What is Design Checking?
Design Checking or checking of design is a process of validating a design and/or a design calculation to ensure that it is error-free and of good quality and is good for engineering and/or fabrication or whatever the end-use of it is.
Checking is also a process of value addition in terms of applying good engineering practices, aesthetics, reduction in cost and thereby providing better value to the client.
A design checklist is prepared for each important design process to aid in the design checking process.
Why design checking is required?
A quality check in design is required to
- Ensure that the engineering deliverables (drawing, calc, etc.) are error-free.
- Ensure that it is in line with the appropriate design standards and codes
- Ensure that there is consistency in the design approach and aesthetics across units in the design
- Ascertain optimization with respect to design and cost.
- Reduce field rework
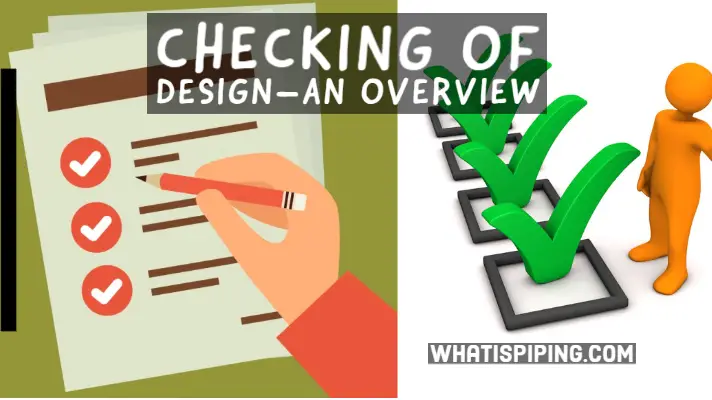
What do we check against?
- Check calculations against applicable codes and standards
- Check design against control documents (P&IDs, Line List, General Arrangement Drawings, vendor drawings, design standards, checklists, etc.)
- Controlled issues of stress isometrics
- Statutory norms and regulations, eg. OISD, IBR, etc.
- Design safety, HSE, and constructability factors
Minimum Quality Plan for design Checking
- Follow appropriate color codes for checking.
- Use appropriate checklists. Signed and dated.
- Continual review of design/model is a must
- List items requiring special attention or independent review
- Conduct design safety and constructability reviews
- Mandatory to conduct inter-squad checks on design documents prior to the final check and issue
- Conduct formal stage-wise collaborative design review/model review sessions
What do we check for?
- The Deliverable is error-free with respect to the inputs provided
- Ease of fabrication, shipping, and erection
- Reduction in material and fabrication costs. Value+++
- Build some flexibility into the design, especially for critical items
- Ensure a consistent design approach for similar pieces of equipment and/or unit area piping
- Aesthetics
Responsibility Matrix for design check
- Every individual is responsible and accountable for checking his deliverable to ensure quality and error-free design.
- Every individual checks, signs, date, and then pass it on to the next individual.
- Calculations/drawings received for checking by the next individual, without a sign and date, shall not be entertained/accepted!!!
- Back-ups of holds and assumptions, if any, are maintained in an orderly manner before the issue
- A signed and dated checklist, completely filled out is a must for any checked document as this is a quality record
- The ultimate responsibility of quality and correctness lies with the lead as he is the one who enforces teams conformance to quality procedures
- Checking is a collaborative effort. Every individual owns and is accountable for an error-free and quality product
Why Design Checking Adds Value
- Owning responsibility and following good practices and procedures results in overall quality
- The use of checklists ensures important points needing check are not missing out
- Design reviews & inter-squad checks ensure interdisciplinary aspects are addressed in the design
- Safety and constructability reviews ensure good overall layout, approach, constructability, maintenance, and operability
- Incorporating fabrication/contractor-specific details and/or preferences into the design helps in easier and faster fabrication and lesser errors
- Facilitates a once-through approach from start to finish thereby saving on time and schedule
- Minimizes rework in design and at the field
Where do we stand today?
- Ownership and accountability by individuals missing. “Next person will check”!!!
- Do not prioritize tasks to ensure project schedules and goals are met
- Work hard but do not “Work Smart”
- Perform checking using either incomplete and/or superseded inputs
- Do not capture design changes and revisions properly. Do not use revision notes.
- Do not follow proper checking procedures, checklists, and colors from the initial stages. Keep this aside only for the final IFC check stage. Too late….!
- Do not check important items/spelling. More focused on irrelevant aspects
- Do not clarify checking procedures, standards, guidelines, checklists, etc. in the job notes upfront
- Do not obtain early client approval on checking procedures and expectations
- Do not have a checking and approval matrix for approval of various deliverables
- Do not maintain discipline holds summary
- Team and team leaders are often not aligned regarding the requirements/expectations of the project
- Final number-crunching during the IFC issue period often affects productivity, and efficiency and lowers team morale
What Needs Improvement?
- Follow a holistic approach toward checking
- Approach and expectations shall be clarified upfront through job notes and induction sessions
- Obtain client approvals and finalize checklists upfront
- Pay attention to minor details. Spell check is also important
- Work smart, prioritize, and be focused
- Checklists and proper procedures shall be used religiously – this is mandatory
- Always check against the latest documents to avoid rework.
- Always start the final check process against a frozen and dated set of documents like P&IDs, LL, etc.
- Lead to incorporate lessons learned in design into checklists as a process of procedural improvement
- Lead to make expectations known to the team, fix individual responsibility and enforce accountability
- Assign the right work to the right individual
- The team is to be told that this is not an individual activity but a team effort. We sail or sink together!
Synopsis
- Effective checking is integral to project success
- Translates into quality, cost, and schedule advantage. Value+++
- Checking is an innovative process, to find the best approach. One hat does not fit all!
- We need to challenge a situation to come out as a winner. Think “out of the box”!
Send me degsin checklist documents pdf.