Cranes are widely used and extremely powerful construction equipment that makes the life of a construction engineer easier. There is no substitute for cranes for lifting heavy products at great heights. But, the operation of cranes at the construction site is full of hazards and risks. If not handled properly, Cranes have the potential to cause major accidents claiming human lives. Thus crane safety is of utmost importance and must be followed minutely to avoid any major accident during operation. In this article, we will explore the causes of crane accidents and crane safety tips to reduce the chances of accidents involving crane operations.
Major Causes of Crane Accidents
The major causes of crane accidents include:
- boom or crane contact with energized power lines (nearly 45% of the cases),
- under the hook lifting device,
- overturned cranes,
- dropped loads,
- boom collapse,
- crushing by the counterweight,
- outrigger use,
- falls, and
- rigging failures.
- Also, some cranes are not maintained properly nor inspected regularly to ensure safe operation.
How Do Accidents Occur?
- Instability – unsecured load, load capacity exceeded, or ground not level or too soft
- Lack of communication – the point of operation is a distance from the crane operator or not in full view of the operator
- Lack of training
- Inadequate maintenance or inspection
- In addition to instability factors, communication, and training, some cranes are not maintained properly nor inspected regularly to ensure safe operation.
Who is at Risk?
- Operators
- Persons at Crane Site
Crane Terminologies
Crane – Consists of a rotating structure for lifting and lowering horizontally on rubber tires or crawler treads
Hoist – Used to lift and lower load. Learn more about hoisting equipment by clicking here.
Boom – An inclined spar, strut, or other long member supporting the hoisting tackle
Boom stops – A device used to limit the angle of the boom at its highest position
Brake – To slow or stop motion by friction or power
Block – Sheaves or grooved pulleys in a frame with hook, eye, and strap
Jib – Extension attached to the boom point to provide added boom length for lifting specified loads.
Boom angle indicator – An accessory device that measures the angle of the boom base section centerline to horizontal
Load – The weight of the object being lifted including:
- Load block and hook
- Wire rope
- Rigging
- Boom attachments
- Ancillary attachment
Outrigger – Support members attached to the crane’s carrier frame which are used to level the crane
Pendants – Stationary wire ropes used to support the boom
Radius – The horizontal distance from the axis of the rotation of the crane’s superstructure to the center of the suspended load
Superstructure – The rotating frame, gantry, and boom or other operating equipment
Counterweight – Weights used for balancing loads and the weight of the crane in providing stability
Deck – The revolving superstructure or turntable bed.
Drum – The spool or cylindrical member around which cables are wound for raising and lowering loads
Crane Parts (Fig. 1)
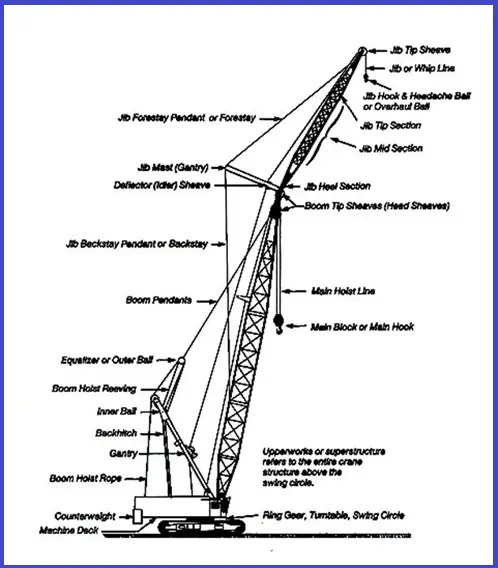
Types of Cranes
- Mobile cranes
- Hydraulic cranes
- Overhead cranes
- Gantry cranes
- Tower cranes
Commonly Used Cranes
- Hydraulic rough terrain crane
- Crawler lattice boom friction crane
Several significant differences between these cranes, primarily in boom hoist and load line controls. The somewhat smooth operation of the boom control adjustments on the hydraulic cranes may falsely suggest that it is simple to operate. The lattice boom friction cranes’ movement in its boom or its adjustment in load position tends to be a little jerky requiring more skill and experience to operate smoothly.
Another difference is the load charts. Due to the fixed boom lengths, the lattice boom friction crane has a more simplified load chart. This requires extensive motion control and anticipation of boom movement to accurately lift or place loads.
The hydraulic crane’s load charts are more extensive making them complicated due to variations in boom length, so more training in multiple charts is required
The differences between these cranes are significant enough to require specific training on each type of crane. Crane operators cannot expect to be totally knowledgeable and proficient in the operation of the many diverse types of cranes available today. They cannot be expected to move from one type of crane to another without adequate education and training on the specifics of each piece of equipment.
Crane Hazards
- Improper load rating
- Excessive speeds
- No hand signals
- Inadequate inspection and maintenance
- Unguarded parts
- Unguarded swing radius
- Working too close to power lines
- Improper exhaust system
- Shattered windows
- No steps/guardrails walkways
- No boom angle indicator
- Not using outriggers
Hazards Associated with Crane Operations
- OSHA’s analysis of crane accidents in general industry and construction identified an average of 71 fatalities each year.
