Valve packing refers to a sealing material or set of materials used to create a tight seal around the stem or spindle of a valve, preventing leakage of fluids or gases through the valve’s bonnet or gland. It is an essential component of valve construction and plays a crucial role in maintaining the integrity of the valve.
Valve packing is commonly used in certain types of valves where a dynamic or static seal is required around the stem or spindle. The following types of valves typically utilize valve packing:
- Globe Valves: Globe valves often require valve packing to seal around the stem. This packing ensures a tight seal between the valve stem and the valve body, preventing fluid or gas leakage when the valve is closed.
- Gate Valves: Gate valves may utilize valve packing to provide a seal around the stem or spindle. The packing helps to prevent leakage when the gate valve is closed.
- Ball Valves: While many ball valves are designed with a stem sealing mechanism such as O-rings, some larger or high-pressure ball valves may incorporate valve packing to provide an additional seal around the stem.
- Plug Valves: Plug valves may employ valve packing to seal around the plug or tapered cylindrical core. The packing helps to prevent fluid or gas leakage through the valve when it is closed.
- Diaphragm Valves: Diaphragm valves typically use a flexible diaphragm as the main sealing element. However, certain designs may incorporate valve packing to seal around the stem or spindle.
- Butterfly Valves: Most butterfly valves utilize a resilient seat for sealing. However, some large or high-pressure butterfly valves may incorporate valve packing around the stem or spindle as an additional sealing mechanism.
It’s important to note that not all types of valves require valve packing. Some valves, such as ball valves with stem seals or check valves, may rely on other sealing mechanisms and not require traditional valve packing. The specific design and construction of the valve will determine the need for valve packing.
Components of Valve Packing Assembly
The valve packing assembly typically consists of several components (Fig. 1) that work together to create a seal around the valve stem or spindle. The specific components may vary depending on the valve design, but here are the common components found in a valve packing assembly:
Packing Rings or Chevron Sets:
The packing rings or chevron sets are individual rings or sets of rings made from the packing material. They are stacked within the packing gland and create a barrier around the stem or spindle. These rings provide the sealing action when compressed against the stem.
Packing Gland:
The packing gland, also known as the stuffing box, is a housing that contains packing rings or chevron sets. It is typically a cylindrical or box-like structure surrounding the stem or spindle, located within the valve bonnet or gland. The packing gland provides support and compression for the packing material.
Packing Gland Bolts:
The packing gland bolts are used to secure the packing gland to the valve bonnet or gland. They hold the packing gland in place and provide the necessary compression on the packing rings.
Gland Follower or Lantern Ring:
In some valve designs, a gland follower or lantern ring is included in the packing assembly. This component is typically placed between the packing rings and the packing gland. It helps distribute the compression force evenly on the packing rings and allows for the injection of lubricants or flushing fluids into the packing chamber.
Packing Gland Nut:
The packing gland nut is a threaded nut located on the top of the packing gland. It is used to adjust the compression force on the packing rings. By tightening or loosening the packing gland nut, the compression on the packing material can be increased or decreased.
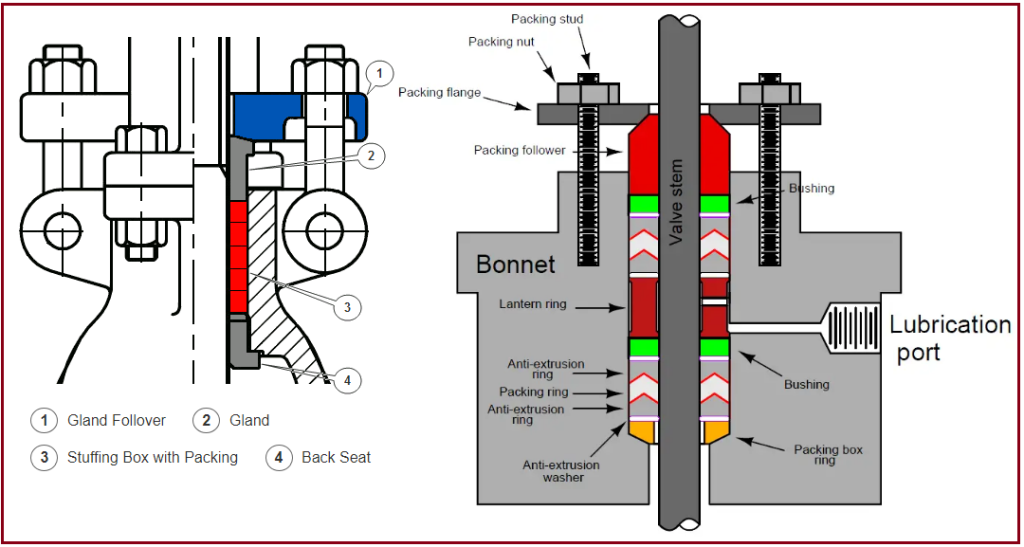
Materials for Valve Packing
Valve packing or valve sealing is typically made of flexible and resilient materials that can withstand operating conditions and provide effective sealing. Common materials used for valve packing include:
Graphite:
Graphite packing is widely used in valve applications. It offers excellent resistance to high temperatures, chemical corrosion, and abrasion. Graphite packing is suitable for various types of valves, including high-pressure and high-temperature applications.
