In the vast world of the piping industry, various components work together seamlessly to ensure the smooth flow and control of fluids. Among these crucial components, valve stems play a pivotal role in regulating fluid flow, isolating sections, and controlling the overall functionality of piping systems. In this article, we delve into the significance of valve stems in the piping industry, exploring their importance, functionality, and the critical tasks they perform to maintain efficient and safe operations.
What is a Valve Stem?
For opening or closing the valve, the valve stem provides the necessary movement to the disc, plug, or ball. The proper positioning of the disk is ensured by the stem of the valve. At one end, they are connected to the handwheel, actuator, or lever, while the other side of the valve stem is connected to the valve disc. For globe and gate valves, the linear motion of the disc is provided by the stem, and the rotating motion is ensured for plug, ball, and Butterfly valves.
Stems are usually manufactured by the forging method. They are connected to the disk by thread or other techniques. The sealing area prevents leakage.
Functions of Valve Stems
Control and Regulation of Fluid Flow:
Valve stems act as the primary mechanism for controlling fluid flow in piping systems. By utilizing different types of valves, such as gate valves, globe valves, and ball valves, valve stems provide the means to open, close, or partially obstruct the passage of fluids. This ability allows for precise regulation of flow rates, pressure control, and isolation of specific sections of the piping network, enabling efficient operations and maintenance.
Flow Direction and Diversion:
Valve stems also facilitate the diversion of fluid flow in various directions within the piping system. By manipulating the position of valves, operators can redirect fluid streams to different branches or alternate routes, accommodating specific process requirements or maintenance activities. This flexibility allows for optimal flow distribution, reduced downtime, and improved system performance.
Fluid Isolation and Safety:
One of the critical functions of valve stems is to provide reliable isolation of sections within a piping system. In cases of maintenance, repairs, or emergencies, valve stems enable operators to shut off the flow of fluids to specific pipelines, preventing leaks, spills, or cross-contamination. This feature ensures worker safety, protects equipment, and minimizes the impact of unforeseen incidents on the overall system.
Pressure and Flow Control:
Valve stems play a crucial role in maintaining desired pressure levels and flow rates within a piping system. By adjusting the position of control valves, operators can modulate flow rates and regulate pressure to meet process requirements. This control enables optimal system performance, preventing excessive pressure, and ensuring the smooth operation of downstream equipment.
Maintenance and Serviceability:
Valve stems facilitate ease of maintenance and serviceability in piping systems. With the ability to isolate specific sections using valve stems, maintenance personnel can work on individual components without disrupting the entire system. This feature streamlines maintenance operations, reduces downtime, and enhances overall system reliability.
Compatibility and Adaptability:
Valve stems are designed to work with various types of valves, allowing for compatibility and adaptability in diverse applications. Whether it’s controlling water, gas, oil, or chemicals, valve stems can be utilized in a wide range of industries, including oil and gas, petrochemicals, water treatment, pharmaceuticals, and manufacturing. This versatility makes them essential components in creating efficient and reliable piping networks for diverse processes.
Types of Piping Valve Stems
There are several types of valve stems used in the piping industry, each designed for specific applications and operating conditions. Here are some commonly used types of valve stems:
Rising Stem:
The rising stem valve features a stem that moves linearly upward as the valve is opened. This design provides a visual indication of the valve position, making it easier to determine whether the valve is open or closed. Rising stem valves are commonly used in gate valves and globe valves. There are two types of Rising Valve stems
- Rising Stem with Outside Screw and Yoke, and
- Rising Stem with Inside Screw
In the case of a rising Stem with an Outside Screw and Yoke, the stem exterior is threaded, while the part of the stem in the valve is smooth. The stem packing isolates the stem threads from the flowing media. There are two different design styles available; one with an attached handwheel so they can rise together, and the other with a threaded sleeve that rises the stem through the handwheel.
For Rising Stem with Inside Screw, the threaded stem part stays inside the valve body. The valve stem packing is provided along the smooth section and it is exposed to the atmosphere outside. In such designs, the stem threads are in contact with the flow medium. When rotated, the stem and the handwheel rise together to open the valve.
Non-Rising Stem:
In contrast to the rising stem, the non-rising stem valve has a stem that does not extend or rise as the valve is operated. Instead, the stem rotates inside the valve, transmitting the motion to the closure element. Non-rising stem valves are often found in ball valves and butterfly valves. These types of valve stems are more suitable where the space is limited. Fig. 1 below shows an example of rising and non-rising valve stems.
