The scope of this article is to take you through a brief introductory view, of the know-how of SMAT (Smart Plant Materials) and the information about the necessary attributes in this software required for piping specification activities.
What is Smart Plant Materials?
Smart plant materials (SMAT) is basically a materials management and administration system for process plants. For example, its main applications are the design, engineering, and construction of processing plants for the chemical, pharmaceutical, and mineral oil industries, and for industrial pipeline construction. The software is developed by Intergraph, currently owned by Hexagon. Because of this, the software is popularly known as Intergraph smart-plant materials or Intergraph smart materials.
SMAT supports materials management for all disciplines, for example:
- Piping (including Supports)
- Instrumentation
- Structural steel equipment (vessels, etc.)
Objectives of Smart-Plant Materials
The main objective of SMAT is to provide continuous support for all processing stages of project management. This includes the pre-project phase of parts and standards specification, design and financial planning, the definition of material requirements, procurement and scheduling, pre-fabrication and installation as well as deadline and cost tracking.
Integration of Smartplant Materials
Smart plant materials can be easily integrated with various well-known 3D piping modeling software packages that are widely used in the design. Some typical examples include:
- PDS (Plant design system),
- SP3D (Smart Plant 3D), and
- AVEVA E3D which makes it a widely used software.
Specification group specialists within the piping department use smart plant materials or SMAT during the proposal and project stage. They are generally a small group confined within the piping department.
They use it to prepare piping specifications with all the materials involved. The whole database required for the preparation of such pipe classes is stored in a separate window in smart plant materials (SMAT), which is regulated by users having specific access to the such window and of course, the Computer Aided Engineers involved. The material requisition generated through SMAT is later sent to procurement for procuring the materials. The overall tracking of material supply status at all stages of the project can be done with a report named “Supply status report” generated through this software.
Identification codes (Ident codes) are also generated through this smart plant materials software. The materials are generated and placed for order with such codes to keep a track of their identification right up to their delivery, storage, and installation at the site.
There are various other standardized reports generated through this software (like materials in various piping specifications (specs), and identification codes (Ident codes in various classes), which can be used at various project stages.
Attributes of SmartPlant Materials
From a piping specification point of view, smart-plant materials have various attributes as depicted in the below figure (Fig. 1).
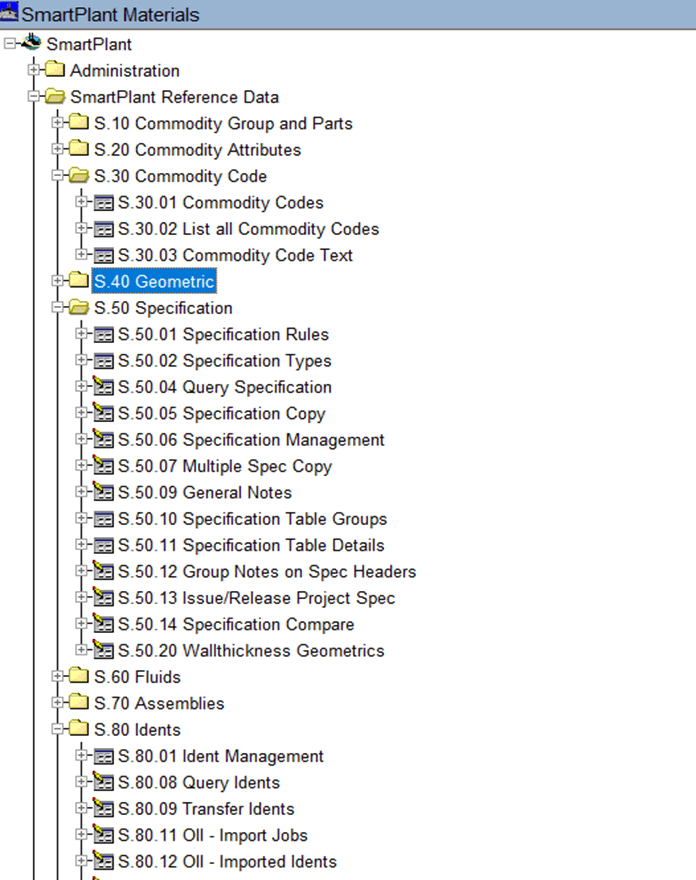
To have general know-how about smart-plant materials modules, the following commonly used attributes have been described.
1. Preparation of pipe classes or piping specifications:
To start with the preparation of the pipe class in smart plant materials modules.
- A reference project pipe class or a standard template pipe class that has already been prepared (such as a pipe class with the same base material, corrosion allowance, and class rating) shall be taken.
- Then go to window S50.05 “Specification copy”
- Then fill in the required attributes with the desired name of the class and the class is copied.
- Once the class is copied, go to window S50.06 “Specification management” and type the class name created in S50.05.
- On similar lines, S50.07 allows you to copy through multiple specifications.
2. Any particular note to be added in pipe class for a component can be done through the S50.09 attribute “General Notes”.
3. Once the pipe classes have been copied, they can then be viewed in the window S50.06 “Specification Management”. Here the various pipe classes copied for the specific project can be viewed below under column Spec code. Refer to Fig. 2 below.