- A study conducted by OSHA showed that nearly 30% of work-related electrocutions involved cranes.
- Although mechanical failures represent only 11% of the causes of crane accidents, they usually result in major accidents involving injuries, fatalities, substantial material costs, and usually spectacular media coverage. Studies and analyses often show they are frequently due to a lack of preventive maintenance or adequate training and/or experience on the part of the personnel involved. Crane operators and other personnel working with cranes need to receive training in crane operations. Cranes and associated rigging equipment must be inspected regularly to identify any existing or potentially unsafe conditions. Regular inspections are before use and during use. If there are problems, get them fixed before continuing work. Preventive maintenance must also be done per the crane manufacturer and/or the supplier’s specifications.
Crane Safety Guidelines
There are various crane safety guidelines that must be followed to reduce the accident potential. Some of these crane safety rules are
1. Proper Planning Before Start-Up
- Level the crane and ensure the support surface is firm and able to support the load
- Contact power line owners and determine precautions. Know the location and voltage of overhead power lines.
- Know the basic crane capacities, limitations, and job site restrictions, such as the location of power lines, unstable soil, or high winds.
- Make other personnel aware of hoisting activities.
- Barricade areas within a swing radius.
- Ensure proper maintenance and inspections.
- Determine safe areas to store materials and place machinery.
2. Competent Person
The competent person must inspect all machinery and equipment prior to each use, and during use, to make sure it is in safe operating condition.
If it needs fixing, take it out of service and don’t use it until it is fixed
3. Load Capacity – Speed – Warnings
Make sure the crane operator can see the:
- Rated Load Capacities
- Operating Speeds
- Special Hazard Warning or Instruction
4. Know the Weight of the Load
- Refer to the shipping ticket or other documentation
- Ensure lift calculations are correct
- Ensure the load is within the load chart rating for boom length and load radius of the crane
- Crane is rated by the maximum weight it will lift at a minimum radius and minimum boom length – the further from its center point, the less it will lift
Crane Overturning Accidents
Basically, overloading is responsible for a relatively small portion of mobile crane accidents simply because a very small portion of lifted loads is at or near rated loads. In concept, load and load-moment indicators are ideal means to assure cranes will not be overloaded. In practice, they fall short of the ideal. The reasons are many and can only be briefly mentioned here.
Some reasons that load or load-moment indicators are not reliable:
- the device has been turned off or is down due to malfunction,
- the device is out of calibration, or
- operating conditions (wind or operating speeds or out of level) are so far from ideal that the published rating can lead to failure. The mounting of a device is itself no assurance operations will be safe. Just like oil pressure or temperature gauges, those devices are not safety devices; they are indicators that advise a knowledgeable operator of load parameters as an aid in making operating judgments.
Some authorities overstress the value of or need for, load or load-moment indicators. There is no doubt that there are operating situations that require a device of that type, but on the other hand, in certain situations, they offer mixed blessings. It has been demonstrated that there is a tendency for some operators to become overly reliant on the devices and to use them in place of judgment. This can lead to accidents when conditions are not ideal. An untrained or inexperienced operator may use the device as a prop and as a substitute for knowing the machine, the load, and the rating chart.
Operators who do not fully understand the meaning of the values on the rating chart, and who do not understand the limitations of the crane and its ratings, will operate carelessly or will allow untrained, inexperienced supervisors to tell them to pick an unsafe load. The number of operators who do not understand rating charts is surprising. The number of supervisors who know little or nothing about cranes is shocking.
Crane Load Limiting Factors
- Not level
- Wind
- Side loads
- On its wheels
- Lifting over the side
- Use of extensions, jibs, and other attachments
- Limits of wire rope, slings, and lifting devices
Mobile Cranes –Lifting Principles
- Center of Gravity
- Leverage
- Stability
- Structural Integrity
Four basic lifting principles govern a crane’s mobility and safety during lifting operations:
- The Center of Gravity Point in the object where its weight can be assumed to be concentrated or, stated in another way, it is the point in the object around which its weight is evenly distributed. The location of the center of gravity of a mobile crane depends primarily on the weight and location of its heaviest components (boom, carrier, upperworks, and counterweight).
- Leverage Cranes use leverage to lift loads. Rotation of the upperworks (cab, boom, counterweight, load) changes the location of the center of gravity, its leverage point or fulcrum.
- Stability Relationship of the load weight, angle of the boom, and its radius (distance from the crane’s center of rotation to the center of load) to the center of gravity of the load. Stability could also be affected by the support on which the crane is resting. A crane’s load rating is generally developed for operations under ideal conditions, i.e., a level firm surface. Unlevel surfaces or soft ground, therefore, must be avoided. In areas where soft ground poses a support problem, mats and or blocking should be used to distribute a crane’s load and maintain a level stable condition.
