A Spiral Wound Gasket is the most widely used common metallic gasket used in industrial applications involving a range of pressure and temperatures. They are popular in the oil and gas, chemical, petrochemical, power, and food industries and prevents leak through flange joints. The concept of spiral wound gasket was first developed by Flexitallic in the year 1912 to serve US refinery operations involving severe temperature and pressure fluctuations.
Spiral wound gaskets are used for
- High-Temperature service applications.
- High-pressure applications.
- Corrosive fluids.
- Flammable Fluids.
- Hydrogen, etc.
Construction of Spiral Wound Gaskets
A spiral wound gasket is a semi-metallic gasket. It consists of a spirally wound v-shaped metallic with a non-metallic filler material. There are three elements that constitute a spiral wound gasket. They are:
Outer ring:
Also known as a guide ring or centering ring, the outer ring of a spiral wound gasket is usually made of carbon steel material. The main purpose of this element is to center the gasket while inserting it into a bolted flange joint.
Inner ring:
The inner ring is one of the most important parts of a spiral wound gasket as it prevents windings from buckling inside the pipe. In the situations of buckling of a gasket, parts of it get sucked into the pipe and eventually flow through the piping system to get caught/wrapped on something. Inner rings prevent this phenomenon and help in avoiding the problem.
Sealing element:
This is the element of the spiral wound gasket that creates a tight seal to prevent leaks. The sealing element encompasses both windings and filler material. In general, spiral wound gaskets use a flexible graphite filler material rated for high temperatures. Graphite as filler material also helps the gasket avoid flange distortion and joint misalignment. Another common filler material is PTFE (Polytetrafluoroethylene). However, PTFE is not suitable for use in high-temperature applications. The most widely used winding materials are Stainless Steel and Monel.
Refer to Fig. 1, which clearly shows these three elements of a spiral wound gasket.
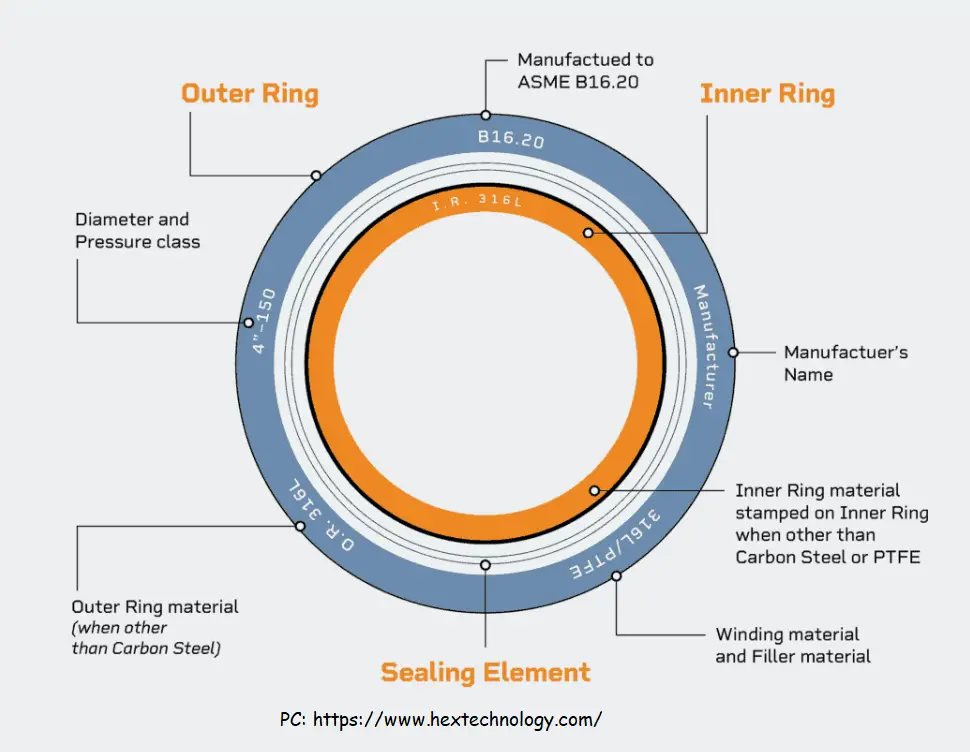
Markings on Spiral Wound Gasket
Spiral wound gaskets are identified using different markings on the gasket. Each marking provides brief information about the spiral wound gasket specification important during the gasket selection process.
Some of the necessary information that the markings on the spiral wound gasket provide are:
- Design Standard or Code: The code based on which the spiral wound gasket is designed and manufactured is clearly marked. In Fig. 1, you can easily find the standard ASME B16.20.
- Name of the Spiral Wound Gasket Manufacturer: One can easily understand the manufacturer of the gasket by looking at the manufacturer name mentioned on the gasket.
