Metal fatigue is a critical phenomenon that affects a wide array of industries, from aerospace to automotive and even oil and gas and consumer electronics. It refers to the gradual weakening of material due to repeated stress, which can eventually lead to failure. Understanding metal fatigue is crucial for ensuring the reliability and safety of structures and components in various applications. Failures due to fatigue can lead to catastrophic results, making it essential for engineers to consider fatigue life in their designs.
What is Metal Fatigue?
Metal fatigue is defined as the progressive and localized structural damage that occurs when a material is subjected to cyclic loading. This can occur below the yield strength of the material, meaning that even under loads that would not cause immediate failure, prolonged stress can lead to failure over time.
The unexpected failure of metallic components by progressive fracturing while in operating condition is known as metal fatigue. Local overstressing of a component sometimes generates a small crack (cracks can be present in the component due to manufacturing defects as well) that slowly keeps on growing with subsequent operating cycles and the metal part keeps weakening. When the crack grows to a critical size, the component fails catastrophically without any warning sign. Such failure is known as metal fatigue failure.
Mechanisms of Metal Fatigue
Metal fatigue failure occurs in three stages:
- Crack initiation
- Crack propagation, and
- Metal failure
1. Crack Initiation: This is the first stage where microstructural changes begin. Initial cracks often form at stress concentrators, such as surface imperfections or inclusions.
2. Crack Propagation: In this stage, the crack grows with each loading cycle. The rate of growth can vary depending on the material, the environment, and the loading conditions.
3. Final Fracture: Eventually, the crack becomes large enough to cause complete failure of the material. This stage often happens suddenly and without warning. Depending on the metal type, the failed surface appears different and does not follow specific rules similar to ductile fractured surfaces.
Factors affecting Metal Fatigue
Metal fatigue of a part is directly related to the number of stress cycles and the value of stress imposed on it. If the local stresses are kept below a defined value, there would not be any fatigue failure on the metal, and the part will operate satisfactorily for an infinite period of time. That limiting value is known as the endurance limit of that material.
Metal Fatigue is greatly affected by the presence of stress raisers like holes, notches, and keyways. Stress concentration increases locally in presence of stress raisers. A metal’s ultimate tensile strength, hardness, and its ability to handle fatigue loads are related to some extent. In general, the higher the tensile strength and hardness, the greater the likelihood of metal fatigue when subjected to high fluctuating loads.
The surface finish of the component also plays a great role in metal fatigue failure. Smooth surfaces increase fatigue life.
So, the parameters that impact the metal fatigue can be summarized as follows:
- Material Properties: The inherent properties of the metal, such as ductility, toughness, and yield strength, play a significant role in its fatigue life.
- Surface Finish: The surface condition of a material can significantly impact fatigue performance. Rough surfaces can act as stress concentrators, reducing fatigue life.
- Environmental Conditions: Factors such as temperature, humidity, and corrosive environments can accelerate fatigue.
- Loading Conditions: The nature of the applied load (static vs. dynamic, tensile vs. compressive) can also affect the fatigue behavior of materials.
Types of Metal Fatigue Failure
Depending on how fatigue failure occurs in a metal part, they can be grouped into various types, as mentioned below:
- Thermal fatigue failure: Temperature changes imposes a type of metal fatigue in components. The temperature change can be because of operating parameters or environmental factors.
- Fatigue failure due to temperature and pressure cycles: Both temperature and pressure cycles combined can induce this type of fatigue failure in a material.
- Corrosion fatigue failure: Highly corrosive environment can cause such type of metal fatigue. An initial crack is normally created by corrosion, which also deteriorates the metal surface, and the metal fatigue tendency increases.
- Vibration fatigue failure: Vibration fatigue is generated in a component due to vibration. Continuous vibration of mechanical equipment can lead to crack generation, which subsequently results in fatigue failure. This type of metal fatigue is because of the stresses occurring over time and includes corrosion and vibration fatigue failure.
How to identify Metal Fatigue?
Several methods are available for determining that metal is starting to become fatigued:
- Visual inspection: Detection of cracks or other deformations can be checked visually after a certain period of time.
- Noise analysis: The probability of metal fatigue can also be understood by noise analysis. Usually, damaged metal makes a specific rattling noise.
- Ultrasonic and X-ray inspection: Non-Destructive Ultrasonic and X-ray inspection is the best method to find out evidence of any crack.
- Fluorescent dyes: They make cracks visible and this provides a hint of fatigue initiation.
- Magnetic powders: Magnetic particle inspection can be used for ferrous materials to find out the crack initiation.
How to increase Fatigue Life?
