What are Pumping Systems?
Pumping systems account for nearly 20% of the world’s electrical energy demand. Furthermore, they range between 25-50% of the energy usage in certain industrial plant operations. The use of pumping systems is widespread. They provide domestic, commercial, and agricultural services. In addition, they provide municipal water and wastewater services, and industrial services for food processing, chemical, petrochemical, pharmaceutical, and mechanical industries.
The function of a Pump
Pumps have two main purposes:
- Transfer of liquid from one place to another place (e.g. water from an underground aquifer into a water storage tank)
- Circulate liquid around a system (e.g. cooling water or lubricants through machines and equipment)
Components of the Pumping System
The main components of a pumping system are:
- Pumps (different types of pumps are explained in section 2)
- Prime movers: electric motors, diesel engines, or air system
- The piping used to carry the fluid
- Valves used to control the flow in the system
- Other fittings, controls, and instrumentation
- End-use equipment, which has different requirements (e.g. pressure, flow) and therefore determines the pumping system components and configuration. Examples include heat exchangers, tanks, and hydraulic machines
Pumping System Characteristics
The pressure is needed to pump the liquid through the system at a certain rate. This pressure has to be high enough to overcome the resistance of the system, which is also called the “head”. The total head is the sum of the static head and friction head.
Static head
Static head is the difference in height between the source and destination of the pumped liquid (see Fig. 1)
Static head is independent of the flow (see Fig. 1)
The static head consists of:
- Static suction head (hS): resulting from lifting the liquid relative to the pump centerline. The hS is positive if the liquid level is above the pump centerline, and negative if the liquid level is below the pump centerline (also called “suction lift)
- Static discharge head (hd): the vertical distance between the pump centerline and the surface of the liquid in the destination tank
The static head at a certain pressure depends on the weight of the liquid and can be calculated with this equation as shown in Fig. 1:
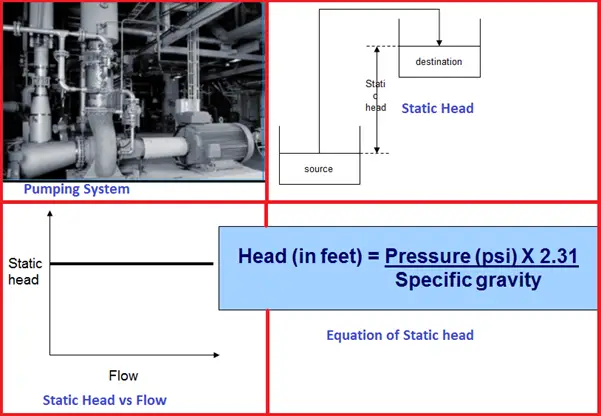
Friction head
- This is the loss needed to overcome that is caused by the resistance to flow in the pipe and fittings.
- It is dependent on size, condition and type of pipe, number and type of pipe fittings, flow rate, and nature of the liquid.
- The friction head is proportional to the square of the flow rate as shown in Fig. 2.
- A closed-loop circulating system only exhibits a friction head (i.e. not a static head).
In most cases, the total head of a system is a combination of static head and friction head as shown in Fig. 2. The left figure is a system with a high static head (i.e. the destination reservoir is much higher than the source). The right figure is a system with a low static head (i.e. the destination reservoir is not much higher than the source).
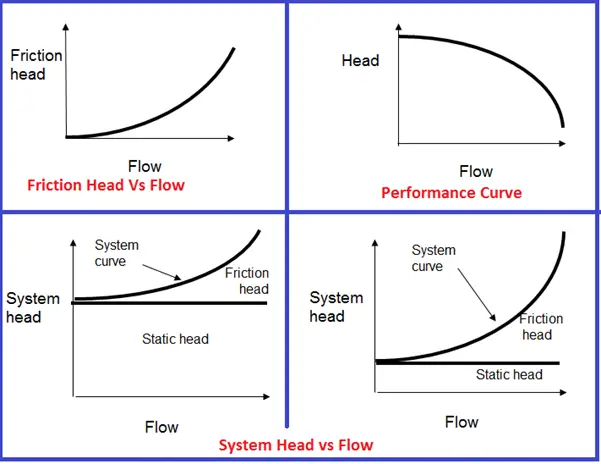
Pump performance curve
The head and flow rate determine the performance of a pump, which is graphically shown in Fig. 2 as the pump performance curve or pump characteristic curve.
