Chemical Cleaning is the procedure for field cleaning of the piping systems especially Steam lines inlet for Turbines and Steam Drums. These pipelines after cleaning shall be free from hydrocarbons, greases, oils, rust, scale, and other impurities. In Chemical cleaning, chemicals are used to dissolve or loosen the hard deposits from process equipment or piping surfaces and removed them.
Why is it necessary to do Chemical Cleaning?
Most of the steam systems have carbon steel pipelines which will have a lot of rust, welding spatters, and slags inside during the construction. The chemical cleaning will reduce the duration of Steam lines flushing by 1/3rd of the actual duration. This will reduce the Project schedule and improve the quality inside the pipelines.
Chemical Cleaning Flow Chart
The following image (Fig. 1) shows a typical flowchart used for the chemical cleaning operation of the steam piping.
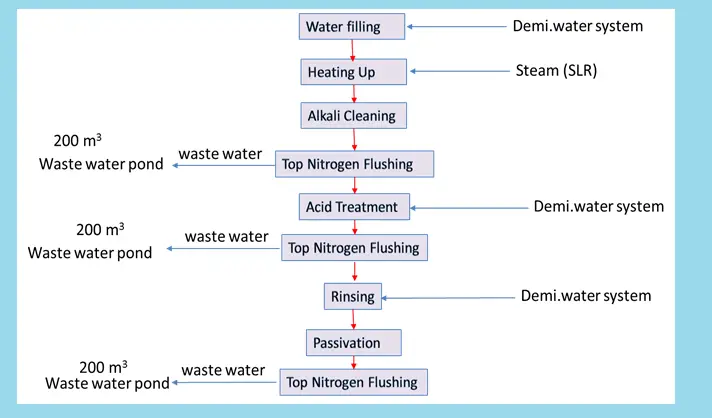
Technical details of chemical cleaning
According to the above Flow chart (Fig. 1), install the required equipment and lines (such as a chemical cleaning circulatory system). The complete system has to be chemically cleaned following several steps. The system has to be divided as per the following P&ID considering the volume. Refer to the below images (Fig. 2, Fig. 3, and Fig. 4) which show the loops and steps in the P&ID for HP, MP Steam System.