- Winding and Filler Material: Both the winding and filler materials are clearly specified on the spiral wound gasket. Specific gasket colors also provide a lot of information regarding the materials.
- Diameter and Pressure class: The size of the gasket and the load the spiral wound gasket can handle, are specified by the Diameter and Pressure Class marking on the gasket. The usual pressure classes for spiral wound gaskets are 150, 300, 400, 600, 900, 1500, and 2500. With an increase in pressure class, the ability of the spiral wound gasket to withstand pressure increases.
- Inner and Outer ring material
Materials for Spiral Wound Gaskets
The usual materials that are used in a spiral wound gasket are provided in table-1 below:
Metal Winding Strip Material | Filler Material | Guide Ring Material |
Stainless Steel Grade 304 | Graphite | Stainless Steel Grade 304 |
Stainless Steel Grade 304L | PTFE | Stainless Steel Grade 316L |
Stainless Steel Grade 316L | Ceramic | Stainless Steel Grade 316Ti |
Stainless Steel Grade 316Ti | Non-sintered PTFE | Stainless Steel Grade 321 |
Stainless Steel Grade 310 | Non-Asbestos Fiber | Stainless Steel Grade 347 |
Stainless Steel Grade 321 | Aluminum | Stainless Steel Grade 410 |
Stainless Steel Grade 347 | Treated Asbestos Fiber | Monel 400 |
Stainless Steel Grade 430 | Nickel 200 | |
Stainless Steel Grade 317L | Alloy 20 | |
Alloy 20 | Titanium | |
Monel 400 | Hastelloy B2 | |
Titanium | Hastelloy C276 | |
Nickel 200 | Incoloy 800 | |
Inconel 600 | Incoloy 825 | |
Inconel 625 | Inconel 600 | |
Inconel X-750 | Carbon Steel | |
Hastelloy B2 | ||
Hastelloy C276 | ||
Incoloy 800 | ||
Incoloy 825 | ||
Duplex Stainless Steel | ||
Tantalum | ||
Zirconium |
Spiral Wound Gasket Color Coding
All spiral wound gaskets are color-coded. The colors of the outside rim, and the color of the stripe along the rim provides the material information of the gasket elements. The color of the outside rim tells the material of the gasket’s winding whereas the rim strip color tells about the gasket’s filler material.
Some typical outside rim colors that tell the material for the inner ring and metallic windings are as follows:
- Yellow means 304 stainless steel gasket material.
- Green is 316 stainless steel.
- Turquoise is 321 stainless steel.
- Blue is 347 stainless steel.
- Orange is for Monel.
- Black is Alloy 20
- Silver is carbon steel
- Brown is for Hastelloy B
- Beige is Hastelloy C
- Gold is Inconel
- Red is Nickel
- Purple is Titanium
Similarly, the common rim strip colors are:
- Pink indicates mica paper
- Gray indicates graphite
- White indicates PTFE
- Light Green green indicates ceramic
In the oil and gas industry, the most frequently seen outside rim colors are Yellow, Green, and Orange signifying that SS-304, SS-316, and Monel are the most widely used spiral wound gasket outside rim materials. The most common strip color in the oil and gas industry is gray which indicates graphite. Fig. 2 below provides a typical cross-section of a spiral wound gasket.
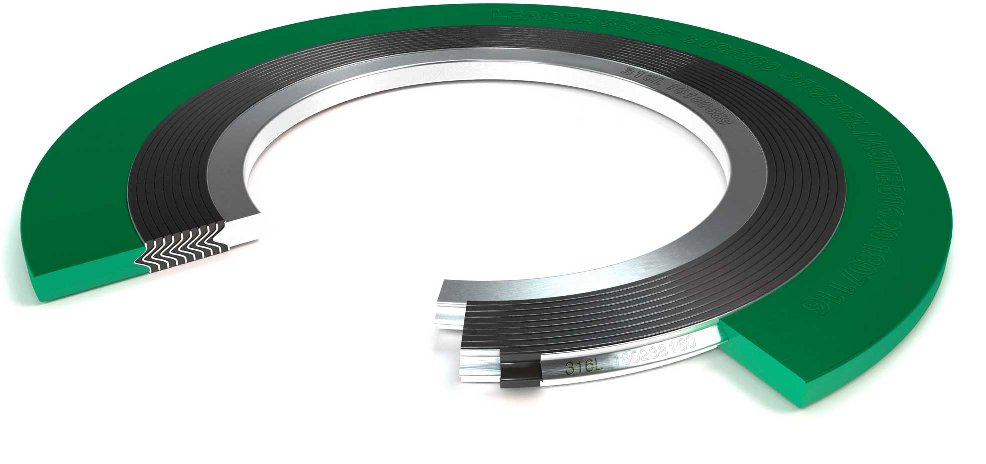
Spiral Wound Gasket Types
Spiral wound gaskets are manufactured in various styles. Some of the common spiral wound gasket styles are:
Style CG – This type of spiral wound gasket is composed of a sealing element and an outer metal ring. The outer ring ensures optimum sealing performance by preventing over-compression. The ring also helps in locating the gasket on the mating flange faces. Style CG gaskets are designed to use on raised and flat-faced flanged connections. They are widely used for mild to moderate service conditions.