Fig. 2 (Top Left) shows a typical curve of a centrifugal pump where the head gradually decreases with increasing flow.
As the resistance of a system increases, the head will also increase. This, in turn, causes the flow rate to decrease and will eventually reach zero. A zero flow rate is only acceptable for a short period without causing the pump to burn out.
Pump operating point
The rate of flow at a certain head is called the duty point. The pump performance curve is made up of many duty points.
The pump operating point is determined by the intersection of the system curve and the pump curve as shown in Fig. 3
The Best Efficiency Point (BEP) is the pumping capacity at maximum impeller diameter, in other words, at which the efficiency of the pump is highest. All points to the right or left of the BEP have a lower efficiency.
Pump Suction Performance
Pump Cavitation or vaporization is the formation of bubbles inside the pump. This may occur when the fluid’s local static pressure becomes lower than the liquid’s vapor pressure (at the actual temperature). A possible cause is when the fluid accelerates in a control valve or around a pump impeller.
Vaporization itself does not cause any damage. However, when the velocity is decreased and pressure increases, the vapor will evaporate and collapse. This has three undesirable effects:
- Erosion of vane surfaces, especially when pumping water-based liquids
- Increase of noise and vibration, resulting in shorter seal and bearing life
- Partially choking the impeller passages, which reduces the pump performance and can lead to loss of total head in extreme cases.
The Net Positive Suction Head Available (NPSHA) indicates how much the pump suction exceeds the liquid-vapor pressure, and is a characteristic of the system design.
The NPSH Required (NPSHR) is the pump suction needed to avoid cavitation and is a characteristic of the pump design.
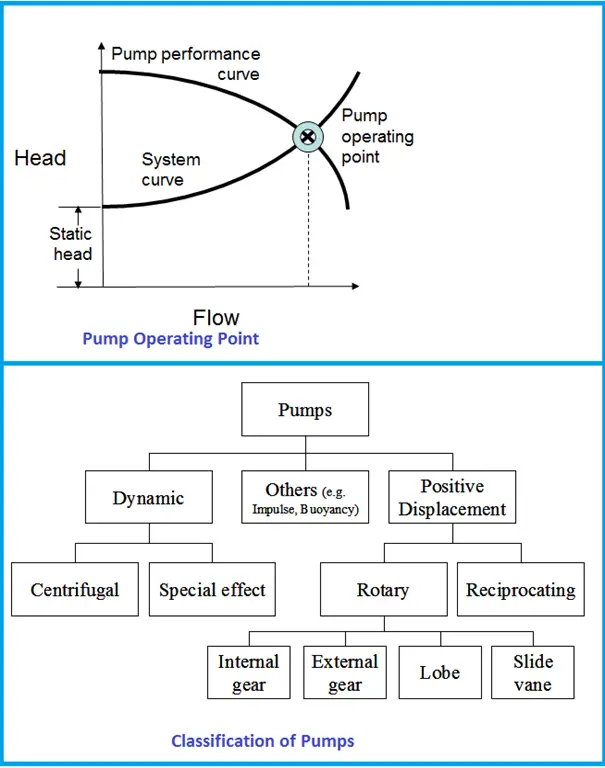
Type of pumps
- Pumps come in a variety of sizes for a wide range of applications. They can be classified according to their basic operating principle as dynamic or positive displacement pumps
- In principle, any liquid can be handled by any of the pump designs.
- The centrifugal pump is generally the most economical but less efficient.
- Positive displacement pumps are generally more efficient than centrifugal pumps but have higher maintenance costs. Click here to know the differences between a centrifugal pump and a positive displacement pump.
Positive displacement pumps are distinguished by the way they operate: liquid is taken from one end and positively discharged at the other end for every revolution.