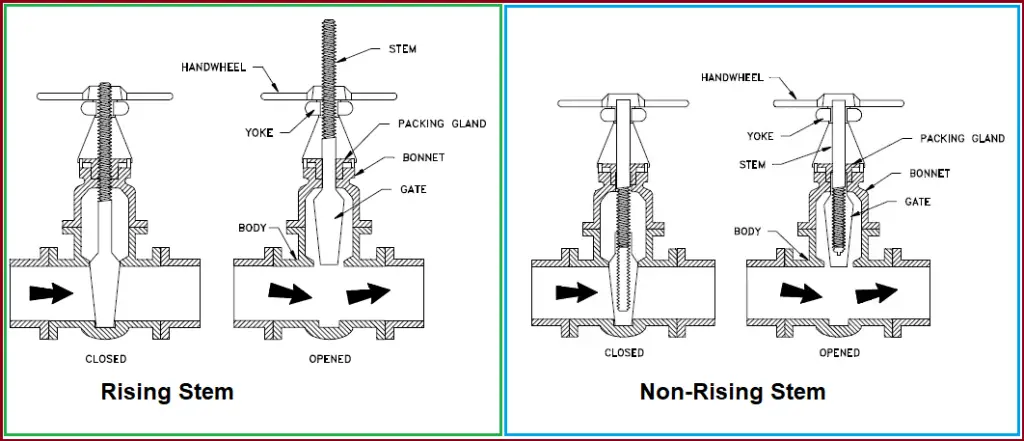
Quarter-Turn Stem:
Quarter-turn stem valves, as the name suggests, require only a quarter turn of the stem to fully open or close the valve. These valves are often used in ball valves and plug valves, where quick and efficient operation is desired.
Multi-Turn Stem:
Multi-turn stem valves require multiple rotations of the stem to open or close the valve fully. These valves typically have a rising stem design and are commonly used in gate valves and globe valves, where fine control of flow is necessary.
Sliding Stem
This valve stem does not rotate or turn but it slides in and out of the valve to open or close the valve. For hand-operated lever rapid-opening valves, this type of valve stem is mostly used. Sometimes, they are also used in hydraulic or pneumatic cylinder-operated control valves.
Hollow Stem:
Hollow stem valves have a hollow or tubular stem that allows for the passage of fluids or gases through the stem itself. These valves are often used in applications where fluid diversion or sampling is required without the need for additional connections or valves.
It’s important to note that the type of valve stem used depends on the specific requirements of the application, including the type of valve, fluid characteristics, pressure, temperature, and operational considerations. Valve manufacturers offer a wide range of options to suit different needs and ensure optimal performance and reliability in various piping systems.
Valve Stem Packing
Valve stem packing refers to the sealing arrangement used around the valve stem to prevent leakage of fluid or gas from the valve body. It serves as a crucial component in controlling and maintaining the integrity of a valve.
The primary function of valve stem packing is to create a reliable seal between the stem and the valve body while allowing the stem to move smoothly during valve operation. It prevents the escape of the process fluid or gas, ensuring that the valve can effectively isolate or control the flow as intended.
Valve stem packing typically consists of a packing material, which is wrapped around the stem and compressed to form a seal. The packing material can be made of various materials, depending on the specific application and the characteristics of the fluid being handled. Common packing materials include graphite, PTFE (polytetrafluoroethylene), aramid fibers, synthetic rubber, or a combination of these materials.
The packing material is usually packed tightly around the stem, forming a barrier that prevents fluid leakage. It is compressed using packing gland followers or packing gland nuts, which apply pressure to the packing material, ensuring a proper seal. The packing gland is typically located on top of the valve body and is adjustable to maintain the desired compression and seal integrity.
Proper packing selection and installation are essential for effective sealing and smooth valve operation. Factors such as temperature, pressure, chemical compatibility, and the specific requirements of the application must be considered when choosing the appropriate packing material. It’s crucial to follow manufacturer recommendations and industry standards to ensure the correct installation and maintenance of valve stem packing.
Over time, valve stem packing may wear out or deteriorate due to factors such as aging, temperature fluctuations, or chemical exposure. Regular inspection and maintenance are necessary to identify and replace worn or damaged packing to maintain the sealing integrity of the valve.
Conclusion
Valve stems serve as the vital link in the piping industry, enabling control, regulation, and isolation of fluid flow. Their importance cannot be overstated, as they play a critical role in maintaining safe operations, optimizing system performance, and facilitating maintenance activities. By understanding the significance of valve stems and their functionalities, professionals in the piping industry can ensure the efficient and reliable operation of piping systems, promoting safety, productivity, and the smooth flow of fluids in various industrial sectors.