Both pipelines and piping systems play a pivotal role in the transportation of fluids, gases, and other materials across various industries. Even though the terms “piping” and “pipeline” are often used interchangeably, there are significant differences between the two. The major differences between piping and pipeline are already discussed here. Note that, there are distinctions between the materials used in piping and pipelines. In this article, we’ll learn some of the differences between piping and pipeline materials while exploring their characteristics, applications, and considerations.
What are Piping Materials?
Piping refers to a system of pipes used to convey fluids within a facility or plant. Piping materials are carefully selected based on factors such as the type of fluid being transported, temperature and pressure requirements, corrosion resistance, and cost considerations. Some of the materials used in Piping are:
Metals:
Common metals used in piping systems are:
- Carbon steel,
- LTCS (low-temperature carbon steel)
- Stainless steel,
- Copper, aluminum, and various other alloys.
Carbon steel is a popular choice for its strength and affordability, while stainless steel is preferred for its corrosion resistance, making it suitable for corrosive environments.
Plastics:
Plastic materials are chosen for their corrosion resistance, flexibility, and ease of installation. Common plastic materials in piping are:
- Polyvinyl chloride (PVC),
- Polyethylene (PE)/HDPE, and
- Polypropylene (PP)
Composite Materials:
Fiberglass-reinforced plastic (FRP) and reinforced thermosetting resin (RTR) are composite materials increasingly utilized in piping. These materials offer a balance of strength, corrosion resistance, and lightweight characteristics.
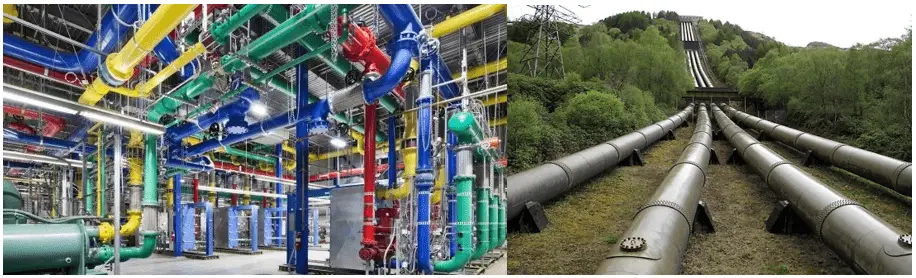
What are Pipeline Materials?
Pipelines are long-distance transportation systems designed to carry large volumes of fluids or gases over extended distances. Pipeline materials must withstand the challenges posed by external environmental factors, such as soil conditions, temperature variations, and potential ground movement. Common materials used in pipelines are:
- Carbon Steel: Carbon steel remains a predominant material for pipelines, especially in the oil and gas industry. It provides a balance of strength, durability, and cost-effectiveness. Pipeline materials use API 5L code for the pipes and API 6D code for the valves.
- High-Strength Alloys: In high-pressure and extreme temperature applications, pipelines may incorporate high-strength alloys such as X65 or X70 to ensure structural integrity.
- Corrosion-Resistant Alloys: For corrosive environments, corrosion-resistant alloys like duplex stainless steel or nickel alloys are employed to prevent degradation over time.
- Non-metallic pipelines: Pipelines can also use PE/HDPE/PP materials or FRP/GRP/RTR/GRE materials for fluid transportation.
Differences between Piping Material and Pipeline Materials
The major differences between Piping and Pipeline Materials can be discussed considering various parameters as mentioned below:
Material Selection Criteria
Piping materials are decided considering the following parameters:
- The type of fluid that will be transported through the pipes
- The design and operating temperatures and pressures of the pipes
- The flow medium characteristics, such as viscosity, density, corrosiveness, abrasiveness, etc.
- The fracture tendencies of the pipes, such as fatigue, creep, thermal expansion, etc.
- The corrosion and erosion of the pipes, such as galvanic, pitting, stress corrosion cracking, etc.
- The environment where the pipes will be working, such as indoor, outdoor, underground, underwater, etc.
On the other hand, pipeline materials are selected considering the following factors:
- The fluid transportation efficiency (the ability of the pipeline to deliver the fluid with minimal losses, such as friction, leakage, etc.)
- Safety and reliability (the ability of the pipeline to prevent or withstand failures, such as rupture, explosion, fire, etc.)
- The environmental impact (the effect of the pipeline on the surrounding environment, such as soil, water, air, wildlife, etc.)