In all positive displacement type pumps, a fixed quantity of liquid is pumped after each revolution. So if the delivery pipe is blocked, the pressure rises to a very high value, which can damage the pump.
Positive displacement pumps are widely used for pumping fluids other than water, mostly viscous fluids.
Positive displacement pumps are further classified based on the mode of displacement:
- Reciprocating pump if the displacement is by reciprocation of a piston plunger. Reciprocating pumps are used only for pumping viscous liquids and oil wells.
- Rotary pumps if the displacement is by rotary action of a gear, cam, or vanes in a chamber of the diaphragm in a fixed casing. Rotary pumps are further classified as internal gear, external gear, lobe, and slide vane, etc. These pumps are used for special services with particular conditions existing in industrial sites.
Dynamic pumps are also characterized by their mode of operation: a rotating impeller converts kinetic energy into pressure or velocity that is needed to pump the fluid.
There are two types of dynamic pumps:
- Centrifugal pumps are the most common pumps used for pumping water in industrial applications. Typically, more than 75% of the pumps installed in an industry are centrifugal pumps.
- Special effect pumps are particularly used for specialized conditions at an industrial site.
Centrifugal Pumps
A centrifugal pump is one of the simplest pieces of equipment in any process plant. The figure (Fig. 4) shows how this type of pump operates:
The liquid is forced into an impeller either by atmospheric pressure or in the case of a jet pump by artificial pressure.
The vanes of the impeller pass kinetic energy to the liquid, thereby causing the liquid to rotate. The liquid leaves the impeller at high velocity.
The impeller is surrounded by a volute casing or in the case of a turbine pump a stationary diffuser ring. The volute or stationary diffuser ring converts the kinetic energy into pressure energy.
A centrifugal pump has two main components. First, a rotating component comprised of an impeller and a shaft. And secondly, a stationary component comprised of a casing, casing cover, and bearings.

What is an Impeller?
An impeller is a circular metal disc with a built-in passage for the flow of fluid. Impellers are generally made of bronze, polycarbonate, cast iron, or stainless steel, but other materials are also used.
The number of impellers determines the number of stages of the pump. A single-stage pump has one impeller and is best suited for low head (= pressure)
Types of Impellers
Impellers can be classified on the basis of (which will determine their use):
- The major direction of flow from the rotation axis
- Suction type: single suction and double suction
- Shape or mechanical construction: Closed impellers have vanes enclosed by shrouds; Open and semi-open impellers; Vortex pump impellers. Fig. 4 shows an open-type impeller and a closed-type impeller
Shaft
The shaft transfers the torque from the motor to the impeller during the startup and operation of the pump.
The function of the Pump Casings
Casings have two functions
- The main function of the casing is to enclose the impeller at suction and delivery ends and thereby form a pressure vessel.
- A second function of the casing is to provide a supporting and bearing medium for the shaft and impeller.
Types of Pump Casing
There are two types of casings
- Volute casing (Fig. 5-A) has impellers that are fitted inside the casings. One of the main purposes is to help balance the hydraulic pressure on the shaft of the pump.
- The circular casing has stationary diffusion vanes surrounding the impeller periphery that convert speed into pressure energy. These casings are mostly used for multi-stage pumps. The casings can be designed as solid casing (one fabricated piece) or split casing (two or more parts together)
Assessment of pumps
The work performed by a pump is a function of the total head and of the weight of the liquid pumped in a given time period. Pump shaft power (Ps) is the actual horsepower delivered to the pump shaft, and can be calculated as follows:
Pump shaft power Ps = Hydraulic power hp / Pump efficiency ηpump
or Pump efficiency ηpump = Hydraulic power / Pump shaft power
Pump output, water horsepower or hydraulic horsepower (hp) is the liquid horsepower delivered by the pump, and can be calculated as follows:
Hydraulic power hp = Q (m3/s) x (hd – hs in m) x ρ (kg/m3) x g (m/s2) / 1000
Where:
- Q = flow rate
- hd = discharge head
- hs = suction head
- ρ = density of the fluid
- g = acceleration due to gravity
In practice, it is more difficult to assess pump performance. Some important reasons are:
Absence of pump specification data
Pump specification data (see Worksheet 1 in section 6) are required to assess the pump performance. Most companies do not keep the original equipment manufacturer (OEM) documents that provide these data. In these cases, the percentage of pump loading for a pump flow or head cannot be estimated satisfactorily.