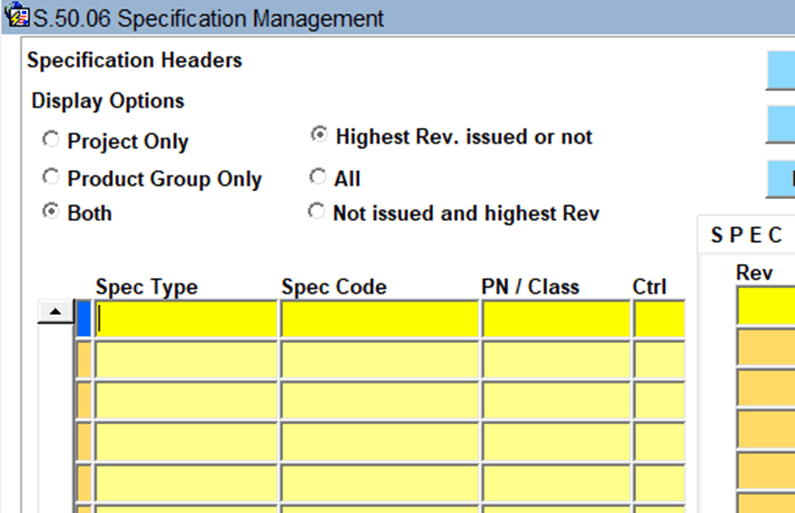
4. Generation of pipe classes with the required components:
Once we type a pipe class copied and created as per the above steps in S50.05, we type it under the spec code here in window S50.06. Then the Pipe thickness with schedule, the branch table, the design code used, the design conditions used, the base material, corrosion allowance, the trim (seat material) for the valves, the flange rating, and the finish can all be added for the desired class.
Once this is done, we double-click under the spec code for the desired pipe class and then start preparing the class by adding the various components in the below window “S50.06 Window 2” (Fig. 3)
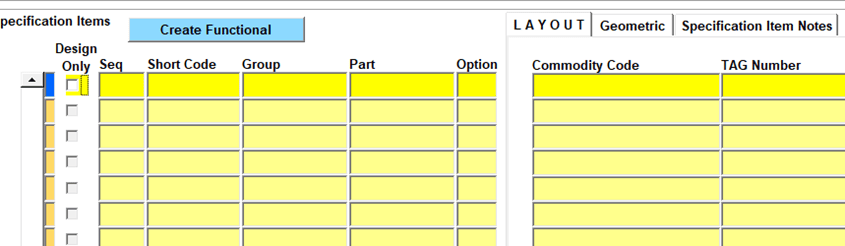
The bulk components such as pipes, fittings, flanges, spectacle discs, blind and spacer blinds, bolts, gaskets, and valves are inserted in the pipe class through a commodity code. The commodity code is where the description for the component is present.
The components/commodity code is then added as per the short code, group code, option code (which can be customized), and sizes.
The commodity code for the components can be created in the common database (only specific users would have access) in Windows S30.01. One such commodity code can be viewed with its description in the window as shown below in Fig. 4:
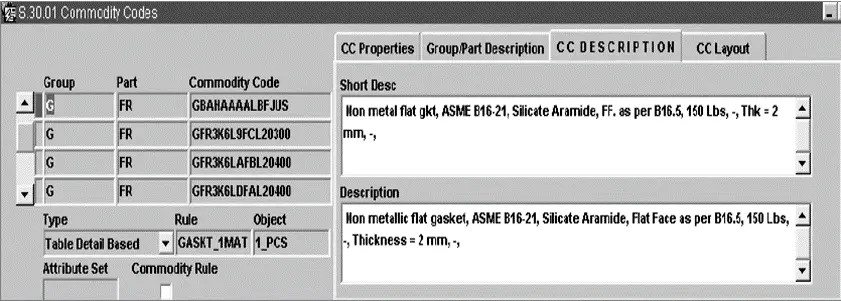
Once the components are inserted in the class as per the contractual requirements / ITB, and Licensor specification, the class can be checked, locked, or issued as in window “S50.06”.
Once locked, the various reports from SMAT are downloaded.
One particular report is where the idents (Identification codes) as mentioned earlier are automatically generated by the software for each commodity code size-wise. For the bulk components, excluding valves, the identification codes are generated with respect to the pipe thickness and geometry present in the database for the relevant thickness, for the bulk valves they are generated separately, linked to the geometrics present in the respective database for the valves as per the relevant standards.
The other report is the pipe specification (prepared as per previous steps) in pdf format which can be downloaded, checked, and further issued to the Client. This report itself can also be customized with the help of software technical support.
The required geometric data for each component is extracted from the common database.
This SMAT software is linked to modeling software such as PDS, SP3D, and E3D, and hence the components can be properly modeled using these geometrics which is already defined per the ASME standards.
5. Window S50.13:
This window in smart-plant materials gives an overall view of the different piping specifications involved in the project and their status (Issued or Revised). Once the piping specification is issued (locked), it can be revised using the revised command.
6. Window S80 Ident management:
The overall identification codes management is done in the window Ident management. This is used during various cycles of the EPC project wherein; the identification codes may not be created or present for a particular component for procurement purposes.
It can well be generated here. It is linked to the common database where the dimensions of components are present as per the ASTM standards.
If at all for a particular size of the component, the identification cannot be created because the geometric was not present. Then in such case, the user (having access to the database) can insert dimensions as required respecting the ASTM standards and link it to the geometric of the component after which the identification code can be prepared.
7. This software also aids the piping material engineers in generating various reports for checks before material requisition. The material requisition report generated through this software is further attached to the purchase specification which is required to place the Purchase order.
I am interested in having your specialty in smartplant materials(SMAT) in the area of oil refinery and petrochemical projects. Please let me know your email address for further discission.
Regards,
S. S. Park
G-PEM, Seoul, Korea
Is there a training institution or school for this kind of software? I am interested to learn and to know more about this Smartplant Material software with regards to piping specification activities. Thank you and have a nice day.
Regards,
J. S. Lazo
Piping Engineer, Philippines