Style CGI – This spiral wound gasket types have an inner metal ring in addition to the outer metal ring. The inner metal ring of the CGI-style gasket constrains the sealing element on both internal and external diameters. It works as an additional compression stop and prevents the inner buckling of the sealing element. At the same time, It creates a physical barrier between the sealing element and the process stream that shields the sealing element from heat and media and prevents erosion. Style CGI type of spiral wound gaskets is recommended for use on raised and flat-faced flanged connections with moderate to severe service conditions.
Refer to Fig. 3, which shows a typical example of different spiral wound gasket types.
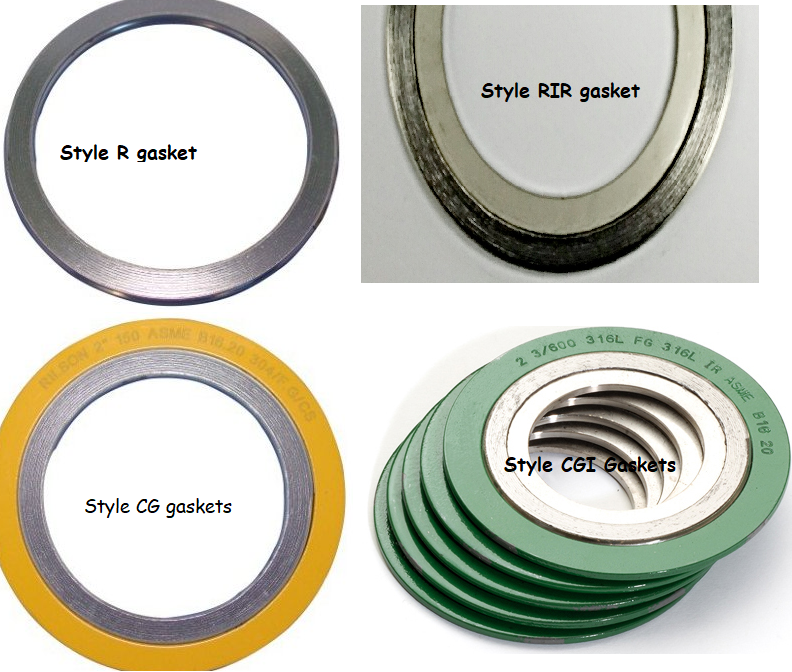
Style R – Style R gaskets consist of a sealing element, and metallic plies are used at the start and termination of the winding process. This improves the stability and sealing performance of this type of spiral wound gasket. Style R gaskets are used on tongue and grooves, male and female, and flat-to-groove flanged connections.
Style RIR – It is comprised of a sealing element and an inner metal ring. The inner ring provides the function of a compression stop as well as creates a physical barrier between the sealing element and the media stream. The inner ring is specially designed such that it reduces turbulent flow. This will minimize flange erosion and prevent debris build-up in the annular space between the pipe bore and the internal diameter of the gasket. They are suitable for use on male and female (spigot and recess) flanged connections.
There are various other types of spiral wound gasket types that are used specifically for special applications.
Spiral Wound Gasket Specification
Spiral wound gaskets are specified using various parameters like:
- Nominal Pipe Size
- Pressure Rating Class of the Connecting Flange
- Gasket Design and Manufacturing Standard
- Gasket Style required
- Outer Ring, Inner Ring, and Winding Materials
- Flange Standard
- Fluid Service where it will be used (Optional)
- Design and operating temperatures (Optional)
Spiral Wound Gasket Thickness
The thickness of spiral wound gaskets usually ranges between 3.2 mm and 4.5 mm. However, for very large diameters, more thickness ranging from 5.5 mm to 7 mm is recommended. The full range of spiral wound gasket thicknesses available in the market is 1.6 mm to 7.2 mm.
Spiral Wound Gasket Pressure Rating
As mentioned earlier, spiral wound gaskets are available in seven pressure-rating classes. They are 150, 300, 400, 600, 900, 1500, and 2500 classes. Spiral wound gasket dimensions are referred to from the design standards. For example, ASME B16.20 has spiral wound gasket size charts in tabular formats that provide all required dimensions with respect to pressure class and pipe size.
Hi , SIR ,
How can we get the pdf format of your postings
Dear Sir, could you please explain the marking: qoute( 2″ 3-600 )unqoute. What is the meaning of 2″, 3 and 600.
same queston about (2 3/600) as shown on the picture.
Can we use a spiral wound gasket for RTJ flanges
Very good information about spiral wound gaskets….!!!