A Bolted tank is one of the atmospheric storage tanks that also play an important role as an alternative to the Welded Tank. These tanks are made from factory-manufactured section staves (known as a Shell-Course in Welded Tank) that have been manufactured in a quality-controlled factory setting. Bolted steel tanks have been in use for more than fifty years. So, the design and construction of bolted tanks are already tried and proven. They provide a long-term, cost-effective solution for a wide variety of uses.
Under certain conditions, a bolted tank is more often selected
- for conditions in which there is no provision to allow hot-work in order to repair/replace an existing tank or built a new one, and
- when there is a concern about the limitations of the working area from the tank user.
Applications of Bolted Tanks
These tanks are commonly found in industrial, commercial, residential applications ranging in size from a few 100 bbls to 10,000 bbls. The most common applications of bolted tanks are listed below:
- Water Sector: Storage of Drinking or Potable Water, Rural Water Districts, Subdivision/Private Water Systems, Water Storage at Municipality, Fire Protection Systems, Waste Water, Finish Water, Process Water, Disinfection, Filtration, and Sludge Storage.
- Food Industry: Salt factories, Flour & Sugar industries, Meals: Soybean, Bone, Fish, Corn, Meat, Blood, Dried Distillers Grain, Starch, Milk Solids, etc
- Mineral Storage: Talc, Lime, Bentonite, Calcium Carbonate, Alumina, Gypsum, Silica, Coal, Phosphates, etc
- Petroleum Products: Drilling Fluids, Crude Oil Storage, Mud, Fuel Oil, etc
- Chemical Storage: Carbon Black, Cement, Activated Carbon, Sodium Nitrate, Fly Ash, Urea Pellets, Sodium Carbonate, Glass, Soda Ash, Potassium Carbonate, etc
- Storage of Bio-Fuels: Caustics, Glycerin, Syrup, Bulk Bio-Diesel, Methanol, Yeast Tank, Raw Feedstock Oils, etc.
- Power generation Industry: Treatment Bins & Silos, Coal Storage, Desulphurization Systems, Fly Ash Storage, etc
In most sectors of the oil production industry, Bolted Tank can also be used to store crude petroleum and other liquids with or without internal piping connections.
In this article, we will study the design and installation of Bolted Tanks that was carried out by the Author during on-site work at South Sumatera, Indonesia.
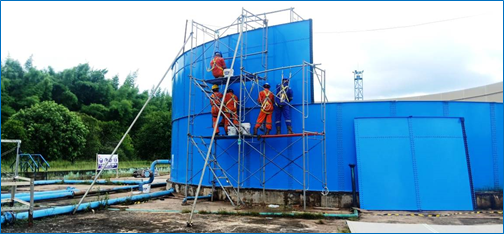
Bolted Tank Design Standard
The API Specification 12B by American Petroleum Institute covers the material, design, fabrication, and testing requirements for vertical, cylindrical, aboveground, closed, and open-top bolted tanks in various standard sizes and capacities.
Generally, these tanks are made for tanks that have internal design pressure approximately atmospheric of:
- 3 oz/in.2 for tanks with a diameter of 15 ft, 45/8 in. and less;
- 2 oz/in.2 for tanks with a diameter of 21 ft, 61/2 in. and 29 ft, 85/8 in.;
- 1 oz/in.2 for tanks with a diameter of 38 ft, 75/8 in. and greater.
API Specification 12B Tanks are divided into several capacities based on bolted tank roof diameter as follows:
- Low Capacity Tanks – Bolted Tanks with a roof diameter under 29 ft, 85/8 in. (100-bbl, 200-bbl, 250-bbl, high 500-bbl, 750-bbl, low 500-bbl, high 1000-bbl, and 1500-bbl capacity) are self-supporting.
- Medium Capacity Tanks – Bolted tanks with a roof diameter of 29 ft, 85/8 in. (low 1000-bbl, 2000-bbl, and 3000-bbl capacity) that are furnished with a structural- or pole-type center support, including a rafter support ring.
- High Capacity Tanks -Bolted Tanks with a roof diameter greater than 29 ft, 85/8 in. (5000-bbl and 10,000-bbl capacity) that furnished with pole-type center support.
Advantages of Bolted Tanks
Bolted Tanks offer various advantages as mentioned below:
Precision in Fabrication
In some quality-controlled factories, bolted tanks are manufactured from superior raw material in accordance with API Specification 12B including cutting, punch press, rolling, bending-into-shape, and applied superior powder coating on the stave surface for both internal or external side.
