In the world of engineering, manufacturing, and facility management, maintenance plays a crucial role in ensuring the longevity and efficiency of equipment and systems. From machinery in a manufacturing plant to oil and gas systems or HVAC systems in a commercial building, effective maintenance strategies are essential for minimizing downtime, reducing costs, and enhancing safety.
What is Maintenance?
Maintenance is the effort required to undertake for maintaining equipment performance similar to new ones. Unscheduled downtime due to equipment malfunction is one of the major concerns for industries, which calls for billions of dollars of losses each year. Maintenance is an important aspect of increasing productivity by reducing such downtimes and improving equipment performance. Maintenance is basically a set of processes and practices that help in the continuous and efficient operation of assets. The major benefits of maintenance are
- Increase in the life of the equipment and other assets.
- Optimization of asset performance.
- Reducing unwanted downtimes, thus increasing production
- Minimizing cost
Types of Maintenance
Broadly, there are two main types of maintenance categories that can further be subdivided into various maintenance-type groups.
- Proactive Maintenance or Preventive maintenance and
- Responsive Maintenance or Corrective Maintenance
1. Types of Preventive Maintenance:
Preventive maintenance refers to the fixing of problems before they appear. This means such maintenance prevents the problem. Inspection of equipment at regular intervals to check the machine’s condition and take necessary action is the motto of preventive maintenance.
It involves scheduled inspections, adjustments, and minor repairs designed to prevent equipment failures before they occur. This strategy is proactive, focusing on keeping assets in good working condition. Fig. 1 below shows a typical workflow of the preventive maintenance philosophy.
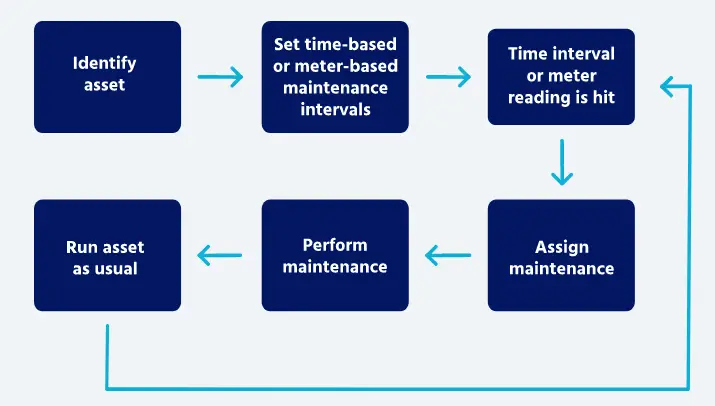
Preventive maintenance is categorized into the following five types
- Time-Based Maintenance (TBM)
- Predictive Maintenance (PDM)
- Failure Finding Maintenance (FFM)
- Condition-Based Maintenance (CBM)
- Risk-Based Maintenance (RBM)
Time-Based Maintenance
Time-based maintenance or TBM calls for maintenance at a fixed time. Normally, taking guidance from the equipment manufacturer’s maintenance plan a fixed interval is scheduled and maintenance work is performed to restore equipment efficiency and performance. Time-based maintenance also requires the replacement of items based on their service life capability.
Predictive Maintenance (PDM)
As the name suggests, this type of maintenance refers to the prediction of the failure probability of equipment and scheduling maintenance to prevent failure. To correctly predict the equipment’s workability and perform predictive maintenance the organization should keep and analyze the following data:
- Equipment history
- All records of downtime, defects, performance, etc
- Equipment condition with respect to working time.
After analysis of the above data and including the experience with similar equipment maintenance dates are fixed.
Failure Finding Maintenance
In failure finding maintenance, potential hidden failures are searched at regular intervals and if discovered are repaired to prevent major breakdowns. So basically this is not a specific type of maintenance but a functional check. Failure to find maintenance increases the system’s reliability.
Condition-Based Maintenance
In the Condition-based maintenance (CBM) strategy, the actual asset condition is monitored and further maintenance requirement is decided. In this type of maintenance, based on visual inspection, scheduled tests, performance data, etc the equipment condition is studied. When some sign of decreasing performance or failure is received, maintenance is scheduled.
Risk-Based Maintenance
Risk-based maintenance considers the philosophy of maintaining the assets carrying the most risk during failure. This philosophy determines the most economical use of the maintenance resources and optimizes the risk of failure. Risk-based maintenance strategy works on the following steps:
- Data Collection
- Risk Assessment and Evaluation of Consequence and Probability of failure
- Ranking of Risks
- Creating an Inspection Plan based on those risk ranking matrices.
- Maintenance planning and Mitigation of risks.
Equipment carrying the greater risk and failure consequences is frequently monitored and maintained. This philosophy and method provide a systematic approach to determining the most appropriate asset maintenance plans in the most economic way.
Advantages and Disadvantages of Preventive Maintenance
Advantages
- Reduced Downtime: Regular maintenance helps identify potential issues before they lead to breakdowns.
- Increased Equipment Lifespan: Regular care can extend the life of machinery and equipment.
- Cost Savings: Preventive measures can save money by reducing the need for major repairs.
Disadvantages
- Time and Resource Intensive: Requires scheduling and can lead to temporary downtime during inspections.
- Over-Maintenance Risk: Performing maintenance too frequently can waste resources if equipment is still in good condition.
