To protect surfaces and improve sliding properties, wear pads are used in industrial applications from earlier days. Also known as slider pads, wear pads increase the wear resistance capability and provide higher strength. In this article, we will explore more details about Piping Wear Pads.
What is a Pipe Wear Pad?
A pipe wear pad is a type of pipe support used to isolate the main pipe surface from direct rubbing with structural surfaces. By installing these on outside pipe surfaces, wear pads for pipe reduce the metal-on-metal damage. Piping wear pads basically replace the contact point from the main pipe to the wear pad material.
What are the Materials used for Pipe Wear Pads?
Wear pads for pipes can be made of metallic or non-metallic/composite materials. Depending on the requirement and temperature of the piping surface, the wear pad material is decided. Common wear pad materials for piping systems are:
- Carbon Steel (Used with CS pipes)
- Stainless Steel (Used with SS piping)
- Composite (FRP, GRP, etc) wear pads (Can be used with metallic and non-metallic pipes)
Purpose/Functions of Pipe Wear Pads
As the outer surfaces of the piping system are constantly experiencing corrosion, wear, and tear they can be weakened easily. Over time, these can even cause the failure of the components leading to plant shut-down or major hazards. In such a scenario, piping wear pads are one of the easy solutions to reduce corrosion and increase pipe system longevity. The main functions that pipe wear pads serve are:
1. They eliminate metal-to-metal damage. There are two modes of damage that can happen:
Metal-to-metal wear damage by rubbing caused by thermal and pressure fluctuations. Wear pads fit on the pipe’s outer surface on support locations and preserve the pipe material.
Galvanic Corrosion due to dissimilar metals: Galvanic corrosion by the electrochemical reaction can occur when dissimilar metals remain in contact with each other. Pipe wear pads isolate dissimilar materials and discourage galvanic corrosion.
2. Wear pads eliminate the possibility of crevice corrosion of the piping system. When a pipe moves over the structure, the motion can pull off the pipe’s outer layer. So, grooves are created for microbes to creep in, resulting in crevice corrosion by bacteria. Wear pads for piping systems to stop these corrosive cells to form by absorbing the surface impact themselves and safeguarding the pipe material.
3. As wear pads are directly fixed on the pipe, they displace along with the pipe without leaving any scope for dust or grit accumulation on the pipe surface which in turn avoids damages that may be caused by dust or grit particles.
4. Installing composite wear pads does not require welding on the pipe which in turn keeps the pipe system fully intact. They are usually fixed to pipes by extremely strong epoxy adhesives.
5. Composite wear pads absorb the frictional forces within then keeping the parent pipe material safe.
6. Wear pads safeguard the piping systems from damaging vibration effects by providing a damping effect and increasing stiffness. Pipe wear pads help the parent pipe material from banging on the support structures.
So, in a nutshell, wear pads drive long-term performance by reducing corrosion, and wear, and thus preserving pipes.
Installing Pipe Wear Pads
Metallic wear pads are welded with pipe similar to reinforcing pads. Composite wear pads are bonded with pipe using epoxy adhesives. Wear pads can fully or partially enclose the pipe. The image in Fig. 1 shows a typical wear pad used in piping systems.
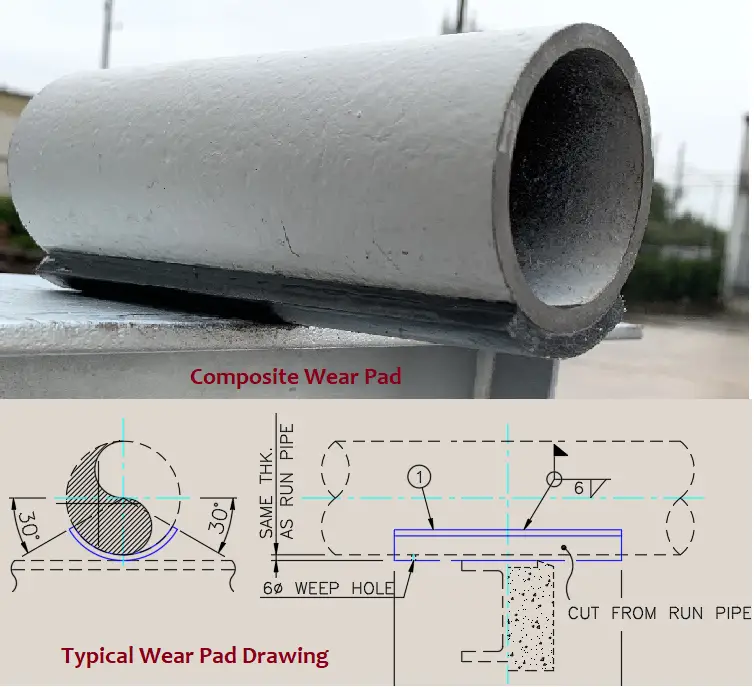
Length of Wear Pads
The minimum length of pipe wear pads is calculated as follows:
- For wear pads with line stops the minimum length of wear pad=structure (beam) width+2*each line stop member dimension+2*one side gap for line stop+50 mm.
- For wear pads without line stops the minimum length of the wear pad= structure (beam) width +maximum thermal movement at that support location+50 mm.
When to use Wear Pads?
Pipe wear pads are extensively used during the following situations:
Use of Metallic Wear Pads:
- Metallic wear pads are used for strengthening thin-walled pipes to avoid local damage in support locations.
- If piping support is experiencing a relatively higher load then wear pads are suggested to safeguard the pipe from support load reaction.
- Wear pad supports are normally suggested for line stops with relatively high loads. In many consultancy organizations, it is a standard engineering practice to use wear pads for all pipe supports of pipes exceeding 24-inch size.
Use of Composite Wear Pads:
Composite wear pads are widely used for
- reducing corrosion.
- damping vibration.
Difference between RF Pad and Wear Pad
The main differences between reinforcement pads and wear pads are
RF pads or Repads are used for pressure integrity. When a piping system is not able to withstand pressure stresses locally due to removing metal for branch connection or high stresses, Repads are used to provide local strengthening. Reinforcing pads are usually provided in equipment nozzle connections, pipe branch connections, or trunnion connections.
On the contrary, wear pads are used as pipe supports. They provide wear resistance and high strength to pipes in support locations.
Normally wear pads for supports are rolled from the pipe so long as the wear pad thickness is acceptable.
I was curios to know if there’s a pipe size limitations for rolling wear pad! Thanks.