Ease of Assembly
Unlike a large field-storage tank that assembles on-site through welding, with strict erection method, a lot of time of inspections, and coating application then the bolted tank can be installed in any situation and arrive at the job site as a ready-to-assemble tank. It makes the erection and construction period very short.
Another important thing that bolted tanks can be erected and bolted up to second rings manually by scaffolding because of its less-weight staves and appurtenances compared to a welded tank that usually uses cranes.
Durability Coating
Surface preparation (SSPC-SP10) and coating application can be applied in the factory-manufactured tanks in a good quality-controlled environment prior to transporting to the job site.
This is very different from large-filed welded tanks that are required to be painted or coated at the job site until the erection/installation is completed.
One of the best coatings used in API Specification 12B Tank is powder coating. These coatings are applied for both internal and external surfaces of each part from 8 to 10 mils of DFT.
Bolts of staves also coated by mechanically zinc-coated or hot-dip galvanized in manufacturing facility depends on client requirements.
Flexibility of Construction
Bolted tanks can also be built over a concrete ring wall (Fig.2A), Concrete Slab (Fig.2B), and Steel Retaining Ring Foundation (Fig.2C).
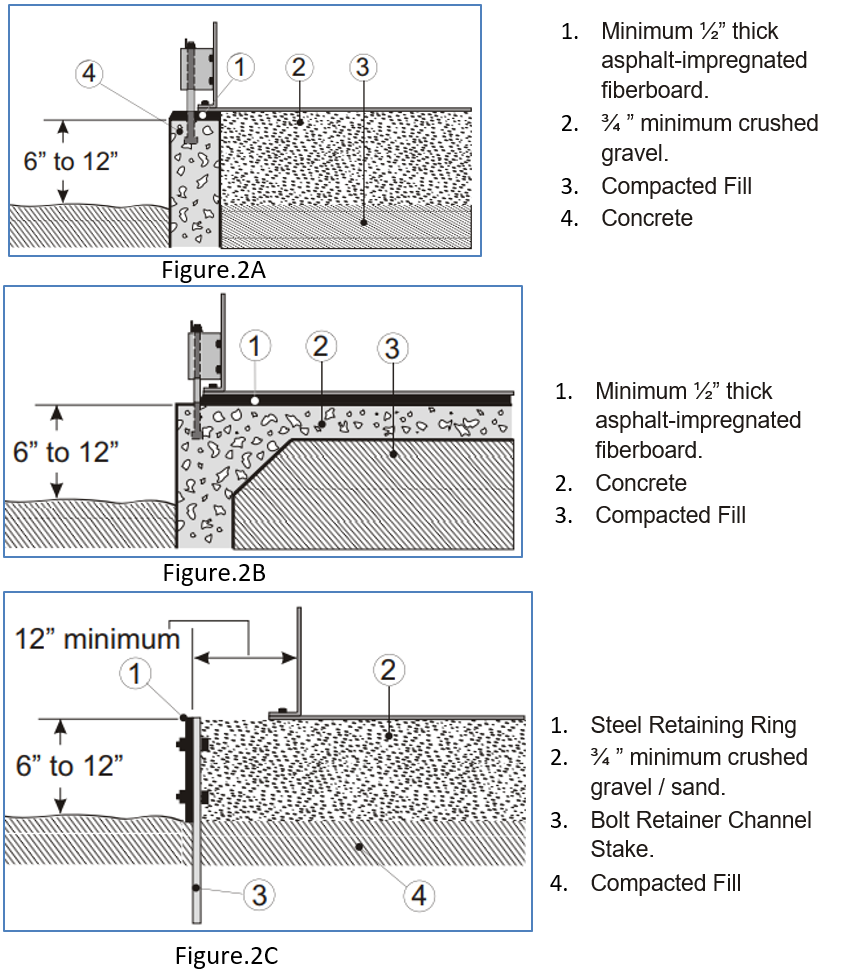
Easy Maintenance of Bolted Tanks
Any damaged part caused by corrosion on panel/section of staves, nozzle neck, clean-out, and gaskets can easily be unbolted and replaced or repaired on the job site.
Bolted Tanks are subject to leaks but can be simply maintained and repaired. In case of any leakage at bolt connections during the hydro test, it is easier for an operator to detect leaks and then re-tightening the bolts using proper tools such as Torque Wrench.
