Stress Corrosion Cracking or SCC is a slow failure mechanism of engineering materials in a corrosive environment. Many ductile metals and alloys fail each year due to stress corrosion cracking which starts with a crack initiation, propagation, and growth of that crack to a damaging limit in exposure to a corrosive environment. Stress corrosion cracking is alloy and environment-specific which means the mechanism varies widely depending on the material and environment. A metal that shows SCC tendency in one environment may not be under SCC attack in a different environment. However, the exact mechanism of stress corrosion cracking is not yet fully developed.
Stress corrosion cracking is a slow and delayed failure process. SCC can initiate and propagate with little or no outside warning of corrosion. Cracks usually start at surface flaws by corrosion, wear, or other processes.
In the steel industry, stress corrosion cracking (SCC) is a form of intergranular corrosion that results in crack formation in a corrosive environment. As steel is the most common industrial material, stress corrosion cracking poses a significant threat to industrial systems such as pipelines, power plants, chemical industries, bridges, and so on.
What Causes Stress Corrosion Cracking?
There are three major factors that contribute to the failure following stress corrosion cracking methodology:
- Tensile Stress (usually because of operational applied stress, thermal stress, or residual stresses from welding and fabrication)
- Corrosive Environment and
- Susceptible material in a certain metallurgical condition promotes premature failure in a component.
Other elements for stress corrosion cracking to occur are temperature and time. Fig. 1 below shows a typical example of stress corrosion cracking.
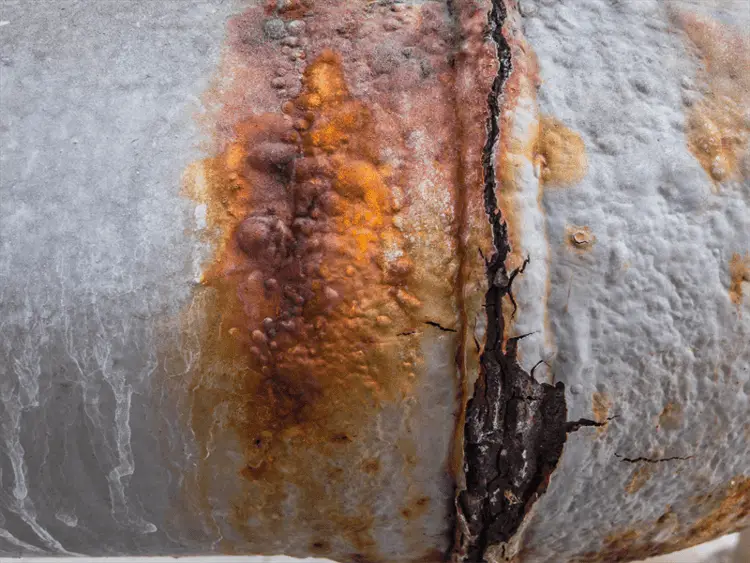
The fracture processes in SCC are accelerated by the presence of cracks and other defects on the components. The failures caused by SCC are sudden and catastrophic in nature and are usually caused at much lower stress levels than yield stress. Some of the typical examples of SCC are listed below:
- Seasonal cracking of brass in an ammonia-rich environment
- Sensitization and stress corrosion cracking of stainless steels in presence of caustic, chlorides, and polythionic acid.
Types of Stress Corrosion Cracking
Depending on the actual SCC mechanism, various types of stress corrosion cracking are found.
- Chloride Stress Corrosion cracking– prevalent in austenitic stainless steels in combination with tensile mechanical stress at a high-temperature condition in the presence of chloride ions and oxygen.
- Caustic Embrittlement-Prevalent in stainless steels in the presence of a high hydrogen concentration under caustic environments.
- SCC cracking of steels in hydrogen sulfide environment in oil and chemical industries.
- Sessional Cracking-Cracking of brass in ammonia environments.
- Craze Cracking-cracking of polymeric materials due to applied stress and environmental reaction.
Characteristic Features of Stress Corrosion Cracking
SCC has the following characteristic features:
- Stress corrosion cracking failure occurs at stress levels much lower than the material yield stress.