- Structural Integrity The crane’s mainframe, crawler track and/or outrigger supports, boom sections, and attachments are all considered part of the structural integrity of lifting. In addition, all wire ropes, including stationary supports or attachment points, help determine lifting capacity and are part of the overall structural integrity of a crane’s lifting capacity.
These elements may also affect structural integrity:
- The load chart capacity in relation to stability;
- The boom angle limitations affect stability and capacity; and
- The knowledge of the length of boom and radius in determining capacity.
Crane Accident– Overturned Crane
The crane in Fig. 2A overturned when it attempted to lift heavy pieces of metal chain in excess of its load rating. In addition, it was side loading which was not part of the load calculation. Even though the outriggers were out, the weight of the load caused the crane to overturn.
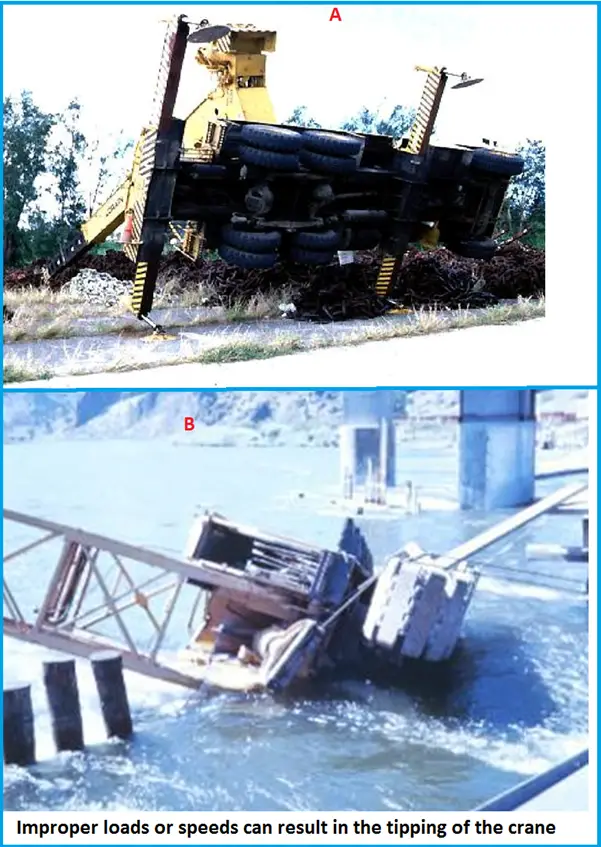
The crane in Fig. 2B overturned while performing loading operations on a pier. The crane was attempting to remove a metal container from a barge when it tipped and slid into the water. The wind caused the load to swing violently causing the load to go outside the swing radius, at that point the load dropped into the water and took the crane with it.
Precautions
- Power Lines: Stay clear from power lines at least 10 feet
- Swing Radius: Stay out of the swing radius of the crane–Make sure there are barrier guards showing the swing radius
- Operator Visibility: Make sure broken windows or other obstructions do not prevent the operator from seeing
- Guardrails: Runways and steps need to have guardrails, handholds, and slip-resistant surfaces
- Suspended Loads: Don’t stand under suspended loads
- Boom Angle Indicator: A boom angle indicator must be on the crane
- Supporting Surface: Cranes must be on a firm supporting surface and level within 1 percent
- The grooves must be smooth and free from surface defects that could cause rope damage. The damaged wire rope must be taken out of service.
- Rigging Equipment Slings: Types of slings include alloy steel chain, wire rope, metal mesh, natural or synthetic fiber rope, and synthetic web. Immediately remove damaged or defective slings from service.
- Annual Inspections: Inspection of the hoisting machinery must be made by a competent person. The employer must maintain a record of these inspections.
What to Inspect
- Correct air pressure and no leaks
- Tires are properly inflated. Conduct regular inspections of tires for excessive wear or damage
- Clearance for tail swing
- Wire rope wear
- Physical damage to the crane
- Loose or missing hardware, nuts, or bolts
- Fluid leaks
Few more useful resources for you…
What is Engineering Process Safety?
Safety Rules during A Field Visit By A Design Engineer
An article on Crane safety during Construction
HAZOP (Hazard and Operability) Study: A brief introduction
An article on Excavation Hazards at Construction Sites
Hazardous Area- Theory, Classification and Equipment selection: A short presentation
An article on THE HAZARDS OF PRESSURE TESTING
Thanks for sharing such an informative article. Anyone in construction or industrial field should be well aware of the safety and precautionary measures regarding cranes. Not only the people operating the crane be certified to operate it but the cranes too should be equipped with the latest and functional warning systems and safety indicators.
Thank you for this article, it will prove useful to me when I start construction of a new commercial building I’ll plan to rent out soon. I plan to build a bit tall so having a crane operator is something I plan on doing since I’ve never had to hire one before knowing these things are crucial to me. I like that you included a list of precautions to take into consideration when working with cranes. I’ll make sure that the power lines are cleared once we have the crane on-site, to prevent any sort of accidents with them.