Temperature Resistance
Piping materials have the capability of carrying fluids at very high temperatures and pressures. While the temperature capability of Pipelines is limited to 232 degrees C as per ASME B31.8 (120 degrees C as per ASME B31.4).
Design Allowable Stresses
Piping materials are limited by the design’s allowable stresses which is governed by the term Sc and Sh which are much lower than the material yield strength. On the other hand, the pipeline material’s design allowable stress is governed by SMYS (Specified minimum yield strength). So, pipeline materials have a very low safety factor than piping materials.
Material Thickness
For the same pressure rating, pipeline materials usually have less material thickness as compared to piping materials. Hence, the weight of the piping materials is more than that of pipeline materials for the same pressure classes.
Hydrotest Pressure
Piping materials are usually hydrostatically tested at 1.5 times the design pressure whereas pipeline materials are hydrotested at 1.25 times the design pressure.
Corrosion Resistance
In most cases, the piping materials have to resist the corrosion generated by the fluid it carries means internal corrosion. While pipeline materials need to withstand external corrosion from soil and environmental factors.
Temperature and Pressure Ratings
Piping materials must meet specific temperature and pressure requirements based on the application, while pipeline materials need to account for the varying conditions along their extensive routes.
Cost Considerations
Piping materials are often selected based on factors such as installation costs and ease of maintenance within a confined space. Pipeline materials, on the other hand, must balance upfront costs with the long-term durability required for extended transportation routes.
Environmental Factors
Pipelines traverse diverse landscapes, and materials must be chosen considering factors like soil conditions, seismic activity, and temperature fluctuations.
Here’s a comparative table that outlines the major differences between piping materials and pipeline materials:
Feature | Piping Materials | Pipeline Materials |
---|---|---|
Scope | Used for smaller, often individual sections or components | Used for larger, continuous segments of transportation systems |
Size Range | Typically smaller diameter, up to a few inches in diameter | Generally larger diameter, from several inches to several feet |
Common Materials | – Carbon Steel – Stainless Steel – PVC – Copper – PEX | – Carbon Steel – Stainless Steel – Ductile Iron – HDPE – Concrete |
Application | Used in residential, commercial, and various industrial applications | Primarily used in industrial and utility applications, including oil, gas, and water transportation |
Pressure Ratings | Generally designed for various pressure ratings depending on application | Designed to handle high pressure and high flow rates over long distances |
Flexibility | Often more flexible and easier to handle and install in smaller sections | Less flexible, typically requires heavy equipment and precise installation |
Jointing Methods | – Threaded – Welded – Flanged – Compression – Solvent Weld | – Welded – Flanged – Bolted – Mechanical Couplings |
Cost | Generally less expensive due to smaller size and simpler applications | Typically more expensive due to size, material requirements, and installation complexity |
Durability | Suitable for a range of applications with varying durability needs | Designed for long-term durability and resistance to harsh conditions |
Corrosion Resistance | Varies by material; options for corrosion-resistant materials like stainless steel or PVC | Often designed with materials or coatings that resist corrosion in challenging environments |
Installation | Easier to install in small sections; often done manually | Requires heavy machinery and specialized techniques for installation |
Maintenance | Generally easier and less costly to maintain and replace | Maintenance can be more complex and costly due to the scale and potential for more significant issues |
Standards and Codes | Subject to various industry and local standards for residential and commercial use | Governed by stringent industry standards and codes for large-scale infrastructure, such as API, ASME, and ASTM |
Temperature Range | Varies by material; some designed for high temperatures, others for cold | Designed to handle extreme temperatures and environmental conditions. However very high design temperatures are usually not expected. |
In a nutshell, Piping materials are often constructed with a wide range of materials and components, such as cast iron, carbon steel, low-temperature carbon steel, alloy steel, stainless steel, duplex stainless steel, nickel alloys, aluminum, titanium, etc. Piping materials also use different codes and standards for the pipes, fittings, and valves, such as ASTM, BS, API 5L, ASME B31, ANSI, DIN, ISO, etc. Pipeline materials have to mainly consider fluid transportation efficiency, safety and reliability, and environmental impact. Pipeline materials are typically constructed with a single type of material, such as steel, plastic, or composite. Pipeline materials use API 5L code for the pipes and API 6D code for the valves.
nice, brother i need to learn more about- construction piping engineer because i have 8yrs experience in automobile field now at last 3yrs working in oil and gas industries…..but my overall experience is 11 in oil and gas industry…..when ever i attend any interview, The interviewer ask you have 11yrs experience in oil & gas industry …when the interviewer ask question…. bce i have 3yrs….