- The materials subjected to SCC are ductile but the failure mechanism is brittle.
- The cracks in stress corrosion cracking are in general caused by corrosion.
- At microscopic levels, intergranular and transgranular cracks are the major features of stress corrosion cracking. Intergranular cracks grow along grain boundaries but transgranular cracks proceed across the grains.
Materials Susceptible to Stress Corrosion Cracking
The following materials are prone to SCC attack:
- Stainless steels (In the temperature range of 415°C to 850°C in chloride, caustic, and polythionic acid environment)
- Carbon Steel (In carbonates, strong caustic solutions, nitrates, phosphates, seawater solution, acidic H2S, and high-temperature water environment)
- Copper and copper alloys (In an environment containing ammonia, amines, and water vapor)
- Aluminum and aluminum alloys (In environments containing moisture and NaCl solution)
- Titanium and titanium alloys (In exposure to seawater, fuming nitric acid, and methanol-HCl environment)
- Polymers (In aggressive acid and alkali environments)
- Ceramics
Stress Corrosion Cracking in Welding
The major cause attributed to stress corrosion cracking is the residual stress generated during welding and fabrication processes. In the stress corrosion cracking of metal alloys, the residual stress due to welding plays a crucial role. Stress corrosion cracking in welding is caused by non-uniform temperature changes during welding. Also, while welding certain steel grades, the solid-state transformation of austenite to martensite during cooling generates a significant amount of residual stresses. For carbon and low alloy steels, while quenching the austenite containing carbon atoms at a fast cooling rate, martensite is formed. In this situation, the carbon atoms do not get a chance to diffuse out from the crystal structure and form cementite. This increases the metal volume which results in significant residual stress.
Mechanisms of Stress Corrosion Cracking
Depending on the type of material and environment, various different Stress Corrosion cracking mechanisms are prevalent in the industry. Some of the well-known SCC mechanisms are:
Mechano-electrochemical model
As per this mechanism of stress corrosion cracking, in an alloy microstructure, there are pre-existing regions that become sensitive to anodic dissolution.
Film rupture model
For alloys having a passive layer on their surface, the film rupture SCC mechanism is well-known. In this mechanism, the corrosion starts following plastic deformation. The plastic strain disrupts the film which discloses the bare metal to the corrosive environment. Soon, a localized SCC attack starts in those areas and the process is repeated resulting in the growth of the cracking.
Adsorption phenomenon
The SCC mechanism considers the material embrittlement in the vicinity of a corroding area.
Pre-existing Active Path Model
Intermetallics and compounds are formed in the already existing paths like grain boundaries which are prone to SCC attack.
How to prevent Stress Corrosion Cracking?
As the mechanism of stress corrosion cracking is not yet fully understood, the prevention methods are based on empirical experiences. In general, one or more of the following methods can reduce the possibility of SCC:
- As tensile stress is one of the major elements helping stress corrosion cracking, lowering the stress levels in components will reduce the potential of an SCC attack. By providing annealing treatment of the component, residual stress can be eliminated to a great extent.
- Eliminating or decreasing aggressive species from the environment where the component is installed will serve as one method of reducing SCC attacks. For example, in the case of austenitic stainless steels, maintaining chloride content below 10 ppm significantly reduces the probability of SCC.
- Selecting more stress corrosion cracking resistant materials will protect the product from stress corrosion cracking.
- The application of cathodic protection reduces failures from stress corrosion cracking.
- In mildly corrosive media, adding phosphate and other organic and inorganic inhibitors can reduce the stress corrosion cracking effects.
- Sometimes, applying a protective coating can be effective.
- Using the shot-peening method to produce residual compressive stress in the component surface can prevent stress corrosion cracking.
- Controlling the temperature and the electrochemical potential reduces the SCC possibility.
Very informative.Thanks.
Hi Anup Kumar, I would like to know is there any way we can artificially fabricate this crack? Because my team trying to fabricate by using electrolysis process, as result we get a defect width: 1mm, length: 50mm and depth: 6.4mm. By saying this defect have thin width of 1mm, can we saying this considered as crack defect? Is there any codes specifically mention crack or crack-like defect specification?