PTFE (Polytetrafluoroethylene):
PTFE packing, also known as Teflon packing, is popular for its low friction properties and resistance to chemicals. It provides effective sealing and is often used in valves handling corrosive fluids or gases.
Flexible Graphite:
Flexible graphite packing is a combination of graphite and other reinforcing fibers. It offers enhanced flexibility, making it suitable for valves with dynamic or moving parts. Flexible graphite packing provides reliable sealing under different conditions.
Synthetic Fiber:
Various synthetic fibers, such as aramid, acrylic, or fiberglass, are used as packing materials in valves. These fibers are resistant to wear, chemicals, and high temperatures, providing effective sealing and durability.
Factors for Selecting Valve Packing Materials
The selection of valve packing depends on factors such as
- The type of fluid or gas being handled,
- Temperature range,
- Pressure range,
- Leakage requirements,
- Frictional and Wear properties of valve sealing material,
- Maintenance and operating costs, and
- other environmental conditions.
The packing material should be compatible with the fluid or gas and capable of maintaining a reliable seal over the valve’s operational lifespan.
Proper installation and periodic maintenance of valve packing are important to ensure optimal performance and prevent leakage. This may involve adjusting the packing gland or replacing the packing when necessary to maintain a tight seal.
Characteristics of Valve Packing Materials
Valve packing materials should exhibit various characteristics to make them suitable for different applications and operating conditions. Here are some common characteristics of valve packing materials:
Sealing Capability:
The primary function of valve packing is to provide a reliable seal to prevent leakage. The packing material should possess excellent sealing capability, effectively preventing the flow of fluids or gases through the valve. They must be elastic and deformable.
Compatibility:
Valve packing materials should be compatible with the fluid or gas being handled. They should resist chemical attack and corrosion, ensuring long-term sealing performance without degradation or damage. This means they should be chemically inert.
Temperature Resistance:
Valve packing materials should withstand the temperature range of the application without losing their sealing properties or deforming. They should be capable of maintaining their integrity and sealing effectiveness at high or low temperatures.
Pressure Resistance:
Valve packing should be able to withstand the pressure exerted on the valve without extrusion or failure. The packing material should have adequate strength and resilience to handle the pressure conditions of the specific application.
Low Friction:
Packing materials with low friction properties help minimize stem or spindle friction during valve operation, reducing wear and extending the valve’s lifespan. Low-friction packing materials also assist in smooth and easy valve actuation.
Wear Resistance:
Valve packing materials should be resistant to wear, especially in applications with frequent valve cycling or abrasive media. They should be capable of maintaining their sealing properties over an extended period, minimizing the need for frequent maintenance or replacement.
Chemical Resistance:
Packing materials should be resistant to the corrosive effects of the fluids or gases they come into contact with. They should be able to withstand the specific chemical properties of the media without degradation or failure.
Flexibility:
Flexible packing materials allow for proper compression and adjustment within the packing gland, ensuring a tight seal around the valve stem or spindle. Flexibility also helps accommodate the movement of the valve during operation.
Ease of Installation and Maintenance:
Packing materials should be relatively easy to install, adjust, and replace when necessary. Proper installation and periodic maintenance are crucial for maintaining optimal sealing performance and extending the life of the valve. Additionally, they must be durable enough.
Types of Valve Packing
There are several different types of valve packing available, each with its own unique characteristics and applications. The choice of valve packing depends on factors such as the type of valve, operating conditions, fluid or gas being handled, and the desired sealing properties. Here are some common types of valve packing:
Braided or Compression Packing:
Braided packing is made by weaving together strands of packing material, such as graphite, PTFE, aramid, or synthetic fibers. It is a versatile packing option and is suitable for a wide range of valve applications. Braided packing provides effective sealing, is relatively easy to install, and can handle various temperatures and pressures.
Graphite Packing:
Graphite packing is widely used in high-temperature and high-pressure applications. It offers excellent thermal and chemical resistance, low friction, and good resilience. Graphite packing is known for its ability to handle extreme temperatures and is commonly used in valves for steam, chemicals, and high-temperature fluids.
PTFE (Teflon) Packing:
PTFE packing is made from polytetrafluoroethylene and is known for its chemical resistance and low friction properties. It is suitable for valves handling corrosive chemicals, acids, or gases. PTFE packing provides reliable sealing and can handle a wide temperature range.
