check for signs of wear, corrosion, or damage.
- Ensuring that bolts and screws remain tight.
- Replacing any damaged straps immediately.
Signs of Wear and Tear
Inspect for:
- Rust or corrosion on metal straps.
- Cracks or breaks in plastic straps.
- Loose or missing fasteners.
Replacement Considerations
If a strap shows significant wear, it’s essential to replace it. Factors to consider when selecting a replacement include:
- Material compatibility with the existing piping system.
- Load requirements.
- Environmental conditions.
Applications of Pipe Straps
Pipe straps are highly versatile components employed across a variety of industries, serving crucial roles in different applications. Here’s an overview of their most common uses:
Residential Plumbing
In residential settings, pipe straps are used to secure water supply lines, drainage pipes, and vent pipes. Proper installation prevents movement that could lead to leaks or other plumbing issues. Typical examples include supporting PVC, copper, or PEX pipes in areas such as bathrooms, kitchens, and basements.
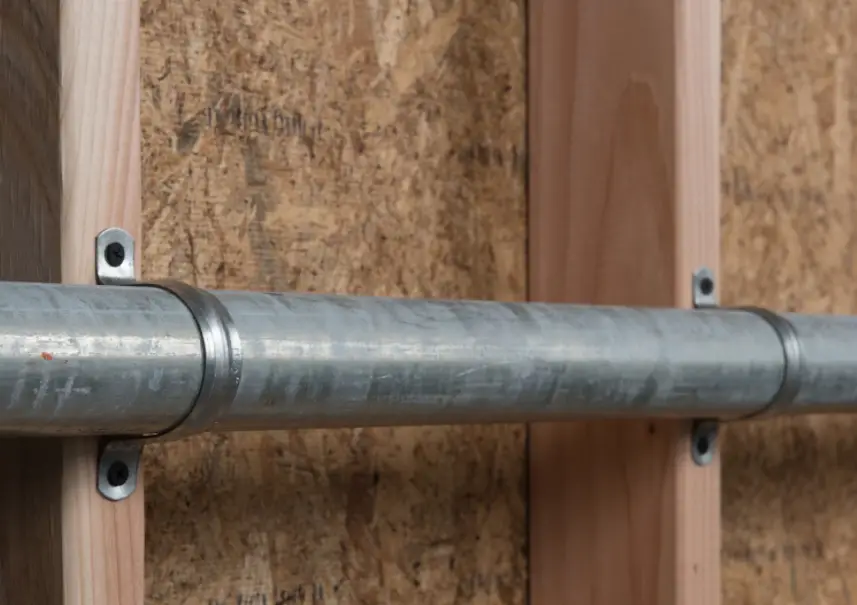
Industrial Piping Systems
In industrial environments, pipe straps are used to stabilize large-diameter pipes that transport fluids, gases, or chemicals. These straps help reduce vibration and ensure the integrity of complex piping systems. Common applications include securing pipes in factories, power plants, and chemical processing facilities.
HVAC Systems
Pipe straps play a critical role in HVAC systems by securing ductwork and piping that transport heating and cooling fluids. Properly installed straps help minimize vibration and noise, contributing to a more efficient system. They are often used to fasten refrigerant pipes in air conditioning systems and secure exhaust ducts in ventilation setups.
Electrical Conduit Support
Pipe straps also play a vital role in fastening electrical conduits, whether metal or PVC, to walls or ceilings. This ensures a safe and organized routing of electrical wires, which is essential in residential, commercial, and industrial electrical installations.
Fire Sprinkler Systems
Within fire protection systems, pipe straps ensure that sprinkler pipes are properly positioned for effective fire suppression. They are commonly used to hold steel or copper sprinkler pipes in place within commercial buildings and warehouses.
Automotive and Marine Applications
Pipe straps are also utilized in vehicles and boats to secure fluid or exhaust lines. For instance, they are used to secure fuel and brake lines in cars, as well as fastening exhaust pipes in boats.
These diverse applications highlight the significance of pipe straps in providing structural support, ensuring safety, and maintaining the functionality of piping systems across various industries.
Pipe straps are fundamental components of piping systems, providing necessary support and stability. Understanding their design, engineering principles, materials, and applications is vital for ensuring safe and effective installations. By adhering to best practices in installation and maintenance, individuals and organizations can enhance the longevity and reliability of their piping systems.