Step-1
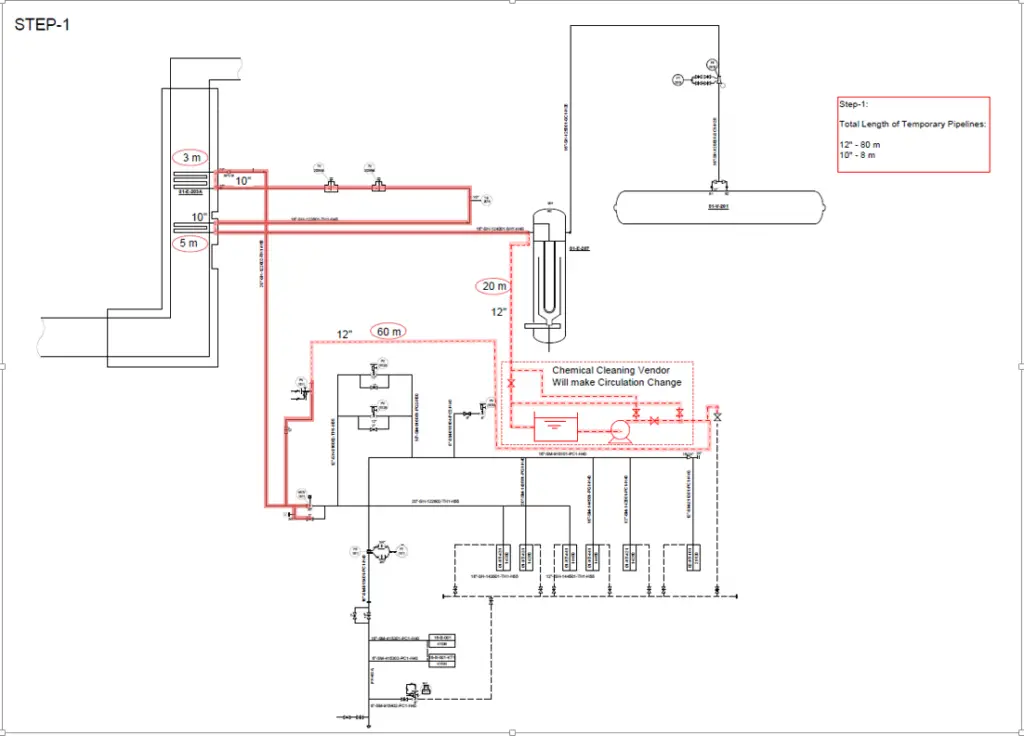
Step-2
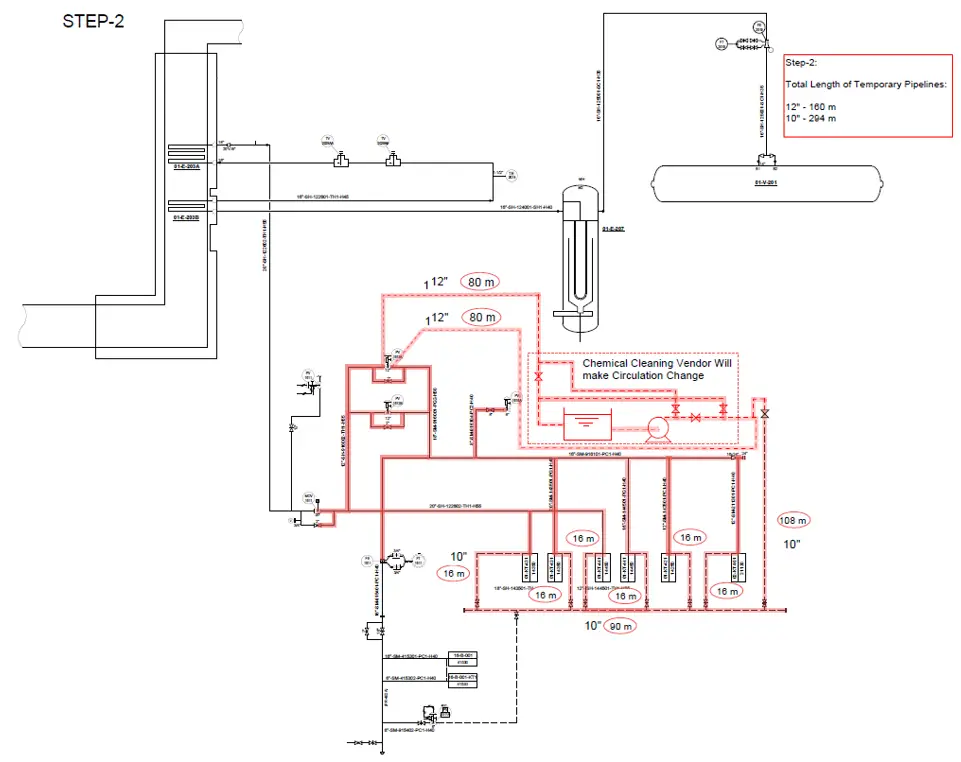
Step-3
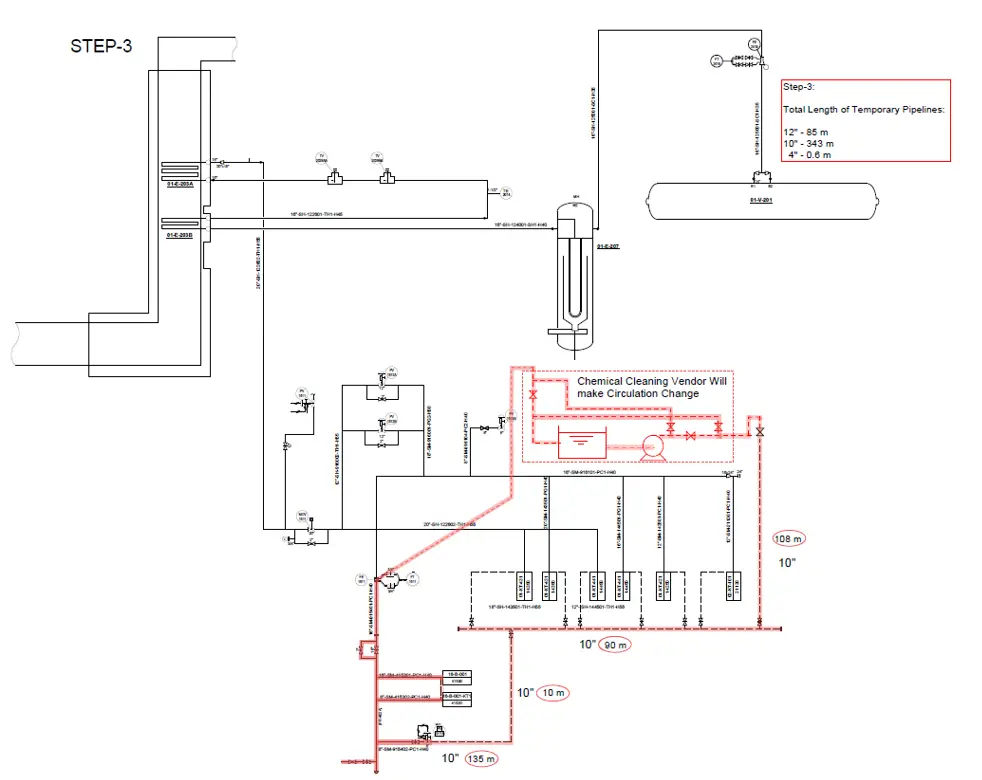
Chemical Cleaning Works shall be performed in accordance with the standard, regulations, and laws of the country of the Project. The mentioned procedure is followed as per the local regulation of Russia.
The following conditions shall be required prior to chemical cleaning.
- Isolation of cleaning system: The cleaning system shall be isolated from the other piping by closing valves. And those valves shall be locked with steel wire and clearly stated: “DON’T OPEN”.
- Instruments: Instrument and instrument leading shall be removed and isolated from systems to be cleaned. If the leading is not able to be removed, the inlet valve of the instrument shall be exactly closed, and the drain valve on the instrument leading shall be opened.
- Unsuitable materials for cleaning: Materials such as aluminum, zinc, copper, and copper alloy are unsuitable for chemical cleaning. So these materials must be removed or changed prior to cleaning.
Chemical Cleaning Procedure
The whole chemical cleaning procedure can be parted into the following steps:
Preparation work for Chemical Cleaning:
The following works shall be completed before starting the chemical cleaning activities;
- a. Erection and installation of temporary equipment such as:
- – Circulation pump
- – Chemical injection pump, chemical dissolving tank, and ejector
- – Steam mixing heater
- – Hydrazine injection system
- – Waste neutralizing tank and wastewater pump
- b. Temporary piping between the tie-in point on the permanent facility and temporary equipment. (For the purpose of by-pass, circulation, and so on)
- c. Installation of solution recovery line onto drain and vent by a rubber hose.
- d. Blind plates shall be inserted at safety valves and non-necessary items.
- e. Installation of the restrictive orifice on the system.
- f. Line/valve check of the system to be cleaned including temporary piping.
- g. Utility piping from the supply point to the cleaning system.
Water flushing and leak test:
Water flushing shall be performed using a temporary circulation pump until the drainage has been clear visually. The water flushing shall be conducted in accordance with the following steps 1 to 3.
- 1) Temporary Piping (water Supply Line): From the water supply connection to the inlet of the cleaning loop.