Tank in Box? Yes
Since bolted tanks are shipped disassembled in sections, they are more compact to transport to the laydown area than the large shell-course of a field-welded tank, and reducing costs.
These staves and accessories usually are packed in banded pallets with ranging sizes and transported by container.
Disadvantages of Bolted Tanks
There are some disadvantages while choosing Bolted Tank as per API Specification 12B:
- Anchorage for overturning loads and
- Seismic design
They are outside of the scope of API Specification 12B Tanks. Therefore, engineering judgment shall be considered to refer to another storage tank code calculation such as Annex E of API Standard 650.
Bolted Tank Design
Basic Tank Configuration (Bolted Tank Parts)
Bolted Tank configuration depends on the capacity of each tank. Refer to Fig. 3 below explaining the parts of a bolted tank.
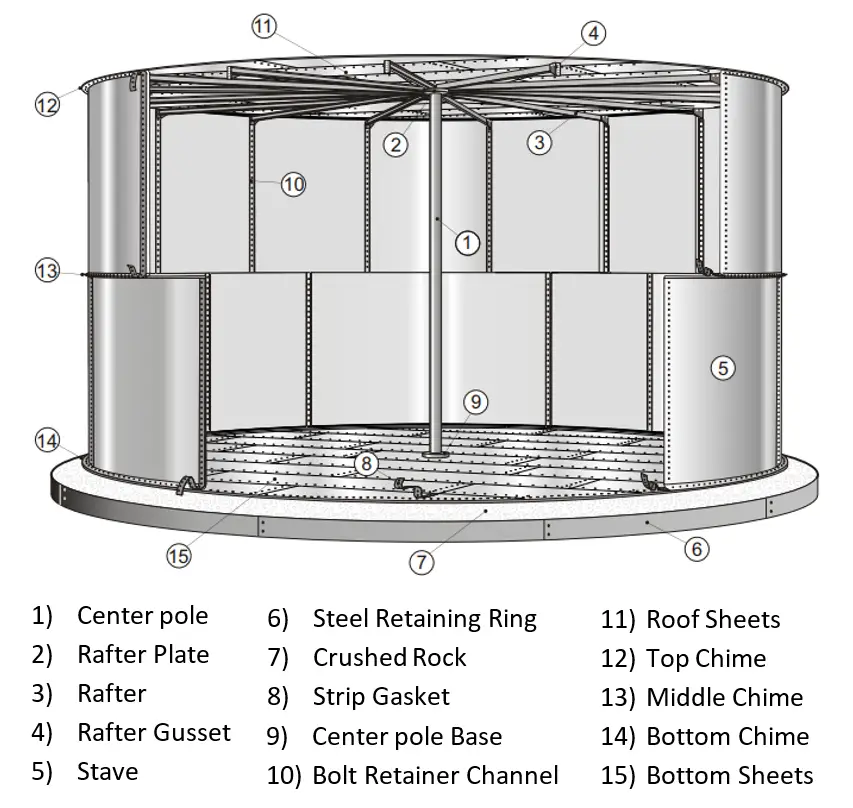
Material of Construction of Bolted Tanks
Bolted Tanks are mostly made of steel that is why it is also known as bolted steel tanks. Typical materials used in bolted tank design are
- Staves (Shell Sheets): ASTM A1011 Grade 40 (not less than 36,000 psi of SMYS)
- Structural shapes: ASTM A36
- Center column: ASTM A53 Grade A
- Man-way & Cleanout: ASTM A1011 Grade 40
- Piping: ASTM 106 Grade B
- Flange: ASTM A105
- Fitting: ASTM A234 WPB
- Gasket: Buna Nitrile, Epichlorohydrin, and EPDM strip
- Bolt/Nut: ASTM A307 Grade A / SAE Grade 5 / SAE Grade 2.