Proper engineering considerations can reduce metal fatigue by increasing its life. While designing a component, various factors need to be considered to increase its fatigue life-
- Avoiding sharp corners: Use of generous radii will reduce stress concentration levels that in turn will increase metal fatigue life.
- Avoiding abrupt Cross-sectional changes: The fatigue life of a metal can be increased by making a smooth transition between cross-sections.
- The fatigue life of materials increases with a decrease in surface roughness. Mirror polished surfaces provide a very good fatigue life as polished surfaces remove stress raisers.
- Good quality welding with no inclusions, gas holes (porosity), or wormholes improves fatigue life.
- Selecting materials having very good fatigue-resistant properties.
- Treating the surfaces that will be loaded cyclically.
Testing for Metal Fatigue
Several testing methods exist to evaluate the fatigue life of materials:
- Wöhler (S-N) Curve: This method involves subjecting a specimen to cyclic loading and plotting the number of cycles to failure against the applied stress. The resulting curve helps engineers understand the fatigue strength of materials.
- Strain-Life (ε-N) Approach: This method relates the strain experienced by a material to its life under cyclic loading, particularly useful for ductile materials.
- Fracture Mechanics: This approach uses the principles of fracture mechanics to predict the growth of existing cracks under cyclic loading.
Determining the fatigue strength of a metal
To determine the fatigue strength of a material in laboratories, the test specimen is prepared following standard guidelines. Then a constant known bending stress is applied to the rotating specimen in the fatigue testing equipment. As the test specimen rotates, the stress applied to any outside fiber of the sample varies from maximum tensile to zero to maximum compressive and back. The test mechanism counts the number of rotations (cycles) until the specimen fails to produce the fatigue strength results.
A curve is plotted by performing fatigue tests on various stress levels and finding the number of cycles to failure. This curve is popular as the S-N curve. Various codes (ASME, BS, CEN, etc) provides the S-N curve in logarithmic scale from where for a specified stress level the number of cycles till failure can be easily determined. The following figure shows a typical S-N curve from ASME Code.
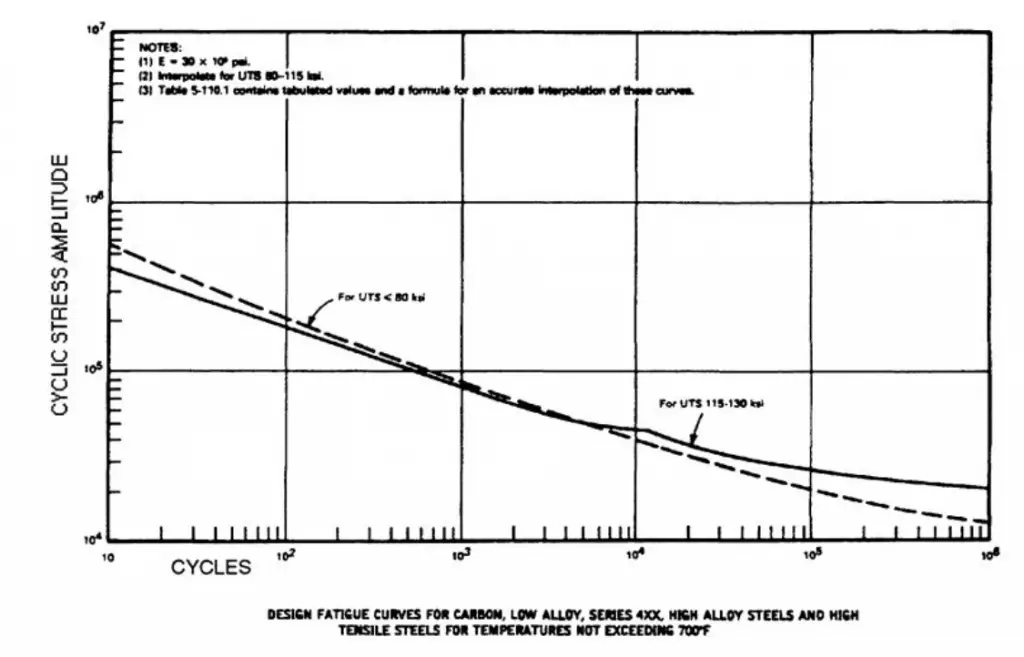
Predicting Metal Fatigue
Mathematical Models
Mathematical models are used to predict the fatigue life of materials based on various parameters. Some of the most common models include:
- Miner’s Rule: This is a linear cumulative damage model that helps estimate the fatigue life based on varying stress levels.
- Basquin’s Law: Used to predict high-cycle fatigue behavior, it relates the stress amplitude to the number of cycles to failure.