Difficulty in flow measurement:
It is difficult to measure the actual flow. The methods are used to estimate the flow. In most cases, the flow rate is calculated based on the type of fluid, head and pipe size, etc, but the calculated figure may not be accurate. Another method is to divide the tank volume by the time it takes for the pump to fill the tank. This method can, however, only be applied if one pump is in operation and if the discharge valve of the tank is closed. The most sophisticated, accurate, and least time-consuming way to measure the pump flow is by measurement with an ultrasonic flow meter.
Improper calibration of pressure gauges and measuring instruments
Proper calibration of all pressure gauges at suction and discharge lines and other power measuring instruments is important to obtain accurate measurements. But calibration has not always been carried out. Sometimes correction factors are used when gauges and instruments are not properly calibrated. Both will lead to incorrect performance assessment of pumps.
Energy efficiency opportunities
This section includes the factors affecting pump performance and areas of energy conservation. The main areas for energy conservation include:
- Selecting the right pump
- Controlling the flow rate by speed variation
- Pumps in parallel to meet varying demand
- Eliminating the flow control valve
- Eliminating by-pass control
- Start/stop control of the pump
- Impeller trimming
- Selecting the Right Pump
Selecting the Right Pump
Fig. 5-B shows typical vendor-supplied pump performance curves for a centrifugal pump where clear water is the pumping liquid.
In selecting the pump, suppliers try to match the system curve supplied by the user with a pump curve that satisfies these needs as closely as possible.
The operating point is where the system curve and pump performance curve intersect (as explained in the introduction)
The Best Efficiency Point (BEP) is the pumping capacity at maximum impeller diameter, in other words, at which the efficiency of the pump is highest. All points to the right or left of the BEP have a lower efficiency.
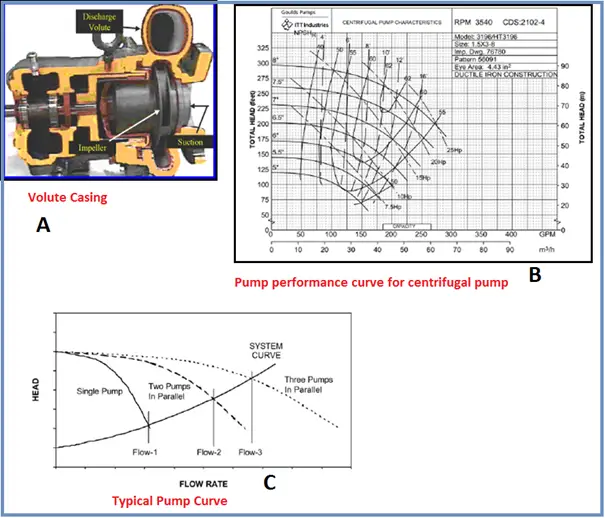
The BEP is affected when the selected pump is oversized. The reason is that the flow of oversized pumps must be controlled with different methods, such as a throttle valve or a bypass line. These provide additional resistance by increasing friction. As a result, the system curve shifts to the left and intersects the pump curve at another point. The BEP is now also lower. In other words, the pump efficiency is reduced because the output flow is reduced but power consumption is not.
Inefficiencies of oversized pumps can be overcome by, for example, the installation of VSDs, two-speed drives, lower rpm, smaller impeller, or trimmed impeller
Controlling Flow: Speed variation
A centrifugal pump’s rotating impeller generates a head. The impeller’s peripheral velocity is directly related to shaft rotational speed. Therefore varying the rotational speed has a direct effect on the performance of the pump.