Size of Bolted Tanks
Bolted Tank designed per API Specification 12B shall conform to the sizes and dimensions below:
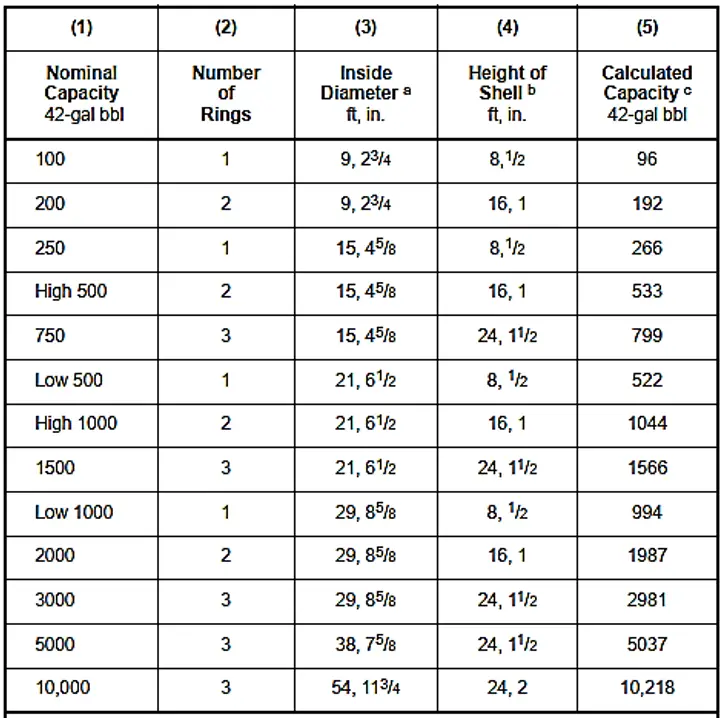
Details of Bottom, Shells, and Roofs
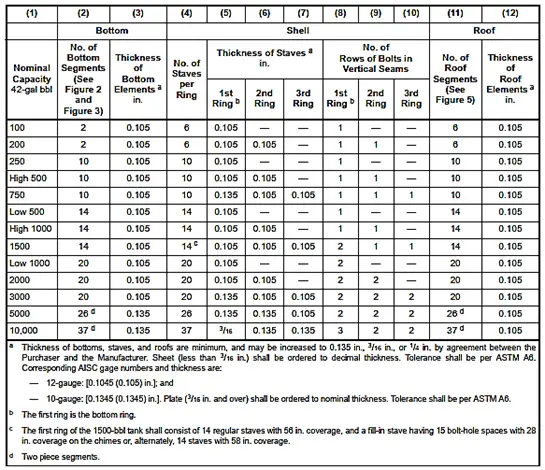
Bolted Tank Construction
In this section, we will briefly discuss the installation sequence for a typical Bolted Tank.
Step 1: Preparation of Bolted Tank Foundation
The first stage in bolted tank construction is to prepare the foundation. Civil team design the foundation based on soil investigation and construct as per design drawings.
Levelness of the foundation shall be check to provide an easy fitting bolted tank.
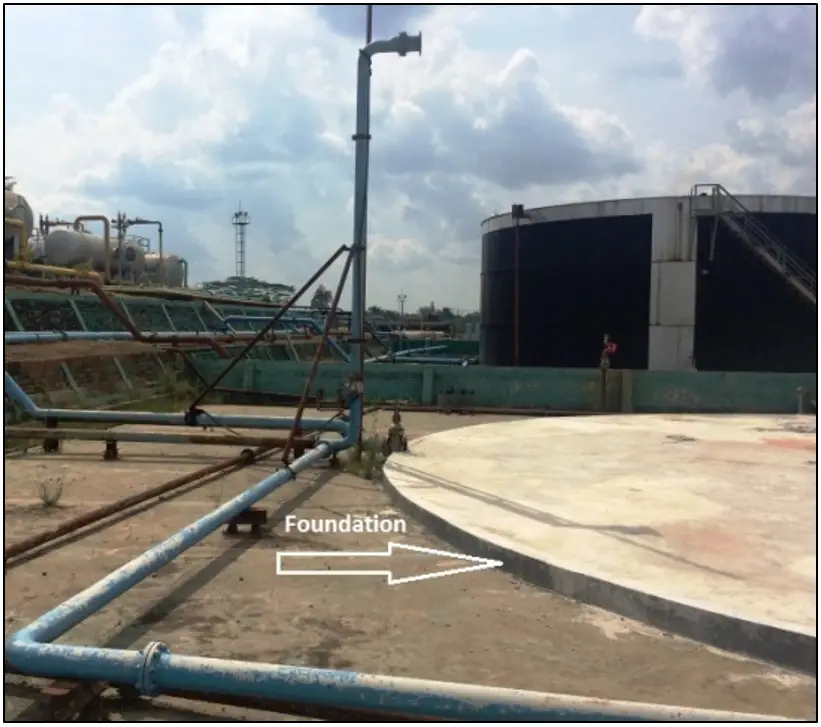
Step 2: Assemble the Bottom (Tank Floor)
In this step the following activities are performed
- Spread the Impingement Fibreboard