Flexible Graphite Packing:
Flexible graphite packing consists of expanded graphite material. It offers excellent flexibility, resilience, and sealing capabilities. Flexible graphite packing is commonly used in valves that require frequent cycling or movement due to its ability to maintain a tight seal even with stem or spindle motion.
Synthetic Fiber Packing:
Synthetic fiber packing, such as aramid, acrylic, or fiberglass packing, is known for its strength and durability. It offers good resistance to wear and is suitable for valves with abrasive fluids or high-pressure applications.
Expanded PTFE (ePTFE) Packing:
Expanded PTFE packing is a versatile option with excellent chemical resistance and low friction. It is suitable for a wide range of fluids, including corrosive chemicals, gases, and hydrocarbons. ePTFE packing provides effective sealing and can handle various temperatures and pressures.
Carbon Fiber Packing:
Carbon fiber packing is designed for high-temperature applications, particularly in valves handling aggressive chemicals or gases. It offers good chemical resistance, high thermal stability, and low friction properties.
Hydraulic Packing:
V-ring packing is the most common type of hydraulic packing. They are used when no fluid leakage is acceptable. In general, they are made of rubber or other polymer/plastic materials. The main features of this type of valve packing are:
- Less friction
- Chemically resistant
- Lubricant requirements can be eliminated
- Good temperature range.
There are four styles of Valve Packing. They are:
- Twisted Packing – Used for general utility or emergency purposes where the packing space is small
- Square-Braid Packing – Widely used for high-pressure valve-stem packing and high-speed reciprocating services.
- Braid-Over-Braid Packing – Applications found for valve stems with out-of-square cross sections.
- Interlocking Braid Packing – This type of valve packing is ideal for applications around small-diameter valve stems. Fig. 2 (Image Courtesy: https://www.fossilconsulting.com/2022/09/23/valve-packing-understanding-packing-for-maintenance/) below shows these styles.
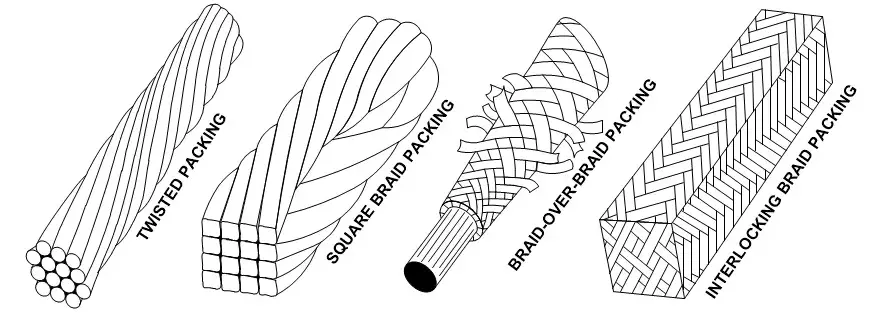
What is Valve Packing Gland
The valve packing gland, also known as the stuffing box, is a component of a valve that houses the packing material and provides compression to create a seal around the valve stem or spindle. It is typically a cylindrical or box-like structure located around the stem where it passes through the valve bonnet or gland. The packing gland contains a threaded or bolted arrangement that allows for adjustment and tightening of the packing material.
The primary function of the valve packing gland is to provide a controlled compression force on the packing material, ensuring a tight seal around the stem or spindle while still allowing for the smooth operation of the valve. By tightening the packing gland, the packing material is compressed against the stem, creating a seal to prevent fluid or gas leakage through the valve bonnet.
What is Valve Packing Nut?
The valve packing nut is a component typically found on the top of the valve stem or spindle, above the packing gland. It is a threaded nut that can be tightened or loosened to adjust the compression force on the packing material.
The valve packing nut serves two main purposes. Firstly, it provides additional compression force to the packing material, further ensuring a tight seal around the stem or spindle. By tightening the packing nut, the packing material is compressed against the packing gland, enhancing the sealing effectiveness.
Secondly, the packing nut allows for the adjustment or replacement of the packing material. Loosening the packing nut enables access to the packing gland, allowing for adjustments to the packing material or the insertion of new packing material when maintenance or replacement is necessary.
The packing nut is typically designed to be easily accessible and adjustable, often using a wrench or spanner to tighten or loosen it. Proper adjustment and periodic maintenance of the packing nut are important to maintain the integrity of the seal and prevent leakage in the valve.
Both the valve packing gland and packing nut are integral components of the valve assembly, working together to ensure an effective and reliable seal around the stem or spindle, thus preventing fluid or gas leakage through the valve.
This is a great overview
PTFE (Teflon) Packing is not preferred over Graphite at moderate and higher temperatures and pressures.