Every EPC company must have project-specific pressure vessel nozzle loading tables which are used for comparing allowable nozzle loads for vessels, columns or towers, heat exchangers, Drums, or any similar type of equipment. Normally forces and moments at the nozzle and shell interconnection are provided in a tabular format. These force and moment values are decided based on the following major factors:
- Nozzle diameter
- Connected flange rating
- Equipment and nozzle thicknesses.
- RF Pad thickness if any
- Equipment diameter, etc.
Using these tables is quite simple. However, we must keep in mind a few points while using those tables. This article will list those important points for using these tables easily.
1. Before checking the tables, find out the load and moment directional drawing from which we have to correlate the Caesar II axis.
2. Each nozzle, including those designated “spare” but with the exception of man-holes and instrument nozzles shall be designed to withstand the forces and moments specified herein. The indicated loads are to be considered to act at the shell/head-to-nozzle intersection.
3. For nozzles matching with any global direction (other than head nozzles) compare the values mentioned on the tables with global force values in CAESAR II output.
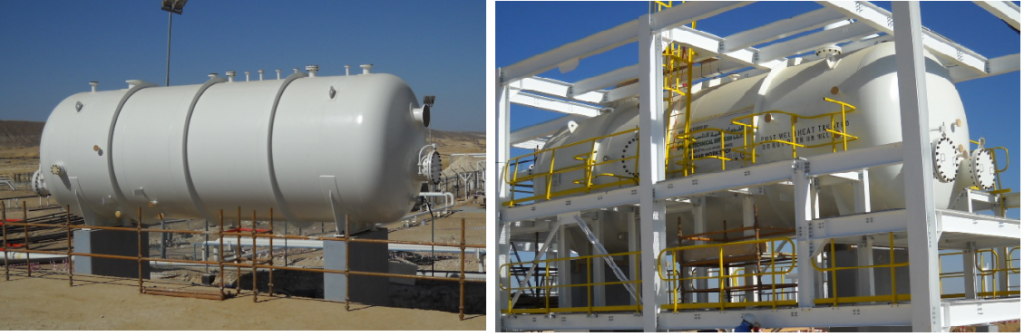
4. For inclined nozzles in the horizontal plane (with respect to any global direction) there are 2 options as listed below.
- Compare loads mentioned in the tables above with local element forces in CAESAR II output. In that case, the local X force will be a radial force and compare other directions to get proper forces.
- Otherwise rotate the CAESAR II input model to match the nozzle axis with any global Caesar II axis and compare the loads and moments.
5. For Head nozzles (nozzle axis and equipment axis same direction) compare Mx and Mz as per √[{(Mx)2+(Mz)2}] ≤ √[{(ML)2+(MC)2}]
6. In the case of any vessels in the packaged area, these values shall not be applicable and nozzle loading shall be coordinated with the vendor.
7. In the case of any licensor / proprietary item, these values shall not be applicable and nozzle loading shall be confirmed by them.
8. Allowable for self-reinforced nozzle shall be more than as mentioned in the above table. In that case, allowable shall be exercised from the vendor.
9. For jacketed nozzles, loads are to be confirmed by the vendor.
10. These tables are not applicable for checking loads at flange faces.
Few more Resources for you..
A short Presentation on Basics of Pressure Vessels
Brief Explanation of Major Pressure Vessel Parts
A Presentation on VESSEL CLIPS or VESSEL CLEATS
Understanding Pressure and Temperature in the context of Pressure Vessel DesignOnline Course on Pressure Vessels
If you wish to learn more about Pressure Vessels, their design, fabrication, installation, etc in depth, then the following online courses will surely help you:
Is this same table for allowable operating nozzle loads to be consulted for Occasional loading also? Can we increase the allowable load components by about 20 to 33% for occasional loading?
This is a very good point. Very often, designers will use a table of allowable loads which never made much sense because the natures of primary and secondary loads are different with varying failure modes. There should be allowable loads for primary, secondary, and one could argue for peak. Occasional loads are typically considered primary.
Very good work
Can we calculate nozzle load by theoretically?
If possible please provide details on amitkadam9590@gmail.com
I qm unable to see any tables due to ads may be. Can someone reply what are formula to decide nozzle load (lb) using diameter in inche