The pump performance parameters (flow rate, head, power) will change with varying rotating speeds. To safely control a pump at different speeds it is therefore important to understand the relationships between the two. The equations that explain these relationships are known as the “Pump Affinity Laws”:
- Flow rate (Q) is proportional to the rotating speed (N)
- Head (H) is proportional to the square of the rotating speed
- Power (P) is proportional to the cube of the rotating speed
As can be seen from the above laws, doubling the rotating speed of the centrifugal pump will increase the power consumption by 8 times. Conversely, a small reduction in speed will result in a very large reduction in power consumption. This forms the basis for energy conservation in centrifugal pumps with varying flow requirements.
- Controlling the pump speed is the most efficient way to control the flow because when the pump’s speed is reduced, the power consumption is also reduced.
- The most commonly used method to reduce pump speed is Variable Speed Drive (VSD).
- VSDs allow pump speed adjustments over a continuous range, avoiding the need to jump from speed to speed as with multiple-speed pumps. VSDs control pump speeds using two types of systems:
- Mechanical VSDs include hydraulic clutches, fluid couplings, and adjustable belts and pulleys.
- Electrical VSDs include eddy current clutches, wound-rotor motor controllers, and variable frequency drives (VFDs). VFDs are the most popular and adjust the electrical frequency of the power supplied to a motor to change the motor’s rotational speed.
- The major advantages of VSD application in addition to energy-saving are:
- Improved process control because VSDs can correct small variations in flow more quickly.
- Improved system reliability because wear of pumps, bearings, and seals is reduced.
- Reduction of capital & maintenance costs because control valves, by-pass lines, and conventional starters are no longer needed.
- Soft starter capability: VSDs allow the motor to have a lower startup current.
Parallel Pumps for Varying Demand
Operating two or more pumps in parallel and turning some off when the demand is lower, can result in significant energy savings. Pumps providing different flow rates can be used.
Parallel pumps are an option when the static head is more than fifty percent of the total head.
The Fig. 5 shows
- the pump curve for a single pump, two pumps operating in parallel, and three pumps operating in parallel.
- that the system curve normally does not change by running pumps in parallel.
- that flow rate is lower than the sum of the flow rates of the different pumps.
Eliminating Flow Control Valve
- Another method to control the flow is by closing or opening the discharge valve (this is also known as “throttling” the valves).
- While this method reduces the flow, its disadvantages are
- It does not reduce the power consumed, as the total head (static head) increases. Fig. 6 shows how the system curve moves upwards and to the left when a discharge valve is half-closed.
- increases vibration and corrosion and thereby increasing maintenance costs of pumps and potentially reducing their lifetimes
- VSDs are a better solution from an energy efficiency perspective.
Eliminating By-pass Control
The flow can also be reduced by installing a bypass control system, in which the discharge of the pump is divided into two flows going into two separate pipelines. One of the pipelines delivers the fluid to the delivery point, while the second pipeline returns the fluid to the source. In other words, part of the fluid is pumped around for no reason, and thus is an energy wastage. This option should, therefore, be avoided.
Start / Stop Control of Pump
A simple and reasonable energy-efficient way to reduce the flow rate is by starting and stopping the pump, provided that this does not happen too frequently. An example where this option can be applied is when a pump is used to fill a storage tank from which the fluid flows to the process at a steady rate. In this system, controllers are installed at the minimum and maximum levels inside the tank to start and stop the pump. Some companies use this method also to avoid lowering the maximum demand (i.e. by pumping at non-peak hours).
Impeller Trimming
- Changing the impeller diameter gives a proportional change in the impeller’s peripheral velocity
- Changing the impeller diameter is an energy-efficient way to control the pump flow rate. However, for this option, the following should be considered:
- This option cannot be used where varying flow patterns exist.
- The impeller should not be trimmed more than 25% of the original impeller size, otherwise, it leads to vibration due to cavitation and therefore decrease the pump efficiency.
- The balance of the pump has to be maintained, i.e. the impeller trimming should be the same on all sides.
- Changing the impeller itself is a better option than trimming the impeller, but is also more expensive and sometimes the smaller impeller is too small.
- Figure 6 illustrates the effect of impeller diameter reduction on centrifugal pump performance.