- Spread and assemble the Bottom Staves from the center of the tank
- Rubber the Bottom with Strip Gasket until complete
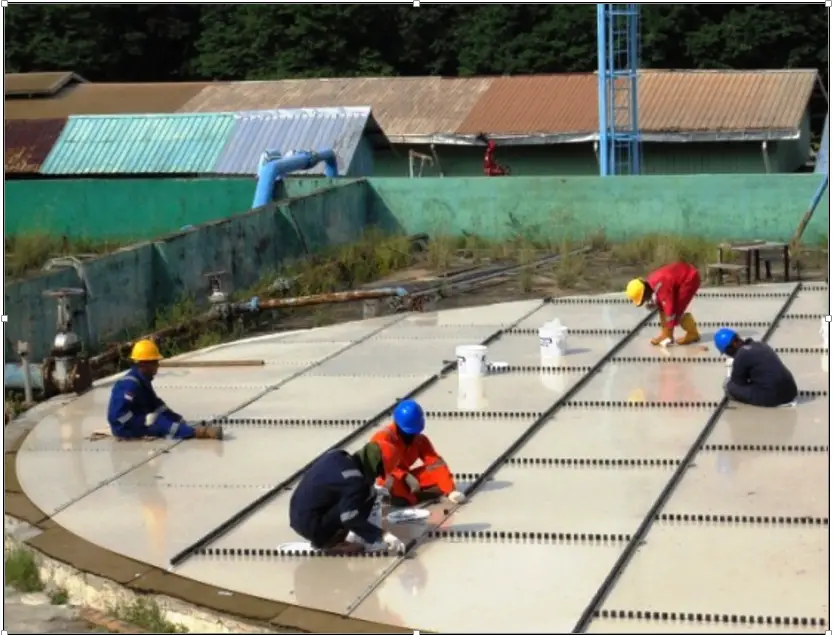
Step 3: Assemble the Staves and Rubbering with Strip Gasket
In this stage, the staves are assembled to give the tank shape. It is a good practice that the first stave to be installed on tank bottom is a stave fitted with a access man-way or clean-out.
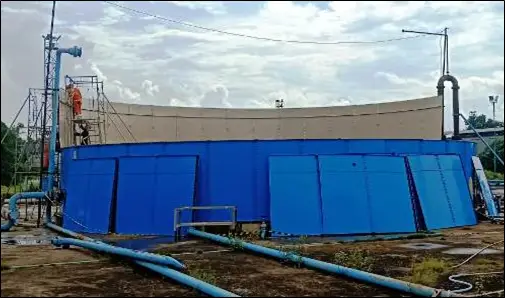
Each panel is bolted together using custom made rubber gaskets to prevent any leakage.
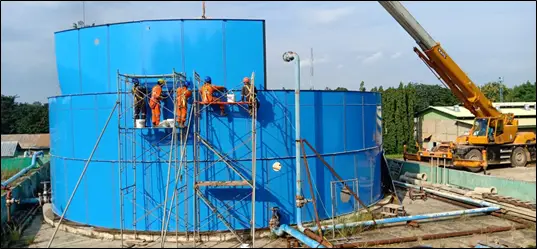
Step 4: Positioning the Center of Column Base Sleeve
Internal columns shall be guided or supported to resist lateral loads (remain stable) even if the roof components are not specified to be designed for the seismic loads, including tanks that need not be designed for seismic ground motion.