Software Tools
Advanced computational tools and simulations have become integral in predicting fatigue. Finite Element Analysis (FEA) allows engineers to simulate stress and strain distributions in complex geometries, providing insights into potential fatigue issues before physical testing.
How to Prevent Metal Fatigue?
There are various options by which metal fatigue can be minimized. Some of them are:
Proper Material Selection
Choosing the right material is crucial in mitigating fatigue. Advanced materials, such as high-strength steels and composites, often have better fatigue resistance.
Design Modifications
Implementing design changes to reduce stress concentrations, such as avoiding sharp corners and using fillets, can significantly enhance fatigue life.
Surface Treatments
Surface treatments, such as shot peening or hardening, can improve fatigue resistance by altering the surface characteristics of a material.
Regular Maintenance
Conducting regular inspections and maintenance can help detect early signs of fatigue, allowing for timely interventions and repairs.
Performing Fatigue Analysis
Metal fatigue can be prevented by following proper engineering design considerations and by performing a fatigue analysis during the design phase. In most situations, the parts that will be subjected to cyclic loadings are known beforehand during the design phase. So, using those data, fatigue analysis can be performed to find out metal fatigue capabilities. Various software programs have the capabilities to perform fatigue analysis of different components, like
- COMSOL Multiphysics
- nCode Design Life
- FRANC 2D/3D
- LIMIT stress evaluation software for fatigue analysis
- eFatigue
- FE-SAFE
- MSc fatigue
- Caesar II
To conclude, metal fatigue is a multifaceted phenomenon with significant implications across various industries. As technology advances, understanding and managing fatigue will continue to be a critical area of focus for engineers and researchers alike. By prioritizing research and development in this field, we can enhance the safety, reliability, and longevity of metal components in an increasingly demanding world.
Frequently Asked Questions: Metal Fatigue
1. What is metal fatigue?
Answer: Metal fatigue refers to the gradual and localized structural damage that occurs when a material is subjected to cyclic loading, leading to the formation and growth of cracks. This can result in sudden and unexpected failure.
2. What are the stages of metal fatigue?
Answer: Metal fatigue occurs in three stages:
- Crack Initiation: Small cracks form at stress concentrators or surface defects.
- Crack Propagation: The cracks grow with each loading cycle.
- Final Fracture: Eventually, the crack becomes large enough to cause complete failure of the material.
3. What factors influence metal fatigue?
Answer: Key factors include:
- Material properties (e.g., ductility, toughness)
- Surface finish (e.g., roughness)
- Environmental conditions (e.g., temperature, humidity)
- Loading conditions (e.g., type of stress—tensile or compressive)
4. How is metal fatigue tested?
Answer: Metal fatigue is commonly tested using methods such as:
- Wöhler (S-N) curves: Testing specimens under cyclic loading to plot stress against the number of cycles to failure.
- Strain-life (ε-N) approach: Relating strain to life for ductile materials.
- Fracture mechanics: Predicting crack growth based on existing flaws.
5. What is a Wöhler curve?
Answer: A Wöhler curve, or S-N curve, is a graphical representation of the relationship between the cyclic stress amplitude (S) and the number of cycles to failure (N). It helps in determining the fatigue strength of materials.
6. How can metal fatigue be prevented?
Answer: Preventative measures include:
- Selecting materials with high fatigue resistance.
- Implementing design modifications to reduce stress concentrations.
- Applying surface treatments (e.g., shot peening).
- Conducting regular maintenance and inspections.
7. What industries are most affected by metal fatigue?
Answer: Metal fatigue is a concern in many industries, including:
- Aerospace
- Automotive
- Civil engineering (bridges and buildings)
- Manufacturing and machinery
8. How can I identify signs of metal fatigue?
Answer: Signs of metal fatigue may include:
- Visible cracks or surface defects
- Changes in color or surface texture
- Unexpected noise or vibration in machinery
- Reduced performance or failure of components
9. Are there any standards for fatigue testing?
Answer: Yes, organizations such as ASTM International and ISO have established standards for conducting fatigue tests, ensuring consistency and reliability in results.
10. What is the role of advanced materials in combating metal fatigue?
Answer: Advanced materials, such as high-strength alloys and composites, often exhibit better fatigue resistance. Ongoing research into new materials aims to enhance performance and reduce failure risks in applications where fatigue is a concern.
11. Can fatigue failure occur without exceeding the material’s yield strength?
Answer: Yes, metal fatigue can lead to failure even under loads that do not exceed the yield strength, as it is the repetitive nature of the loading that contributes to crack formation and growth.
“How to Prevent Metal Fatigue?” is incorrect. How To is a preface to instruction, it is not a question. “How to Prevent Metal Fatigue;” (short for “This is How to Prevent Metal Fatigue”) is the correct way to write this statement.