What is a Cryogenic Valve?
Piping and Pipeline systems handling liquid hydrogen, oxygen, helium, nitrogen, liquefied natural gas, or similar very cold fluids require to use of cryogenic valves. The term cryogenics deals with materials and processes below -1010C (-2390F). Hence, Cryogenic valves must be designed with properties to handle such low temperatures. The main difference between cryogenic valves from standard valves is that they are able to work in such low temperatures with high pressures.
Problems with Cryogenic Valves
The main problem with cryogenic valves is that any fluid leakage to the atmosphere through gaskets or gland seals will degrade the valve and associated equipment performance. Also, such leakage at the valve stem will cause localized icing that may seize the valve-operating mechanism. This is the reason valves for cryogenic applications must be designed for high performance and truly zero leakage as per API 598.
Codes and Standards for Cryogenic valves
Codes and standards used for cryogenic valves are:
- BS 6364
- BS EN 12567
- BS EN 1626
- BS EN 12300
- MSS SP-134
- ISO 28921-1
- ISO 21011
- ISO 10497
- ASME B16.34
Why do cryogenic valves have long stems? | Design Consideration of Cryogenic Valves
All cryogenic valves for liquid natural gas, methane, oxygen, ammonia, etc applications are specially designed. Cryogenic valves usually have extended bonnets so that the valve stem seals are kept away from the cold source. This will serve two important purposes:
- The valve stem seals will have a relatively higher temperature.
- There will be sufficient space to provide insulation between the pipeline and the lever/handwheel operating the valve.
Size and Pressure Rating of Cryogenic Valves
Cryogenic valves for industrial applications can be found in various sizes and pressure classes. The size usually ranges from 1/8 inch to 88 inches (3 mm to 2240 mm). The pressure rating of cryogenic valves varies from ultra-high vacuum pressure to 700 bar. All these valves are capable of working at a temperature down to -2540 C (-4250F).
Materials for Cryogenic Valves
Usual materials that are used for constructing a cryogenic valve are Aluminum, Monel, Brass, Bronze, Stainless Steel, Incoly, Zirconium, etc. PTFE or graphite is normally used as the seal material.
Common Valves for Cryogenic Applications
Usual valves used for cryogenic applications are specially designed globe, angle, gate, butterfly, and ball valves. So, selecting the right type of cryogenic valve for the required application is essential. There are no strict available guidelines for valve type in cryogenic service. But, there is a trend to select quarter-turn ball valves and triple-offset butterfly valves.
Triple Offset Butterfly Valves for Cryogenic Services:
Triple-offset butterfly valves are high-performance widely used valves for cryogenic services. The offsets in such valves reduce the rubbing and wear between the seat and seal.
The triple offset design has a resilient stainless steel ring that is installed in the disk assembly to provide a zero-leakage seal for cryogenic duties.
The seal and seat contact surface is cone-in-cone construction. These cones are inclined and the contact angle between the seat and seal generates a slight wedging effect that flexes and radially compresses the disc-seal ring. Regardless of the flow direction or line pressure, the valve provides very good shut-off capability.