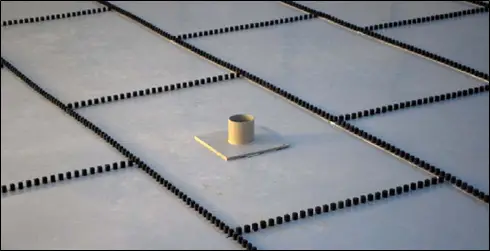
Step 5: Assemble and Positioning the Center Pole of Column Pipe
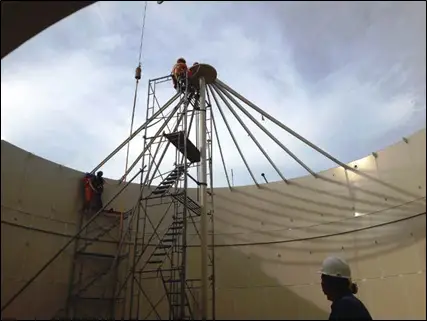
Step 6: Assemble the Roof Deck
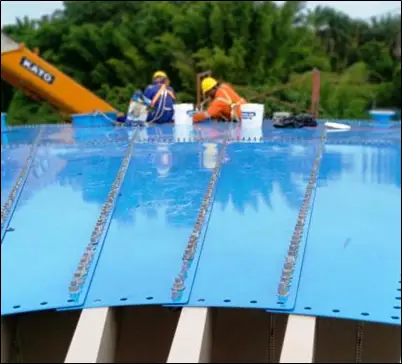
Step 7: Installation of Internal Weir and Skimming Pipe
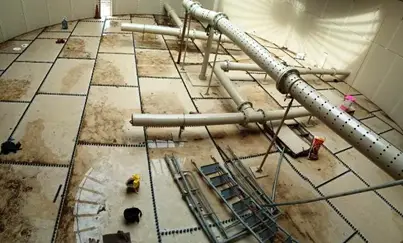
Step 8: Complete Installation until Finish
Complete the Bolted Tank installation prior to installing the appurtenances of Bolted Tank as mentioned below.
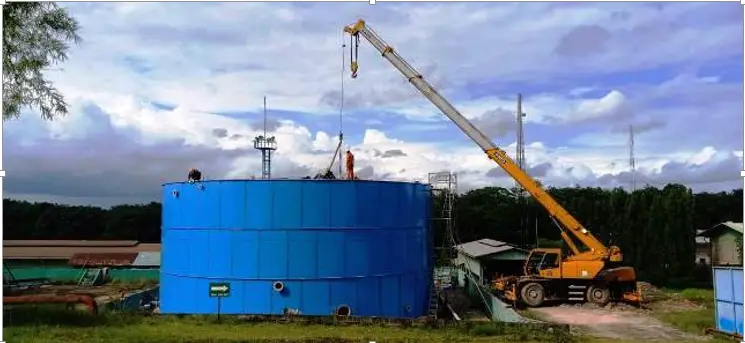
Fig. 15 shows the general arrangement drawing of the above Bolted Tank.
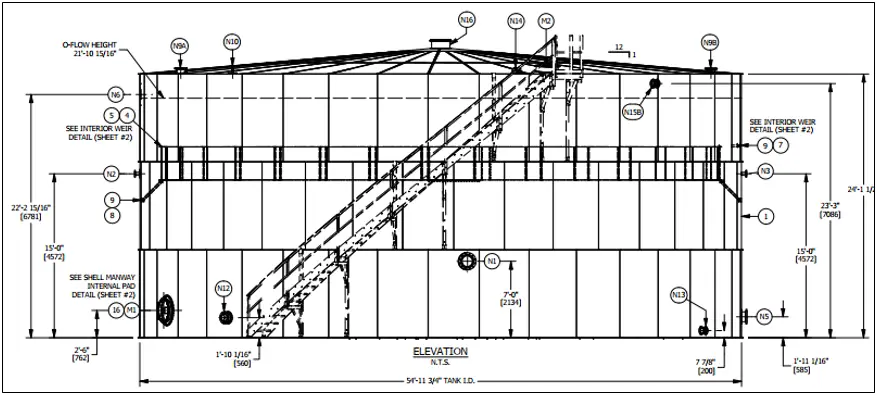
Appurtenances of Bolted Tanks
The following accessories or associated items are relevant to bolted tank design and construction. Learn more according to the list below:
- Vent / Breather Valve: to prevent overpressure and vacuum conditions by allowing atmospheric air to flow into the tank.
- Pressure Vacuum Relief Valve: can act as Safeguard. However, if the tank contains hazardous material, these types of safeguards should only be considered as a last line of defense against the malfunction of other safeguards in the hierarchy. For more details, please refer to API 2000.
- Roof Hatch / Gauge Hatch: which permits the cover to lift under abnormal internal pressure.
- Flame Arrester (Vertical, In-line type): to prevent flames entry into the tank in the event of external fire
- Cathodic Protection: Sacrificial anode c/w Portable Reference and Test Point to protect the tank from corrosion.
- Internal Skimming Pipe: Optional, depending on Process Requirement. Install inside the tank; employed as oil & water separation.
