A pipe rack is a very important part of process piping. A Pipe Rack can be defined as a steel-framed structure that supports and carry pipes inside the processing plant and transfer the fluid between equipment and storage facilities or utility areas.
While designing a pipe rack, there are two main factors into which a stress engineer should look at details. Those are
- Expansion loop design and placement and
- Pipe rack loading to Civil for the rack design.
The following write-up will list the considerations while designing the pipe loop and rack loading.
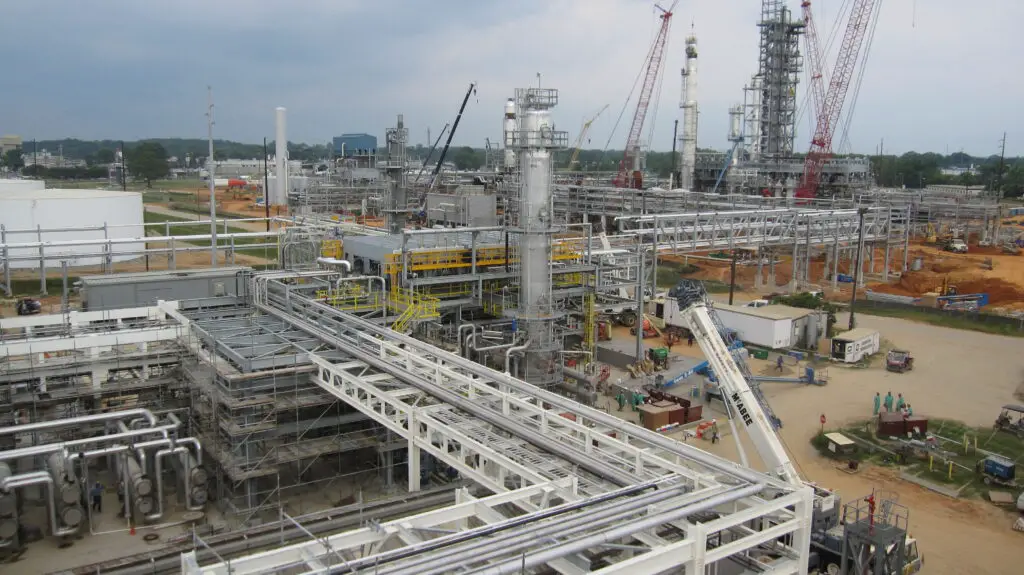
Expansion Loop design and placement
In most organizations, there are no defined criteria for designing and placing an expansion loop in a pipe rack. So most of the time the expansion loop is designed and located based on user experience. The important parameters which govern the design of the expansion loop are listed below:
- A. Design/Maximum operating temperature of the line
- B. Allowed Displacement or movement (Normally allowed thermal displacement is 250-300 mm inside a loop and 75-100 mm in outside turns)
- C. Allowed Expansion stress (normally within 80% of code allowable)
- D. Line size (Bigger sizes require more leg to absorb expansion)
- E. Loop Supporting Requirements (locations at which the loop will be supported)
- F. Fluid type (Normally Flare and condensate lines require a 2D loop)
- G. Line sagging criteria from Project specification (Sometimes Steam, Condensate, Two-Phase flow lines, and Flare lines require sagging limited within 3-5 mm for others it can go up to 15 mm)
- H. Rack length and width
After having the above-mentioned parameters ready one can proceed to locate the loops over the rack. Follow the below-mentioned steps as a preliminary guideline:
a. Select an elevation of the pipe rack and check what the lines running over that rack.
b. Select the line with maximum temperature first. Check the allowed maximum movement outside loop (say 75 mm) and place the first anchor at a distance that will be nearer to the allowed thermal movement (75 mm) as mentioned above.
c. Now as one anchor is fixed one can easily calculate the thermal displacement at design temperature towards the other end/turn. If the displacement is within the allowed displacement (75mm) then an expansion loop is not required. But if the calculated displacement is more (>75mm) then the expansion loop is required. From this displacement, you can decide how many expansion loops are required for the straight run allowing a maximum of 250-30 0mm displacement inside the loop. (Care should be taken for expansion leg requirement as sometimes allowing 300 mm displacement may cause expansion failure or huge anchor load. In that case, increase the number of expansion loops.)
d. It is better to place lines with high temperatures outside of the rack so that a longer loop length can be achieved on the other side.
e. It is better to nest the loops in a single location (the same structures can be utilized for supporting)
f. Don’t mix lines that required 2D loops with lines that required a 3D loop in the same elevation.
g. It is better to place anchors in similar locations for deciding anchor bay.