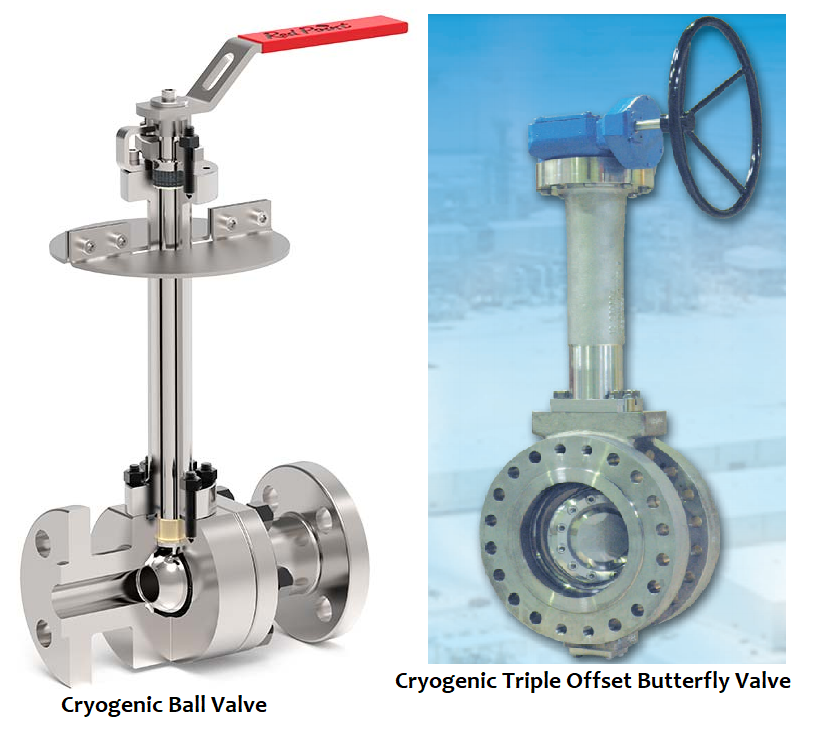
Ball Valves for Cryogenic Application:
Piping and pipeline systems for LPG, LNG, thermal fluids, liquid oxygen, and nitrogen applications use double-seal ball valves. They can be of reduced and full bore types. Cryogenic ball valves incorporate a vapor space of sufficient height that allows gasification in the area below the gland. This keeps the gland packing at near ambient temperature.
With an increase in pipe sizes, the gate and globe valves become difficult and costly to actuate. That is the reason they are restricted to smaller pipe sizes and applications not requiring a remote operation.
Features of Cryogenic Valves
- Cryogenic valves should be lightweight as the lightweight valve mass is easier to cool from ambient to cryogenic temperature.
- Lighter cryogenic valves usually have lower conductivity that helps in reducing heat influx as compared to heavier constructions.
- Flange and welded configurations are usually used for cryogenic piping connections. However, welded valves are better.
- Cryogenic valves should be assembled in a clean room and be lubricant-free or utilize lubricants compatible with cold service. While purchasing a cryogenic valve, documented cleaning procedures must be collected to verify and follow proper procedures during the assembly process.
Testing of Cryogenic Valves
The following tests are usually required to perform for cryogenic valves:
- Shell strength test: Hydrostatic or Pneumatic test to 1.5 × Maximum Working Pressure.
- Shell leak test: For the leak test of the shell usually a Pneumatic test is performed with 1.1 × Maximum Working Pressure.
- Seat leak test: Pneumatic test to 1.1 × Maximum Working Pressure.
- Cryogenic prototype test: This test is performed following BS 6364 Appendix A.
- Cryogenic production test: The procedures for Cryogenic testing of valves are provided in BS 6364 and the same is followed.
Where are Cryogenic Valves used? | Applications of Cryogenic Valves
Cryogenic valves are widely used in
- LNG liquefaction plants
- LNG terminals
- LNG transportation systems
- Food and beverage industries
- Air separation plants
- Steel production plants
- Research laboratories
- Chemical and petrochemical plants
- Aerospace storage facilities
How Cryogenic Valve is installed in Piping?
To maintain a warm gas seal, the valve is located so that the stem has a minimum angle of 15 degrees to the horizontal. Preferably, the valve is in a horizontal pipe run to simplify piping arrangements.
In this article of cryogenic valves, the temperature mentioned is -101Deg.C however in article with subject : “What is cryogenic piping” the temperature mentioned is -29 or -150 deg. C and below.
Can you please clarify.
It’s great that you talked about how the main difference between cryogenic valves from standard valves is that they are able to work in such low temperatures with high pressures. I was watching a show about factories the other day and I saw how some of them used cryogenic liquid relief valves. The valves looked more complex than the usual types of valves, so they were really interesting to see.