- Outside Tank Ladder & Spiral Stairway
- Roof Walkways and Handrails
- Access Man-way & Clean-out
- Liquid Level Indicator: to monitoring the level of liquid inside of the tank, include LLL, Normal, and HLL.
- Foam Chambers: to prevent flame by delivering foam to the surface of flammable.
- Overflow Pipe: to prevent spillage by overfilling. It should be installed at the highest point of the tank shell at least as big as the largest inlet pipe, or larger if there is more than one inlet piping system.
- Skimming Pipe Supports and U-bolt
- Nozzles and Connection Pipes: include Flange, Nozzle Neck, and Bolting.
- A nameplate (API Specification 12B Monogram).
Bolted Tank Manufacturers
There are a number of manufacturers who specialize in the manufacture of the bolted tanks made from the stave.
The following below are some of the suppliers widely known worldwide
- Superior Tank Co, Inc.
- CST Bolted Tanks
- American Tank Company, Inc.
- Tank Connection
- TARSCO-TF Warren Group
- National Storage Tank
- United Tank Services
- Center Enamel
Bolted Tanks vs Welded Tanks
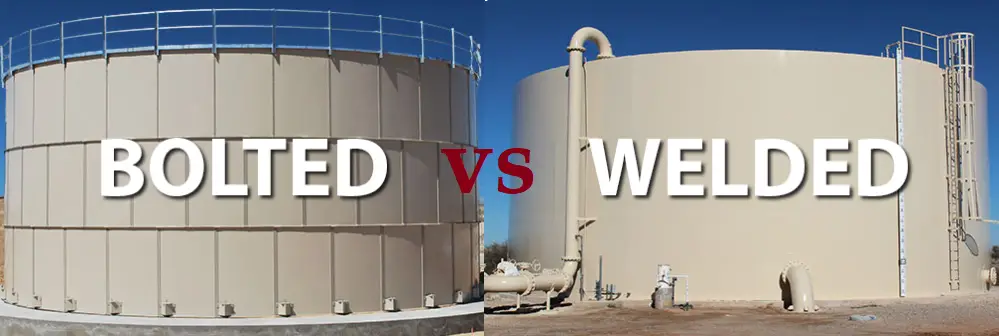
The major differences between bolted tanks and welded tanks are tabulated below:
Bolted Tank | Welded Tank |
Bolted Tanks are designed as per API Specification 12B / AWWA D103 | Welded tanks are designed as per API Standard 650 / API Standard 620 |
Quick Installation is the main feature of bolted tanks. | Welded tanks need more Installation time |
Highly Flexibility in bolted tank installation | Installation of welded tanks is less flexible |
Bolted tanks provide easy maintenance and Repair | The maintenance and repair work on welded tanks are comparatively Difficult |
Bolted tanks provide a Cost Effective Solution | Welded tanks are relatively Costlier |
References and Further Studies
- API Specification 12B – Specification for Bolted Tanks for Storage of Production Liquids
- Storage Tank and Equipment – Bob Long & Bob Garner
- www.gctanks.com
- https://superiortank.com/
For more details about Storage Tanks, you may refer to these following articles:
https://whatispiping.com/brief-presentation-storage-tanks
https://whatispiping.com/storage-tank-failure-examples-causes-and-prevention
https://whatispiping.com/difference-between-api-650-and-api-620
i learned that it’s highly help me
It is glad to know if this article is beneficial to you.
Any bolted tank design engineer plz contact on 8860602980
Where do you find the torque spec for the bolted 5000bbl tank?
Hi,
You can refer to the manual book from Bolted Tank supplier; Superior Tank or CST.
Very nice information for easy way thanks lusi
My application is, first storing the normal water then heating it up to 90 Degree C by feeding the steam.
Is this tank works for it
Hi Srini,
There are no specific rules in API 12B which regulate the allowable operating temperature, but this can be checked together with the rules of API 650 Appendix M.
This is a good learning point on API 12B tanks; however, I have a question: since this is a bolted tank and the specification didn’t mention welding, how will the access ladder be attached to the tank / tank shell? I am curious to learn.
Thanks for your assistance.
Hi Samuel,
The exterior ladder was attached to the tank shell using the same bolt at the intersection of each shell/course with additional legs. Moreover, you may check the type of ladder depending on the total height of the tank. Sometimes, use only a monkey ladder with a cage, etc.