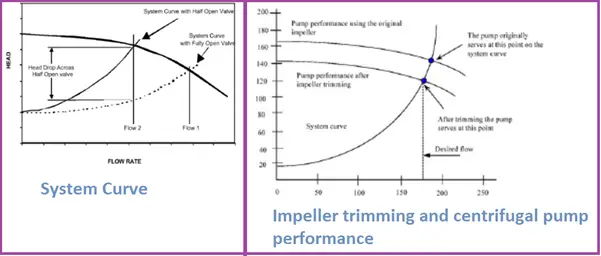
Figure 6 illustrates the effect of impeller diameter reduction on centrifugal pump performance.
- With the original impeller diameter, the flow is higher
- With the trimmer impeller, the flow is lower
Parameter | Change control valve | Trim impeller | VFD |
Impeller diameter | 430 mm | 375 mm | 430 mm |
Pump head | 71.7 m | 42 m | 34.5 m |
Pump efficiency | 75.1% | 72.1% | 77% |
Rate of flow | 80 m3/hr | 80 m3/hr | 80 m3/hr |
Power consumed | 23.1 kW | 14 kW | 11.6 kW |
The above table compares three options to improve energy efficiency in pumps:
- changing the control valve, trim the impeller and variable frequency drive.
- The VFD clearly reduces power most, but a disadvantage is the high costs of VFDs.
- Changing the control valves should at all times be avoided because it reduces the flow but not the power consumption and may increase pump maintenance costs.
Few more Pump Related Resources for you..
Cause and Effect of Pump Cavitation
Major Factors Affecting the Pump Performance: An article
NPSH for Pumps: Explanation and Effect
Water Hammer Basics in Pumps for beginners
Mechanical Seals for Rotary Pumps
Thanks for helping me learn more about pumps and pumping systems. I didn’t know that many pumps can be classified based on thee operating principle they use. I’m kind of interested to learn if this means pumps under a certain classification are all about the same size or if they could vary as well.
Hey can you please describe the easy way to understand the discharge ability of every pump… How they are relatable. Specially positive displacement pump
Beautifully explained
A very good and insightful piece for refreshment. However I didn’t clearly get the pump curves
This article gives us suggestions on pumps pumping systems .In order to get better information and guidance you can come In this link. It plays a vital role in taking us through. It can be really great for people like me who are looking for grabbing more knowledge about. One must check this Baheatpumps.co.nz it gives us more info on this topic.
It is a pleasure worth reading this article as it is stating about the pumps pumping system. This is one of the best write up. Such illustrations are given that a layman could even understand. It is an easy to comprehend blog which can be instigated by all at least once. This is a great post; I will share as much as I can.I have seen similar information at one place, you can also see on Comfortgroup.co.nz
It is one of the best write up on the pumping system . Before hitting on the other blogs I would request everyone to give a try over here to get the best available content. The article is much informative regarding work as well.
If the author of the small presentation of pumps tries to include assembly, erection and allignment of pumps to driver then the whole presentation will be very much useful to even a beginerto entrepreneurs.
Nevertheless it is a very nice presentation by the author.
Details regarding: After instalation leveling including elevation level to match suction and delivery piping nozle levels as given in approved drawings, allignment with driver keeping pump as the master, grouting (initial up to pocket level) with propper foundation bolts, final allignment with out pipe & with pipe , final grout( including various types of grout and their strength and importance) with propper shuttering on all sides including inside incase of verical pumps; pre commission & commission will definitely make the author’s contribution on pumps-A manual on pumps.
Nevertheless this is a tremendous rendering by the author which is a precise manual on pumps selection while designing plant layout.
Very informative, thank you.
It’s great that you also mentioned that energy efficiency is an important thing to consider when it comes to industrial pumps. I’m currently looking for the best ones in the market because I might need them for my farm someday. Having an intricate irrigation system would be important to set up for such an undertaking.
Now I understand that Best Efficiency Point determines the highest efficiency a pump can operate under. I’ll have to note this if I do look for specific types such as ones used in chemical processes. it would be great if a manufacturer can offer trial periods to see if the equipment fits the needs of the buyer.
This article is great for people like me who are looking for more knowledge about pumps and pumping. Thank you