Click on the following link to know more details about preventive maintenance: Preventive Maintenance: Definition, Types, Philosophy, Advantages, and Disadvantages
2. Types of Corrective Maintenance
Corrective maintenance is any maintenance task that resolves a problem with a piece of equipment and returns it to operational condition. This is also known as reactive maintenance. Corrective maintenance work can be both planned and unplanned. The following image shows the workflow of typical corrective maintenance philosophy.
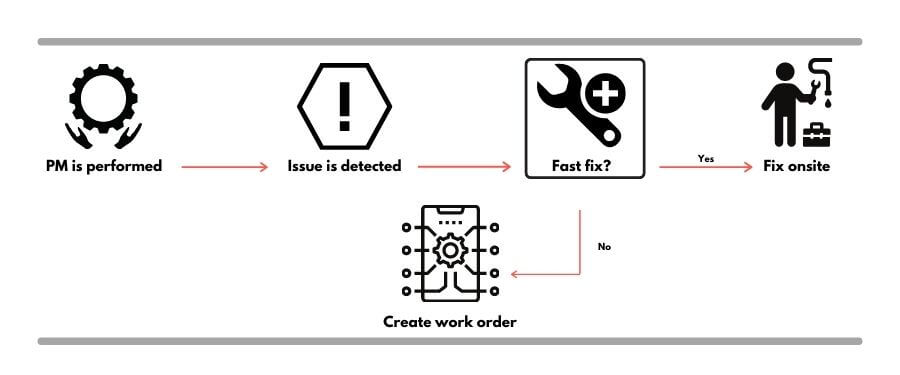
Normally there are three situations that call for corrective maintenance:
- If a piece of equipment or part breaks down
- If any issue is identified during condition monitoring
- If routine inspection discovers any potential fault.
Reactive maintenance, often referred to as “breakdown” or “emergency” maintenance, occurs after equipment has failed or broken down. This type of maintenance is unplanned and is typically initiated in response to a malfunction.
There are two types of corrective maintenance
- Planned or Scheduled corrective maintenance and
- Unplanned or Unscheduled corrective maintenance
Planned or Scheduled Corrective Maintenance
Planned corrective maintenance is the corrective action that is not immediate but planned or scheduled depending on the urgency and nature of the deficiency identified. The risks involved and costs involved are major parameters to determine the planned corrective maintenance schedule. This is also known as deferred corrective maintenance. Example: An AC is not providing proper cooling due to refrigerant gas leakage. So, s work order is created to repair it during the next inspection.
Unplanned or Unscheduled corrective maintenance
Unplanned corrective maintenance needs immediate attention due to some kind of critical failure and must be repaired without delay as it directly relates to cost. This philosophy is also known as Immediate Corrective Maintenance. Example: A pump is inspected and repaired after every 200 hours but it breaks down after 150 hours of operation and it calls for an emergency repair. Similar cases are examples of unplanned corrective maintenance.
Advantages and Disadvantages of Corrective Maintenance
Major advantages of Corrective Maintenance are:
- Minimal planning requirement
- Lower short-term costs
- Simplified maintenance process
- For non-critical equipment, without much impact, this is the best maintenance philosophy and can be cheaper.
The main disadvantages of Corrective Maintenance are:
- Increased Unpredictability
- Paused operations and hence production loss
- The increased cost of maintenance
- Equipment life is not optimized.
- Higher long-term costs
- High safety concerns
Preventive Maintenance vs Corrective Maintenance
Let’s have a look at the major differences between Preventive and Corrective maintenance. For ease of understanding and comparing the differences between corrective and preventive maintenance are tabulated below:
Corrective Maintenance | Preventive Maintenance |
Corrective maintenance refers to maintenance after the failure of an asset. | Preventive maintenance is aimed at preventing failure and is scheduled before equipment failure. |
Corrective Maintenance is a less complex and simple process. | Preventive Maintenance involves proper planning to prevent equipment failure, Hence it is complex. |
Corrective maintenance is normally more expensive as equipment has already failed and needs replacement or extensive repairs. | It prevents equipment failure and thus preventive maintenance is normally less expensive. |
Loss of production and time due to asset failure | The chances of equipment failure are reduced to negligible production and time loss. |
It is only performed when a breakdown occurs. | Preventive Maintenance is performed at regular intervals. |
Corrective Maintenance increases the need for preventive actions. | Preventive Maintenance reduces the need for corrective actions. |
Overall equipment lifecycle and efficiency reduces | Equipment lifespan and efficiency are increased by regular preventive maintenance |
This is hazardous considering the safety | From the safety of employees and working environment considerations, preventive maintenance is better. |
It requires a greater number of employees or technicians to perform corrective maintenance which increases the workload. | The smaller number of technicians perform preventive maintenance decreasing the workload. |
Online Courses on Maintenance Aspects
To learn more about various maintenance aspects, Enroll in the below-mentioned courses, by clicking on the subject:
Very good
Sir i want to learn
Great work man..good for fresh engineers
This is gourab ( chemical engineer)/14 yrs exp in caustic soda plant
Muy buen artículo para ingenieros mecánicos con y sin experiencia en temas de piping.
we want to see detail .
that nice
Hi,
please send me link , where from download pfd notes or book