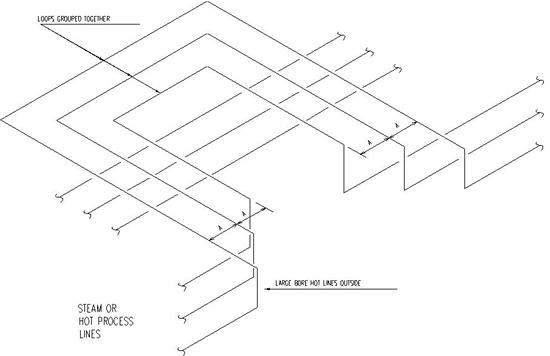
- h. After deciding the loops check the loop length requirements from Pipe-Data-Pro, Caesar modeling (most optimized approach), Nomograph, Manual calculation, etc.
- Click here to know more about Piping Expansion Loops
Pipe Rack Loading
Rack loading is provided to CSA for the economic design of the pipe rack. Providing pipe rack loading is a very difficult task for a stress engineer as most of organizations do not have any guidelines. Normally Pipe rack loads are transferred in 3 stages:
- a. Initial rack loading for rack foundation design (before piling): The project has just started and very little data is available. The piping design places the lines over the rack based on preliminary P&ID. Rack loads are provided mostly based on assumption/experience. Conservative loads are to be provided.
- b. Rack loading for member sizing (after 30% model review): Most of the data has started arriving. Loads are to be provided based on actual analysis.
- c. Rack loading for final member checking (after 60% model review): All vendors are decided. Line size and locations are finalized. All critical lines are fixed. Loads are provided for checking designed members again. Loads are to be provided based on Software analysis.
Few points to keep in mind while providing Rack loading:
- 1. Operating, Water filled, and Occasional loads for big-size lines (> 16-inch NPS) are to be provided separately. For guides and anchors, loads with and without friction should be provided.
- 2. For the Flare line 1/3rd water-filled weight can be considered.
- 3. Proper directions to be marked.
- 4. After the long run doesn’t provide a guide in the immediate first possible location after the bend.
- 5. Consider concentrated loads of inline valves, flanges, equipment, etc.
- 6. Sometimes large equipment is placed over the pipe racks (Air Fin Fan Cooler, Heat Exchangers, etc). So take the operating weight of equipment from the mechanical group.
- 7. Cable tray loads are to be taken from the electrical/instrumentation group. (In absence of data a uniformly distributed load of 1.0 KPa for a single level and 1.9 KPa for a double level of cable trays can be considered)
- 8. Include the forces of PSV reactions if applicable.
In the absence of data, the following guidelines can be used as preliminary piping loads:
- a. A uniformly distributed load of 1.9 KPa for piping, product, and insulation can be considered for line size (for each line)
- b. For line size larger than 12-inch nominal diameter actual concentrated load including the weight of piping, product, valves, fittings, and insulation shall be used.
Click here to know about the Pipe rack layout design considerations.
please advice me any thumb rule to find out the supporting load on the tack in begining stage ..i dont have guideline in my company as i am doing first time to give preliminary load for civil ..
As you said i considered line form PID ..but i’m worried how can i distribute load in each support…like load on axial stop and guide..
dear arun. normally preliminary piping loads on racks are given 150-250 kg/m2 which take in account for a full rack deck of 12″-14″ piping. then concetrated loads are transmitted to take into account for bigger pipe loads than 12″-14″. civil dpt usually takes into account friction on statistical basis of 10% of vertical piping loads, but for concetrated piping 12-14 or more the pipe stress engineer should give appropriate values. if you need any help plz contact me at socrate.martino@gmail.com and i will be glad to give you ther tips.
It’a very nice posting!
But I can not understand exactly for the determination of anchor location and the number of loop. Because I’m a beginner at piping stress analysis.
Could you explain once again with actual example?
Please upload blog on pipe rack width calculation with one or two exercise of how to calculate rack width.
Thanks for the great explanation.
1- if we have several 2,3, 4inches lines on the piperack, should we consider these sizes for specifying uniform loads? or we should consider all lines are 6″ full of water?
2- How can we calculate horizontal loads of uniform loads?
Hi, I have a doubt related to steam pipe load whether we consider water filled pipe for steam line or empty pipe. This will directly impact on the anchor bay loading as there will be a vast difference in both the loadings.
Thanks