- 2) Temporary Piping (Circulation Pump Suction and Discharge Line) Flushing route:

- 3) Piping System, Temporary piping (Return Line) Flushing route:

After water flushing, water circulation shall be established in the cleaning loop and pressurized to the maximum pressure of the Circulation Pump. Leaks shall be rectified if any.
Heating up:
- To establish water circulation, steam shall be introduced into the cleaning system from the existing steam line.
- Heating shall be continued till the temperature becomes up to 70℃.
Degreasing:
The required quantity of chemicals shall be provided by the contractor in Chemical Injection Tank while the heating up is going on. After completion of heating up, the chemical solution shall be fed into the system to be cleaned by operating of Chemical Injection Pump.
Degreasing shall be performed under the following conditions with continuous circulation. (If the following condition is different from the contractor’s procedure, an alternative procedure shall be submitted.)
- Chemicals:
- Sodium hydroxide (NaOH)-0.05 %
- Sodium carbonate (Na2CO3)-0.3 %
- Trisodium phosphate (Na3PO4)-0.3 %
- Detergent- 0.05 %
- Temperature: 70 – 85°C
- Treating time: 12 hours
Alkalinity shall be monitored every hour to identify of quality of the cleaning solution.
Rinsing:
The cleaning solution shall be drained out from all of the low points under atmospheric pressure. Effluent including the following rinsing effluent shall be transferred into Neutralization facilities provided by the contractor.
Water shall be fed to the cleaning system until the system becomes full water. Before filling, initial flushing shall be done by Down Flow. Rinsing operation shall be performed in accordance with the following step.
- Water filling with initial flushing
- Circulation for 1 hour
- Drain out
This operation shall be repeated until circulating water becomes pH less than 10.
Re-Heating:
To establish water circulation, steam shall be introduced into the cleaning system from the existing steam line. Heating shall be continued till the temperature becomes up to 70℃.
Acid cleaning:
The required quantity of chemicals shall be provided by the contractor in Chemical Injection Tank while the heating up is going on.
After completion of heating up, the chemical solution shall be fed into the system to be cleaned by operating Chemical Injection Pump.
Acid cleaning shall be performed under the following conditions with continuous circulation. (If the following condition is different from the contractor’s procedure, an alternative procedure shall be submitted.)
- a. Chemicals :
- The citric acid (C6H8O7) – 3 %
- Ammonia (NH3)- Adjusting amount to pH 3 – 3.5
- Corrosion inhibitor (IBIT 30AR is recommendable)-0.3 %
- Suspending agent (Ammonium bifluoride, NH4HF2)-0.3 %
- b. Temperature: 70 – 85℃
- c. Treating time: 6 – 8 hours
Fe-ion concentration, acidity, and pH shall be monitored every hour. When the Fe-ion concentration reached equilibrium for 1 to 2 hours, the acid cleaning shall be finished. During the acid cleaning, the distribution of the flow rate shall be controlled and partial circulation and reverse circulation shall be carried out at a suitable time.
Cooling down:
Steaming into the cleaning loop shall be stopped and the system shall be allowed to cool down to 60℃ by natural radiation with continuous circulation.
Ammoniation:
The circulating solution shall be ammoniated to a pH of 8.5 to 9.0 with a gradual injection of ammonia. The identification of pH shall be done at every point of the cleaning loop.
Passivation:
Sodium nitrite as a passivation agent shall be prepared in Chemical Dissolving Tank and this chemical solution shall be injected into the chemical cleaning loop.
The treating conditions are as follows (If the following condition is different from the contractor’s procedure, an alternative procedure shall be submitted.)
- a. Chemical: Sodium nitrite (NaNO2) -0.5%
- b. Temperature: Approx. 60°C
- c. Treating time: 2 hours or more
Final rinsing:
The cleaning solution shall be drained out from all of the low points under positive nitrogen pressure. Effluent including the following rinsing effluent shall be transferred into the Neutralization facility provided by the contractor.
Before filling, initial flushing shall be done by Down Flow. Rinsing operation shall be performed in accordance with the following steps.
- Water filling with initial flushing
- Circulation for 1 hour
- Drain out under nitrogen pressure excluding the final drain out
This operation shall be repeated until the circulating water becomes clean.
Rinsing shall be performed with freshwater containing 100 mg/L of hydrazine (N2H4,) and 50 mg/L of ammonia. In the final stage of rinsing, flushing of drain lines shall be carried out.
Final Drain Out:
Rinsing water shall be drained out and air blowing need to be done. After completion Nitrogen purging should be carried out for prevention.
Final Inspection and Evaluation
The condition of the cleaned pipelines will be checked visually to make a comprehensive evaluation. According to the cleaning feedback, further actions will be taken.
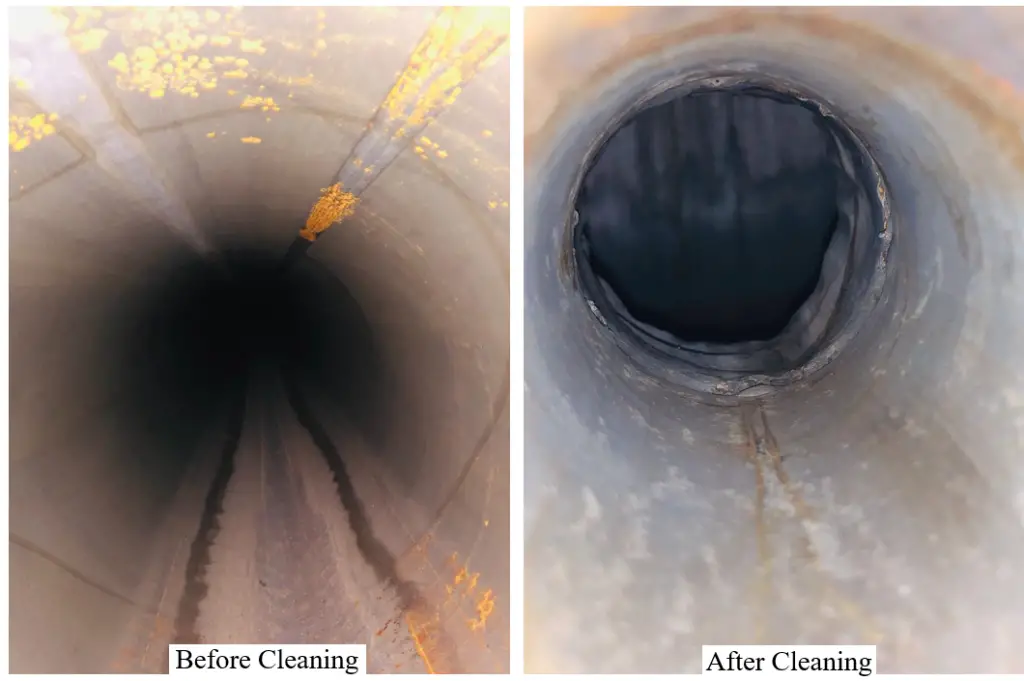
After chemical cleaning, Wastewater management is very important due to chemicals that are used are highly toxic. Chemical cleaning can be carried out after getting Client approval.
Few more related articles to enhance your knowledge.
An article on “Internal Cleaning of Piping System”
Cleaning Requirements of Piping Systems
Dear sir
I am msc in chemistry and I am in chemical cleaning field since last one month I have a doubt in degreasing stage how to check alkalinity if you have any procedure please send it to my email id
Hey ! Post is amazing and helpful for all the people who are looking for all purpose cleaner, and I hope you will continue to do post amazing posts or blogs in future.
Hey ! Post is amazing and helpful for all the people who are looking for all purpose cleaner, and I hope you will continue to do post amazing posts or blogs in future. we are also in this field in which we provide all types of cleaners whether it is for floor, clothes, or for any of the surface in the home.
Kindly check it once : https://www.drbacti.com/
Cleaning material inquiry
Safety procedure also shall mention in safe work method.